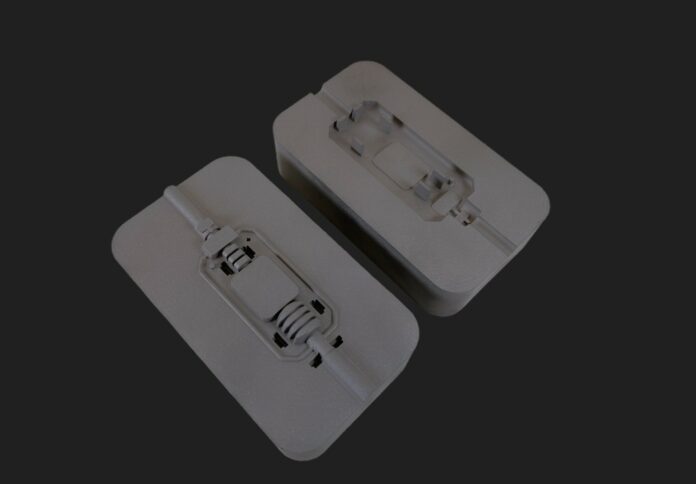
Remember Mantle? a manufacturer who turned stealth mode off in 2021 with the launch of TrueShape, a hybrid bound metal printing solution that processes metal pastes and that is specifically designed for tooling applications?
Since its launch, the company has been adding shaping capabilities to its solution while exploring new applications it can achieve with (new) customers.
On the heels of Westminster Tool that we discovered two years ago, Spectrum Plastics Group, a DuPont Business and medical contract manufacturer, Heyco Products, a Penn Engineering company specializing in wire protection and termination for a range of industries, or even General Pattern, an injection molder with in-house tooling services are other companies that have been exploring the capabilities of TrueShape.
Those customers reveal that Mantle’s solution could be ideal for medical device tooling, or to increase one’s toolmaking capacity and project speed by automating a portion of the toolmaking process.
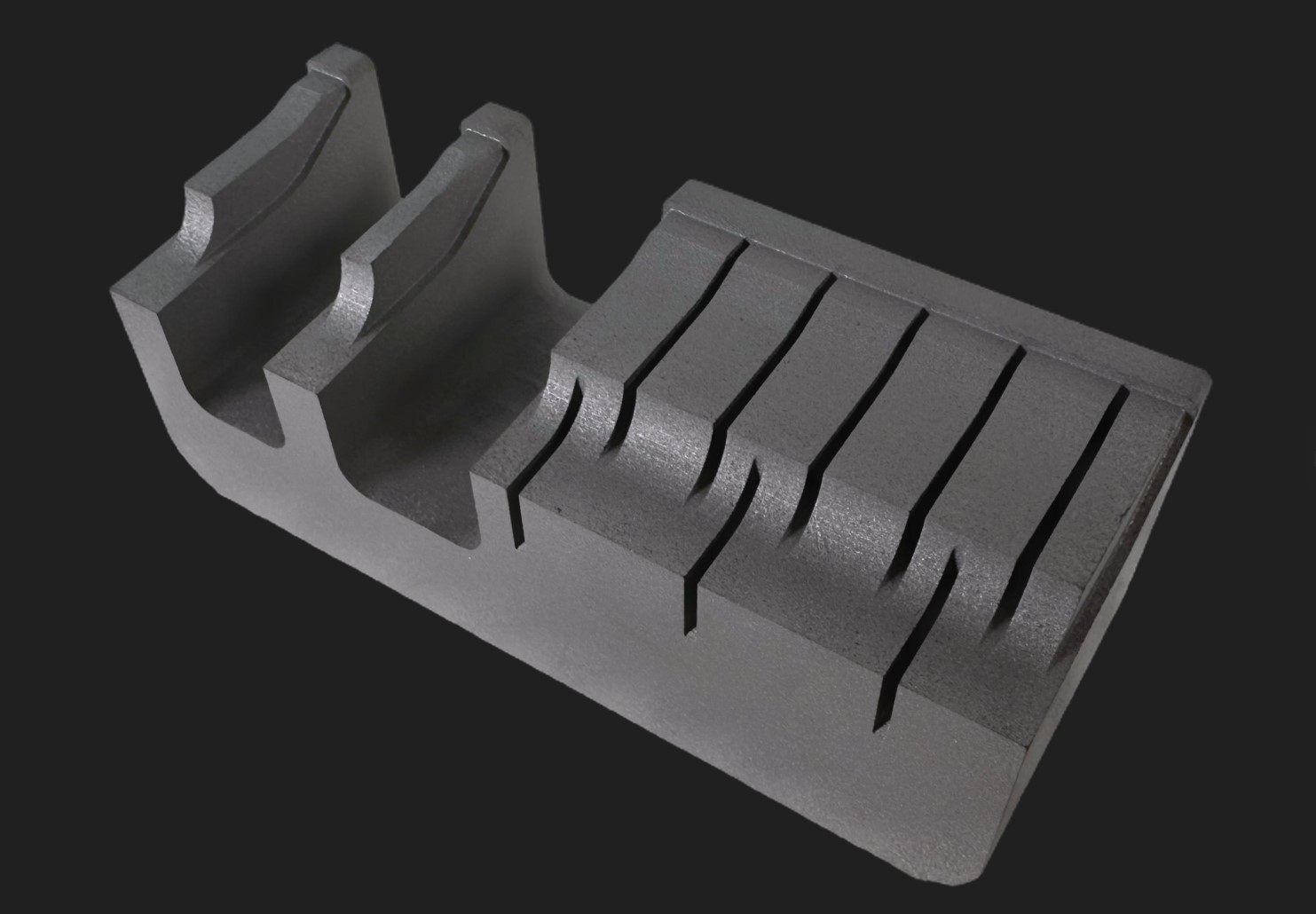
Beyond these manufacturing objectives, the technology would help address a shortage of tool makers.
Across manufacturing as a whole, especially in toolmaking, labor scarcity has emerged as a predominant challenge, hindering manufacturers’ efficiency and capacity to build tooling. Recognizing the growing scarcity of skilled toolmakers, General Pattern decided to automate its toolmaking processes and bolster capacity by relying on Mantle’s 3D printer.
The investment in Mantle underscores the company’s dedication to cutting-edge technologies and highlights its potential to alleviate the industry’s labor shortage. General Pattern anticipates the benefits of this investment to include heightened efficiency, decreased reliance on specialized labor, and improved customer service through faster and more efficient operations, a press release reads.
“Introducing Mantle into our operations has elevated our approach to toolmaking. With the simple press of a button, we can now effortlessly create tools, which completely changes our ability to tackle labor challenges and enhances our capacity to better serve our customers. Recently with a slide for a transportation trim component, for example, we skipped the finishing process entirely. Instead, we printed it, assembled it into the mold, and immediately began molding parts. This not only saved us the 40 hours of traditional toolmaker time typically required to build this slide, but also freed up my team to focus on other critical projects,” Denny Reiland, CEO at General Pattern.
Remember, you can post job opportunities in the AM Industry on 3D ADEPT Media for free or look for a job via our job board. Make sure to follow us on our social networks and subscribe to our weekly newsletter: Facebook, Twitter, LinkedIn & Instagram ! If you want to be featured in the next issue of our digital magazine or if you hear a story that needs to be heard, make sure you send it to contact@3dadept.com