3D Printed electronics is one of the young areas of application of additive manufacturing. In his analysis of the 3D printing market in 2018, President Nano Dimension USA, Inc. Simon Fried, told us that the evolution of this market “has been similar to how traditional additive mechanical manufacturing evolved. The companies leading the adoption of additive manufacturing are the same kinds of industries that are now making strides in the direction of additive manufacturing of electronics — including aerospace, defense and R&D organizations. During 2018, this revolutionary area of 3D printing continued gaining traction, its impact will be felt in products, production systems and design-flows.” This statement left a great number of unanswered questions among additive manufacturing professionals, especially engineers from engineering offices. We have decided to tackle them in this segment.
With the digital revolution, communications technologies are heavily intertwined and products are increasingly being electrified. For this reason, specialists of this field are continuously looking for new ways to improve the production of smaller, complex and functional tools such as inks onto flat surfaces using printing processes usually intended for the graphics industry (screen, ink-jet, flexo, gravure, etc.) or RFID tags, sensors, displays, smartcards, keypads, and packaging. Common characteristics of these applications include low costs and the fact that high- performance is not required.
However, the recent development of tools for AM has raised three main challenges in efficiently applying 3D Printed electronics. For Christoph Völcker from the Innovation Lab – AM Würth Elektronik eiSos GmbH & Co. KG, those main challenges are materials, techniques (hardware) and data.
Materials
Just like classic additive manufacturing technologies such as FDM, we also observe that, combining electronically functional materials to AM enables complex 3D geometries and results in the creation of devices that cannot be created using conventional 2D printing methods.
Depending on the purpose of manufacturing, producers can use two main types of materials: dielectric materials (which means that no current will flow through the material when a voltage is applied) and conductive materials (which means the material can conduct the electric current). A few examples of dielectric materials include Hatchbox PLA, ColorFabb bronze-fill PLA whereas Electrifi (Multi3D LLC), the graphene-based conductive PLA (Black Magic 3D), or even the carbon black-based conductive PLA (Proto-pasta) are conductive materials.
Those various materials raise the challenge of cross-contamination during the fabrication. Indeed, it is difficult to combine two different filaments during the printing process. According to a research from Duke University (in the USA), “cross contamination of conductive materials will result in either shorting between conductive traces, or in the interruption of a conductive trace with non-conductive materials.”
Although several 3D printers with multiple nozzles can be found on the market – understand FDM 3D Printers – most of them are not able to prevent cross-conta-mination whereas “typical multi-material 3D printers use two separate nozzles at the same Z height, but this method leaves the inactive nozzle in a position where it is likely to scrape across the printed surface and cause cross-contamination”, explains the research from Duke University. According to experts, one approach to solve this issue is to extrude multiple materials through the same nozzle.
This challenge is observed when 3D printed electronics is applied with professional 3D printers. At the industrial level, Nano Dimension, one of the companies that specializes in 3D printed electronics, mentions the need of more material options to produce high-complexity and high-functionality parts. While comparing all 3D Printing materials used in the AM industry, Simon Fried told us: “Polymers are getting stronger and a wider range of metals are now printable. For electronics, additional functional aspects such as dielectric constants and looseness are paramount.”
Hardware
So far, a few number of companies can efficiently supply 3D printers for electronics. Despite this limitation of hardware, one can mention, in addition to Nano Dimension, Optomec, BotFactory and Voxel 8 as other manufacturers of electronics 3D printers on the market.
Released in 2017, Nano Dimension’s 3D printer DragonFly 2020 produces multilayer printing of conductive traces using an inkjet technique at a lateral resolution of nearly 30 µm. Experts from Duke University stated that it is time consuming to develop novel electronic inks for ink-jet processes, not to mention the difficulties encountered. This is mainly due to the need to adapt the surface tension and viscosity (8–12 cp) of the ink to obtain a desired droplet size (∼30 µm) and reproducible jetting characteristics. Furthermore, “clogging can be an issue if the size of the particles or the amount of solids in the ink is too high”.
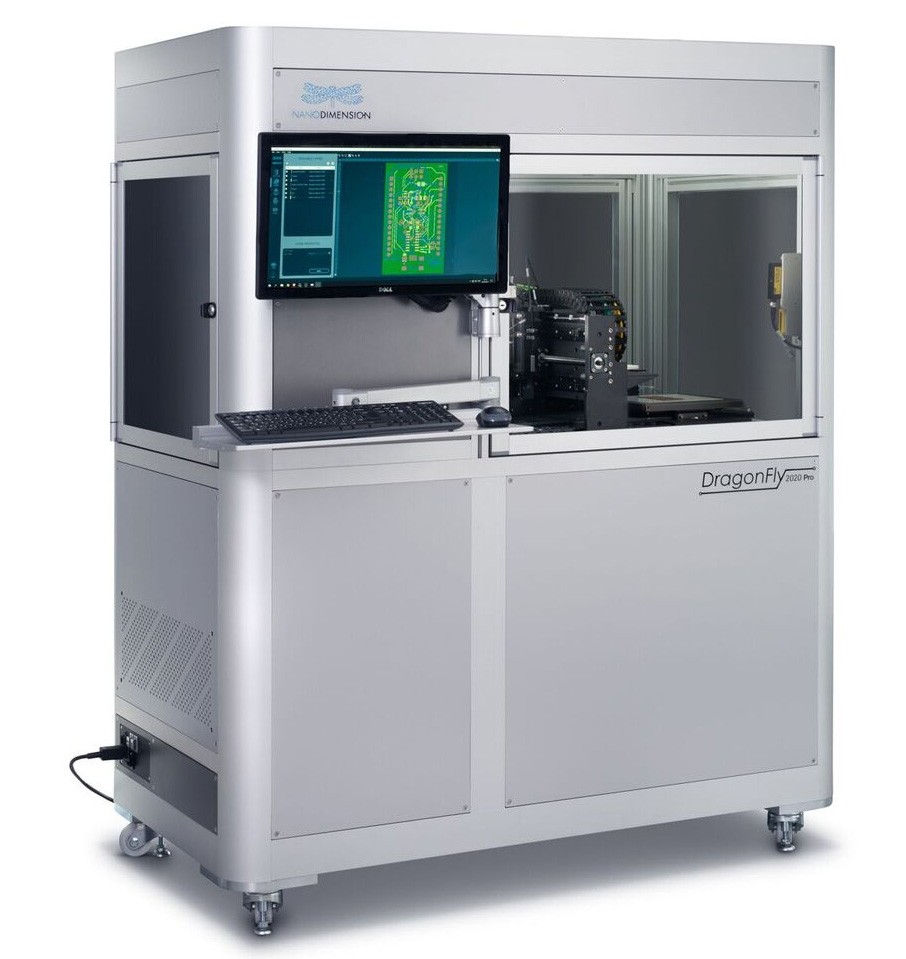
Optomec on its side, has developed the Aerosol JetTM process. The 3D printer enables the deposition of polymeric and metal inks for sensors. The process is a non-contact one, compatible with a wide range of conductive, insulating and resistive materials. The 3D printer has already enabled the production of conformal sensors, low loss passives and antennas for on-chip and off-chip electronics.
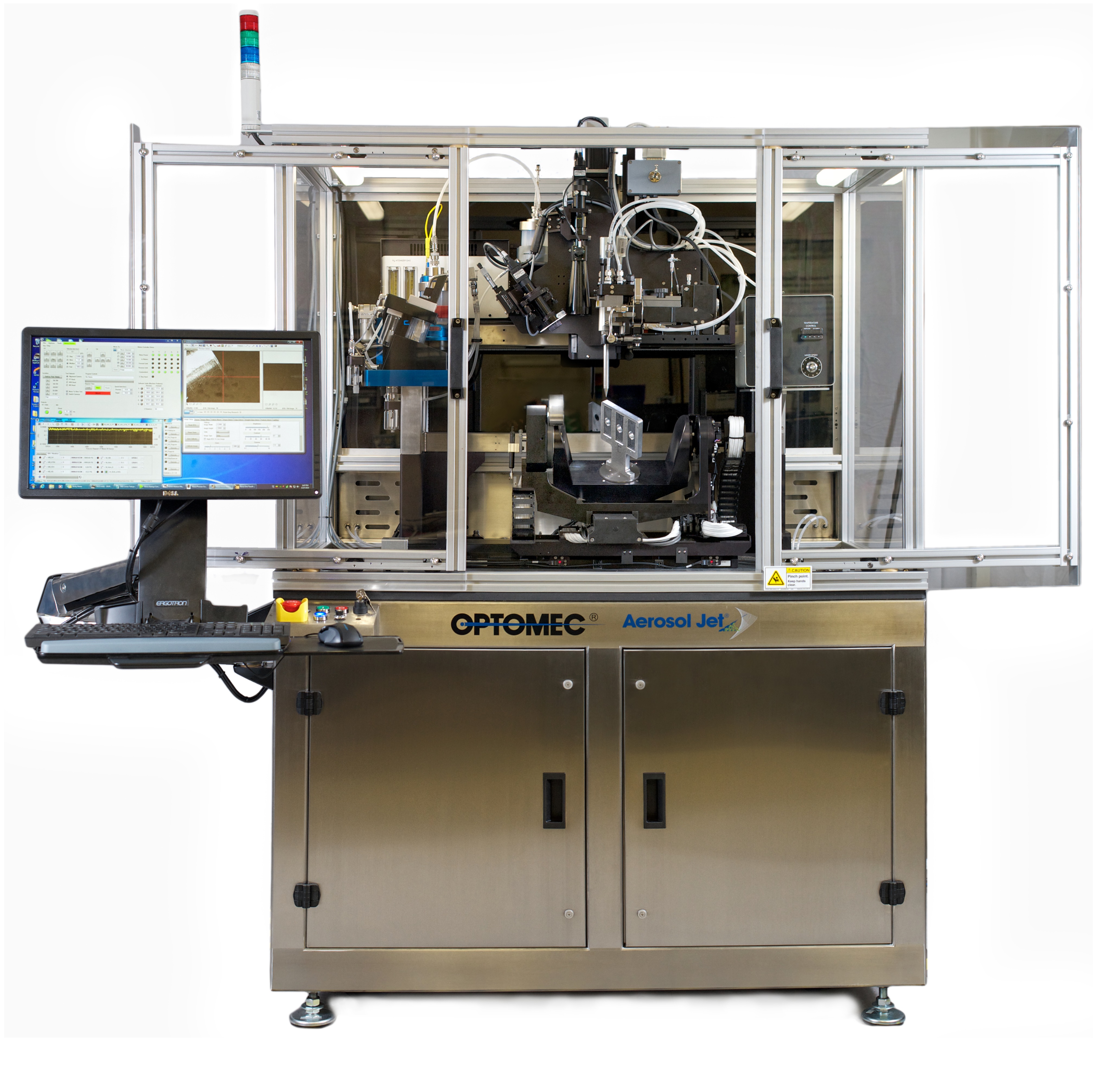
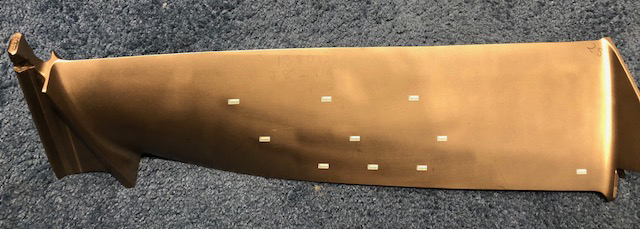
As for this process, it requires the use of a sheath gas as nozzle, to eliminate the clogging issues that plague ink-jet.
In 2015, the market discovered BotFactory’s Squink PCB Printer followed by the SV2, a few months later, a Desktop PCB Printer. It is, as per the company’s words, “capable of printing multilayer circuits, dispensing paste onto pads, and pick-and-placing components onto the board”.
Lastly, the Voxel8 3D printer is a mix of conventional plastic filament extrusion nozzle with a syringe-based silver ink extruder. One thing that characterizes this printer is the pause that can be done during the printing process to enable manual placement of circuit components. However, the printer cannot achieve print free-standing structures in the Z-direction, with recommended trace thicknesses < 500 µm.
This overview of 3D printers shows a lack of suppliers of electronics 3D printers, despite the existing quality on the market. Furthermore, based on analyses and researches that have already been carried out on 3D printed electronics, the use of this technology also presents a limitation at the post-processing stage where techniques should be implemented to achieve the full production of a 3D printed part with the desired electronic properties.
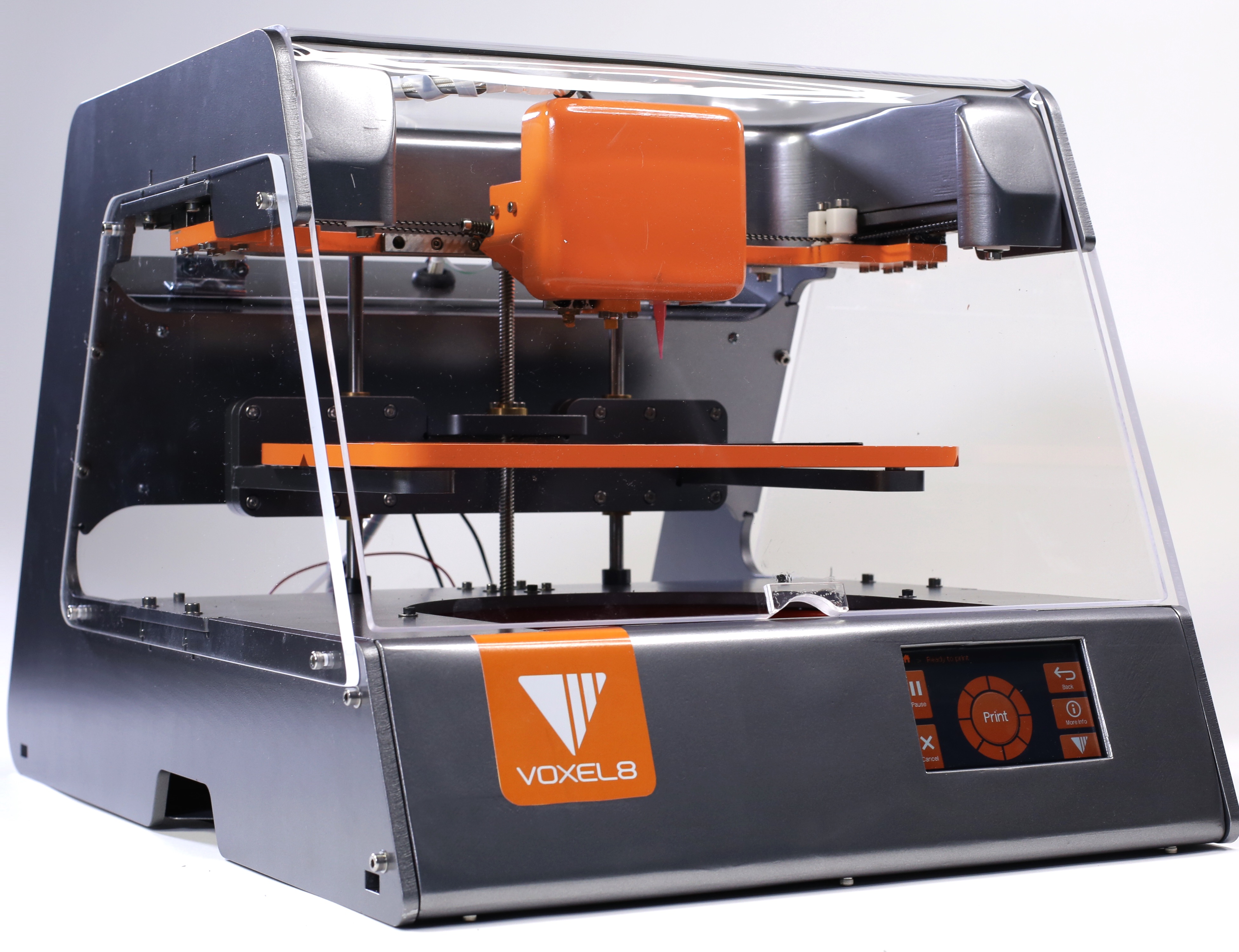
Data
In much the same way that big data brought a range of benefits to various industries & companies, it has also proven to play a crucial role in the growth of 3D printing.
In this particular industry, data enable an accurate analysis at the software level. Furthermore, the more complex the part to 3D print is, the more data might be needed.
Even though, experts weren’t able to bring a more in-depth opinion on this part, analysts believe that data have further facilitated applications in 3D Printed electronics. For this reason, this latter field would be a cheaper option for companies.
Final Thoughts
Although engineering plastics and metals were almost the overriding narrative of 2018, the field of 3D printable electronics aims to enable low-volume, on-site/ on-demand production of highly complex and easily customizable electronic structures while reducing material waste, energy consumption, prototyping time, and cost relative to conventional electronics fabrication methods. At this level though, the market is in major need of more material & hardware options and more solutions to overcome the challenges encountered at the post-processing stage.