In the automotive industry, a great deal consists in producing not only a performant part but also a lighter one. A recently launched modular system for automotive tooling enables to address this issue. Indeed, the mix of carbon fiber beams and unique 3D-printed elements leads to jigs and inspection fixtures that are 90% lighter than traditionally manufactured tools.
Launched by Rapid Fit, a tool manufacturer and subsidiary of Materialise, the company used 3D printing to manufacture the mounted forms, mounting points as well as the frame connectors.
The advantage of lightness
Thanks to lightness, it becomes easier and quicker for one person to operate and move the fixtures without using heavy equipment.
Remember the features of the carbon fiber presented in the April issue of 3D Adept Mag (Page 34). It integrates all current standards in terms of functionality, precision, stability, and stiffness. Furthermore, it minimizes thermal expansion; therefore, is suitable for applications such as measuring rooms, production environment as well as climatic chambers.
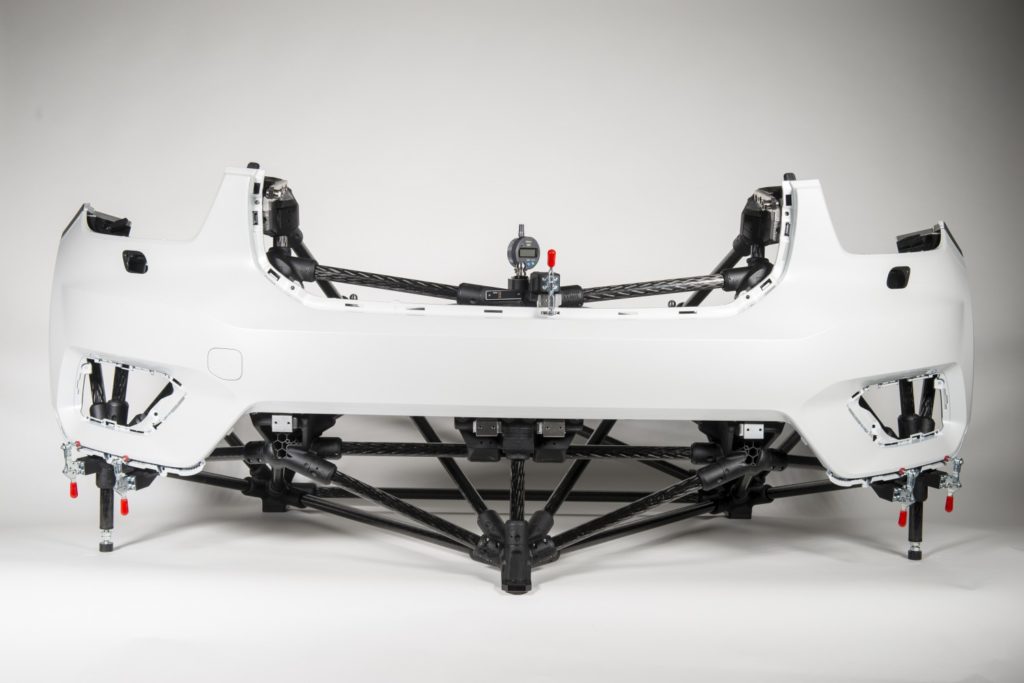
The use of Additive Manufacturing by Rapid Fit “wherever necessary makes it possible to develop solutions for very complex forms and integrated functionalities. Snap fits and clips that can be detached again increase repeatability and improve the representation of the part environment. The utilization of standardized parts that can be used again saves costs in the long run.”
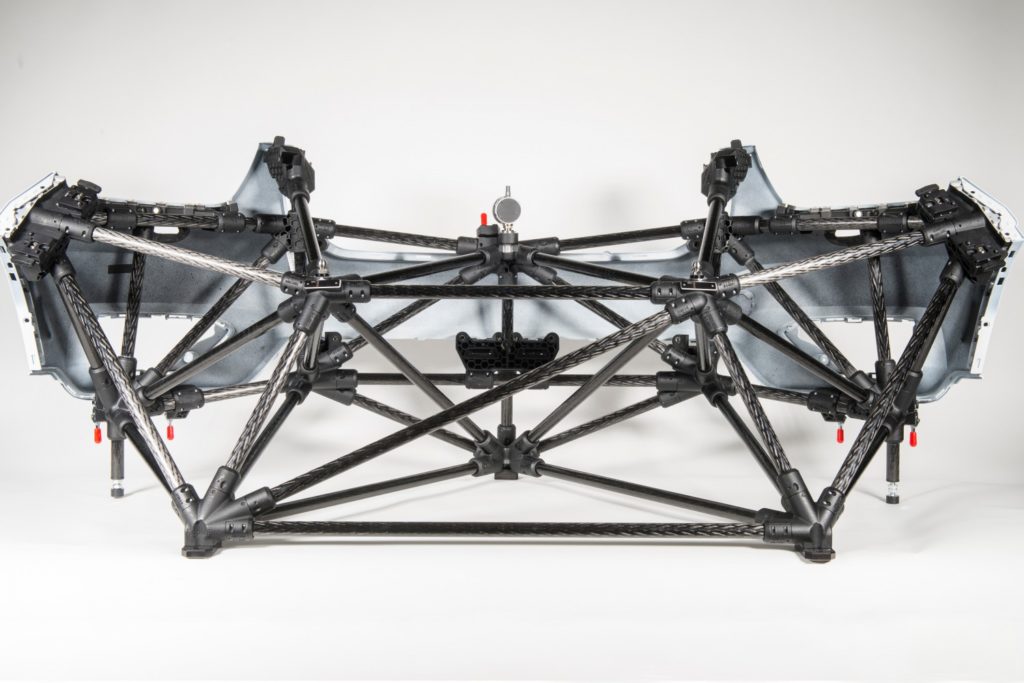
Lastly, technically speaking, the Rapid Fit’s team used CAD data and a parametric library to manufacture a jig. The parametric library is a big advantage in terms of customization and time saving. After the production of the parts by Materialise, they are mounted onto the framework and calibrated with a high-end coordinate measuring machine (CMM).
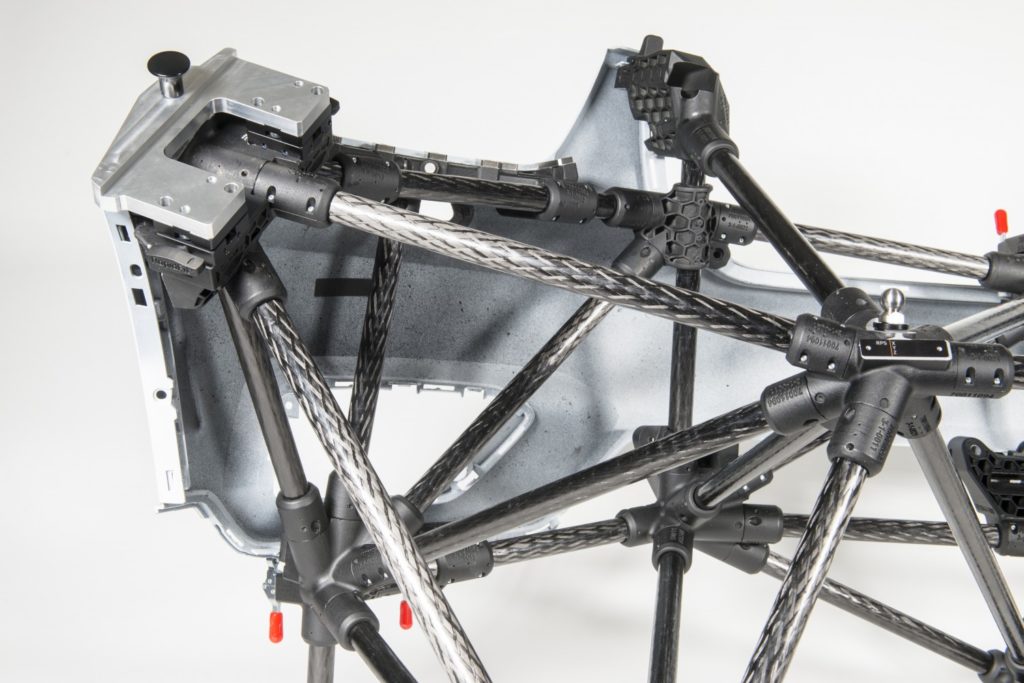
For further information about 3D Printing, follow us on our social networks and subscribe to our newsletter!
Would you like to be featured in the next issue of our digital magazine? Send us an email at contact@3dadept.com
//pagead2.googlesyndication.com/pagead/js/adsbygoogle.js
(adsbygoogle = window.adsbygoogle || []).push({});