Autonomous driving, e-cars, digital services and more features: a lot is requested from car manufacturers who continuously need to be efficient, cost relevant and more responsive to the market’s changes. At the heart of these requests, lies the need for a cleaner, more sustainable future of both vehicle use and production, a need that XEV has well understood and is determined to address.
With over two decades in the automotive industry, Lou TIK has built up extensive experience in leading Chinese car companies where he held management positions and helped launch more than 15 cars. Despite the slow speed of 3D printing when he first discovered it, he felt it could play an important role in car manufacturing. It has been three years that TIK has founded XEV and additive manufacturing is at the heart of its production technologies. We caught up with the founder to know where the company is headed.
How did you decide that AM will be the main enabler in your production environment?
In 2015, we took part in a European competition dedicated to new mobility and production solutions. We proposed a solution that aims to drastically improve the user experience by providing zero emission with maximum freedom.
At the time, the 3D printing market had already evolved compared to what I knew in 2010 and following the feedback we got at this European competition, I couldn’t stop thinking that I must bring this technology in a new company. I therefore decided to found the company at the end of 2017 and we began our operations in 2018.
At XEV, we focus on core problems surrounding urban mobility by providing affordable, individual transport responsible for the environment.
What changed since then?
Obviously, over time, we discovered the various areas of improvements that still need to be made to make the technology viable for our production needs. So, we looked for ways to improve and automate the AM process.
Fortunately, we have built up a team that brings to the table an expertise in the main domains we must be experts in: automotive and additive manufacturing. With experts from this key vertical industry and experts from the AM industry, we are uniquely positioned to meet the expectations of the automotive market, and to develop technology solutions that take into account the manufacturing requirements.
Could you please elaborate on your manufacturing process?
Yes, sure. First, I want to point out that we co-developed FDM-based industrial 3D printers in collaboration with a partner.
The AM systems can achieve multiple tasks into one go due to the automated features that have been especially developed for the systems. One of our goals was to achieve quality printing and accuracy while achieving mass production. We put all our know-how in postprocessing and used robots in order to achieve an “injection molding look and feel”. This entire process is our key value: from manufacturing to the desired final part.
We came to realize how valuable this process is in 2019 when several automakers reached out to us to leverage our 3D printing solutions.
XEV ambitioned to mass-produce its YOYO series using AM. At what stage is the project now?
We were very ambitious at the beginning, as we wanted to produce the entire car using additive manufacturing. We came to realize that the technology was not mature enough to meet that purpose. We have therefore decided to produce parts that are usually produced via moulds with AM. Our FDM printing solutions will be dedicated to the production of parts such as the big cover of the dashboard, the inside of the front tanker, the door blade to name a few.
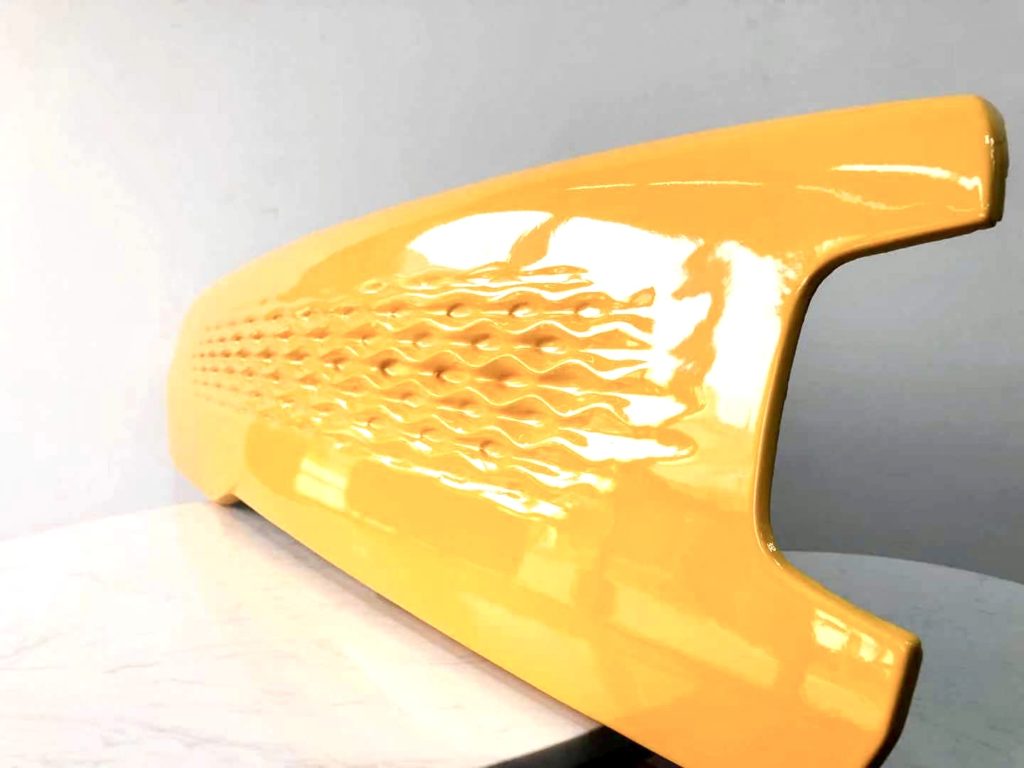
Legend: door blade – image via XEV
We will increase the database of car components that can be 3D printed and will release the 3D printable parts over time. We will give multiple choices to the customer so that he chooses the version that suits him best. We understand that not everyone wants the same thing, which is why we have implemented a modular approach that will enable to provide the customer with a tailor-made vehicle. Two from years now, we will see a full 3D printed car on the road, but we are not there yet.

Legend: frombumper – image via XEV
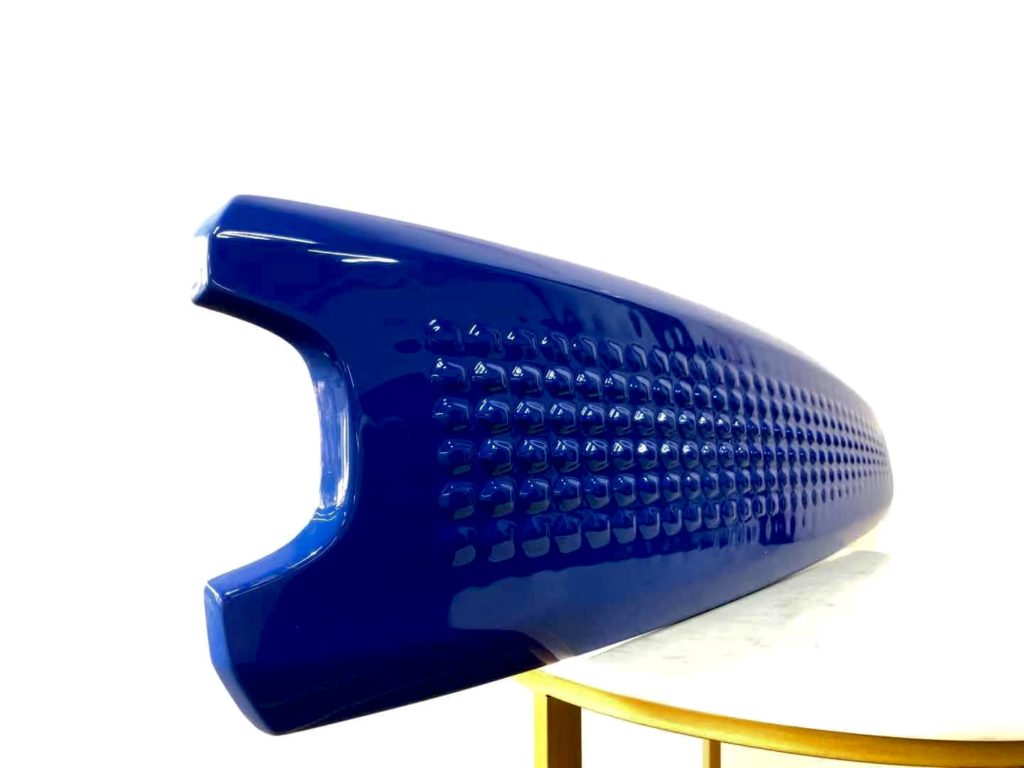
We know the company opened an innovation center in Shanghai but will the YOYO series be available on the European market as well?
The car will be for the European market first. It has been designed for the European market and its production requirements comply with the European legislation. It will probably be the much affordable car on the market (~ 10 000 €).
According to you, what challenges do designers still need to overcome at this level?
I think the big change is that there is a transition in the way designers work. With “Design for AM”, designers have more possibilities compared to the way they worked with conventional manufacturing processes. One thing they need to acquire is experience. There are so many things to master in DfAM and there are no real standard guidelines yet. Therefore, they can only reach this mastery of tools with experience.
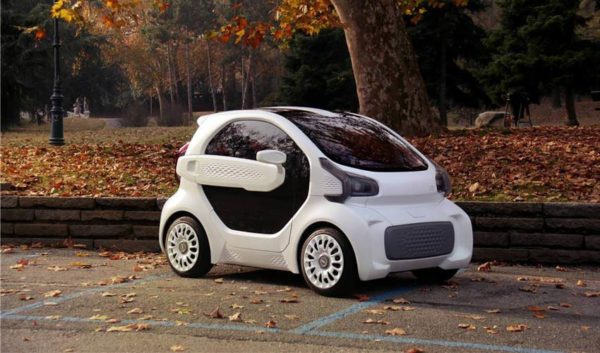
Anything else you would like to share?
I believe that even though machine manufacturers improve the AM processes, it’s up to companies like us to use the technology, explore its applications, and push its boundaries. That being said, we can’t wait to officially launch our YOYO series in the upcoming months.
This feature has first been published in the 2021 March/April issue of 3D ADEPT Mag