In the industry, most engineers that are able to print something that was not previously possible to achieve, leverage generative engineering. Very few companies develop generative engineering design software, yet they are uniquely positioned to disrupt the industry. One of these companies is ELISE GmbH.
Backed by BMW Group, ELISE develops an open software platform that helps engineers accelerate product design and automate the development process.
At the 4th AM Forum in Berlin, one of the developers told 3D ADEPT Media, they have been working for several years to respond to a single question: “How to empower engineers so that they develop complex structures in a short time & close the gap between development & production?”
Rather than delve into long explanations, the company recently unveiled an example of application that literally answer this question: a 3D printed bike.
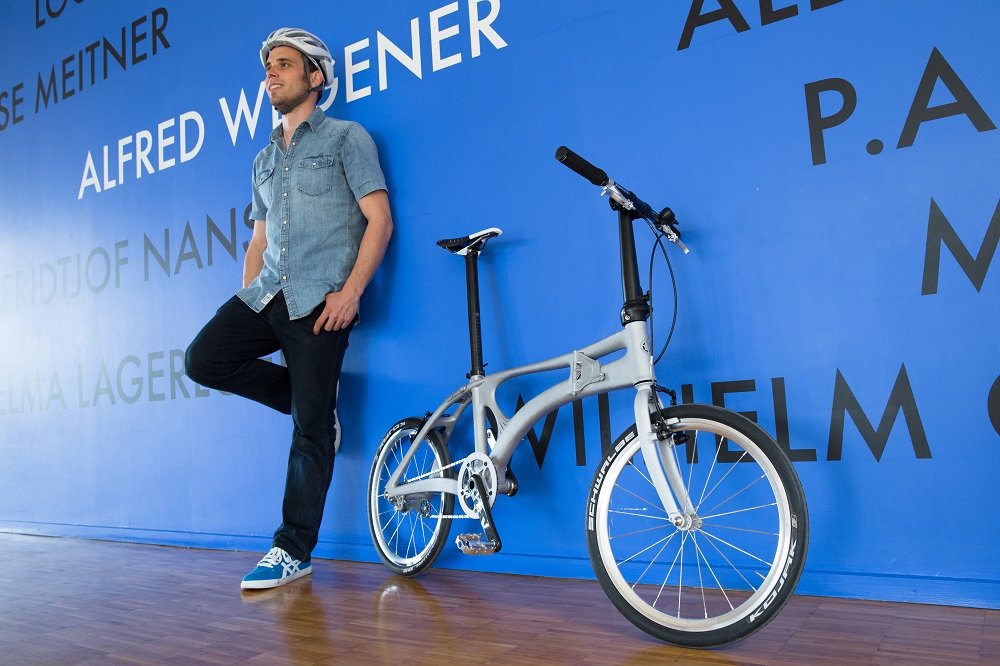
The company said this bike is “inspired by nature”. By using their software to develop the bike’s design, the computer has helped the developer calculate several design variants.
Furthermore, thanks to topology optimization, the engineer quickly assessed critical load paths as well as parametric optimizations with evolutionary algorithms, required to determine the appropriate frame geometry of the bike. CAO on the other hand, helps minimize notch stresses during the production.
“The pipes of the Bionic Bike are not hollow at all points and have no uniform thickness. Instead, they consist of a completely new lattice construction on the inside in high-loaded areas.
In this way, the frame is custom-made for a specific user. For a lighter cyclist, the algorithm would construct it differently without much effort. Once the DNA is created, you could also easily change the bike type and transform the folding bike into a mountain bike in no time. It thus frees the developers from many constraints and helps them to create better products”, said the company on its LinkedIn page.
Generative Engineering Design methodology therefore allows for an automatic adaptation of detailed design in case of styling modification, leading to automatically recreated linked features such as component boundaries, if the designer’s vision evolves.
3D printed with aluminium, the bike would be 60% lighter than classically developed bike designs. Furthermore, using the DNA established engineering methods; the engineer would save 74% of time in product development.
Last but not least, “the integration of adaptive lattice structures ensures an additional reinforcement in highly loaded areas inside the frame. These fine-tunings and the transfer of mechanical principles inspired by lightweight structures of diatom shells led to the development of an outstanding product”, we read on the company’s website.
Remember, you can post AM job opportunities for free on 3D ADEPT Media or look for a job via our job board. Make sure to follow us on our social networks and subscribe to our weekly newsletter: Facebook, Twitter, LinkedIn & Instagram! If you want to be featured in the next issue of our digital magazine or if you hear a story that needs to be heard, make sure to send it to contact@3dadept.com