Despite the tangible benefits AM can bring in the production of electric motors, this application still remains one of the most complex ones for the industry. One company of the industry has been specifically created to support the development and commercialization of this application, and recently a new consortium has also announced its commitment to an electrified future. From the 3D printer manufacturers’ side of the industry, ExOne is the first to officially announce its interest in tackling this topic. The future company of Desktop Metal will work alongside Tennessee-based startup Maxxwell Motors, a company that specializes in Axial Flux motor development. In a few words, Maxxwell Motors’ mission consists in accelerating the transformation of electric motor design & manufacturing with a portfolio of motor and generator solutions.
Together, both companies will work on the development of a unique copper e-winding design for its axial flux electric motors, which can be used in electric cars as well as a range of other heavy-duty vehicles and industrial devices.
A smooth transition to hybrid and pure electric power vehicles
Optimized copper windings and rotors in electric motors are a major enabler in the transition to hybrid and pure electric power vehicles. As explained in an article dedicated to the reasons why there is a business model for AM in the electric motor market, most existing manufacturing processes for windings are expensive, and often limit designs in a way that also limits their performance.
A proof of concept has already demonstrated ExOne’s binder jetting ability to design in a way that removes many of the hurdles that come with traditional manufacturing. While additional development and testing are now underway, let’s note that Maxwell’s ultimate goal is to binder jet 3D print winding assemblies as a monolithic piece, eliminating the need for coil wrapping, bending, tooling, and welding of individual parts together.
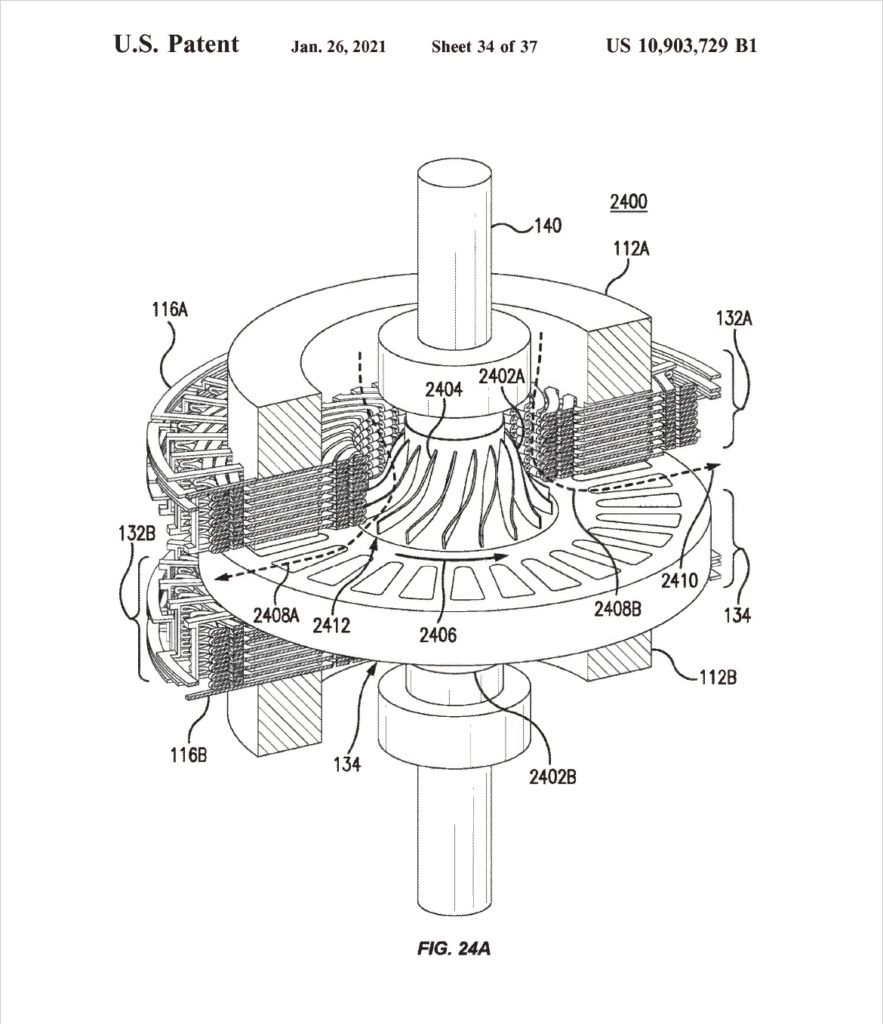
“When we 3D print it, a lot of the challenges just go away, and we can actually improve the performance of the motor itself,” Maxwell’s CEO Michael Paritee said. “At Maxxwell, we’re taking the most sustainable, and additive manufacturing, point of view as possible to truly improve efficiency, reduce waste and optimize performance.”
Indeed, ExOne reminds that when produced with binder jet 3D printing, the final part would require less manufacturing steps and energy utilization, as well as less material waste to produce – also resulting in components that are more efficient and deliver improved performance. What’s more, high-speed binder jetting is relatively affordable.
“The ExOne team is proud to work with both traditional manufacturers and visionary startups working to change the world with innovative concepts such as these,” said John Hartner, ExOne’s CEO. “As the automotive industry enters a new era of electrification, our world-class team of engineers stands ready to help solve some of the most pressing challenges with our binder jet 3D printing technology.”
Remember, you can post job opportunities in the AM Industry on 3D ADEPT Media free of charge or look for a job via our job board. Make sure to follow us on our social networks and subscribe to our weekly newsletter : Facebook, Twitter, LinkedIn & Instagram ! If you want to be featured in the next issue of our digital magazine or if you hear a story that needs to be heard, make sure to send it to contact@3dadept.com