The capabilities of pellet 3D printing are yet to be discovered. In a recent collaboration with Model No., a designer of modern and sustainable furnishings in the US, 3D Systems EXT Titan™ Pellet solution was leveraged to 3D print on-demand furnishings in a very short deadline.
As a reminder, Titan™ Pellet was developed by Titan Robotics, a company 3D Systems acquired two years ago, to expand into pellet extrusion 3D printing. The 3D printer can print medium-to-large formats as it features a build volume of 1070mm x 1070 mm x 1118 mm (42’’ x 42’’ x 44’’). In general, pellets enable industrial production with lower costs, faster print times, and a wide range of material options.
In this specific case, by relying on recycling sawdust and transforming other plant waste into materials suitable for 3D printing, Model No. aims to achieve a zero environmental impact throughout the production chain.
By 3D printing with pellets on EXT Titan Pellet systems, Model No. has been able to use its own sustainable bio-resin compounds while dramatically increasing deposition rates to produce products faster.
« Endless Loop: From Waste to Wanted »
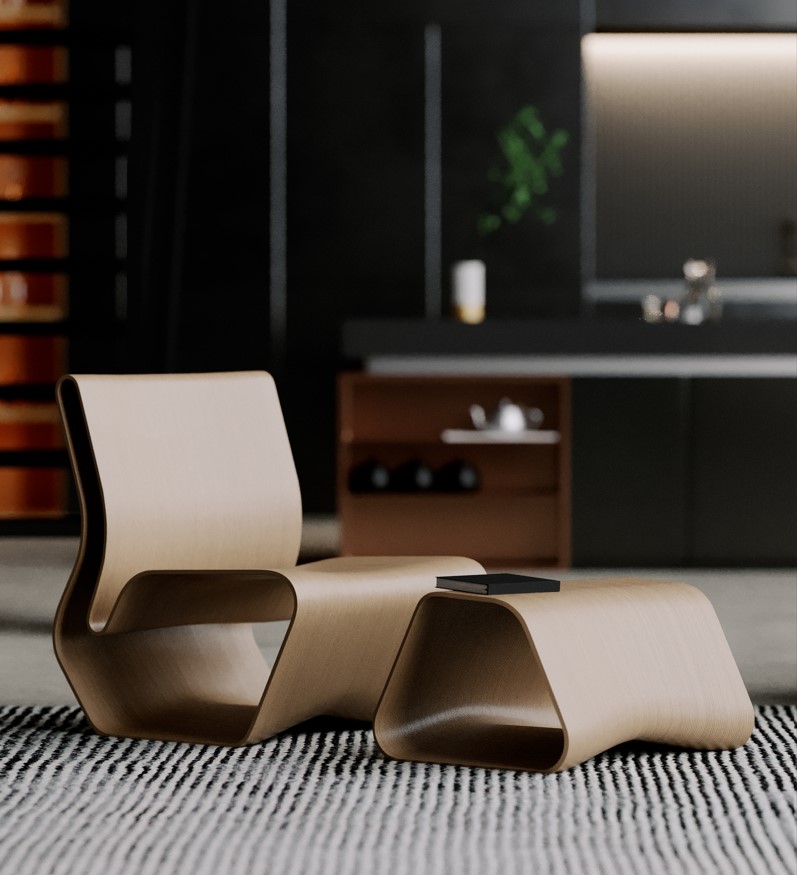
As part of their collaborative project “Endless Loop: From Waste to Wanted”, Model No. and a small number of design partners developed a collection of entirely circular, zero-waste products. They sourced reclaimed wood from the Bay Area (California) to create furniture using their CNC machine.
The sawdust waste from CNC milling was used to make 3D printable bio-resin pellets. The recycled wood-based PLA pellet material was then used to print unique furniture and art pieces that complemented the wood pieces while neutralizing the environmental impact of subtractive milling.
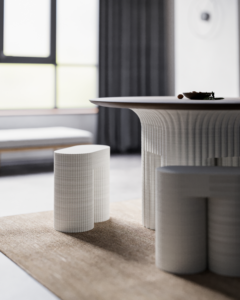
Whether 3D printing with bio-based resins, machining wood or sewing fabric, all the materials used by Model No. in its products are regenerative, biodegradable, recyclable and certified sustainable. All the company’s resins are formulated from recycled plant waste that can be composted in as little as 5 years. To make the process entirely circular, Model No. is also working on a recycling program that enables its customers to recover and reuse its products at the end of their life cycle.
According to Philip Raub, CEO de Model No. , in the near future, these technologies will enable their customers and partners to develop solutions for end-of-life products. In the meantime, they also offer them “a take-back program.” And everything they manufacture generates no waste, because they use 3D Systems’ large-format 3D printers, which generate virtually no waste and are solar-powered.
Remember, you can post job opportunities in the AM Industry on 3D ADEPT Media for free or look for a job via our job board. Make sure to follow us on our social networks and subscribe to our weekly newsletter: Facebook, Twitter, LinkedIn & Instagram ! If you want to be featured in the next issue of our digital magazine or if you hear a story that needs to be heard, make sure you send it to contact@3dadept.com