One of the most advanced methods in additive manufacturing is Cold Metal Fusion, a solution developed by Headmade Materials, to create metal 3D printed parts from SLS 3D printers. As a reminder, Cold Metal Fusion is not a 3D printing process but a solution that can be combined to SLS 3D printers to help produce metal 3D printed parts.
Recently, SLS 3D printer manufacturer Sintratec provided a detailed guideline on how to use the Cold Metal Fusion process on its Sintratec S2 3D printer for final metal parts preparation.
Here’s how you can make lightweight automotive gear using a CMF process and an SLS 3D printer from Sintratec
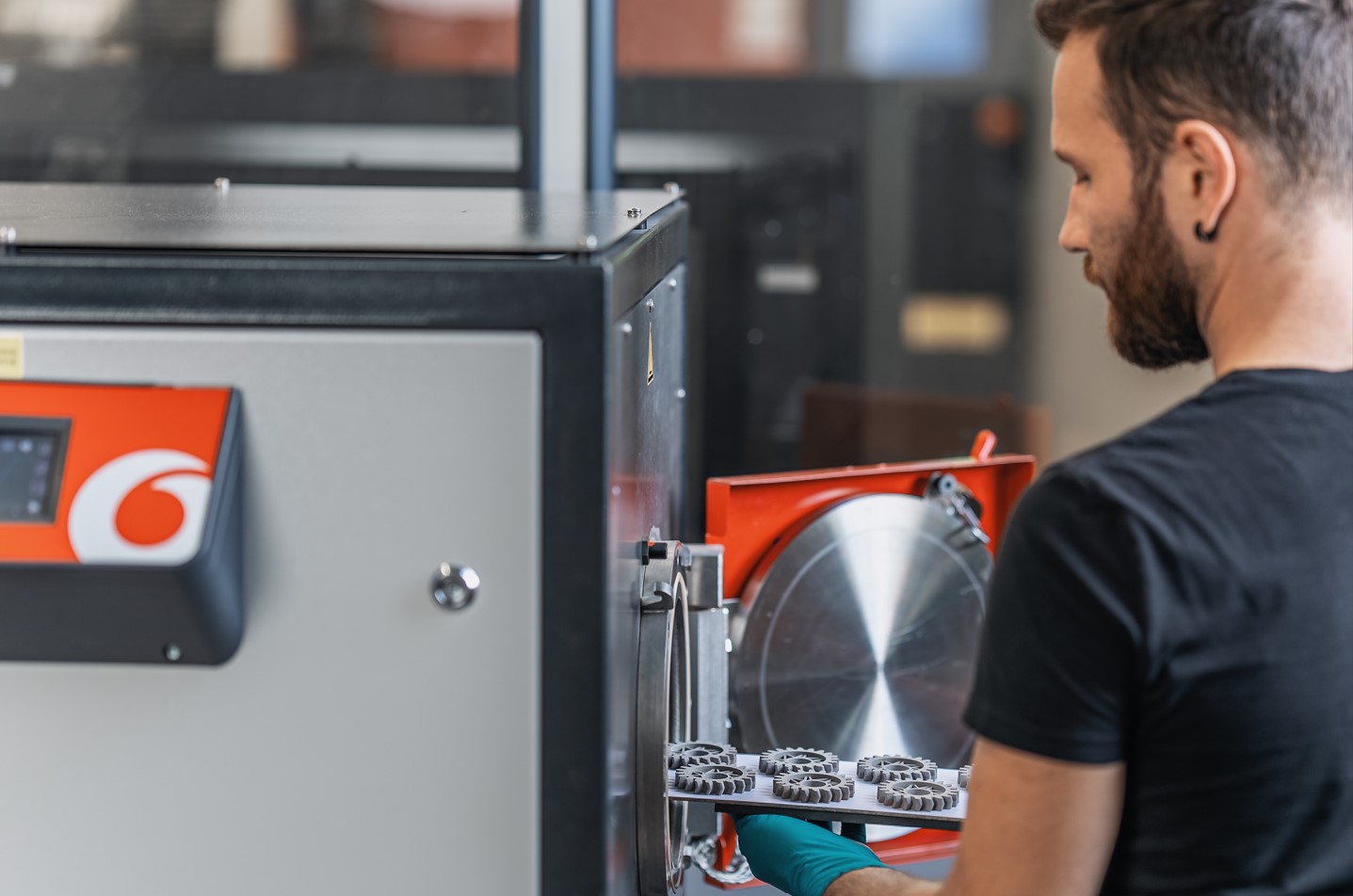
The 3D printing process starts by identifying the intricate geometry of the lightweight part and then using Sintratec’s All Material Platform for the purpose. The Sintratec S2 and the MCU-160 Build Module are used for 3D printing lightweight automotive gear.
The M2 tool steel and 17/4PH stainless steel created by Headmade Materials for SLS technology are the only two materials available in the CMF machine to make the metal part. However, Sintratec in its guideline advocates the use of 17/4PH for the automotive gear 3D printing.
The first step is “print job preparation” where similar to the standard selective laser sintering (SLS) process is first prepared inside the Sintratec Central software. Once it’s done the 3D model is imported, duplicated and arranged to build up the volume. At this moment beware of shrinkage of the CAD design in the sintering stage. This varies as per the material, for 17/4PH it’s 14 percent.
After the set up is done the print job should be sliced and exported to the system through a USB drive or local network. Then the Material Handling Station’s build module’s powder containers are filled with Headmade 17/4PH material by automatically calculating the amount of powder.
The second step is “printing and depowdering” where a Sintratec S2 is used for the Fusion Module. First, the print job is selected to start the 3D printing using the touch screen. Since it’s a Cold Metal Fusion process, the powder bed is kept at a much lower temperature (50°C) than the conventional polymers to stabilise the 3D printing process and reuse unsintered materials. Similar to the polymer process, the build mode is removed to depowder the green parts in the material handling station.
The third step is “post-processing” where the last bits of powder that remained after depowdering are removed in the washing station with a 30 bsr water jet, ensuring a smooth finish with high accuracy of 3D printing. This step is crucial in additive manufacturing as green parts are very brittle and need to be handled carefully. The plastic binder matrix with metal spikes sticking out of it makes the green parts more prone to breakage. The green part achieves a high strength status when the plastic melts and fills the cavities at the printing stage.
The fourth step consists of “debinding the green parts” by loading them onto a tray and taking them to the debinding station. The acetone solvent in the debinding chamber penetrates the green parts’ walls and starts extracting the plastic components as the solvent floods the chamber with gradually rising temperature. The parts are removed for further processing after a night of debinding and at this stage they are called “brown parts”.
In the fifth stage called the “Sintering Brown Parts”, the brown parts are transferred to a sinter furnace while the chamber is heated to more than a thousand degrees to let the metal particles form a dense metal part and burn away the last bits of plastic. Irrespective of the furnace size and the number of brown parts under processing the sintering needs to be done for 10-15 hours. Once sintering is over, the metal parts are removed to give the ultimate finishing touches.
The end result of this five-stage 3D printing process of a lightweight automotive gear is a pure stainless steel 17/4PH part with no sign of plastic residue.
Sintratec assures the metal parts created through additive manufacturing show the same level of mechanical performance as those generated through conventional manufacturing. On the contrary, the metal parts created through the CMF process exceed the MIM standards as it has excellent elongation of 13.2 per cent after hardening. Along with CMF Alliance hardware this technology will help lightweight automotive gear users to manage porosities as the design have free-flowing channels that make them superior in mechanical properties.
Remember, you can post job opportunities in the AM Industry on 3D ADEPT Media free of charge or look for a job via our job board. Make sure to follow us on our social networks and subscribe to our weekly newsletter : Facebook, Twitter, LinkedIn & Instagram ! If you want to be featured in the next issue of our digital magazine or if you hear a story that needs to be heard, make sure to send it to contact@3dadept.com