Composite 3D printing is not just about materials as we recently discovered with Anisoprint. Like other AM technologies, it’s also a matter of software and one company we are closely monitoring in the field is e-Xstream engineering.
The company of Hexagon’s Manufacturing Intelligence division has unveiled new simulation and virtual manufacturing capabilities of its Digimat software that would allow engineers to weigh up the production cost of composite 3D printing.

If you are an attentive reader of 3D ADEPT Media, then you know from one of our conversations with e-Xstream that the company develops tools that can speak “the AM language” and DIGIMAT is its simulation software platform designed for the modeling of composite materials.
As many professionals usually compare the production cost of 3D printing with the cost of the same part via conventional manufacturing processes, the latest version of DIGIMAT meets this specific need and more. It also improves engineers’ virtual engineering processes by validating the composite’s microstructure with CT scans of manufactured parts.
This means that in your cost evaluation, if you want further details about material utilisation, employee time, energy, and the required post-processing steps, DIGIMAT got you covered. Such a holistic approach for cost evaluation goes beyond the simple quest for the ideal process chain for production.

According to the company, “it can also be used to perform batch optimisations to print as many parts as possible in parallel, increasing production capacity and reducing lead time. It can also be used in production planning, to consider the total cost of ownership of machines and amortise those costs over the projected production volumes. This information is visualised for the user through plots and pie charts, so the cost breakdown can be easily analysed for different scenarios.”
Improving performance predictions with CT scans
The software company lay emphasis on the platform’s capability to reduce some technical challenges.
After a CT Scan of the part for instance, operators can import the 3D RAW image to build a finite element model of its two-phase microstructure (eg. carbon fibre reinforced polymer) in Digimat and model its behaviour. The company explains that by embedding this validated material model in their Computer Aided Engineering (CAE) tools, a design engineer can perform analyses that account for variations within a manufactured part to reduce material use or avoid points of failure.
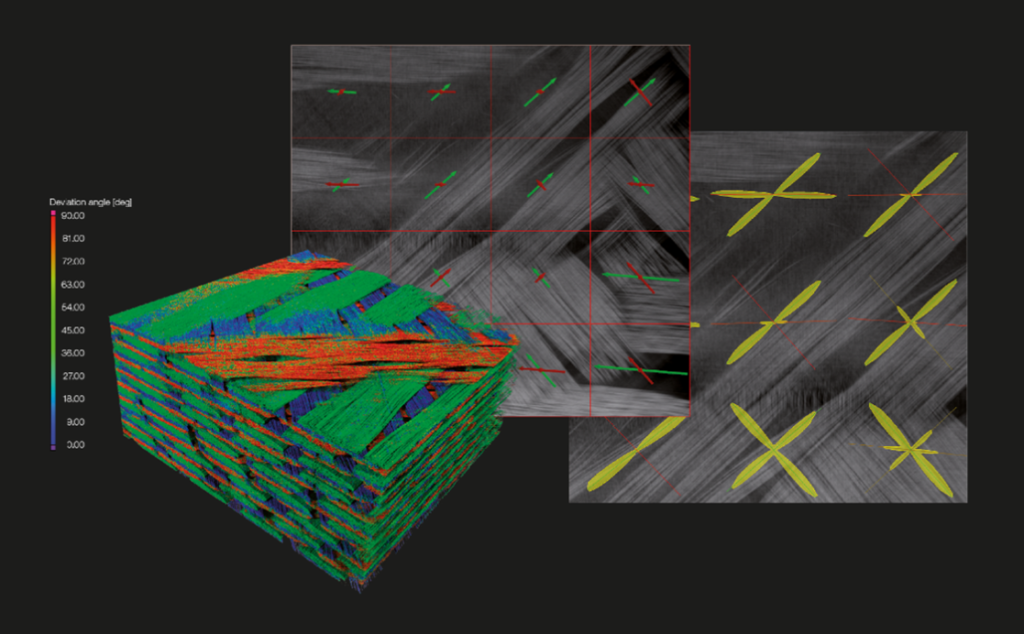
Connecting physical measurement with virtual testing also improves the accuracy of Integrated Computational Materials Engineering (ICME) processes when a new material system is introduced. The part performance can be compared to the simulated process to validate and certify the material model. CT scan validation also supports helps materials professionals refine the microstructure models they have built manually to improve the accuracy of future simulations.
When refining new manufacturing processes, users can capture information about the part, material, 3D printer or process used and their physical tests as they work using material lifecycle management. e-Xstream engineering’s MaterialCenter software captures a traceable, validated database of those trusted material properties so that they can be used in the design phase of a product. Using material lifecycle management, information can be easily documented within multi-disciplinary teams and shared throughout an organisation capturing valuable knowledge for reuse by authorised users.
Predicting the material behaviour of a CT-scanned microstructure is a computationally intensive process, for example it could take several days to analyse complex behaviour such as creep using Central Processing Units (CPU) computing only. By optimizing these processes for Graphics Processing Units (GPUs), some tasks can now be performed interactively by the engineer because results are produced in minutes. Benchmarks show the time required to analyse the stiffness of a material is reduced by 98%. This rapid solve time, combined with the introduction of a command line interface, also enables the use of Digimat finite element models within automated cloud-based optimization workflows on high performance computing platforms.
When producing high performance structures such as aerospace components from composites, the Progressive Failure Analysis (PFA) model makes it possible to define safety margins for a structure and make optimal use of the expensive materials and processes. The latest version of Digimat performs these complex Camanho model analyses twice as fast, making it possible to perform a parametric study to define defect tolerances and maximise production yields.
Remember, you can post free of charge job opportunities in the AM Industry on 3D ADEPT Media or look for a job via our job board. Make sure to follow us on our social networks and subscribe to our weekly newsletter : Facebook, Twitter, LinkedIn & Instagram ! If you want to be featured in the next issue of our digital magazine or if you hear a story that needs to be heard, make sure to send it to contact@3dadept.com