Mis à jour: l’article a été mis à jour pour réfléter le fait que nous considérons les machines dont les volumes de construction avoisinent le m3.
La plupart des adeptes de la fabrication additive (FA) partagent le même rêve : être en mesure de réaliser une production évolutive (en grand volume). Pour que ce rêve devienne réalité, la plupart des industriels envisagent souvent d’utiliser des machines dont les volumes de construction avoisinent 1m3. Alors que la fabrication additive grand format (LFAM ou Large Format Additive Manufacturing) gagne du terrain, nous sommes en droit de nous demander comment et si elle peut également être considérée comme un candidat viable pour la production.
Si tout le monde s’accorde à dire que la fabrication additive grand format (LFAM) à grande échelle est une question de taille, les spécifications de la taille des applications ont toujours été sujettes à interprétation. Comme vous l’avez peut-être vu ci-dessus, nous avons déjà disqualifié des machines dont les volumes de construction avoisinent les 600 × 300 × 600 mm (23,62 × 11,81 × 23,62 pouces), car nous cherchons à explorer la candidature à la production de machines capables de produire des moules de coque de yacht, des outillages pour autoclave, des torches massives imprimées en 3D comme celle-ci, des meubles grandeur nature, des bateaux ou même des maisons. L’élément de mesure clé est donc la capacité de l’imprimante 3D à produire des composants de grande taille en une seule fois, par opposition à la production de plusieurs pièces qui doivent être assemblées.
La question de la taille évacuée, rappelons que comme toute technologie de fabrication qualifiée pour un environnement d’industrie 4.0, la LFAM vise également à mettre à l’échelle les opérations de fabrication tout en prenant en compte la vitesse, la précision, la résistance mécanique, la facilité de personnalisation, etc. Pour qu’une telle industrialisation se produise, les fournisseurs de technologies doivent fournir des indications claires sur la façon de relever les défis qui ralentissent l’adoption de la technologie. Parmi le large éventail de processus techniques susceptibles de déboucher sur des applications à grande échelle, on se rend compte que les principaux défis à relever tournent souvent autour de trois aspects clés : les logiciels, les matériaux et les coûts.
Le dossier ci-dessous vise à aider les industriels à :
- Comprendre les principales différences entre la conception pour la FA grand format et la conception pour un « processus de FA standard »
- Les principales considérations relatives aux matériaux qui pourraient ouvrir la voie à de (nouvelles) applications de fabrication additive à grande échelle.
- Comprendre les pièges courants de la fabrication additive à grande échelle et où se situe exactement la considération du coût au milieu de tout cela.
Pour aborder ce sujet, nous nous sommes appuyés sur l’expertise de Justin Ferguson, ingénieur principal en solutions chez Autodesk pour la partie logicielle, de Kyle Calvert, ingénieur en applications composites chez Ingersoll Machine Tools pour les points de vue des matériaux et des coûts, ainsi que d’Andy R. Bridge, directeur du développement commercial chez Additive Engineering Solutions, LLC pour le point de vue de l’utilisateur.
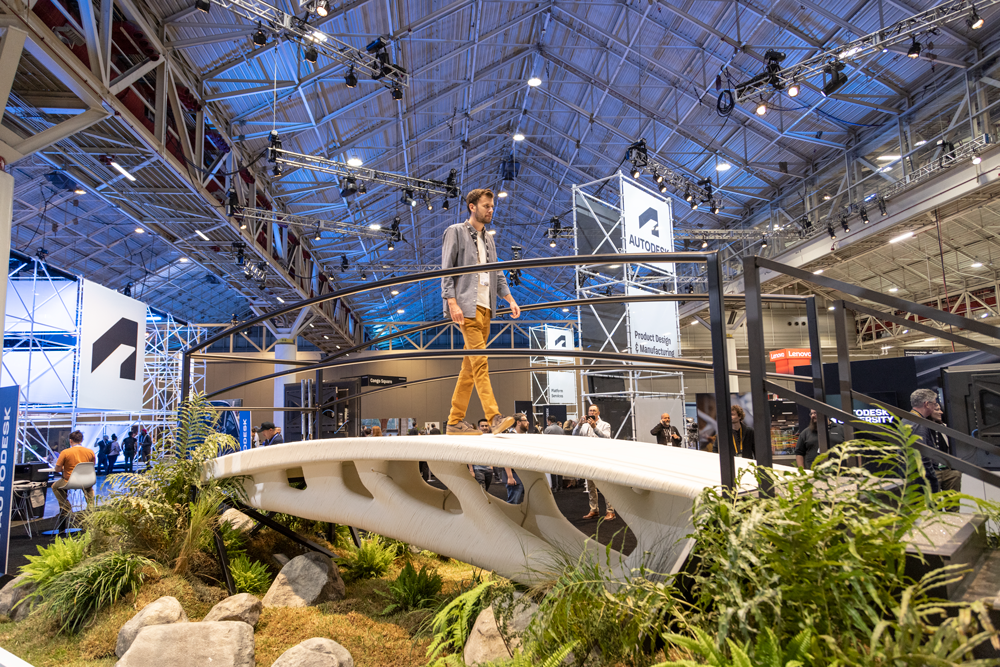
Concevoir pour la FA grand format
Comme indiqué dans notre Catalogue international des solutions de FA 2023, nous avons identifié trois types de technologies de FA à grande échelle – chacune d’entre elles ayant une large gamme de sous-processus :
- Les technologies basées sur l’extrusion, où l’on trouve les procédés d’extrusion de matériaux en granulés (FGF) et d’extrusion de matériaux en filaments (FFF),
- Les procédés à base de poudre, une catégorie qui comprend les approches de fusion sur lit de poudre, les procédés de projection de liant et de matériau et même les procédés de pulvérisation à froid,
- Et les procédés de dépôt d’énergie dirigée (DED) où nous avons identifié la fabrication additive par faisceau d’électrons (EBAM), le soudage par dépôt de laser (LDW) et la fabrication additive par arc électrique (WAAM).
Il est intéressant de noter que même si certains procédés de fusion sur lit de poudre peuvent fabriquer des pièces de plus d’un mètre cube, en utilisant plusieurs lasers et un lit de poudre plus grand et multizone, les plus grandes percées en termes de taille proviennent de l’adoption croissante des procédés DED et, en particulier, des procédés basés sur la WAAM.
En ce qui concerne la conception, connaître les différents outils de conception de la boîte à outils DfAM est une chose, les utiliser à bon escient en est une autre, surtout si l’on sait que chaque processus de FA et chaque machine comporte son lot de défis.
Tout en reconnaissant les particularités de chaque machine et de chaque processus, Justin Ferguson d’Autodesk souligne « qu’une tâche universellement difficile, indépendamment du processus, consiste à reconnaître les zones (pendant le processus de conception) où il peut y avoir une collision entre le matériel d’impression et des sections déjà imprimées ou des éléments non imprimés ».
La bonne nouvelle, c’est que lorsqu’on utilise un processus LFAM, on a la possibilité d’imprimer en 3D en une seule pièce, ce qui élimine le travail d’assemblage, accélère la production et augmente l’intégrité structurelle parce qu’il n’y a pas de joints ou de coutures.
Comment élaborer une stratégie pour augmenter l’échelle de votre impression 3D en toute sécurité ?
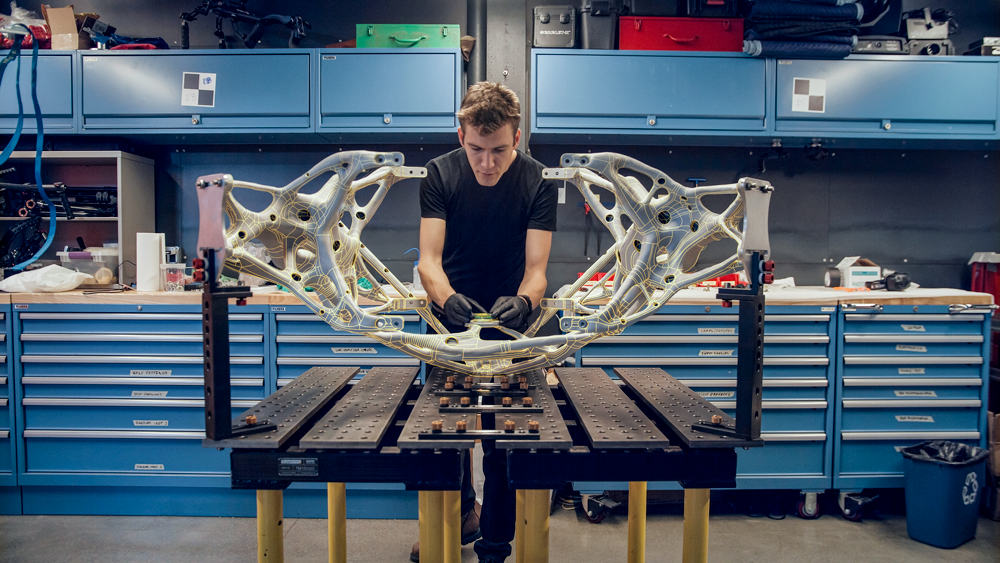
Ferguson identifie cinq points essentiels qui peuvent aider le concepteur à différencier la conception pour la LFAM de la conception pour un « processus de FA standard » : la machine elle-même, le rétrécissement de la taille de la pièce pendant ou après l’impression, la dépendance de la force par rapport à la direction d’impression, la division en sections planaires séparées ainsi que la nécessité d’insérer des matériaux non imprimés.
Il explique ci-dessous le raisonnement qui sous-tend chacune de ces considérations et donne quelques conseils pour résoudre des problèmes tels que le rétrécissement pendant et/ou après le processus d’impression :
« Selon le procédé LF-AM, les métaux (DED, Directed Energy Deposition), les plastiques (FFF, Fused Filament Fabrication/FGF – Fused Granule Fabrication), les agrégats (argile et béton) et autres, différentes stratégies de conception deviennent cruciales à adopter.
1- Dans la fabrication additive à petite échelle, nous disposons normalement d’une machine fixe avec un système de coordonnées unique et une enveloppe de fabrication fixe. À grande échelle, nous pouvons utiliser un système robotisé ou imprimer sur une autre pièce, mais en général, nous n’avons pas de système de coordonnées fixe ni de volume de construction fixe. Alors que les imprimantes de bureau ne se déplacent souvent que sur trois axes, les imprimantes à grande échelle ont souvent plus d’axes de mouvement, qu’il s’agisse de se déplacer sur un rail ou d’incliner la tête de l’outil. Ces processus grand format réalisés avec des machines multi-axes permettent de créer des caractéristiques qui ne dépendent pas de l’angle de surplomb. Cela nous permet de sortir du « processus de FA normal » de la conception pour la fabrication additive (DFAM). Par exemple, il devient possible de construire et de concevoir sans structures de support, mais cela peut introduire de nouvelles complexités telles que la manière de découper, la préparation de la surface (lors de la construction de caractéristiques sur des caractéristiques), etc.
2- La plupart des procédés LF-AM verront une réduction de la taille des pièces pendant ou après l’impression en raison de conditions telles que le refroidissement des métaux et des thermoplastiques ou le séchage/la polymérisation des agrégats et des thermodurcissables. En outre, lorsque les impressions LF-AM augmentent en taille, les couches supérieures « écrasent » les couches inférieures si elles ne sont pas refroidies ou durcies de manière adéquate.
Si, par conception, il y a un arrêt pendant l’impression puis un redémarrage, par exemple pour imprimer une nouvelle caractéristique ou pour permettre un refroidissement adéquat, la taille et la forme de la pièce sont susceptibles de changer avant que nous ne continuions.
Au centre technologique Autodesk de Birmingham, nous utilisons une extrudeuse de granulés thermoplastiques montée sur un robot à poignet sphérique Kuka à 6 axes. Au cours d’un projet, nous avons déterminé que la meilleure façon de continuer avec précision était de surimprimer, puis de découper à une hauteur connue à l’aide d’une broche de fraisage, avant de reprendre l’impression. Il s’agit d’une différence majeure pour la LF-AM, car la séparation du modèle en sections d’impression, la détermination des quantités de surimpression, puis la quantité d’usinage, tout cela doit être pris en compte dans le processus de conception. Si la fabrication hybride (additif et soustractif dans la même configuration) n’est pas une option, la quantité de rétrécissement des sections d’impression est très importante, de même que la détermination de l’endroit où s’arrêter et de la durée de l’arrêt, de sorte que le rétrécissement soit prévisible et compensable.
3- Un autre domaine dans lequel la FA grand format est très différente de la « FA ordinaire » est celui de la résistance qui dépend de la direction de l’impression. Dans une machine de type lit de poudre laser, par exemple, le modèle que le laser sintérise peut modifier la structure du grain et la résistance qui en résulte. L’un de nos clients, qui utilise une machine laser à poudre, a constaté qu’il pouvait obtenir une meilleure structure de grain si l’ensemble de la pièce était créé dans une trajectoire continue. La structure de grain souhaitée peut se propager continuellement avec une vitesse et une chaleur constantes.
4- Lors de la création de géométries complexes telles qu’un tube cintré ou d’autres formes complexes, il peut être décidé de diviser la pièce en sections planes distinctes, chacune ayant une direction de construction différente – comme pour la construction d’un tube avec des sections en forme de coin. Un ingénieur peut aussi décider de changer la direction de construction sur chaque couche et de moduler la vitesse, l’alimentation ou d’autres paramètres du processus pour obtenir une forme de couche non plane.
5- Si on considère certaines des plus grandes impressions, telles que les maisons, il est nécessaire d’insérer des matériaux non imprimés. Les fenêtres, les portes, les systèmes de chauffage, de ventilation et de climatisation, les installations électriques, les poteaux, les poutres et d’autres éléments doivent être pris en compte dans le processus DFAM. Si les matériaux non imprimés font partie intégrante de la structure, comme les poteaux ou les poutres, déterminer quand arrêter l’impression pour les insérer et s’assurer qu’ils ne provoqueront pas de collisions avec l’équipement de dépôt par la suite sont des étapes nécessaires qui sont propres à ce cas d’utilisation la LFAM ».
Que se passe-t-il lorsque votre pièce est tout simplement trop grande pour la plus grande des machines ?
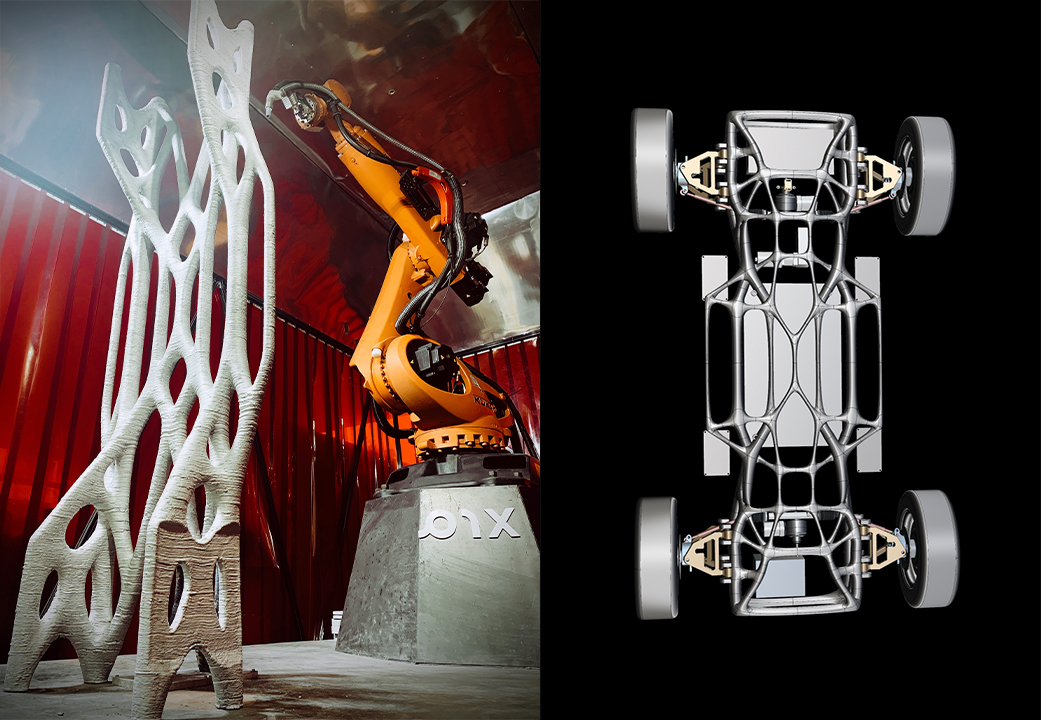
Il va sans dire que plus la pièce finale est grande, plus l’impression est difficile. La seule option à ce stade consiste à diviser votre modèle en composants imprimables en 3D que vous assemblerez par la suite. Diviser votre modèle directement dans votre logiciel de CAO est une excellente idée, car vous pouvez directement concevoir des aides à l’alignement, éviter les coupes qui traversent directement des zones spécifiques et sélectionner des coupes qui ne sont pas situées dans des zones fragiles de l’impression.
Pour Ferguson, « la physique commence vraiment à jouer un rôle lorsque les pièces deviennent plus grandes. Par exemple, la structure d’un mur devra être conçue différemment si votre perle mesure 1 cm de large contre 15 cm de large. Pensez au poids de la pièce à mesure que les couches augmentent. Pour le procédé DED et d’autres procédés, les couches inférieures peuvent s’écraser ou les structures murales peuvent même se déformer sous l’effet du poids considérable des grandes pièces.
Dans le cas des procédés FFF/FGF, si l’impression n’est pas verticale ou plane, il est possible que les couches subissent des compressions et des tensions à mesure que le poids augmente. Cela peut entraîner des défaillances dans les impressions et doit être pris en compte dans le processus de conception, ce qui est beaucoup plus difficile à mesure que la taille des pièces augmente.
Enfin, déterminer si des structures de soutien sont nécessaires et comment elles doivent être appliquées devient vraiment une question de conception assez difficile avec des pièces finales de grande taille, comme l’impression de bâtiments ou de fusées. S’il y a des supports, ils ont généralement été conçus de manière très spécifique. »
Principales considérations sur les matériaux pour les applications LFAM
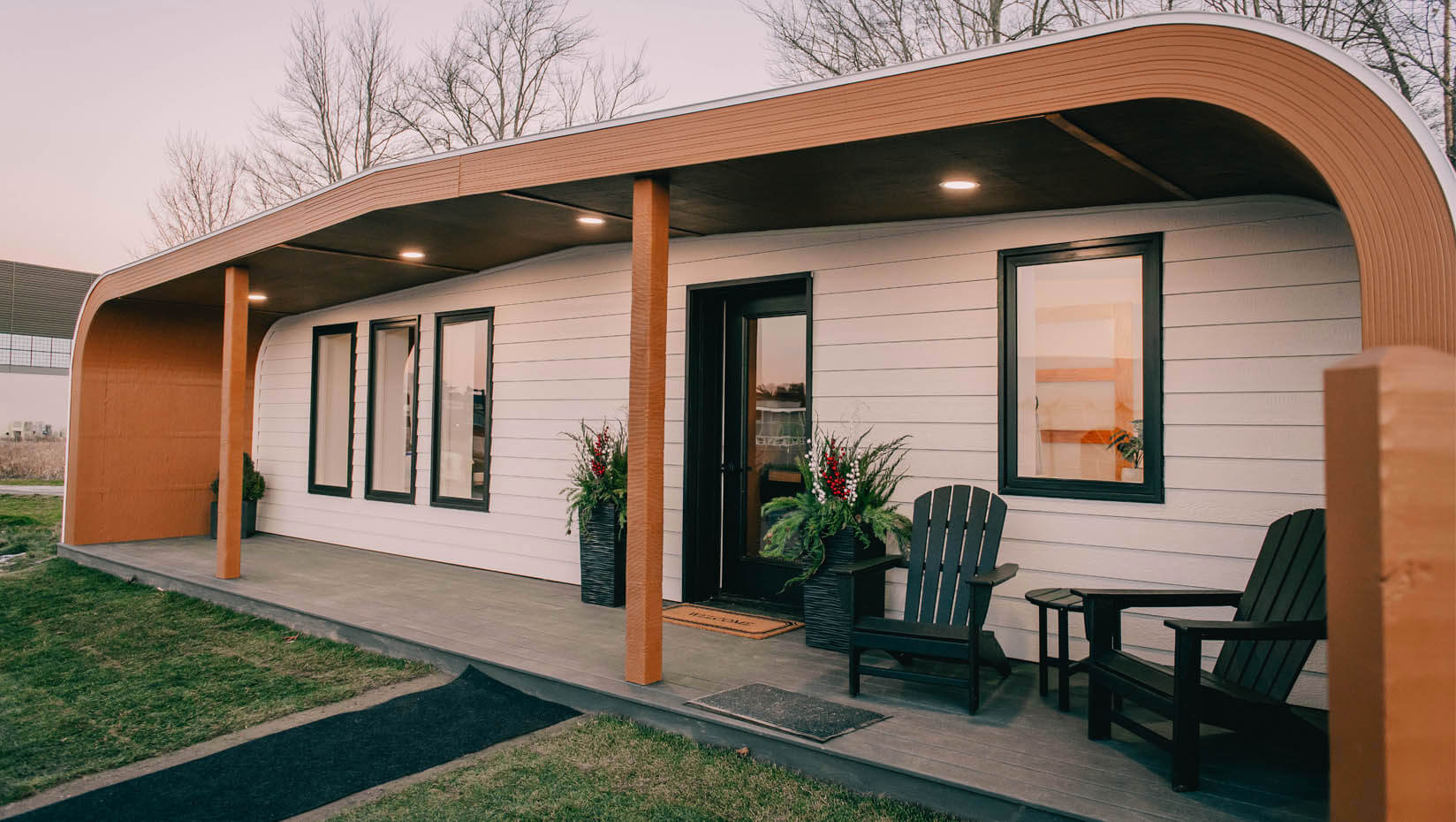
Les matériaux et les coûts ont toujours été mentionnés comme le plus grand défi de la FA, quelle que soit la technologie utilisée. Ces défis sont les mêmes, voire exacerbés, pour LFAM, car les applications couvrent différentes technologies.
En ce qui concerne les matériaux, la rugosité de la surface, la tolérance aux dommages, la résistance à la fatigue et à la traction inférieure, etc. sont autant de problèmes qui peuvent affecter une impression 3D. Ces problèmes sont souvent liés à une incohérence dans les propriétés des matériaux. Quel que soit le processus utilisé, ces problèmes peuvent toujours survenir lors de la fabrication d’applications grand format.
« Il peut toujours y avoir un défaut. Parfois, lors de l’impression, il est difficile de voir où se trouve le défaut. Pour un grand nombre de pièces que nous fabriquons – la plupart de nos pièces sont destinées à l’industrie aérospatiale -, nous fabriquons un moule ou un outil de formage à chaud ; ces pièces qui permettront au client de créer la pièce d’utilisation finale. Et lorsque ces problèmes surviennent, nous ajoutons un facteur de sécurité. Ainsi, même si un défaut altère les propriétés du matériau, la pièce finale est suffisamment solide ; nous combinons cela avec des essais non destructifs », déclare Calvert, ingénieur des applications composites chez Ingersoll Machine Tools. Selon l’expert d’Ingersoll, il existe un certain degré de déflexion admissible dans un moule au cours du processus de pose des fibres, qui permet de produire une pièce de haute qualité. Étant donné que le procédé d’impression vise à remplacer l’outillage métallique par un outillage polymère grand format fabriqué de manière additive, le procédé de fabrication doit résister aux forces du processus de stratification sans dévier (changer temporairement de forme) au-delà d’une certaine valeur. Cette déviation peut être mesurée afin de quantifier si l’outil répond aux exigences requises pour cette méthode de fabrication.
« Par ailleurs, il est également possible d’identifier ces défauts au fur et à mesure qu’ils se produisent en suivant les paramètres du processus à l’aide de systèmes thermiques et de vision. Toutefois, comme il s’agit d’une technologie très récente, la plupart des fabricants de machines dans ce domaine en sont encore à la phase de collecte des données. À mesure que nous obtenons plus de données sur ce qui se passe pendant le processus d’impression, nous pourrions utiliser l’apprentissage automatique pour identifier les paramètres qui doivent être adaptés et résoudre le problème afin de prédire les erreurs futures », ajoute Kyle Calvert.
N’oublions pas que Calvert partage son expertise ici en pensant aux polymères, en particulier aux granulés utilisés pour la technologie d’extrusion de polymères d’Ingersoll dont le volume de construction est supérieur à un mètre cube.
Il va sans dire que les solutions pour remédier à l’incohérence des matériaux varient d’un fabricant à l’autre et d’une technologie à l’autre.
Additive Engineering Solutions, LLC utilise actuellement la LFAM pour la production en série. Même s’il n’a pas précisé le type de LFAM qu’il utilise, Andy R. Bridge explique qu’il s’appuie actuellement sur un contrôle du processus basé sur les statistiques pendant le processus d’impression, suivi d’inspections dimensionnelles et parfois d’inspections de l’intégrité du vide, afin de remédier à ces incohérences.
À l’avenir, les matériaux qui apporteront un avantage substantiel en termes de performance et de résistance (aux UV et à l’eau en particulier) ouvriront probablement de nouvelles applications dans le segment de la LFAM. À ces éléments, Calvert ajoute des matériaux moins coûteux et des matériaux présentant de meilleures propriétés isotropes. L’ingénieur en applications composites insiste sur le fait que certaines de ces exigences peuvent être plus strictes pour certains utilisateurs, comme les fabricants de pièces pour l’aérospatiale.
« Pour les fabricants de pièces aérospatiales, le coefficient de dilatation thermique (CDT) n’est pas aussi bon que celui des métaux, car le matériau est un polymère. Lorsque vous essayez de mettre le moule dans un processus d’autoclave, il travaille plus que le métal. Plus ces polymères techniques s’améliorent, plus nous nous rapprochons du remplacement des métaux dans la fabrication des moules », note Calver.
Outre ces exigences techniques, il convient de noter que les formats de matériaux recyclés/réutilisés/upcyclés sont les prochains domaines d’intérêt que les fabricants aimeraient voir se développer.
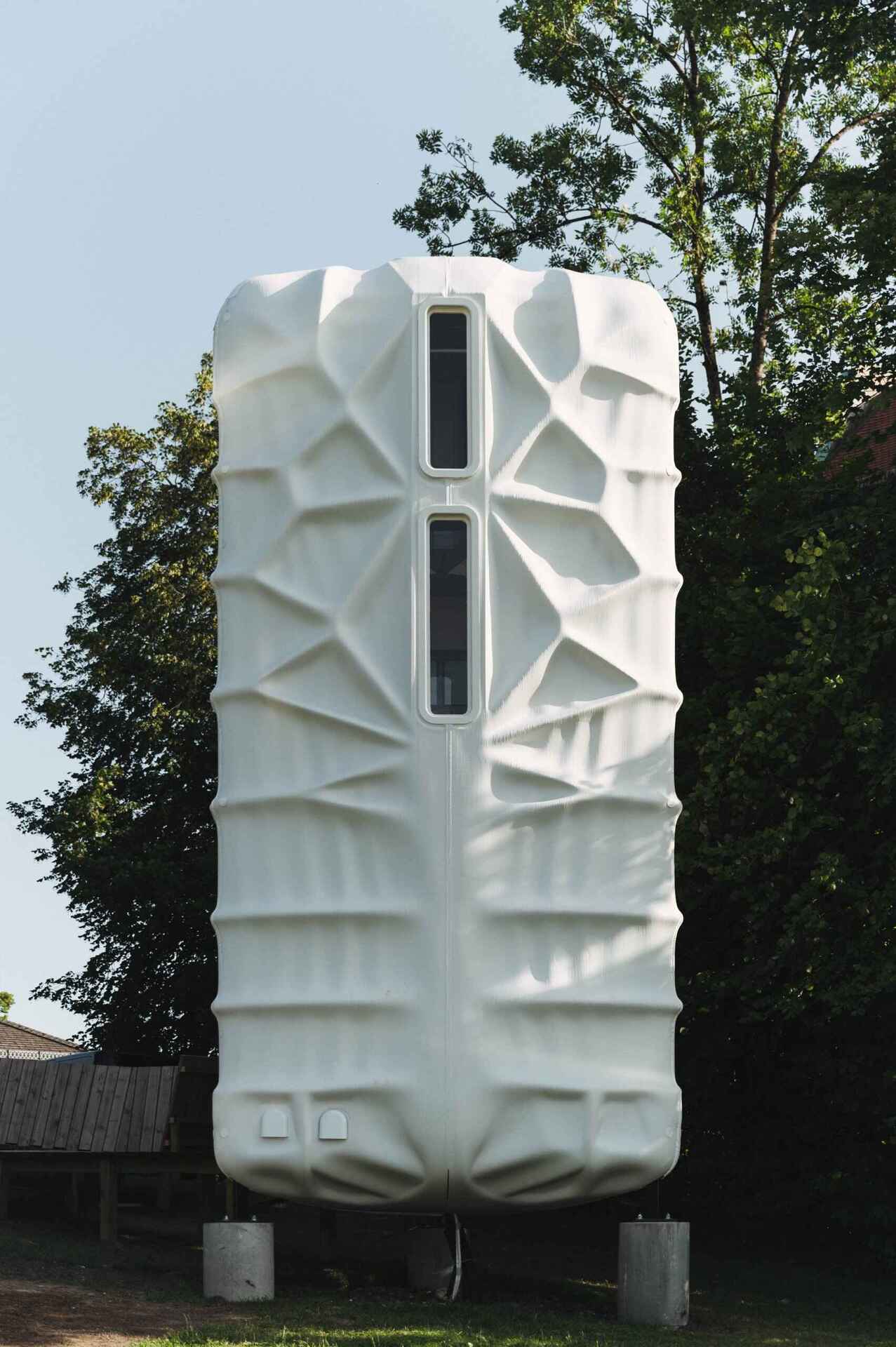
Une période difficile pour les plastiques en général
« Les plastiques en général ont du mal à rester à l’extérieur », souligne l’expert d’Ingersoll. « Les experts en matériaux ont travaillé sur l’ajout d’additifs dans le plastique afin qu’il puisse mieux résister aux UV et à l’eau, mais tant que nous ne disposerons pas d’un plastique capable de durer plusieurs années à l’extérieur, sous le soleil ou la pluie, il sera plus difficile d’adopter la LFAM à grande échelle. »
En outre, le coût est un autre élément clé qui empêche une plus grande adoption de la LFAM. Pour notre expert, les fabricants de machines dans ce segment de niche sont actuellement en concurrence avec les processus de fabrication conventionnels, le bois ou d’autres méthodes de prototypage bon marché pour la fabrication de pièces.
Cela signifie que :
- Si la production augmente et que le prix des matériaux baisse,
- Si de nouvelles pièces d’ingénierie dotées de meilleures propriétés matérielles permettent de fabriquer des pièces d’utilisation finale et pas seulement des moules ou de l’outillage, il y a de fortes chances que les fabricants de machines de ce segment de niche soient en mesure d’améliorer leur compétitivité,
- Il y a de fortes chances que davantage d’industries adoptent les technologies LFAM à base de granulés.
Matériaux utilisés dans d’autres processus
Si nous n’avons pas identifié de particularités pour d’autres procédés, c’est simplement parce qu’il n’y a pas de problèmes spécifiques que l’utilisateur d’un procédé de FA standard ne connaisse pas déjà. Comme ces matériaux sont généralement les mêmes, mais utilisés à plus grande échelle, les principaux problèmes qui nécessitent une attention particulière sont généralement observés au niveau de la conception et/ou du processus d’impression.
À cet égard, Ferguson d’Autodesk prévient que « la tendance est aux machines à lit de poudre de plus grand format, ce qui nécessite une plus grande attention lors de la préparation de la construction, du parcours de l’outil et des étapes de simulation, car plus les pièces imprimées sont grandes, plus le coût de l’échec augmente de façon spectaculaire ». Anticiper les problèmes potentiels avant de commencer l’impression est donc important. « Netfabb permet par exemple de simuler des parcours d’outils DED pour l’analyse thermique et mécanique. Cela permet aux utilisateurs d’observer la température interne de l’ensemble du modèle pendant qu’il est imprimé, et les aide à décider quand ajouter des pauses dans le parcours de l’outil pour le refroidir. Il est même possible de prédire à quoi ressemblera la forme déformée finale », ajoute Ferguson.
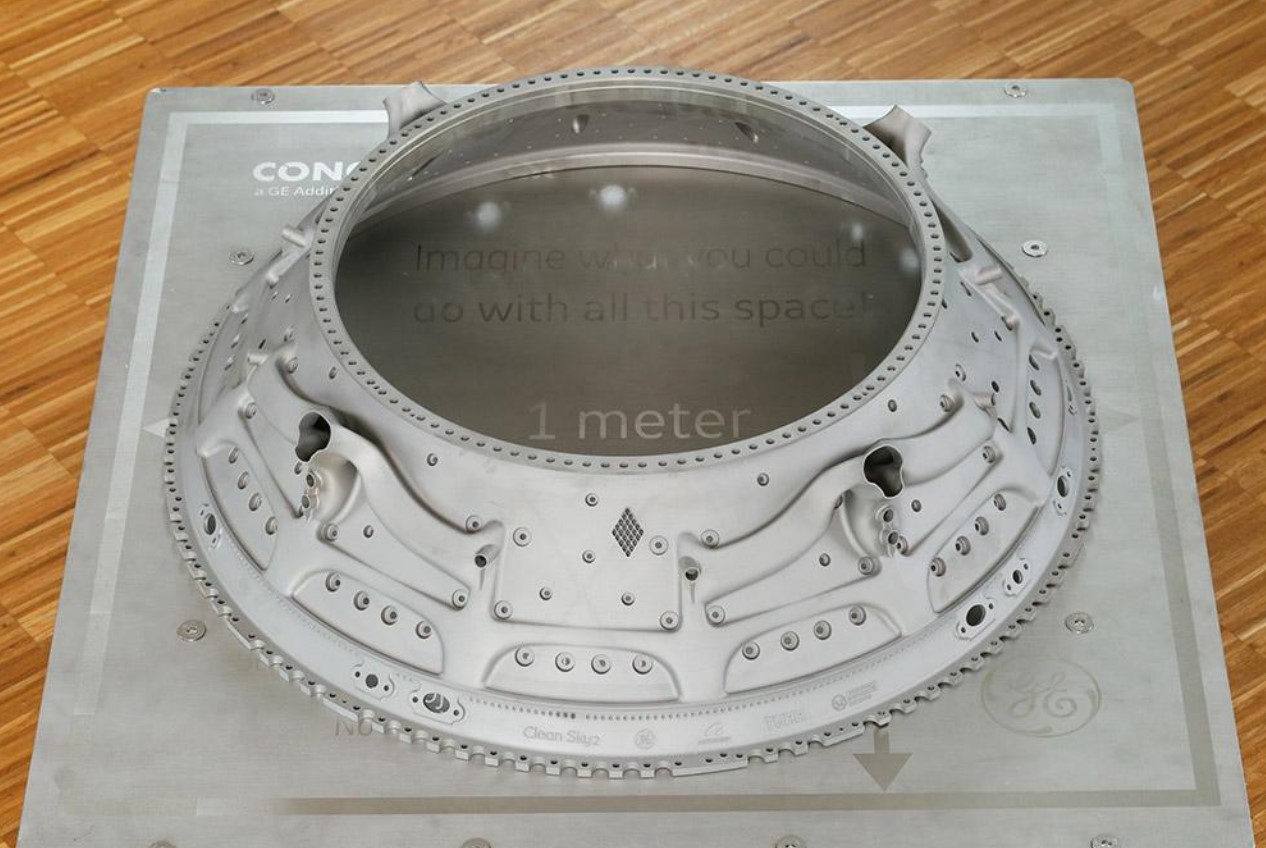
Cela dit, Fusion 360 dispose d’autres outils qui peuvent également contribuer à une bonne impression avec la LFAM, pour les plastiques et d’autres matériaux qui peuvent avoir des motifs de remplissage complexes. Le fournisseur de logiciels a récemment introduit le Volumetric Latticing, un outil qui permet aux utilisateurs de créer des structures de remplissage qui peuvent apporter de la résistance tout en utilisant moins de matériau, répondant ainsi aux exigences en matière de coût, de poids et/ou de durabilité.
Les pièges courants de la fabrication additive à grande échelle et autres considérations relatives aux coûts
Tout comme la FA en général a conduit de nombreux industriels à avoir une appréciation erronée de la technologie, les processus LFAM peuvent souvent induire des attentes déguisées pour ceux qui ne sont pas familiers avec les différentes technologies.
Sur la base des informations fournies par Ferguson, Calvert et Andy R. Bridge, nous pouvons d’ores et déjà signaler les pièges ci-dessous :
- La LFAM ne remplace pas les processus de FA existants, elle les complète. Pour les grandes pièces, il ne s’agit pas de remplacer d’autres formes de FA ; il s’agit de remplacer la fabrication manuelle des pièces à partir de zéro ou les processus soustractifs traditionnels.
- Étant donné que la plupart des procédés LFAM comportent une fonction robotique, les gens pensent souvent qu’il s’agit de systèmes prêts à l’emploi. Les opérateurs doivent toujours être bien formés. Plus les processus seront automatisés, plus le processus de formation sera rapide.
- Des grandes impressions et plus de matériaux signifient qu’il est coûteux d’avoir un défaut d’impression. Analysez les impressions d’essai pour bien comprendre votre processus, essayez de connaître vos problèmes avant qu’ils ne surviennent. Déterminez si les sections défectueuses peuvent être coupées et/ou réparées.
- La plupart des machines LFAM de plus d’1 m x 1 m x 1 m ne sont pas des machines produites en série. Il s’agit généralement de systèmes sur mesure ou en phase de démarrage, qui peuvent donc être difficiles à utiliser et nécessiter un logiciel sur mesure.
- Ne pas connaître suffisamment bien un processus peut être considéré comme un piège, qui coûte plus cher (gaspillage), introduit des points de concentration de stress, une sous-impression ou une surimpression, etc. Le débit de matériau sortant d’une buse, par exemple, ajoute sa propre difficulté et n’est pas spécifique à un processus. Dans de nombreux cas, il n’est tout simplement pas possible d’interrompre ou de modifier la vitesse d’extrusion à la volée, ou alors c’est une perte de temps considérable.
- Il convient de garder ceci à l’esprit : outre les coûts d’investissement pour l’équipement d’impression grand format, il y a de nombreux autres domaines de coûts à prendre en considération. Il s’agit notamment des logiciels, de l’expertise en matière de polymères, de l’expertise en matière de conception, du contrôle des processus, de l’investissement en ingénierie et de la formation. Certains produits finaux, comme l’outillage pour l’aérospatiale, nécessitent également des fraises CNC de précision à grande échelle.
- Enfin, parfois, ce ne sont pas les coûts qui comptent, mais les délais.
À ce jour, l’industrialisation reste un objectif à atteindre pour ceux qui explorent l’utilisation des technologies LFAM. Les cas d’utilisation déjà développés avec les processus vont des prototypes à la production de petites séries dans les secteurs de l’aérospatiale, de la marine et de la construction.
Ce que nous trouvons le plus intéressant, c’est cette tendance dans l’industrie de la construction – où il y a un besoin de réduire les heures de travail. Par ailleurs, les applications dans ce domaine révèlent que l’impression 3D béton n’est pas toujours le seul candidat à la production qui peut être utilisé pour atteindre cet objectif.
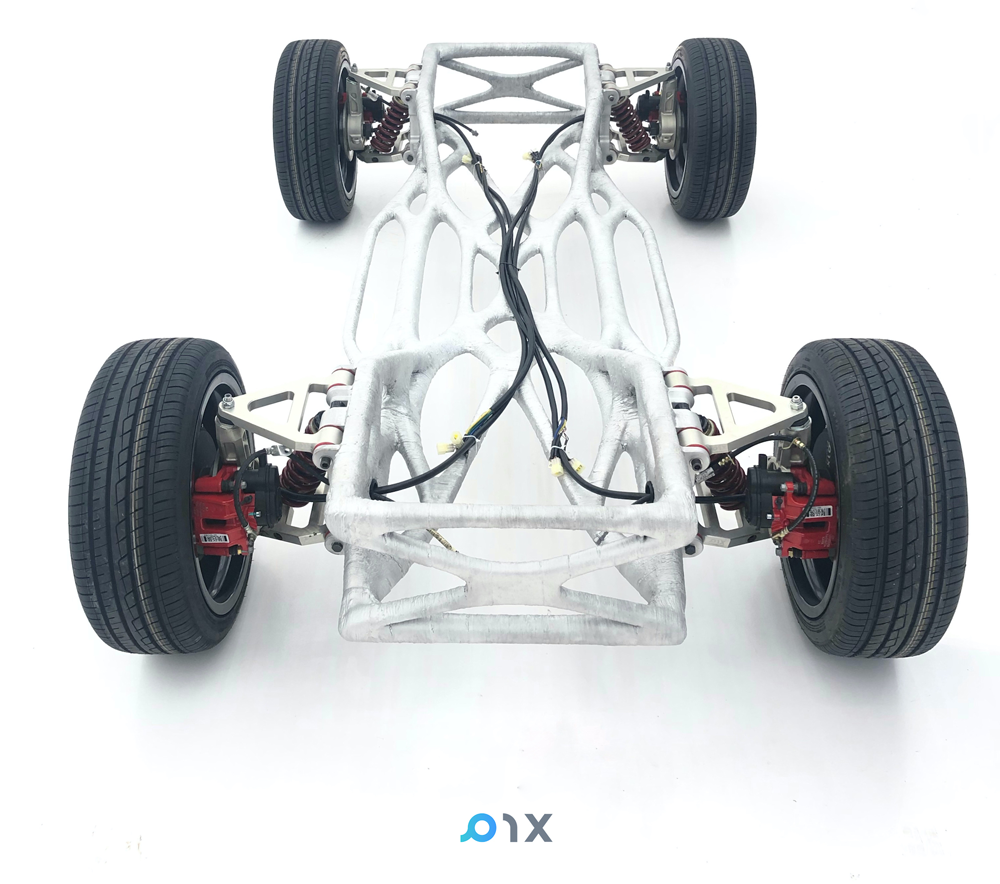
Quelques mots sur les entreprises participantes
Additive Engineering Solutions (AES) est une entreprise de fabrication avancée qui fournit des solutions de fabrication additive polymère grand format (LFAM). Qu’il s’agisse d’imprimer en 3D des outils et des moules de grande taille pour l’industrie aérospatiale et de la défense ou d’imprimer des pièces d’utilisation finale de grande taille pour les marchés des véhicules aériens autonomes, AES a l’ambition de démontrer sa capacité à fabriquer une variété de produits avec plus d’efficacité et de personnalisation que les méthodes traditionnelles. L’entreprise envisage d’explorer les matériaux vitrimères dans un avenir proche pour les applications LFAM.
Autodesk est un éditeur de logiciels qui propose plusieurs solutions susceptibles d’aider le LFAM, allant du simple tranchage 2,5D au tranchage multiaxe et non plan, à la capacité de piloter des machines de bureau, des machines hybrides et des robots, et à la possibilité de simuler des empreintes métalliques afin de détecter les problèmes éventuels avant d’entrer dans la machine. Autodesk propose des logiciels qui couvrent la majeure partie de l’espace additif, y compris le LFAM. L’un des problèmes rencontrés dans tous les secteurs d’activité est l’idée que les données sont séparées, généralement programmées dans un logiciel distinct de celui de la conception. Dans le cas de la fabrication additive, et en particulier du LFAM, le fait de devoir passer d’un logiciel de conception et d’un logiciel de programmation à l’autre pour modifier la conception signifie beaucoup d’exportations et d’importations. Les solutions logicielles de l’entreprise sont conçues pour éliminer ce problème et permettre un flux de travail plus transparent.
Ingersoll construit de grandes imprimantes 3D à polymères et des machines automatisées de placement de fibres. Le portefeuille de l’entreprise comprend des imprimantes à portique et des imprimantes 3D robotisées. Toutes les machines sont hybrides et peuvent être équipées de fonctions d’impression, de fraisage, de placement automatisé de fibres (AFP) ou de pose automatisée de bandes (ATL). Ingersoll propose également des services d’impression par contact pour l’outillage aérospatial, l’industrie maritime ou les applications de meubles grandeur nature.