Traditional suspension component design has been largely constrained by the limitations of subtractive manufacturing methods, leading to inevitable compromises in design complexity and system integration. Additive manufacturing, however, breaks these bounds, offering engineers unprecedented freedom to pursue innovative designs for suspension systems, particularly in the structuring of uprights.
The article below emphasizes how AM enables system-wide integration and optimization, tailored vehicle dynamics through design innovation, and advances in materials through new applications.
Additive Manufacturing technologies enable the design of suspension uprights not just as isolated components, but as essential elements of a cohesive vehicle system. AM facilitates the merging of multiple parts into a unified, complex assembly. This integration, exemplified by the merging of motor and gearbox elements directly within the suspension uprights, significantly reduces part count, curtails weight, and optimizes space—enhancing vehicle dynamics profoundly.

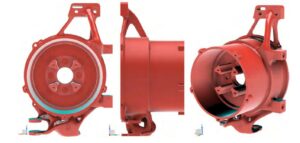
AM’s impact on vehicle kinematics is transformative, allowing for intricate geometries and integrated designs that advance wheel control and stability, critical for high-performance racing. The technology’s precise control over material deposition also enables engineers to refine stiffness and damping characteristics, improving handling and driving predictability.
As for materials, both polymers and metal alloys can be customized to display properties that meet specific performance needs, such as optimal strength-to-weight ratios essential for racing. AM’s design freedom allows engineers to explore innovative lattice structures and internal geometries that maintain strength while reducing mass.
Additive manufacturing transcends its role as a mere production technique to become a pivotal element in automotive design and manufacturing. By adopting AM in suspension design, automotive engineers can achieve an integration and performance level previously thought unachievable. As AM technology continues to advance and become more accessible, its integration into automotive manufacturing is expected to accelerate, redefining industry standards for vehicle performance and efficiency, particularly in the racing sector.
This new manufacturing paradigm not only fosters the ongoing enhancement of vehicle performance but also promotes a more innovative approach to automotive design, signaling exciting prospects for future developments.
Reference:
[1] Jesus Peraza-Garcia, Comparing and Contrasting the Merits of Additive Manufactured Electric Vehicle Suspension Components: GFR Case Study, Master Thesis, Oregon University, Mar2024 – Copyright © 2018 Oregon State University – Licensed under the Apache License, Version 2.0 – Images and research are available to download here: https://ir.library.oregonstate.edu/concern/parent/0v838860f/file_sets/zc77sz67j
About the author:
This article has been written by Stephanie Giet, PhD. Giet spent the last 12 years working with metal additive manufacturing (AM), particularly for aerospace.
More recently, she validated the full AM value stream to manufacture, qualify and certify AM parts for commercial flight with EASA. Today, she shares technical insights into the use of metal AM technologies and their applications to industrial products.