A joint-project carried out by European Space Agency (ESA), OHB System AG as well as Austrian manufacturers Incus and Lithoz GmbH will develop and test 3D printing in a micro-gravity environment.
As a reminder, Lithoz is a founding company of Incus – that could provide here its expertise in a gravity environment given its recent experience with the ISS. Incus on the other hand, develops a Lithography-based Metal Manufacturing (LMM) process that turns 3D files into prototypes and small-scale production of components in MIM (metal injection moulding) quality.
As you may know, micro-gravity environments usually raise several challenges in terms of constant supply of goods, research materials and equipment, as well as eventual spare parts in case of any failure of individual components..
With the goal of enabling long-term self-sufficient missions, the space experts from the ESA want to explore the use and reuse of both existing lunar surface materials and recycling of lunar base materials, derived from production waste and end-of-life items.
The fabrication of required items and spare parts, on board and on demand, has proven to be a viable alternative to reduce transportation costs and volume of cargo missions from Earth, as well as minimize production waste.
As far as this project is concerned, Incus explains that its technology can produce spare parts from recycled metal waste, which could enable the utilization of recycled powders from scrap metals that are available on the Moon. A press communication also states that in contrast to the currently predominantly used direct metal laser melting techniques, the LMM process uses a paste or suspension as feedstock and does not rely on the use of highly spherical gas-atomized powders or support structures. The production of dimensionally accurate components separated by the thermal demolding process does not require any time-consuming, mostly manual reworking and is completely safe for the operator.
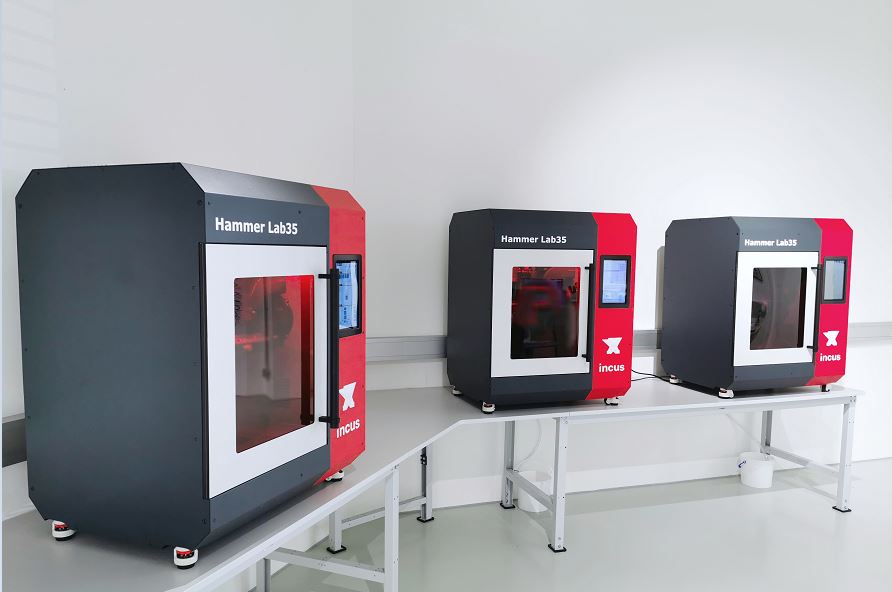
The team of this project therefore has 18 months to assess the feasibility of processing scrap metals available on the Moon’s surface to produce a high-quality end-product via a zero-waste process.
It goes without saying that all constraints of a space environment should be taken into account here. They include for instance, considering the potential contamination of the metal powder with lunar dust. Furthermore, a deep assessment of the influence of impurities on the sintering and result of the final microstructure will lead to optimization of the binder quantity and type, as well as the development of a sustainable manufacturing chain in space.
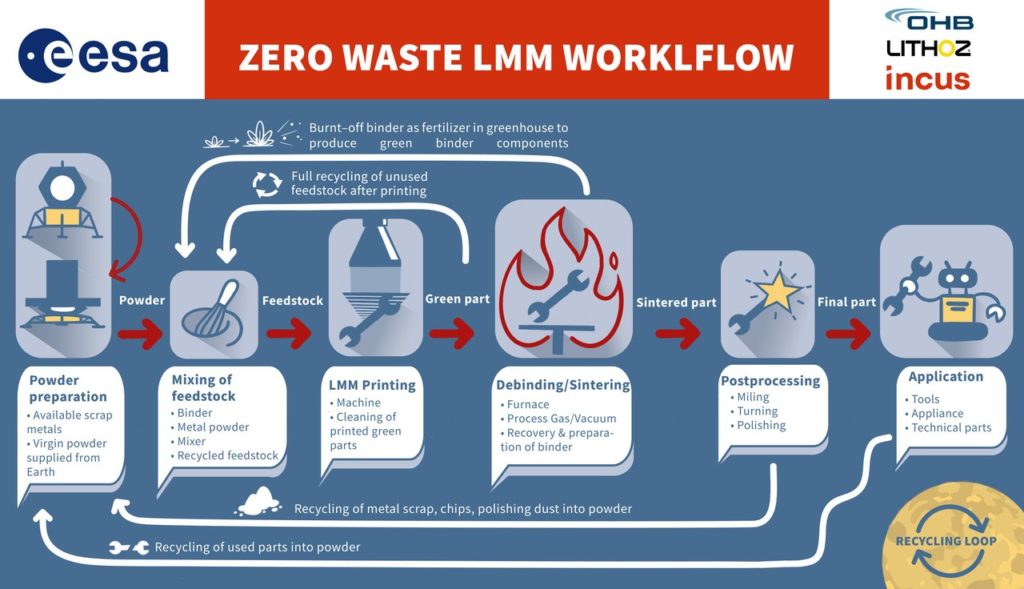
Antonella Sgambati, Human Spaceflight System Engineer at OHB System AG, states: “The possibility of reducing our dependency on Earth by utilizing existing lunar surface materials and recycling lunar base scrap metal represents the only solution to guarantee a sustainable settlement. This project and this novel LMM process will be important steps in making such a settlement a reality due to the fact that this technology could have a chance to operate successfully in space.“
Remember, you can post job opportunities in the AM Industry on 3D ADEPT Media free of charge or look for a job via our job board. Make sure to follow us on our social networks and subscribe to our weekly newsletter : Facebook, Twitter, LinkedIn & Instagram ! If you want to be featured in the next issue of our digital magazine or if you hear a story that needs to be heard, make sure you send it to contact@3dadept.com