Imagine if the security scanner that detects gas residue in a public environment malfunctioned due to the breakdown or failure of a material used in the manufacturing process of a given part. When we put it this way, we immediately perceive the importance high-performance materials can have in the fabrication of a part.
When leveraging additive manufacturing technologies, multinational companies usually have various experts in-house that will be able to bring their expertise in the choice of the appropriate system, the right material and the appropriate pre- and post-production systems. Imagine now a situation where an SME does not have these experts in-house to facilitate the decision-making process. Choosing an industrial or a professional 3D Printing system is already not an easy task. This task gets harder when it comes to materials.
Indeed, as technology advances, the rise of technical terms such as high-performance materials, engineering materials or advanced materials, is gaining momentum. In an era where companies tend to claim to be the “first” to launch their technology onto this market, it is easy for the prospective end-user to get lost by the (sometimes) abusive use of technical words by companies.
This article, therefore, aims to clarify the meaning of high-performance materials. It aims to help users identify the various types of high-performance materials, to understand materials characterization and to determine the additive manufacturing technology that suits those materials best. To discuss this topic, we have asked a number of questions to VBN Components, Armor Group and Malvern Panalytical B.V.
High-performance materials, engineering materials or advanced materials?
Over the millennia, human beings have harnessed various substances to develop new and useful materials not ordinarily found in nature. The truth is, nobody expects the explosion in materials research that marked the 20th century. From automobiles to aircraft, sporting goods to skyscrapers, clothing to computers and a host of electronic devices—all bear witness to the potential of materials.
Several types of materials can be leveraged to manufacture parts of these industries. However, the demand for higher quality components is driving manufacturers and suppliers to master machining and assembly procedures of high-performance materials.
High-performance (engineering) materials aim to achieve the higher performance of engineering materials in the areas of: material strength, deformation resistance, functionality, light-weighting, corrosion resistance, high-temperature capability, materials processing efficiency, sustainability and multi-functionality.
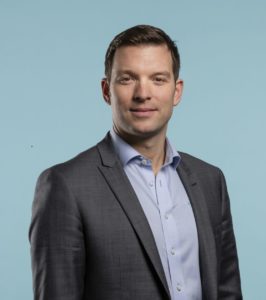
According to Pierre-Antoine Pluvinage, Business Development Director at ARMOR GROUP, for the AM brand KIMYA, thermal resistance, mechanical resistance and shock resistance are often the first key performance indicators taken into account to identify high-performance materials:
“High-performance materials are first characterised by their thermal performance. Another key performance indicator may be their chemical or mechanical resistance, or shock resistance properties.
However, thermal performance is not necessarily the only defining feature of a high-performance material: it can provide functional properties that other engineering materials or readily-available materials would not provide.”
Furthermore, it should be noted that several terms including engineering materials or advanced materials are often used to designate high-performance materials. Yet, a slight difference can be observed between the two terms:
Engineering materials are a broad term that refers to selecting the appropriate materials for the application in which the engineered part is being used. It requires to focus on a particular grade of material based on its properties such as malleability or tensile strength.
Materials that are utilized in high-technology applications are referred as Advanced materials. They are typically traditional materials whose properties have been enhanced, and also newly developed, high-performance materials. Simply put, when the focus is made on a particular grade of material, or when new properties have been developed based on traditional materials, the new material is termed as “advanced material” or “high-performance material”. Those materials are, for instance, metallic foams, magnetic alloys, special ceramics etc. They are used in High-Tech devices like computers, aircrafts, electronic gadgets, etc. Some of their applications include integrated circuits, lasers, LCDs, fiber optics and many more.
Engineering materials that might derive from them include metals (ferrous and non-ferrous metals), ceramics, polymers, composites, semi-conductors and bio-materials. However, as part of this article, a key focus will be made on polymers and metals.
High-performance materials: polymers (plastics, thermoplastics, polycarbons)
A material is more complex than just its chemical composition. Its properties depend on its microstructure, which can evolve – during the process – or the life of the material.
The challenge is even bigger for material producers of polymeric high-performance materials. Indeed, for demanding industries like transport, automotive, or even aerospace, industrials are continuously looking for lightweight materials as efficient as metal, glass or rubber.
In this vein, the Business Development Director of ARMOR Group explains that we do not only talk about high-performance materials when it comes to additive manufacturing. As a matter of fact, high-performance materials are used in several production processes like metal injection moulding or machining processes. “The challenge is to assess how to use these materials and adapt them to 3D printing technologies while maintaining their native properties”, said the expert from ARMOR Group.
Their increasing use in additive manufacturing demonstrates that the most coveted materials can withstand high temperatures. These materials include: PAEK (PEEK, PEKK), PEI or ULTEM as well as PPSU.
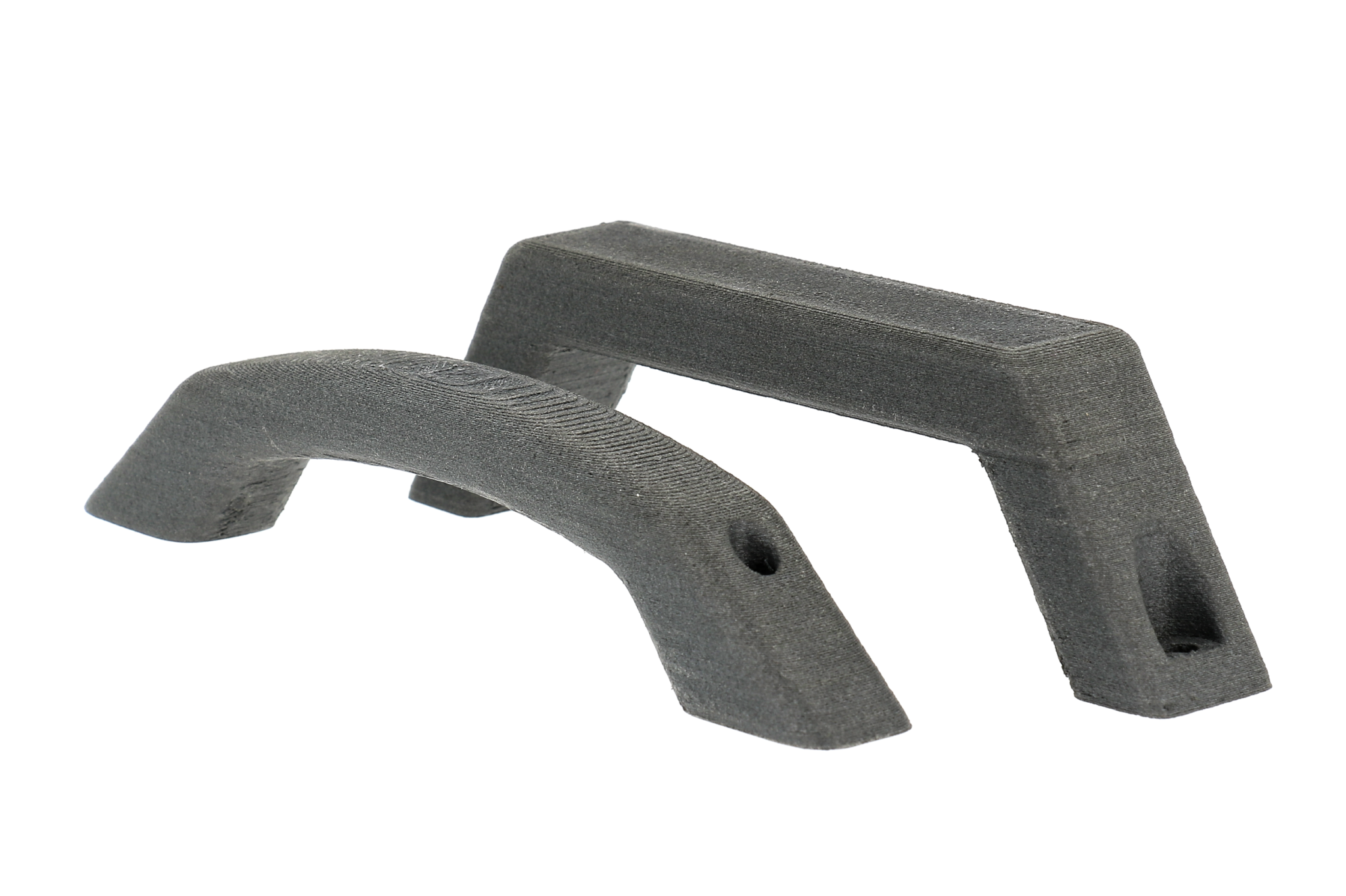
When one or more polymers or additives are added to a resin, this combination results in an engineering plastic that integrates high-strength and several good properties. For example, to develop the material Kimya PEKK-A, Arkema Kepstan PEKK Resin has been added during the manufacturing. The final material integrates a slower crystallization ratio, which leads to more effective adhesions. Furthermore, it is acknowledged for its high resistance to high temperatures (260°C), and its ability to receive other functionalities.
Now, to attest to the quality of this material, and its ability to be processed on various 3D Printers, materials characterization comes into play.
Materials Characterization
As technology advances, material characterization increasingly becomes sophisticated. Several techniques exist to study and measure physical, chemical, mechanical and microstructural properties of materials. The process can be applied at several stages of materials development.
However, whatever the process is, the overall goal is, on the one hand, to understand key elements required to resolve important issues, such as causes of failure and process-related problems, on the other hand, to make critical materials decisions.
Both standardized analytical methods and specialized application-specific advanced techniques can be applied during such process.
When it comes to 3D Printer filaments, mechanical properties such as strain stress, yield strength, hardness, impact strength or bending are first tested for all newly manufactured materials. Their tests enable to range the materials according to their specifications and to determine if the material meets the customer’s requirements. Furthermore, material scientists carry out a tensile strength test to compare the commercial and manufactured filament.
As far as ready-to-commercialize materials are concerned, Pierre-Antoine Pluvinage mentioned some of the criteria that are taken into account to attest to their quality :
“There are several criteria to consider when it comes to monitoring filaments’ quality: diameter checks, ovality checks, imperfections checks (air bubbles). We might also add printability, as well as the evaluation of the functional attributes linked to the product’s technical specifications”, explains ARMOR Group.
The ideal additive manufacturing process
Polymers-based high-performance materials can be processed on either an FDM 3D Printer or a SLS Technology. However, in this specific case, let’s see their prerequisites on an FDM 3D Printing solution.
Despite their ability to withstand high temperatures, the AM operator should pay attention to three temperature environments: the extrusion temperature, the printing plate, and the printing chamber. A nozzle that presents a too high temperature might lead to a partial deformation of the printed part or a material’s seepage. A low temperature, on the other hand, does not enable a perfect cohesion between layers.
As far as the printing plate is concerned, if the temperature is too high, it will not be possible to remove the printed part easily. Indeed, the first player would have adhered so much to the printing plate that the latter could be damaged. A low temperature will cause an adherence issue and will lead to part deformation.
As for the heated chamber, its temperature enables to obtain good adhesion between layers and prevents shrinkage when the melted material becomes solid.
In addition to these temperatures, the AM operator should also pay attention to the crystallization phenomenon of the materials. Semi-crystalline materials like PEKK tend to form crystals in environments hotter than their glass transition temperature. This phenomenon might first lead to a shrinkage and part deformation, and at the end, lead to a failure of the printing process.
“High-performance materials benefits lie precisely in their versatility and wide range of possible applications. Semi-crystalline materials typically offer outstanding chemical and mechanical properties including [the ability to withstand] high-temperature conditions. They can be used in structural applications as well in applications that imply rubbing and erosion. For example, PEKK-SC presents a high chemical and thermal resistance combined with electric and dielectric insulation properties. Amorphous materials such as PPSU or PEKK-A perfectly maintain their mechanical properties until glass transition temperature and present excellent electrical properties. Thanks to their exceptional dimensional stability, these materials are suitable for precision components”, concluded ARMOR GROUP’s spokesperson.
High-performance materials: metals
Although thermoplastics drew the most attention in the early days of 3D printing, metal AM remains the technology that drives the most the additive manufacturing industry.
Metals are known as ductile materials. In other terms, they can easily withstand tensile stress. However, the more technology advances, the more issues including high melting points, layer thickness, print speed and production capacity, are addressed.
A number of different metals are available in powdered form to suit various processes and requirements. Those powders include titanium, steel, stainless steel, aluminium, and copper, cobalt chome, titanium as well as nickel-based alloys. Those materials also include precious metals like gold, platinum, palladium and silver.
The increasing interest in high-performance materials made with these materials lies in the fact that those 3D Printed components are not often reproduced. In the long-run, if the operator has succeeded in taking advantage of all stages of the manufacturing process, he can benefit from low production costs.
In the same vein, it should be noted that to attest to the quality of the aforementioned powders, the same properties are not necessarily always tested.
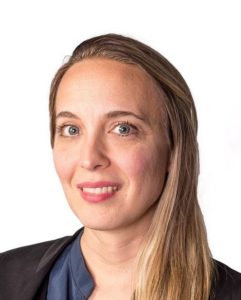
VBN Components for instance, develops a high-speed steel named Vibenite® 280, Isabelle Bodén, Customer relations manager, explained that for this material, the actual wear in usage (“how much material is worn off when exposed to i.e. abrasion”) and the long-term hardness are key characteristics that should be taken into account to attest to the quality of this material.
“Our materials are extremely wear-resistant. For example, our high-speed steel Vibenite® 280 is used in a gear hob, cutting twice as deep and lasting twice as long before needing regrinding, compared to a top, traditional steel in the same application. The carbides in our materials are very fine and well-dispersed, resulting in hardness levels up to 72 HRC and higher toughness than you would expect from such hard materials”, explained the spokesperson form the Sweden-based company.
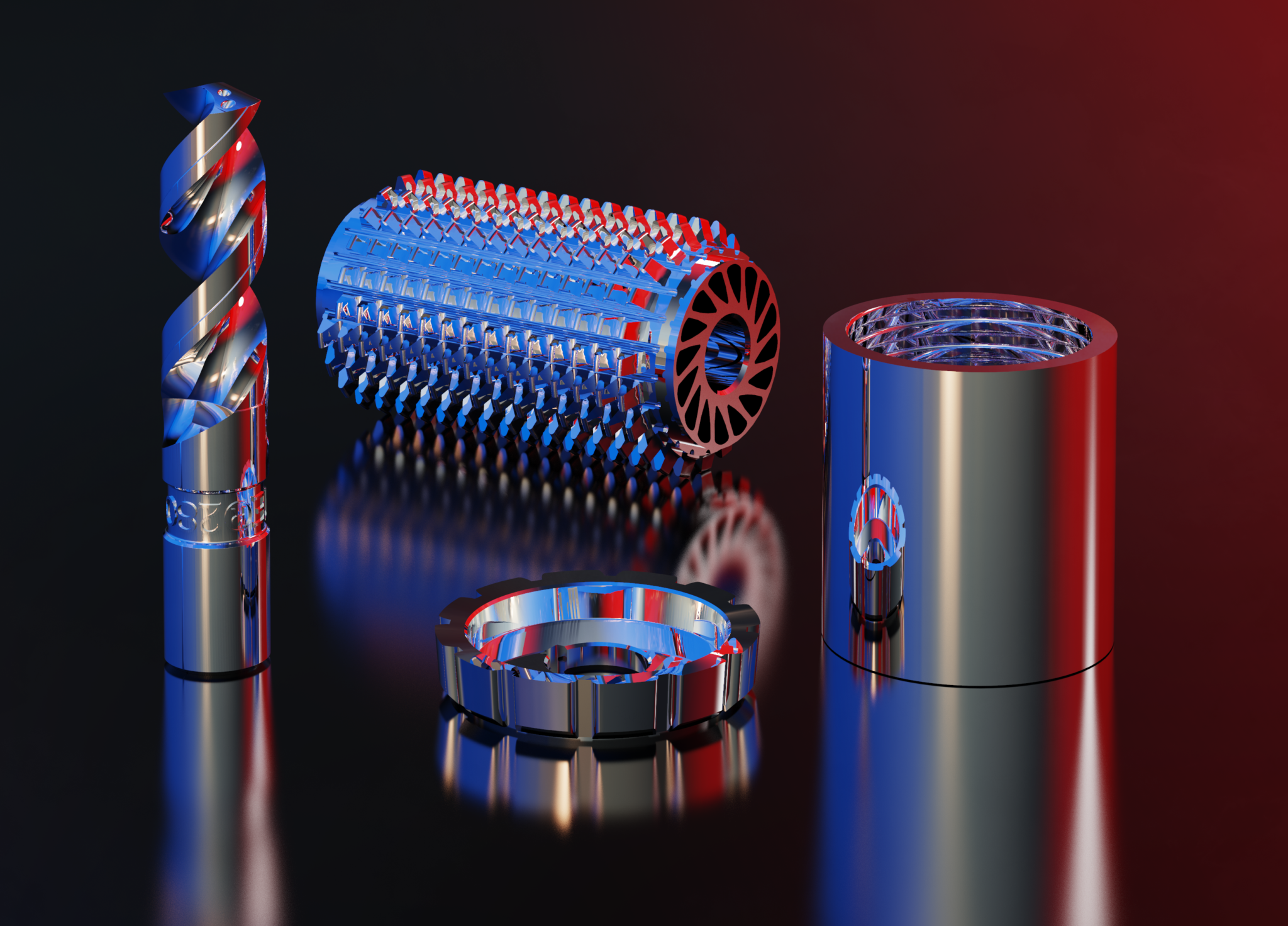
Materials characterization
For the AM of a given part, the cost of the powder represents up to one third of the production cost, not to mention that commercial viability should be backed by a robust supply chain and effective powder recycling strategies. Moreover, there are over 14 metal-based AM technologies today. However, we will take into account powder-bed fusion technologies to discuss these analytical techniques.
According to Malvern Panalytical, “the chemical and physical properties of the powder directly impact the build process and final component quality and must be controlled and optimized to ensure process robustness and consistency. To achieve this powder, properties must be characterized at various stages in the supply chain, from new alloy development through to powder recycling. Laser diffraction, automated image analysis, X-ray fluorescence (XRF) and X-ray diffraction (XRD) are four key analytical techniques that are commonly used to characterize additive manufacturing powders.”
Laser diffraction is interesting to measure the particle size distribution of metal, ceramic and polymer powders for additive manufacturing. In powder-bed fusion processes, particle size distribution affects powder bed packing and flowability which in-turn impacts on build quality and final component properties. Using a laser diffraction process enables to achieve particle size distribution in a few minutes using either wet or dry dispersion techniques.
“Automated static image analysis can be used to classify and quantify the size and shape of metal, ceramic and polymer powders by combining particle size measurements such as length and width, with particle shape assessments such as circularity and convexity on a statistically representative sample (>10,000 particles)”, explained Malvern Panalytical.
Lastly, if XRF helps materials scientists to determine the elemental composition of metal alloys and to detect the presence of contaminants or inclusions, XRD provides information about the micro-structural characteristics that can be influenced by thermal and mechanical processes.
To sum up, the development of AM machines is an important area of focus as technology is continuously adapted to deliver higher throughputs. However, the properties of the powders used are increasingly taking a big part of the production strategy. Materials characterization is just the beginning of the story. #StayTuned