“Any destination in the AM maturity model is the perfect place where to be.”
Taking one’s first steps into AM or evolving in this industry calls for a range of methods or processes that all converge towards the same goals: acquiring new skills, implementing the right steps for a go-to-market strategy, staying informed on the current state of the market or learning new ways to grow one’s business model – all of which can be achieved through industry publications/trade press, academic institutions and consultancy firms. As we look back over 2022, it makes sense to take into account the point of view of experts that are shaping the AM market from an education and/or a consultancy standpoint – and understand through them the 2022 AM market and what would be areas of interest in 2023. Once combined with the right experience and expertise, the unique understanding of experts from academic institutions and consultancy firms enables them to get to the bottom of a problem that often has its roots in the industry itself; or to share takeaways based on their close connections with the AM end user – all of which is useful to help both technology providers and adopters to move forward. In this specific case, the experts we decided to rely on are Olaf Diegel and John Barnes.
Both gentlemen have many super powers.
Diegel is probably one of those coolest professors I wish I had when I was a student. He teaches AM in its entirety and is always looking for a way to apply and explore this technology. His most famous application remains a range of 3D printed guitars with bold designs.
On the other hand, Barnes’ notable experience prior to founding TBGA in 2017 is his experience as a senior manager at Lockheed Martin’s Skunk Works where he helped bring metal 3D printed parts to a number of experimental military aircrafts and where he led several other programs to foster the adoption of AM technologies. Today, with a team of ADDvisors®, TBGA’s goal is to get AM qualified and in service across a range of industries.
AM learning and research in 2022
AM learning is often said to become more complex, research is happening at a break-neck pace and ever-advancing technologies are driving new teaching models. Diegel told us they have a dedicated full semester post-grad course focused on design for AM, and they offer a lot of industry 3- or 4-day hands-on DfAM courses (through ASTM and Wohlers Associates) to company engineers.
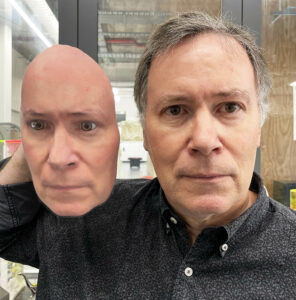
Furthermore, compared to previous years, “it seems the end of all the pandemic restrictions has created a thirst for hands-on learning”, the professor of AM explained. “I think that a lot of students have been fairly deprived of practical and applied work during the pandemic so, now that it is possible to get back into the labs and workshops, I am finding a lot of students really want to get their hands dirty with solving practical engineering problems. And, in my opinion, because design for additive manufacturing (DfAM) is not a theoretical area of knowledge, but rather one that must be practically applied to add true value to products, students are just loving it. And the same goes for companies. As they are starting to realize just how critical good design for AM is to them being able to economically implement AM, they are crying out for knowledge to do it the right way”, he said.
For Barnes, training has always been one of the major roadblocks to AM adoption. After over 2 decades in the AM industry, and five years of TBGA, he still emphasizes on it:
“I think awareness and appreciation of what AM can do is still relatively young. Whether we call it training, or skills development, we are seeing in almost all ‘mature’ countries that the qualified workforce is the missing item in manufacturing industries. If you take a step back, any time when you come with something disruptive, by nature, it’s hard for people to deal with it. Plus, given the diversity of the technology available, there are many solutions to choose from, and most people are stuck because they just don’t know what AM can do. They are still not designing products that can really take advantage of AM, because it requires risks, it requires a step change process”.
On another note, this integration of knowledge and ways of thinking to tackle complex challenges has been achieved somehow thanks to face-to-face encounters. Diegel drew our attention here on a consequence of the pandemic that deeply affected the educational system and that we didn’t really pay attention to last year. To him the big difference 2022 brought compared to the previous year, was getting to meet face to face with people again. “That includes students, colleagues, companies, and friends. And also, a huge difference was for students and companies to not have direct access to the machines when the lab was closed. It always seems harder to solve engineering problems, or design great products, over Zoom or Teams. And we’ve had over 2 years of that, so it’s good to get back to the machines and build real parts, physically test ideas, and do all that fun stuff. [In general], around the world, education has, of course, been heavily impacted by the inability of people to be able to travel, which means there has been a huge drop in international students. But hopefully, that will now start to correct itself”, he continues.
Barnes remains practical and focuses on the need to look at one’s maturity AM model to analyse AM processes, applications and somehow one’s progression. From our understanding, the proprietary model would aim to balance product requirements, company’s awareness, data and skills needed to use AM through a five-level matrix.
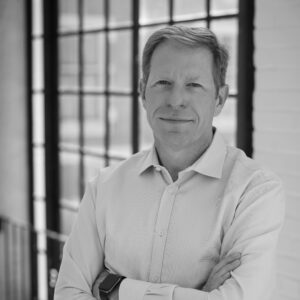
“It’s a way to adjusting to the chaos”, TBGA’s founder points out. “At the end of the day, that part that needs to be created has requirements and skills, knowledge and data are required to estimate these requirements. The maturity model basically just says: ‘you need to do your own race; you need to figure out what’s best for you and your products’. And this model is different if you are making prototypes, tooling, or end-production parts. While we recommend to start creating design prototypes and text fixtures, we also usually tell people that any destination in their maturity model is the perfect place to be.”
On a research standpoint, research activities concerning printing and post-process advanced technologies, innovative materials and design/simulation tools are gaining momentum. In this list, topics that have been raising organizations’ interest this year, often include the improvement of the design and manufacturing workflow through advanced methods and software tools, environmental sustainability opportunities of AM, advanced post-processing technologies and/or AM infrastructure for data management and cloud-based additive manufacturing. For Diegel, one area that absolutely requires focus right now is machinery:
“At the moment, most AM systems are ‘dumb’. By that, I mean that AM can actually be quite difficult to get good parts out of. All sorts of things can go wrong during the print process. The machine may not spread enough material for a layer, the layer may not fuse properly to the layer below, the part may distort while it is printing and crash the build. It doesn’t matter what technology you use; sh*t happens… But, at the moment, the AM systems do not yet have the intelligence to pick up a potential fault while it is happening, and then correct it during the print process. Many systems even have high-tech vision systems or melt-pool monitoring systems, but they don’t yet use them to take intelligent corrective action. A short feed of powder, for example, is a not uncommon occurrence in metal powder bed fusion. And, from a computer vision point of view, it is relatively easy to detect. So why do none of the systems do that and, when they pick up a short-feed, they re-spread another layer of powder to correct the error? To me, it is making the machines a bit smarter and idiot-proof that still needs a fair bit of work to greatly increase the adoption of AM for larger-scale production. And making all the systems way, way, way faster! [On another note], speed is of the essence. At the moment, one of the factors that makes AM so expensive for production is that it is incredibly slow compared to many other conventional manufacturing technologies. So, to vastly increase options, we need to see the AM systems greatly increase in speed. We are starting to see that, with companies, for example, adding more lasers to their systems, but I think we may need a bit more of a quantum boost in speed. So, whoever cracks that first will probably gain good competitive advantage.”
Barnes on the other hand believes that there is already certain movement that is happening on the machines side, at the productivity level. “The area professionals want to look at now is the digital space. There should be a lot of focus on cybersecurity and what it actually means; the digital workflow can be improved. A lot of companies are jumping into that space now and provide solutions that look different from what we’ve seen in the past. Some software solutions now enable to rectify and smooth that workflow. And this will get bigger moving forward”, he outlines.
Please keep in mind that these warnings are not meant to water down any single advances that have occurred on the AM market this year. As a matter of fact, Diegel recognizes that material producers went one step further in their development:
“Copper now seems to be a hot material in the metals area. We are also starting to see some slightly more eco-friendly polymers for powder bed fusion (SLS) like nylon 11 that is made from castor beans rather than petrochemicals. Another trend I noticed at the recent Formnext AM show, in Frankfurt, was the huge proliferation of larger-scale robot arm-based 3D printers, both for printing larger-scale polymer or metal parts”.
And all of this does not take into account the little wins at the user level.
Adoption across vertical industries – and users in general: where are we?
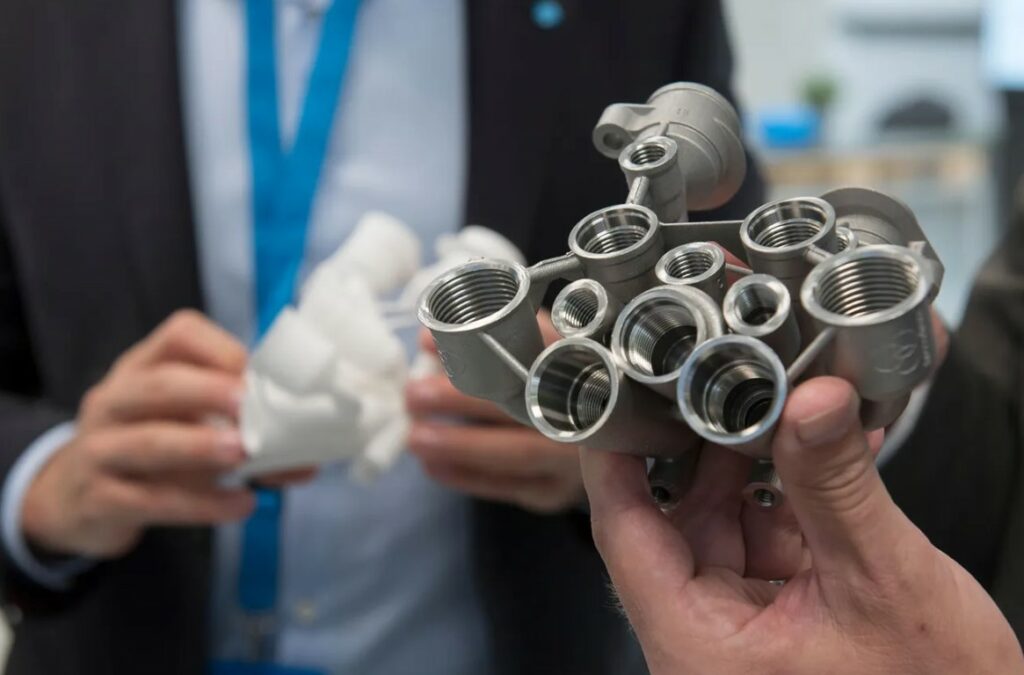
“Finally, after many years of research into materials, machines, technologies, etc. (which is definitely great and important), design for AM is starting to be appreciated as an area of core importance if we want to see AM much more widely adopted, so we are starting to see that as a growing research area”, Diegel continues. According to our expert, in addition to AM users, many professionals including machine manufacturers and machine salespeople have been overlooking this area of DfAM – while they should be the one alerting users on the importance of this concept. The road is definitely still long ahead as many companies still design for machining or injection molding; and thereafter have a mild heart attack when they are told what it would cost to print.
“If they learned to redesign it the right way, they could potentially reduce the part cost from anywhere between 25% to well over 90%. So I see a large part of our role being in educating on how to design for AM the right way, and how to add enough value to their parts, through good design, to overcome the high costs of additive manufacturing”, the professor adds.
Another thing that was also prevalent within TBGA’s exchanges with companies this year was the willingness for the latter to do it cheaper, better and faster with AM – unlike previous years were the interest was just in using AM. At that time, the only question was then: “what are we going to make”? I may be wrong but to me, asking if it can be done cheaper, better and faster might imply that users are no longer at the pre-production level. They have started exploring things that influence production and are looking to challenge the status quo of the technology. It’s about finding a better way to improve the performance of one’s product.
“The other thing we’ve noticed a lot since the pandemic is companies’ willingness to use AM to reduce risks. A lot of companies are manufacturing in distant areas and are now looking to a plan to mitigate that risk. I always tell people that if you’re a CEO of a company and you cannot address this concern, you’re going to get fired. It doesn’t mean you have to answer the question immediately, you should at least have this conversation”, Barnes continues.
While he believes these two questions will continue to fuel conversations next year, he also hopes that in terms of adoption of AM per say, the use of AM will see a lot of traction in the high-end automotive industry (EVs), and in the repair industry. This does not take into account the fact that problems around the supply chain, inflation and other energy issues will continue to prompt people to explore new solutions – and for that to happen, “we need more brains”, [irrespective of their gender and skin colour], Barnes concludes.
This interview has first been published in the November/December edition of 3D ADEPT Mag.
Remember, you can post job opportunities in the AM Industry on 3D ADEPT Media for free or look for a job via our job board. Make sure to follow us on our social networks and subscribe to our weekly newsletter: Facebook, Twitter, LinkedIn & Instagram ! If you want to be featured in the next issue of our digital magazine or if you hear a story that needs to be heard, make sure you send it to contact@3dadept.com