La demande croissante de pièces imprimées en 3D de grande taille implique que les utilisateurs de la fabrication additive doivent avoir des attentes réalistes lorsqu’ils tentent d’étendre leurs opérations. Si la comparaison constante entre la fabrication additive grand format (LFAM = Large Format Additive Manufacturing) et les processus d’impression 3D de bureau est souvent inévitable, il faut également garder à l’esprit que la LFAM se présente sous de nombreuses formes et que chacune de ces approches a sa propre recette pour réussir. Une conversation avec Scott Vaal, de Thermwood, nous aide à comprendre certains des éléments clés du succès de la technologie LSAM.
Reconnue pour ses technologies de routeur CNC, Thermwood est l’une de ces entreprises qui n’a plus besoin d’être présentées dans le monde de la fabrication additive. L’entreprise s’est fait un nom dans le domaine de la fabrication additive à grande échelle (LFAM) – avec sa technologie LSAM (Large Scale Additive) – et continue d’intriguer avec le lancement récent d’un processus de fabrication additive qui n’imprime pas en 3D.
À mesure que la FA gagne en maturité, il est essentiel de comprendre les défis inhérents à chaque technologie et les solutions qui peuvent être explorées pour les relever. En effet, malgré les obstacles communs à certaines technologies, je suis convaincue que la façon dont chaque équipementier aborde le problème rend sa technologie plus attrayante ou non.
Cet article vise donc à comprendre certains des obstacles techniques liés au procédé LSAM et les solutions mises en place par Thermwood pour les surmonter. Pour ce faire, nous nous concentrerons sur les problèmes techniques qui peuvent survenir au niveau de la conception et des matériaux, ainsi qu’au cours du processus de fabrication.
Par ses réponses, Scott Vaal, chef de produit LSAM, nous a fait comprendre que chaque élément de la chaîne de valeur de la fabrication est d’une manière ou d’une autre lié à un autre – par conséquent, ils ne nécessitent pas nécessairement des solutions/approches individuelles.
Lorsque des problèmes techniques au niveau de la conception affectent le processus de fabrication
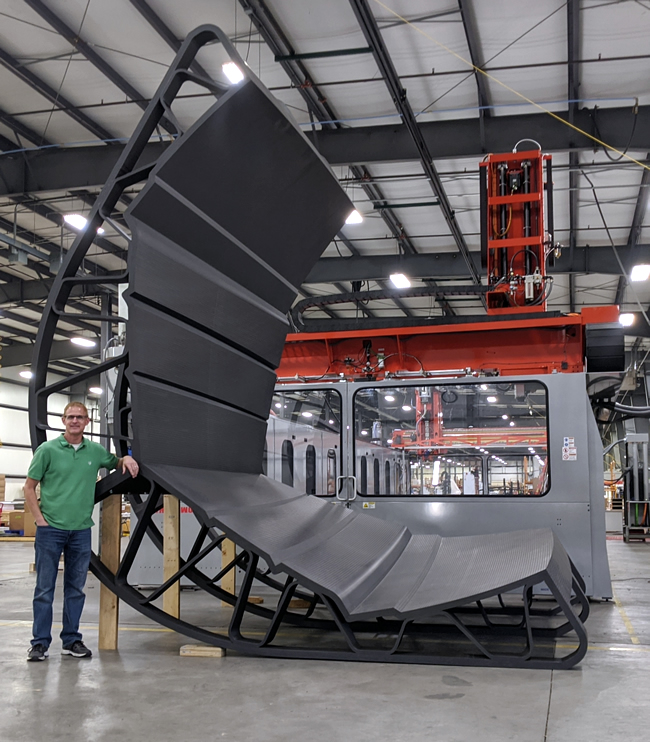
Le procédé LFAM peut élargir l’enveloppe de conception grâce à sa capacité à imprimer plusieurs grandes pièces en une seule opération. Par rapport à la FA à petite échelle, la consolidation des pièces et la réduction du temps de fabrication sont d’autres facteurs qui jouent en faveur du LFAM.
L’année dernière, lorsque nous avons discuté d’une stratégie visant à augmenter l’échelle de l’impression 3D avec le procédé LFAM, cinq points essentiels avaient été identifiés pour aider le concepteur à faire la différence entre la conception pour le LFAM et la conception pour un « processus de FA standard » : la machine elle-même, la réduction de la taille de la pièce pendant ou après l’impression, la dépendance de la force par rapport à la direction de l’impression, la division en sections planaires séparées ainsi que la nécessité d’insérer des matériaux non-imprimés.
Vaal attire tout d’abord notre attention sur le fait que chaque pièce est différente et qu’il convient d’examiner la meilleure méthode à utiliser. Cela signifie que la taille de la pièce ne rend pas nécessairement la conception plus difficile. En effet, il note que dans certains cas, « il est possible de réduire considérablement la main-d’œuvre en incorporant autant de pièces que possible dans une seule impression, mais il n’est pas toujours pratique d’imprimer de cette manière. De même, dans certains cas, il est plus rapide d’imprimer la pièce en plusieurs sections plutôt qu’en une seule pièce. En effet, il faut au moins laisser le temps à une couche de refroidir à la température idéale avant de commencer la suivante. Cela signifie que vous pouvez avoir une vitesse d’avance réduite pour imprimer la pièce en un seul morceau, mais que vous avez la vitesse et la capacité de sortie nécessaires pour imprimer 4 morceaux en même temps, ce qui réduit le temps d’impression d’un quart. Bien sûr, cela peut signifier que vous devrez coller ou attacher les pièces les unes aux autres, ce qui prend également du temps ».
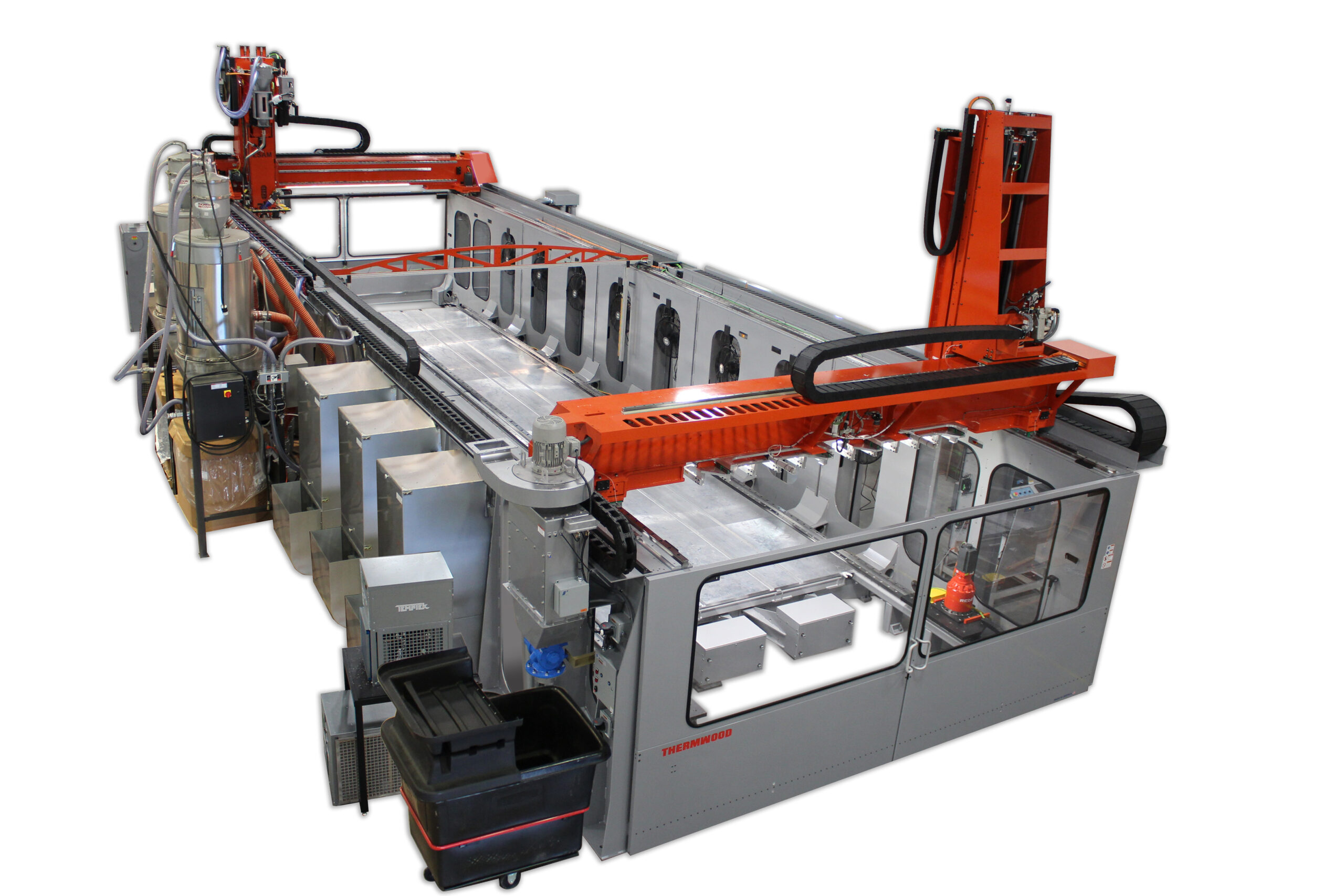
Cela dit, pour le chef de produit, on utilise le processus de forme quasi nette où l’on imprime généralement des billes beaucoup plus grandes qui créent des cuspides plus importantes entre les couches imprimées.
« En général, on imprime des billes légèrement surdimensionnées dans le but de post-usiner les surfaces qui doivent être lisses et précises, telles que les surfaces frontales d’un moule ou d’un outil de formage. La plupart du temps, vous éviterez les stratégies de remplissage lourd ou complet et utiliserez une méthode plus creuse avec des renforts spécifiques et précis là où c’est nécessaire. Cela permet de réduire le poids et de mieux contrôler les grandes différences de chaleur à l’intérieur de la pièce, ce qui est particulièrement important lors de l’utilisation de matériaux à haute température adaptés à l’outillage d’autoclave », ajoute-t-il.
Outre ces points essentiels, il convient de garder à l’esprit que les éléments tels que les parois minces et les petites caractéristiques doivent être évités autant que possible. En effet, la taille importante des billes et la difficulté des démarrages et des arrêts rendent ces caractéristiques propices aux erreurs. Pour résoudre ce problème, certains équipementiers ou fournisseurs de logiciels recommandent de s’assurer que l’épaisseur est au moins deux fois supérieure à la largeur du cordon lors de la conception de sections à parois minces.
Grâce au logiciel de tranchage du fabricant, LSAM Print 3D, les utilisateurs de la technologie LSAM peuvent créer des programmes d’impression de qualité destinés au LSAM et à la FA à grande échelle. Toutefois, Vaal prévient qu’« il est parfois difficile, voire impossible, de créer des modèles d’impression présentant les épaisseurs de paroi adéquates requises pour la méthode de tranchage planaire à grande échelle, en particulier lorsque les surfaces d’écoulement sont ondulées et courbes complexes ». Le logiciel LSAM Print 3D peut créer automatiquement les épaisseurs de paroi du chemin d’impression en fonction des dimensions des cordons d’impression que vous utilisez, ce qui permet d’obtenir des chevauchements cohérents entre les passages des cordons. Il appliquera également automatiquement le stock de découpe nécessaire pour que vous n’ayez pas à modifier la géométrie de la pièce juste pour obtenir un stock d’impression supplémentaire pour l’usinage. Grâce à son véritable environnement CAO, vous avez la liberté d’orienter vos pièces comme vous le souhaitez et de choisir la méthode d’impression qui vous convient le mieux. Le logiciel LSAM Print 3D dispose des outils et des techniques nécessaires pour ajouter facilement des renforts ponctuels et d’autres supports à l’impression. Il vous donne également la liberté d’avoir des paramètres uniques pour différentes zones de l’impression, de sorte que vous n’êtes pas limité à un seul ensemble de paramètres pour essayer d’imprimer la totalité de la pièce. Et peut-être le meilleur de tous, il crée les programmes de découpage et d’impression directement à partir de formats CAO réels tels que les solides, les surfaces et les corps de feuilles, de sorte qu’il n’est pas nécessaire de créer un fichier .stl de qualité déjà réduite juste pour créer un programme d’impression. »
Autres difficultés au cours de la phase de fabrication
Le warping, le contrôle de la température et l’adhésion des couches sont quelques-unes des difficultés que l’on rencontre souvent au cours du processus de fabrication. Si vous êtes un lecteur régulier de 3D ADEPT Media, vous savez probablement déjà que Thermwood a développé une solution pour le contrôle de la température.
Il est intéressant de noter que la clé pour minimiser le gauchissement et l’adhérence des couches réside souvent dans le choix des matériaux utilisés au cours du processus de fabrication. Les principaux facteurs influençant l’adhésion entre les couches sont les propriétés des matériaux, la température de recouvrement, les forces de gauchissement et toute forme de compactage ou de laminage de la couche après l’extrusion. Pour certaines applications, les matériaux à faible taux de rétrécissement et ceux remplis de fibres à brins courts pourraient constituer de bonnes options.
En ce qui concerne le gauchissement, l’expert de Thermwood explique que « cela commence en fait avec le substrat d’impression breveté du LSAM qui fournit une forte adhérence initiale, puis la surface spéciale flotte avec la pièce pendant qu’elle refroidit et se rétracte. Une fois les premières couches refroidies, la surface reste solide tout au long du processus d’impression, évitant ainsi les déformations et les tensions qui se produisent sur d’autres substrats. En outre, l’obtention et le maintien de températures optimales tout au long du processus d’impression sont importants pour contrôler la déformation, mais peut-être plus encore pour assurer une bonne adhérence des couches. Comme [indiqué ci-dessus], Thermwood résout ce problème grâce à sa fonction brevetée de contrôle de la durée de la couche intégrée au système de contrôle LSAM, qui contrôle et maintient dynamiquement les conditions de température appropriées. Tout aussi important pour l’adhérence de la couche est le compactage actif que vous obtenez grâce à la roue de suivi de la compression brevetée de la LSAM, qui améliore considérablement la liaison entre les couches et fournit les meilleurs résultats en termes de solidité latérale d’un cordon à l’autre ».
La constance, « l’une des meilleures caractéristiques de la technologie LSAM ».
Alors que l’incohérence des propriétés des matériaux est souvent l’un des principaux problèmes à résoudre dans un processus de FA « standard », les utilisateurs du procédé LSAM de Thermwood ne devraient pas rencontrer de difficultés à cet égard.
« Notre système breveté Melt Core fournit le matériau le plus précis et le plus cohérent possible et, grâce à la roue de suivi de la compression brevetée, vous obtenez les dimensions de billes les plus précises et la cohérence des microstructures composites imprimées. La cohérence est particulièrement importante lors de l’impression d’outillage pour autoclave à haute température, où nous devons compenser avec précision l’anisotropie de l’ECT et d’autres changements de forme. Cela signifie également que nous devons avoir des fournisseurs de matériaux capables d’assurer la cohérence entre de nombreux matériaux. Heureusement, nous avons plusieurs fournisseurs en qui nous pouvons avoir confiance », affirme Vaal.
Si cet article aborde quelques-uns des problèmes les plus fréquemment rencontrés au cours d’un processus de fabrication impliquant le procédé LFAM, il est juste de dire que cette liste n’est pas exhaustive. Nous sommes convaincus que plus les utilisateurs de FA évalueront le procédé LSAM de Thermwood, plus nous mettrons en évidence les spécifications et tirerons des leçons qui pourraient contribuer à la réussite du développement de chaque produit.
Comme le souligne Vaal : « Thermwood cherche toujours à améliorer ses produits, ses processus et ses logiciels. Nous ne restons jamais inactifs, et il est donc difficile de savoir ce que nous réserve l’avenir en matière d’innovations LSAM. Nous travaillons constamment en interne, avec nos clients et avec des centres de recherche pour trouver des solutions et des améliorations innovantes. »
Ce contenu a été produit en collaboration avec Thermwood. Il a été initialement publié dans le numéro de Mai/Juin de 3D ADEPT Mag. Toutes les images sont utilisées avec l’autorisaton de Thermwood.