Six years ago, MX3D became famous in the AM industry when it announced it could create a metal bridge using its WAAM-based robotic 3D printing technology. Since then, the Dutch team has developed a range of digital tools that can create a new form language for architectural objects.
Yesterday therefore marked the inauguration day of this 3D printed steel bridge in the oldest neighbourhood of Amsterdam, in presence of Her Majesty the Queen of the Netherlands, Máxima. Her presence reinforced the governmental role in enabling such innovation. Indeed, as many governments across the world that strive to build smarter cities, the City of Amsterdam makes no exception to this rule as it acts as a facilitator in this project.
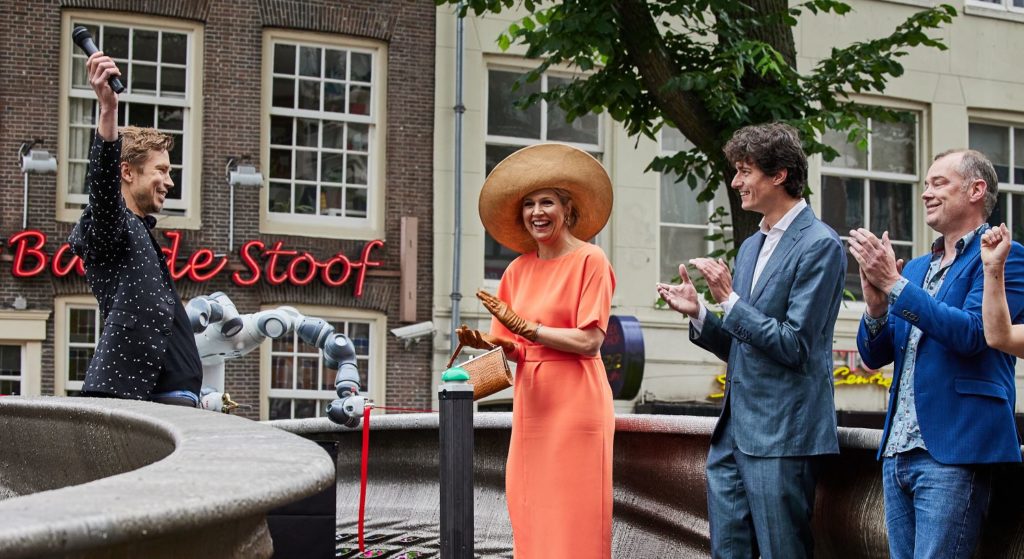
As a key partner of the project, the support of the city, stadsdeel Centrum and its CTO office were essential in making this complex project succeed. The project in turn helped MX3D to gain worldwide success with its product: a software license that turns a welding robot into a high end 3D metal printer.
Focus on the smart bridge
Designed by Joris Laarman Lab with Arup as lead engineer, the smart bridge will be placed over one of the oldest canals in Amsterdam’s Red light district.
As announced two years ago, in collaboration with academic and industry researchers, the City of Amsterdam will use the bridge’s data streams to explore the role of IoT systems in the built environment. They will explore if they can use such systems to anonymously analyse crowd behaviour, to help better understand the impact of tourism in the Red Light District. The project also addresses questions about open data, data ethics, and citizen ownership of city analytics. For this purpose, the bridge was granted a two year permit by the city of Amsterdam.
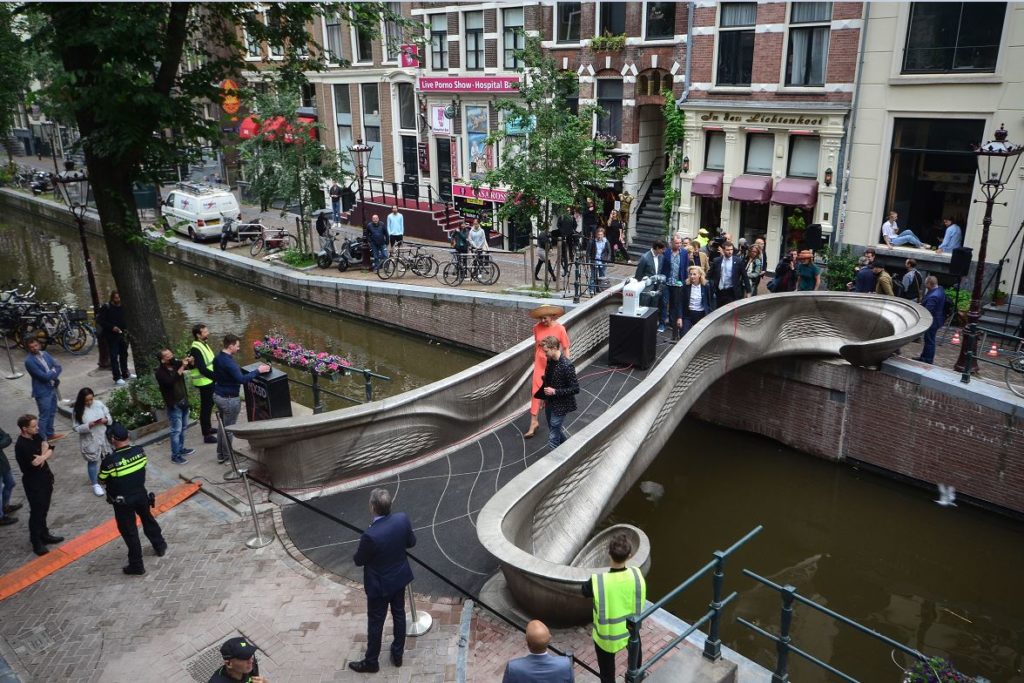
To achieve this vision, required an extended collaboration between MX3D, The Alan Turing Institute (the Turing), Arup, Autodesk, FORCE Technology, and the University of Twente. Between them, they have spent the last three years creating and installing a sophisticated sensor network, to enable real-time data collection, to represent those data flows in live models, and to create usable analytics on top of that data which feeds into a Digital Twin of the bridge.
A press release explains that a team of researchers from Autodesk designed bespoke software and served as the primary systems integrator for the smart bridge. Autodesk software collects data from the sensor network and visualises it in a digital twin model representing the bridge’s response to use in real time. Autodesk worked closely with the partners of the Data Centric Engineering Programme at the Turing as well as FORCE Technology and University of Twente to design and install the sensor network. Even in its prototype form, this network was useful when performing structural testing on the bridge. Load testing and materials testing were both conducted by the Data Centric Engineering team, which proved that the bridge is able to hold at least a 19.5 ton load, well above its ultimate design load.
The UK’s national institute for data science and artificial intelligence (AI), the Turing, began its involvement with the bridge by assembling an interdisciplinary team of data science and AI experts from its Data Centric Engineering Programme. The Turing is hosting the bridge data for the full two year period covered by the bridge’s current operating permit and has conducted a thorough ethics review of the project to ensure that the scientific goals of the project do not compromise the privacy of the public. Using a custom data platform, the Turing supports researchers who require access to the sensor data stored in its secure cloud. The Turing researchers have expertise to develop novel and advanced digital twin models for prototypes of the MX3D bridge and are now applying these techniques to evolve the digital twin of the physical bridge as it is used.
“The Bridge is only the beginning for our technology, by now MX3D has introduced its metal printing tool on the industrial market, and with this tool already many companies have started printing like us. I am looking forward to all positive impact and new ideas our client will realize”, Says Gijs van der Velden, CEO MX3D.
The NOW furthermore funded a project called ‘BRIDE’, in which University of Twente, TU Delft, Amsterdam Institute of Metropolitan Studies and MX3D study the social side of a digital world, like the bridge. What do citizens want from smarter infrastructures, do they even want it? What are the ethical boundaries data collection should adhere to? Should a city collaborate or even be in the lead? How can we design the data sharing equitably?
Remember, you can post free of charge job opportunities in the AM Industry on 3D ADEPT Media or look for a job via our job board. Make sure to follow us on our social networks and subscribe to our weekly newsletter : Facebook, Twitter, LinkedIn & Instagram ! If you want to be featured in the next issue of our digital magazine or if you hear a story that needs to be heard, make sure to send it to contact@3dadept.com