A look at GF Machining Solutions for post-processing and an eye on medical applications
The big world of manufacturing continuously requires companies to embrace new thinking, new processes and new machinery. With centuries of experience in manufacturing, Georg Fischer (aka GF) has dedicated its core business to address the challenges of this universe. Through its three divisions GF Piping Systems, GF Casting Solutions, and GF Machining Solutions, the Swiss company delivers its services across 33 countries, with 140 companies, 57 of them being production facilities. However, the division GF Machining Solutions is the one that draws our attention today. With expertise in EDM (electrical discharge machining), laser texturing machines, milling and advanced manufacturing unit, the company has been operating in stealth mode ever since it has debuted on the additive manufacturing segment.
Although its extensive experience in machining has helped build its presence in the additive manufacturing arena, like its fellow companies, GF Machining Solutions also relied on collaborations with other AM companies, the most prominent collaboration being the one with 3D Systems. In this continuous quest to address the unique needs of companies that are battling to adopt AM in production environment, the advanced manufacturing unit is continuously making adjustments and improvements on hardware and software environments; improvements in a nutshell that will simplify the path to a seamless and efficient production workflow.
These adjustments also require a focus on “automation products which are tooling and robotics – as well as digital transformation which is quite transversal to all technologies”, Romain Dubreuil, Head of Additive Technologies told 3D ADEPT Media in an interview.
Furthermore, although the company usually talks about it as part of its “integrated manufacturing solutions” and rarely as an individual solution, our conversation with Dubreuil sheds light on specific hardware that has been developed for the much-required post-processing stage.
“This stage of the manufacturing process can either be done by ‘depowdering’ or finishing of AM parts by machining operations.
As far as finishing is concerned, we can complement the printing of the part with one of the conventional manufacturing machines in our portfolio. This can be a standard milling machine or a standard wire EDM machine. In many cases, they can fit well as many operators after the printing stage, machine the part to improve the finishing in a certain area for instance”, Dubreuil outlines.
As we will discover later on, in the lines below, AM offers so much possibilities for complex implants and biomedical products that 3D printed parts sometimes need further machining and finishing. At this level, workpiece fixturing devices for clamping are often used to process the part and to facilitate subsequent processes.
“We have also developed a specific solution that can cover the needs of AM in this regard”, Dubreuil points out.
Named CUT AM 500, this post-processing machine is designed to meet the specific needs of AM and is based on the company’s expertise in EDM. Described as an automation-ready alternative to using standard EDM, the process looks like a band saw that separates additively manufactured parts from the build plate. The CUT AM 500 is a good complement to laser powder-bed fusion (LPBF) metal 3D printers.
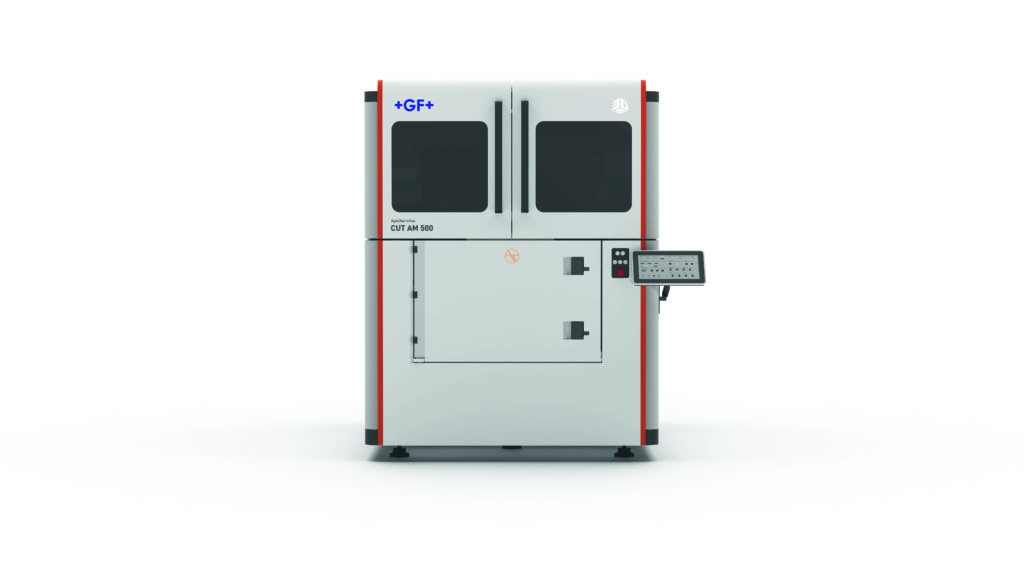
“Although it has been developed with LPBF in mind, it does not necessarily mean that our portfolio cannot be used for other manufacturing technologies such as Electron Beam Melting or simply metal applications in general”, the Head of Additive Technologies notes.
With a size of 510 x 510 x 510 mm, the system allows for the removal of products from large build plates with a weight of up to 500 kg, cleanly and without cutting forces. According to the manufacturer, the process would ensure parts integrity thanks to the tilting table, the horizontal wire EDM process and the customizable baskets. In addition, unlike other post-processing systems, this one enables the integration of a clamping system for easier clamping and referencing as well as automation readiness.
Manufacturing choices
Taking a product from idea to design and 3D printing requires both experience and the appropriate technologies. Although we only focus on post-processing here, let us remind that the ideal AM process includes the entire ecosystem, from quality control processes for incoming powder to software, post-processing, and process controls on finished products. We can never stress this enough but each of these items is crucial to a successful production in highly regulated sectors.
“In general, we focus more on production applications. We are very active in different segments: mould and die, energy and aerospace, industries in a nutshell, where AM can bring benefits to increase performance and weight, and improve parts accuracy. That being said, we also keep a strong focus on the medical industry. One of the major applications in this field remains spinal implants that require technologies that meet the requirements of AM”, Dubreuil states.
A quick look at the manufacturing of a dental implant.
As applications remain a good proof-of-concept of the way technology works, the Head of Additive Technologies and his colleague Dogan Basic share with us a few details on the production of a dental implant as well as several post-processing tasks that can be achieved before getting the desired finished part.
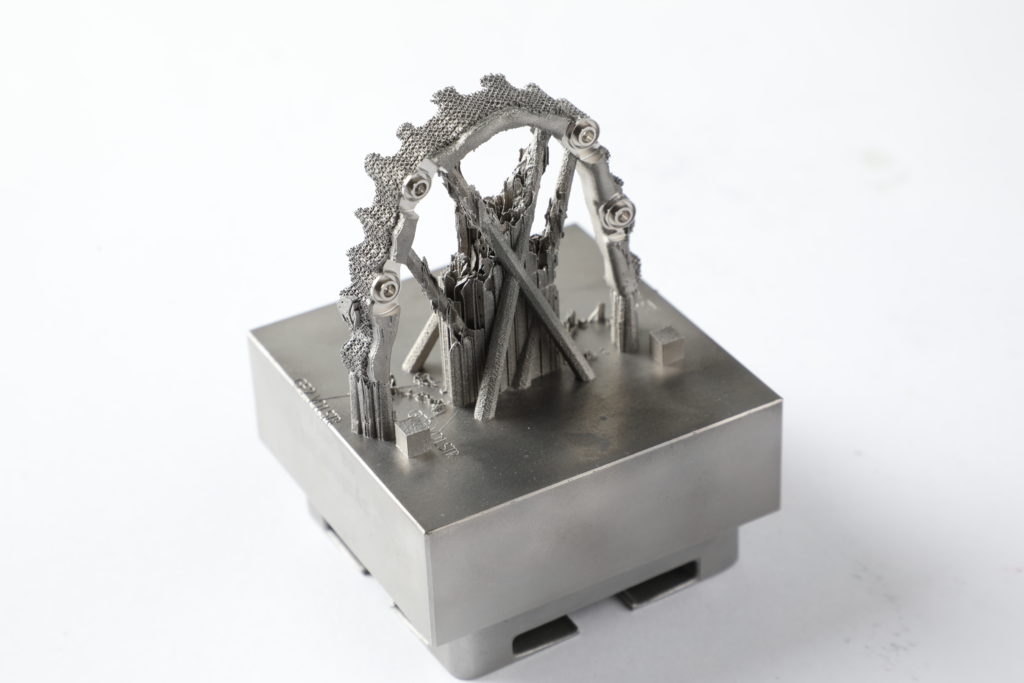
Although we do not know for which purpose the implant has been produced (whether it is for research or commercialization purpose), the manufacturing team used the well-known DMP Flex 350, a LPBF-based industrial 3D printer that sported a new look the last time we saw it at Emo Hannover 2019. During the printing process, not only does the system ensure a consistently low oxygen environment but also very high density. We know from the manufacturer that the part has been produced using the LaserForm® CoCrF7 material and was printed with 30um layer thickness.
However, what raises the most our interest, is both the accuracy in terms of manufacturing time and post-processing operations.
“It will take 34 min to print one part but obviously, you will print multiple parts at the same time. (9 hours to print 20 parts). We print them on our small System 3R plates in order to facilitate the post-processing operations. It will take around 23 min to mill each part and just a couple of minutes to separate them with the CUT AM 500”, Dogan Basic from GF Machining explains.
As mentioned earlier, complex implants sometimes need further machining. To address this issue, operators can use this equipment called “System 3R” available in a range of pallet sizes. With the help of a conventional lathe, they can cut each pallet from the stack directly, allowing for the separated BuildPals to be used for further additive manufacturing work while post-processing continues.
In this specific case, Dogan explains that before the milling operation, the part traditionally goes through heat treatment operation and thereafter, through a 5-axis milling operation to ensure that the “connections” are milled for the screws.
Thereafter, “you will have potentially hand finishing to remove potential residual supports and a cleaning operation.”
It’s only after these tasks that the implant can easily be fixed in the jaw.
Concluding Thoughts
Additive manufacturing is certainly one of the industries where there will always be something new to learn and GF Machining’s perspective in this post-processing segment shows that there is no “one-size-fits-all solution”. That’s why getting into AM is one thing, and taking the right steps to incorporate its whole process chain is another one, but if it is done well, the rewards one can get can only be substantial.
This feature has first been posted in the 2021 January/February issue of 3D ADEPT Mag.