
Most of the issues addressed in the additive manufacturing industry often concern software or materials. That is understandable because software and materials play a key role in improving the production process of a part, but a successful additive manufacturing of a functional part also depends on other external elements in the environment: gases.
For several reasons and often unconsciously, gases are given second-rate treatment and yet, their presence in the production environment might have an impact during and after the additive manufacturing process.
While we have (almost) no control over the air we breathe, in the additive manufacturing industry, companies like Linde are trying to “manage what seems to be out of control”, in order to allow manufacturers to have a successful additive manufacturing process.
How do they do it? Pierre Forêt, Additive Manufacturing specialist and Head of the AM unit at Linde addresses this issue in this #OpinionoftheWeek.
Linde is an international German group that specializes in gases and engineering. The company has positioned itself in the additive manufacturing arena in the same way as Air Liquide or Praxair.
Although the company was created in 1879, Pierre Forêt tells us that he has been working there for over 10 years, and for the past 4 years, he has been leading the additive manufacturing unit of ten people, dedicated to providing solutions for industrial gases for the AM market. Apart from its subsidiaries in Europe and America, the Munich-based company has a facility that features the necessary equipment and technologies that enable Pierre Forêt and his team to achieve this goal.
When and why Linde entered the AM industry?
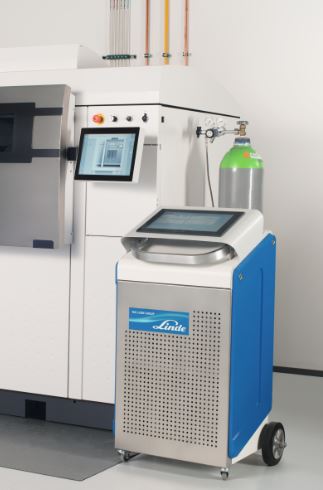
Linde produces gas molecules (oxygen, argon, etc.) that are used in many processes. In the case of additive manufacturing, inert gases such as argon or nitrogen are often enrolled in the production environment.
What’s interesting is that, when we look at the complete value chain, the role of gases is not quite often well perceived and yet the production process involves them. For instance, the powder used as material in the 3D printer has been produced with a big amount of gases. The production process itself involves the presence of gases in the production environment and even during the post-processing stage, a process called Hot Isostatic Pressing utilises temperatures in a contained high-pressure atmosphere to eliminate internal porosity and voids within cast metal materials and components. Basically, Hot Isostatic Pressing process is used in high end applications to compact the part.
As gases play a key role at different stages of the production process, our role is to develop gas technologies that will complement AM systems in order to ensure a good manufacturability.
Developing gases for various sectors of activity has been our core business for decades, but since 2016, given the growth of the AM market, we have decided to hire in-house experts and to dedicate a complete unit to this sector in order to best support our customers.
How would you explain the role of gases in AM?
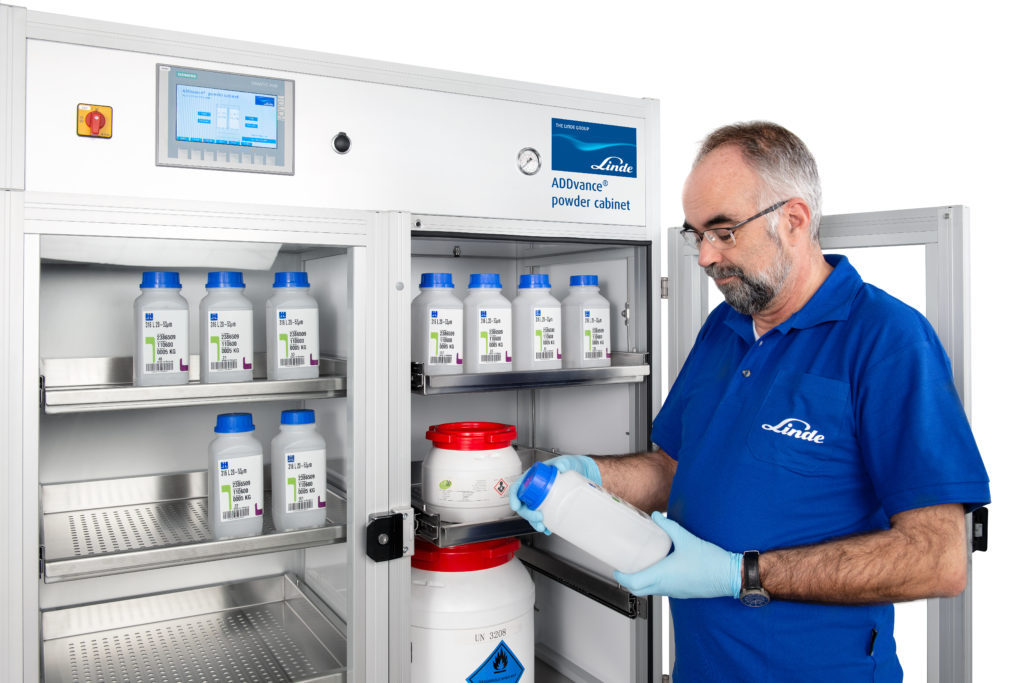
AM is still a young technology. Many customers in the automotive, aerospace and even the medical industries successful achieved their applications thanks to additive manufacturing but the usage of this technology remains quite small compared to applications performed with traditional processes.
A hundred years ago, people were keen on using the welding process. At the very beginning, they did not care about the quality of gases they were using; cheap gases with a lot of impurities. Over time, they realized that if they use the appropriate gas mixture, they could increase the productivity and the quality of the welding process.
The same phenomenon can be seen in the AM industry. AM has been used for several years now but lately, professionals have become aware of the influence of gases on the aspect of the final part. Our role is therefore not only to raise awareness on the presence of gas molecules but to develop solutions that might facilitate their use.
Could you tell us more about the ADDvance® powder cabinet and how it ensures metal powder integrity for additive manufacturing?
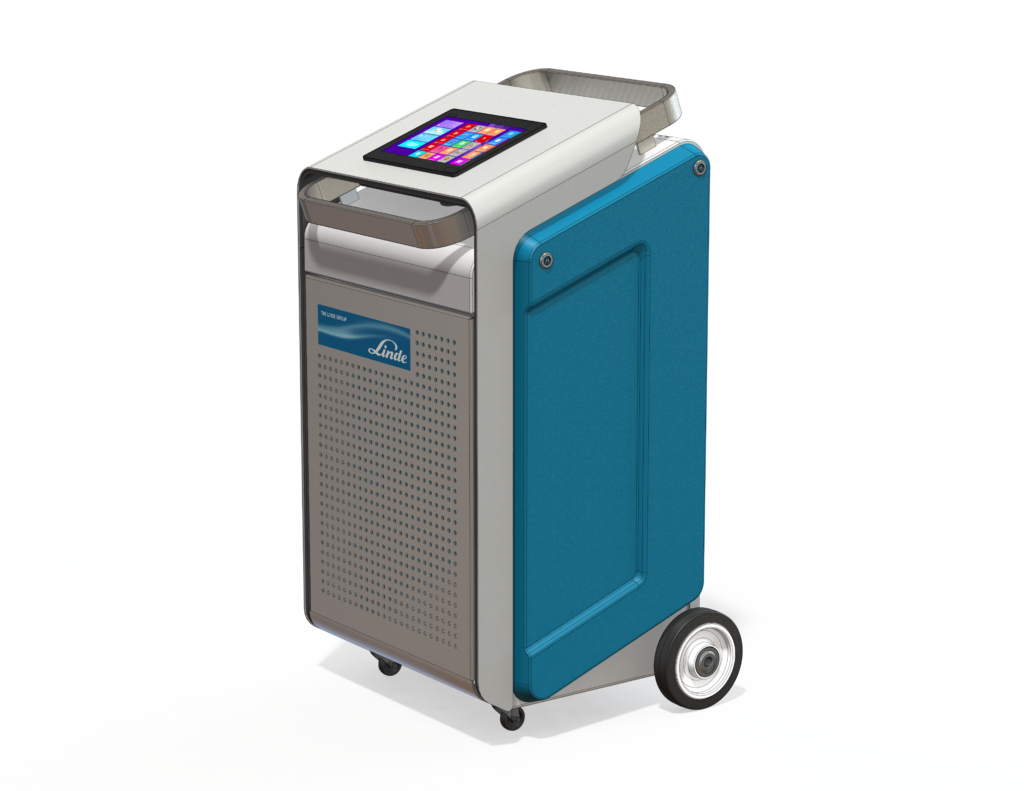
One of our customers worried about the purchase of an extremely expensive powder, the titanium (its price can go up to 300€ per kg) and he needed a lot of powder for a process. The only thing is that, in addition to be expensive, the powder is very sensitive to humidity, which means that it is easy to lose the essence of the powder; and that will definitely impact the printing process.
In order to avoid this waste of money, the ideal solution was to develop a system that could both spur the powder and remove humidity. That’s how we have developed the ADDvance® powder cabinet that contains neither air nor humidity.
The storage solution functions with a moisture control and monitoring feature that enables to continuously measure humidity levels. It releases a great amount of purge gas flow as soon as the doors are closed to rapidly remove moisture in the air. It then applies a lower stream of gas to ensure a consistently low level of humidity. So, there is no quality loss.
You have recently signed a partnership with GEFERTEC. What will be your role in this partnership? What’s the aim of the project?
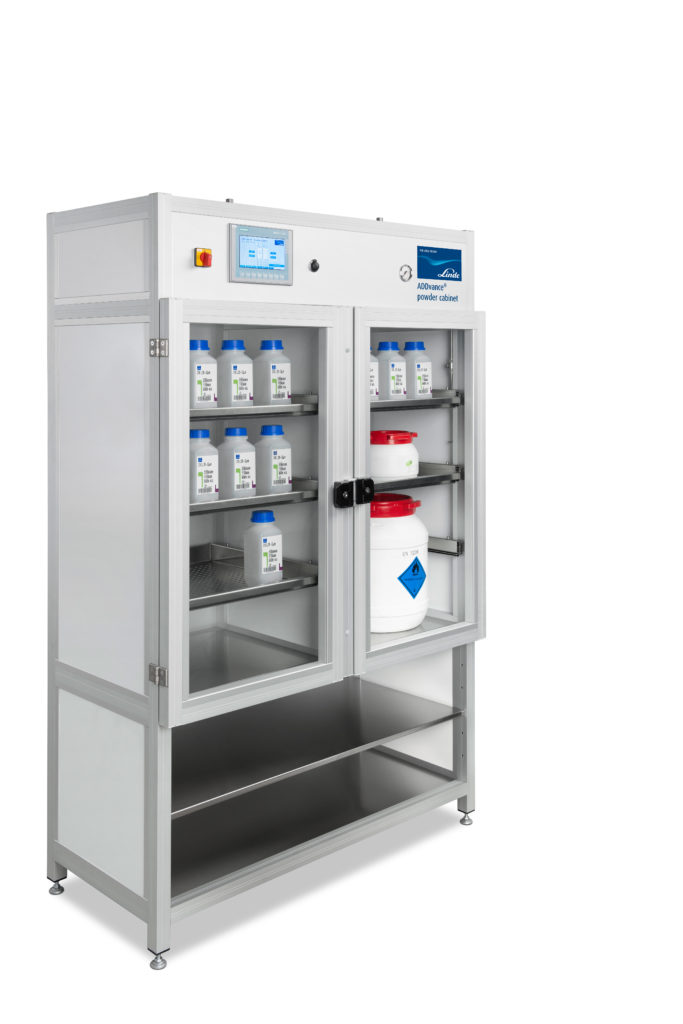
We started this project last year with GEFERTEC and other partners. This project is based on Gefertec’s 3D Metal Printing process (that use a wire and an arc vs laser and powder in the Laser-Powder Bed Fusion process) and the goal is to enable the production of large parts in a short time.
In this project, we will be looking at the production of titanium parts and as explained earlier, gases play a key role in the use of this wire. Indeed, it is a material whose usage is convenient when it is combined with appropriate gas mixtures. And Linde comes into play at this stage.
Your last word?
We will communicate more on our R&D activities and show the community our results on the influence of oxygen inside a 3D printer. We have several projects that are ongoing with titanium, nickel-based alloy and other materials. I believe our opinion in this matter will help the community to bring AM to a more robust level.
For further information about 3D Printing, follow us on our social networks and subscribe to our newsletter
Images: courtesy of Lidne – Would you like to subscribe to 3D Adept Mag? Would you like to be featured in the next issue of our digital magazine? Send us an email at contact@3dadept.com
//pagead2.googlesyndication.com/pagead/js/adsbygoogle.js (adsbygoogle = window.adsbygoogle || []).push({});