Designed in nTop software, produced with Origin Programmable PhotoPolymerization (P3) technology using Henkel’s Loctite 3DP resins
Following the 3D-Printed nasopharyngeal swabs and the multi-material F-16 hydraulic tube clamp, we are going to discover another application made possible with Origin’s Programmable PhotoPolymerization (P3) technology.
This time, the application will be a head lice treatment device, a device that will be produced by Enventys Partners, a product launch agency that designs, prototypes, manufactures, fulfills, crowdfunds, and markets new products and startup businesses.
For Enventys Partners, this product development is an important milestone in which initial prototyping and end-use manufacturing will be fulfilled on a single machine. The whole idea started when FloSonix Ventures reached out to the product launch company with the need to design and manufacture a new head lice treatment device offering a better user experience with improved ergonomics for technicians.
According to Enventys Partners, with a projected demand for 200-300 devices annually, each device requiring many plastic components, the costs associated with traditional tooling, injection molding, and manufacturing were unjustified. Enventys Partners turned to additive manufacturing from the beginning to achieve cost-savings without sacrificing product quality.
“The Origin One 3D printer allowed us to make several initial options for our client to choose from and then make tiny tweaks almost in real-time without delaying the project or incurring huge expenses,” said TJ Root, senior design engineer for Enventys Partners. “By prototyping on the same machine that will make the final parts, we had extreme confidence in every piece we were making.”
To meet the requirements of FloSonix Ventures, the cocktail of the perfect manufacturing process therefore requires the use of nTop software as well as production with Origin’s Programmable PhotoPolymerization (P3) technology using Henkel Loctite 3DP resins.
While the nTop software helps to design and improve device ergonomics, Enventys Partners explored several Henkel Loctite 3DP resins which include Loctite 3D 3843, IND403 and MED413, materials that can deliver toughness, temperature and color needs in a single device, while providing high part dimensional stability and good surface finish.
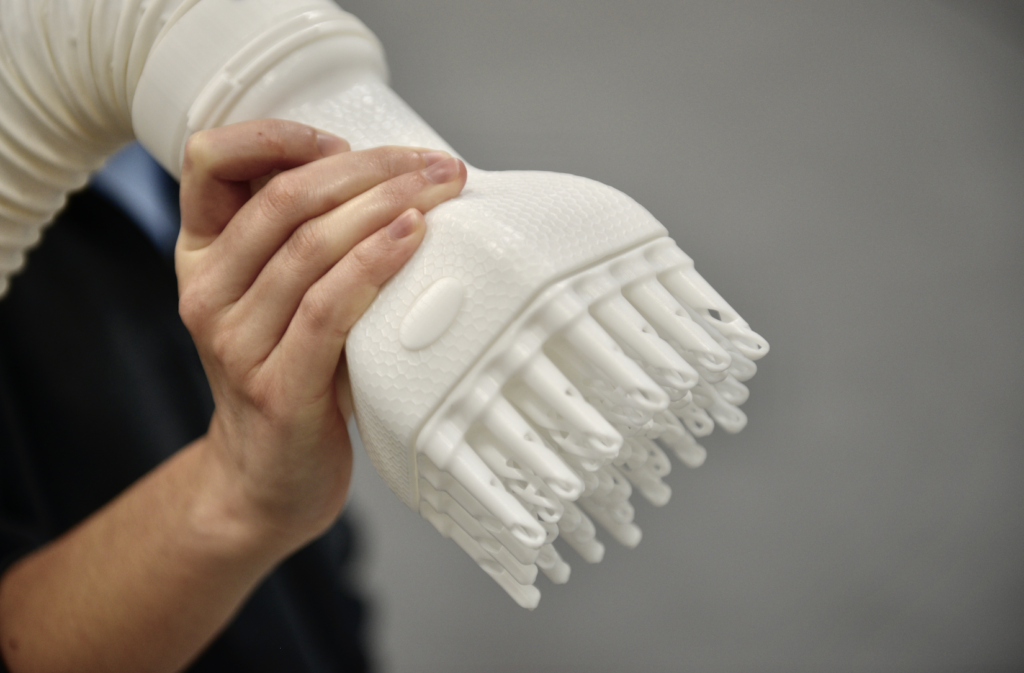
“We are excited to see this product come to market, said Ken Kisner, Henkel’s Head of Innovation for 3D printing. “This application highlights the versatility of 3DP and the multitude of applications that Loctite 3DP materials can serve.”
Furthermore, the manufacturing process on the new Stratasys company’s technology, Origin One, helps the team at Enventys Partners gain design freedom and control over the process.
This included component consolidation, adding assembly features, and final tuning parameters to achieve desired accuracy. According to Enventys Partners, with injection molding, the process would have required more parts, further assembly steps and would have certainly be more costly; not to mention that given the complexity of a complex medical device like the FloSonix, it would also have required different suppliers with multiple points of failure throughout the prototyping to production timeline.
“Enventys Partners’ approach to this application is incredibly innovative and an ideal process for any brand taking a complex mid-volume product to market quickly and economically,” said Christopher Prucha, co-founder of Origin and now the head of the Origin team at Stratasys. “By using an additive first approach; combining parts, designing custom textures, and taking advantage of Origin One’s material selection and final part quality, they’ve created a playbook for product development using additive manufacturing.”
Remember, you can post job opportunities in the AM Industry on 3D ADEPT Media free of charge or look for a job via our job board. Make sure to follow us on our social networks and subscribe to our weekly newsletter : Facebook, Twitter, LinkedIn & Instagram ! If you want to be featured in the next issue of our digital magazine or if you hear a story that needs to be heard, make sure to send it to contact@3dadept.com