Fraunhofer IGD, the research institute behind the Cuttlefish® 3D printer driver – first unveiled in 2021, has given hope to patients who need ocular prostheses. Occularists who use the research institute’s requisite software and printer driver, can produce tailor-made ocular prostheses.
First experiments were conducted at the Moorfields Eye Hospital in London. “Optimally adapted artificial eyes can enormously enhance the quality of life of those affected,” explains Johann Reinhard, Deputy Department Head of the 3D Printing Technology Competence Center.
As a reminder, the 3D printer driver translates 3D scan data or 3D models generated by design and texturing software for 3D printers of various manufacturers.
The data-driven design and 3D printing process developed by the Fraunhofer team ensures that the prosthesis is not only a perfect match for the patient’s remaining good eye, but is also a perfect fit for the empty eye socket. Fraunhofer IGD’s Cuttlefish:Eye software and Cuttlefish® printer driver enable the ocularists to use this technology. The software is already approved as a medical device in the UK and will be making its debut in mainland Europe soon.
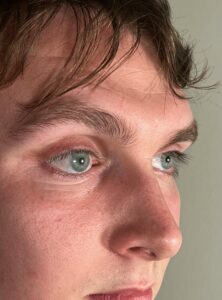
The artificial right eye, shown on the left. The eye prostheses produced with the aid of Fraunhofer IGD’s 3D printing technologies match the appearance of the healthy eye and fit into the eye socket. (Source: Stephen Bell, Ocupeye Ltd)
As part of a research, the researchers examined both the appearance and the shape of the ocular prostheses in a sample of ten patients. The appearance criterion included the size and color of the iris and pupil as well as the texturing of the sclera. The ocularist treating the patients rated these points as excellent.
“Patients describe the 3D-printed ocular prostheses as ‘life-changing’,” adds Reinhard. In terms of the shape criterion, the analysis of the ten cases helped to clarify the types of patients for whom the ocular prostheses are more suitable and the types for whom they are less so. The necessary adjustments as well as the final direction of gaze and mobility of the prosthesis were considered.
The automated nature of 3D printing brings the dual advantage of consistently high quality and shorter production times. As the input from ocularists is reduced, this leads to significant reduction in manual labor; depending on the quantity, this reduction can be as much as a factor of five. “More importantly, however, more patients can be treated and their waiting time for a new prosthesis can be shortened,” adds Reinhard.
Gentle procedure
The digital measuring and production process is also particularly painless for patients. Optical coherence tomography (OCT) is used to create a scan of both the eye socket and the healthy eye, while an integrated camera provides a color-calibrated image. The traditional alginate impression of the eye socket is no longer necessary. Cuttlefish:Eye uses a statistical shape model to predict the best-fitting prosthesis shape and is able to do this despite incomplete information on the surface of the eye socket.
In just a few minutes, the OCT data is used to calculate an accurately fitting 3D model of the eye prosthesis which is a close visual match to the healthy eye. Production takes place on a multi-material 3D printer, which is controlled using the Cuttlefish® 3D printer driver. The prostheses are manufactured and distributed by Ocupeye Ltd.
Eye prostheses usually become necessary after serious injuries or illness; in Europe, around 750,000 people are affected. Hopefully, with such type of solutions, this number could be reduced.
Remember, you can post job opportunities in the AM Industry on 3D ADEPT Media free of charge or look for a job via our job board. Make sure to follow us on our social networks and subscribe to our weekly newsletter : Facebook, Twitter, LinkedIn! If you want to be featured in the next issue of our digital magazine or if you hear a story that needs to be heard, make sure to send it to contact@3dadept.com