If there is one area where health and medical 3D Printing differ from general 3D Printing, it is liability. The term has never been so controversial than in this field. Indeed, 3D printed medical and health-related models can result in various forms of liability issues, and surprisingly, one way to avoid liability issue with 3D Printing/Additive Manufacturing is to ensure that post-processing has been completed properly.
Most of the times, we usually talk about post-processing challenges in demanding industries such as aerospace, space or even automotive. Reality shows that any fabrication utilizing additive manufacturing can require a form of post-processing stage, or “pre-post-processing”, as per the words of Solukon’s CEO Andreas Hartmann.
In the medical 3D Printing industry, this stage is even more complex as professionals manufacture complex parts that are often inserted in the human body. The risks that might occur in such a vital environment often lead to more challenges than expected, as told by French company Coulot Décolletage.
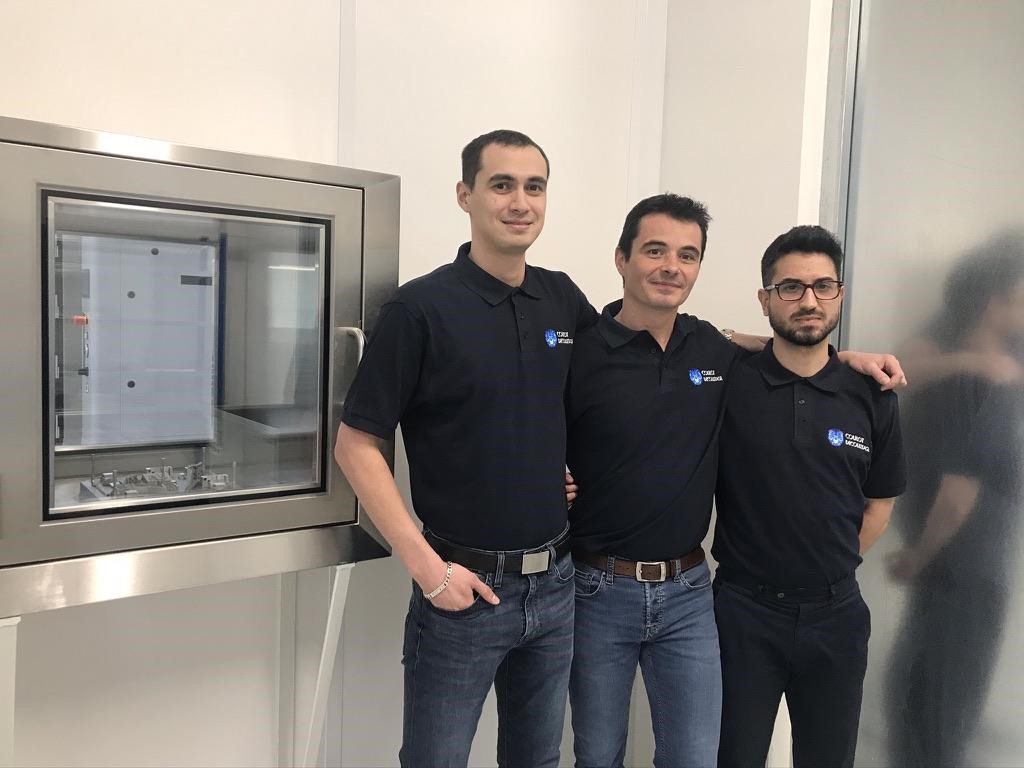
Founded in 1985, Coulot Décolletage provides aerospace companies with various components it manufactured using conventional manufacturing processes. A decade later, in 1996, the company reaches a fundamental milestone and decides to gear product offering towards the medical industry. Several certifications and various collaborations with international medical distribution groups in hand, Coulot Décolletage is acknowledged today for its ability to manufacture complex products including medical prostheses or implants for the spine, orthopedics and neurology fields.
In 2016, the company begins to leverage additive manufacturing in its production workflow. Satisfied with the results, it gradually constitutes its additive manufacturing production portfolio. At present, with two metal additive manufacturing 3D Printers and one polymer 3D Printing system, the medical parts manufacturer can produce complex parts, improve osseointegration and save production time and costs.
“This technology has opened up new avenues for product development. Indeed, the designs are more optimized and the material is used only for its strict utility”, states Saby Eric, AM Manager at Coulot Décolletage.
What the team at Coulot Décolletage did not know, it is the challenges they were about to encounter after the printing process.
COMPLIANCE WITH REGULATIONS BUT NOT ONLY…
First, as discussed in the March/April issue of 3D ADEPT Mag, several considerations should be taken into account prior to investing in additive manufacturing technologies. As a reminder, these considerations fall into four main key areas which include machine and tooling costs, production environment, design for additive manufacturing, and the stages that follow the printing process (better known as post-processing).
In the case of our French company, the production environment and the postprocessing stage were even more crucial as the company handles complex materials.
Due to handling of complex powders in their working environment, and to comply with the French governmental decree of 05 December 2016, the “first challenge was to put in place a building that meets all the regulatory requirements related to powders”, explains the company.
Once it was done, the next challenge occurred: the removal of powder residues in the internal structures of additively manufactured parts. “The parts produced by additive manufacturing always contain powder residues that we cannot remove manually. In addition, the complex geometries do not facilitate the “depowdering process”. We therefore need to “de-powder” our part before the heat treatment, otherwise the powder will be sintered in the part and the part will be thrown away. [Not to mention that with regard to] medical requirements, we must work on clean, powder-free parts. That’s the reason why we turned to Solukon, a company which offers depowdering machines”, adds the AM Manager at Coulot Decolletage.
“AN EFFECTIVE DEPOWDERING MUST BE APPLIED”
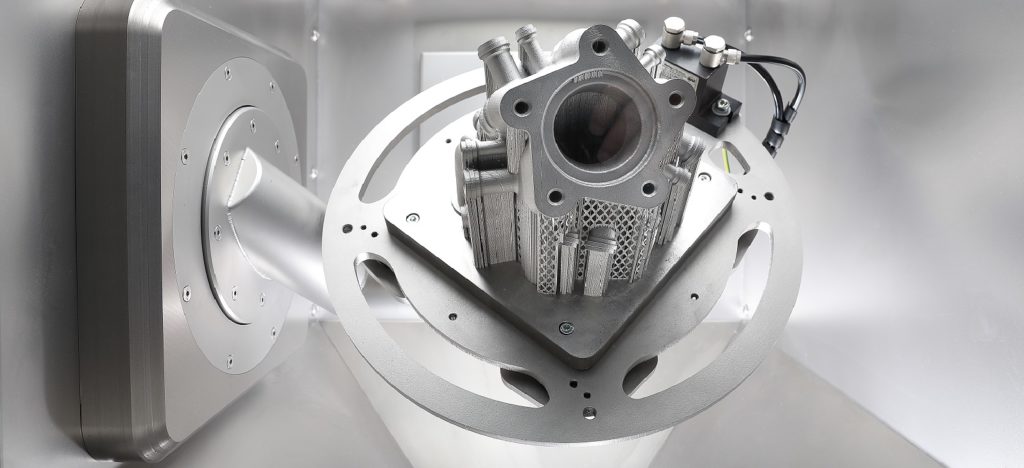
Solukon has gained extensive experience in various powder removal applications across industries. Through its automated powder removal technology, the manufacturer aims to close the gap between manufacturing and post processing.
The company is using the SFM-AT-300 to remove the remaining powder on the part. However, removing that powder manually was really time-consuming for Coulot Decolletage.
Indeed, before the integration of Solukon’s technology into its production portfolio, Coulot Decolletage used to leverage manual powder coating for such tasks. Not only this method is “obviously insufficient”, but it “cannot be repeated on 1000 parts”, explains Saby Eric.
Imagine a scenario where a 3D printed intervertebral cage still contains a lot of powder after the fabrication stage and the damages it can cause into a human body if this postprocessing stage is not met properly. Therefore, to prevent this powder from sintering in the lattice structure, it is crucial to entirely remove the powder.
One advantage brought by Solukon in this regard, is automation. “The machine is easy to use, efficient for depowdering the parts and safe [for] ATEX materials such as titanium”, completes the operator.
What the company appreciates the most is “the vibration system coupled with the rotation of the platform under inerting”.
THE UNIQUENESS OF MEDICAL APPLICATIONS
Unlike other industries, applications of additive manufacturing in the medical industry have to meet the most stringent requirements. Parts accuracy, cleanliness and even compliance with regulations and medical standards per country are just some of the key features that enable the manufacturing process in this field to stand out from the crowd.
Interestingly, additive manufacturing turns to be the ideal candidate for the production of some parts. Parts that should be customized to fit the body of a patient for instance, parts that integrate complex geometries or parts with bionic forms and structures are best produced via AM.
The only thing is that, “the more complex the structures of the components are, the more complex is the task of meeting the demands for fast and reliable cleaning. The materials used, such as Titanium, meet all requirements but are expensive and difficult to handle due to their flammability”, explains Hartmann, Co-founder and technical director.
Solukon’s cleaning method addresses these issues with its systems. By using the company’s system, the operator collects the powder released during cleaning for reuse.
Furthermore, Solukon has also been able to address another peculiarity of medical 3D Printing: the size of components.
As parts produced for the medical industry are usually small, it is possible to arrange several parts on the build tray. The only thing is that, the production of several parts this way, is usually performed with a small Z-dimension, which might lead to short production times but might increase the need for quick unpacking and cleaning.
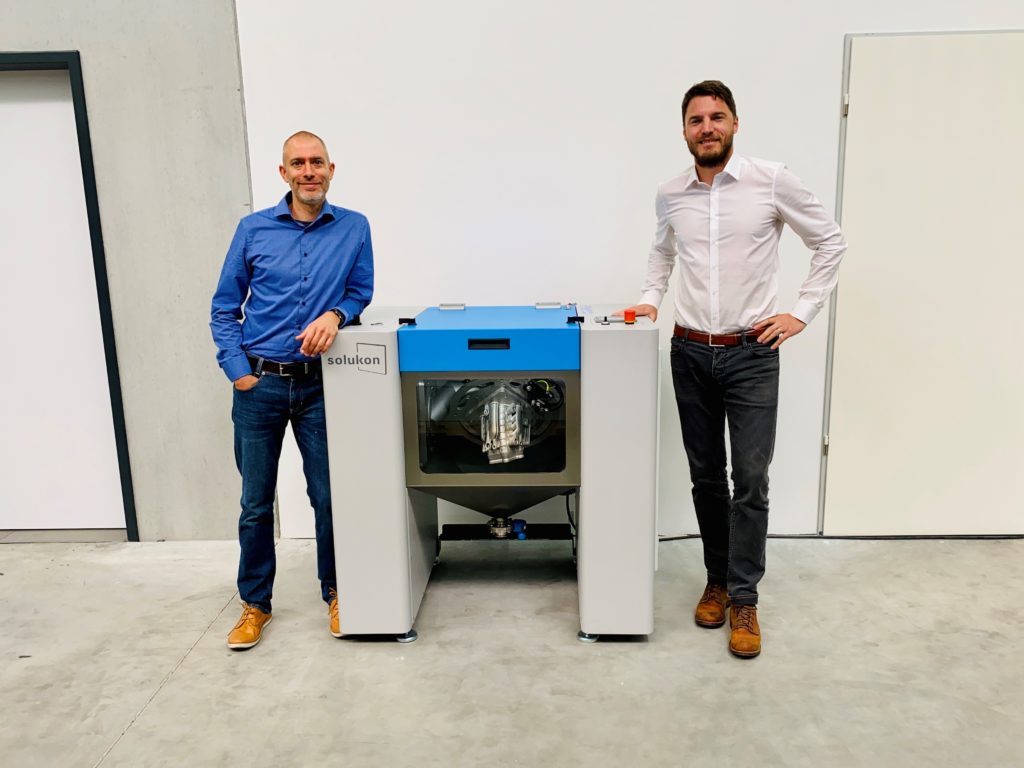
To address this limitation, Solukon has developed the SFM-AT200 system. The system which is a particular good fit for medical applications, “is characterized by a geometrically optimized process chamber, which is flooded with protective gas in a very short time. Thus, the cleaning time including non-productive times such as loading and chamber inerting can be reduced to a few minutes. Serial cleaning processes are now easily possible”, says Hartmann.
“The simple and compact design saves installation space, inert gas and acquisition costs at the same time. Due to the good accessibility for cleaning and filter change, a material change can also be carried out in a short time. Considering the requirements of the medical-AM production, the SFM-AT200 is the right choice”, adds Michael Sattler, Global Sales Director.
Solving a depowdering and cleaning issue is not an easy task. A constant manufacturing environment will be pointless if scaling and automating post-processing operations remain a hurdle. Ultimately, the appropriate post-processing solution in place opens the door to a high degree of repeatability and productivity. More importantly, for a vital industry such as medical, it somehow leads to the development of medical devices that are safe enough to be inserted in the human body, and that becomes a matter of liability.
This article has originally been published in the May/June issue of 3D ADEPT Mag. On September 10th at 14:45 – 15:30 CET, during the Additive-Talks Day, Solukon will discuss “Costs & Considerations for Investing Into an Additive Manufacturing System” and on September 24th at 05:00 PM, the company will hold a webinar on medical applications in the AM industry. Make sure you save your seat to learn more about the company’s expertise in the additive manufacturing industry.