Designing in additive manufacturing is almost always linked to the part an engineer will model with the right software tool. It’s right but there is more. Remember when we told you that the true success of an application usually depends on an underappreciated component: material? Here is the thing, when we look at metal and polymer powder materials for instance – which are the most widely used types of materials in AM -, we come to realize that only a short number fulfills the requirements to comply with up-to-date additive processes routes. The reason for this is simple: many powder materials deliver insufficient characteristics for their processability and to achieve the desired part properties. To address those limitations, companies like Dressler Group (DG) have been working hard to help industrials (including material producers & OEMs) make the right choice when it comes to the selection and design of powder materials for AM.
To address these limitations, those powder designers often bring a multi-disciplinary expertise around the table. In Dressler Group’s case, the company’s expertise in grinding and finishing has been instrumental to advise manufacturers across industries. Founded in 1978, the family-owned business has always been active in research and development. Over the years, the company has built up a portfolio of services that includes all types of grinding and complete warehouse, packaging and shipping logistics. The company can conduct test grindings from just a few grams to individually specified large quantities, with absolute reproducibility and just-in-time production.
In 2015, DG decided to expand its activities into the AM industry. Following a few pilot projects in 2016, the company reached a turning point in its journey when it joined HP’s open material platform as key material developer.
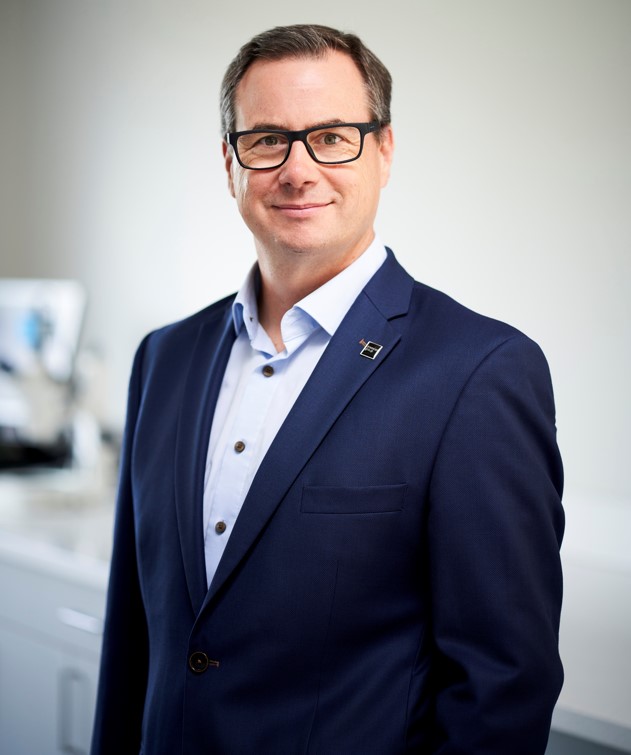
That being said, DG’s key focus has always been on plastics. This focus on plastics is quite understandable when we see their massive use in additive manufacturing, all technologies included. Jan Dressler, CEO of Dressler Group notes: “the majority of industrial systems are set up to work with plastics, and plastics continue to be processed in greater volumes than metals”. The CEO does not deny the importance of metals in certain industries (and applications) like aerospace, but highlights the increasing trend to explore plastics in metal-replacement applications:
“3D printing [may have] a much more spectacular impact in aerospace engineering when compared to plastic applications for the lifestyle sector, such as in shoe manufacturing” but [interest in plastics grows even further to reduce weight. “Attempts are being made to replace metals with plastics in industries like aerospace, car manufacturing, and robotics. In many cases, high-performance materials such as PEEK and PEKK can act as substitutes for aluminium”, Dressler adds.
Another advantage I see, when I think of polymers is that they deliver excellent possibilities of "custom-made" manufacturing, thanks to the diversity in their molecular structure, and the cost-effective material base and production processes. Somehow, this urges to explore the tailor-made production of technically sophisticated parts for automotive or other demanding industries but the currently available range of basic materials, let alone their modifications, is still limited – especially when it comes to their processing by laser-based AM processes. PP & TPU remain for instance, two of the most commonly used plastics in AM technologies based on powder-bed processes.
“They rank as good to very good when it comes to processability”, our guest in this Opinion of the Week outlines. “Engineering plastics are already well suited to handling a wide range of AM powder bedding processes. However, basic and high-performance plastics still show plenty of potential. Here, the use of cheaper basic plastics is important in order to reduce component costs and bring them into line with what’s considered competitive in classic manufacturing processes.”
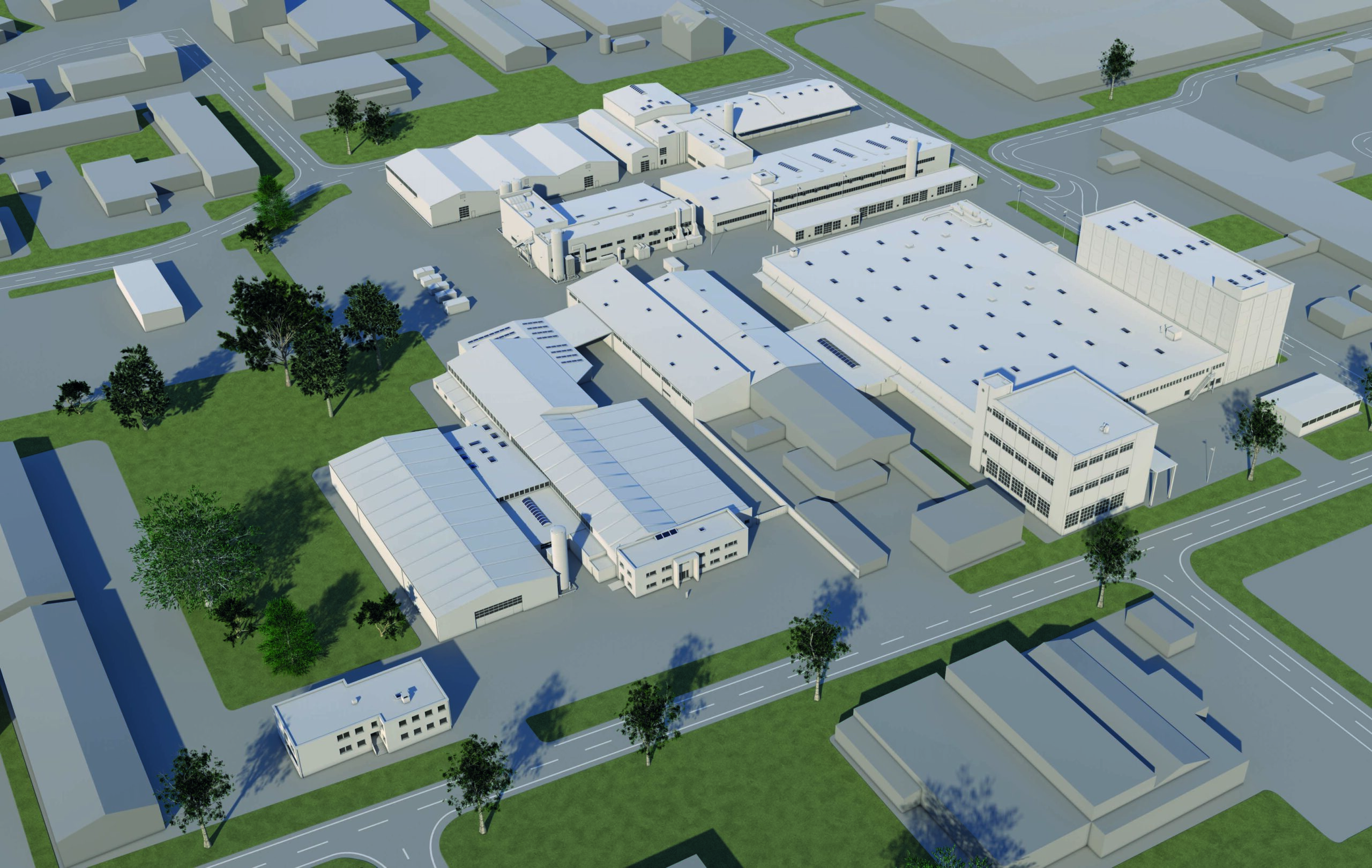
Dressler recalls that his company was the first to grind TPU to a level of quality suitable for AM. While they achieved the same with polypropylene (PP), he alerts on the fact that, when it comes to the selection and design of materials, other factors now come into play in decision-making processes, factors that include for instance “sustainability, recyclability, bioplastics, etc.”
However, if it makes sense to take into consideration these factors given the most pressing issues related to climate change but let us not forget that the most affected stakeholders (material producers) in this debate should remain profitable. In AM especially, industrialization usually leads to profitability. The one-million-dollar question in this equation therefore is: can recycled materials (and derivatives) drive industrialization?
Dressler attempts to provide a response: “In our opinion, on the whole, recycled materials are suitable for demanding industrial applications. However, they do not perform yet as highly as a "virgin" raw material would. To give an example, we know that when using polyamide 12 in laser sintering the material ages significantly during the process. What happens to the material and powder here is highly complex [but that’s a different topic]. However, what we can say is that in the process of building an average building, approximately 10 to 20% of the materials used are converted into components. A further 25 to 40% of the powder is less thermally stressed and can therefore normally be reused without any issues. The remainder is so heavily stressed that it has to be refreshed with about the same amount of new powder before it can be recycled. Other materials, such as PP, are inherently less sensitive to ageing, but filled polyamides (filled using reinforcing materials) are even more sensitive than unreinforced polyamides.
A lot is happening in this area at the moment, however. For example, a novel approach in process technology should make it possible in the future to combine 80% reused materials with 20% new materials, with tolerable quality loss.
Recycling will become increasingly prevalent in the future, however, simply due to stricter environmental regulations and cost pressures, even in high-tech applications.”
Addressing the current needs right now, with the right tools.
In six years of activities in the AM industry, DG has evolved more or less away from the trade press, in stealth mode – a fair strategy for all companies looking to adequately demonstrate proof of concept.
Grinding may still be at the heart of its AM business, but I believe the company creates the most value with holistic “plug and play” solutions that deliver seamless batch-to-batch quality thanks to their “powder design”. That’s anyway how AM business works.
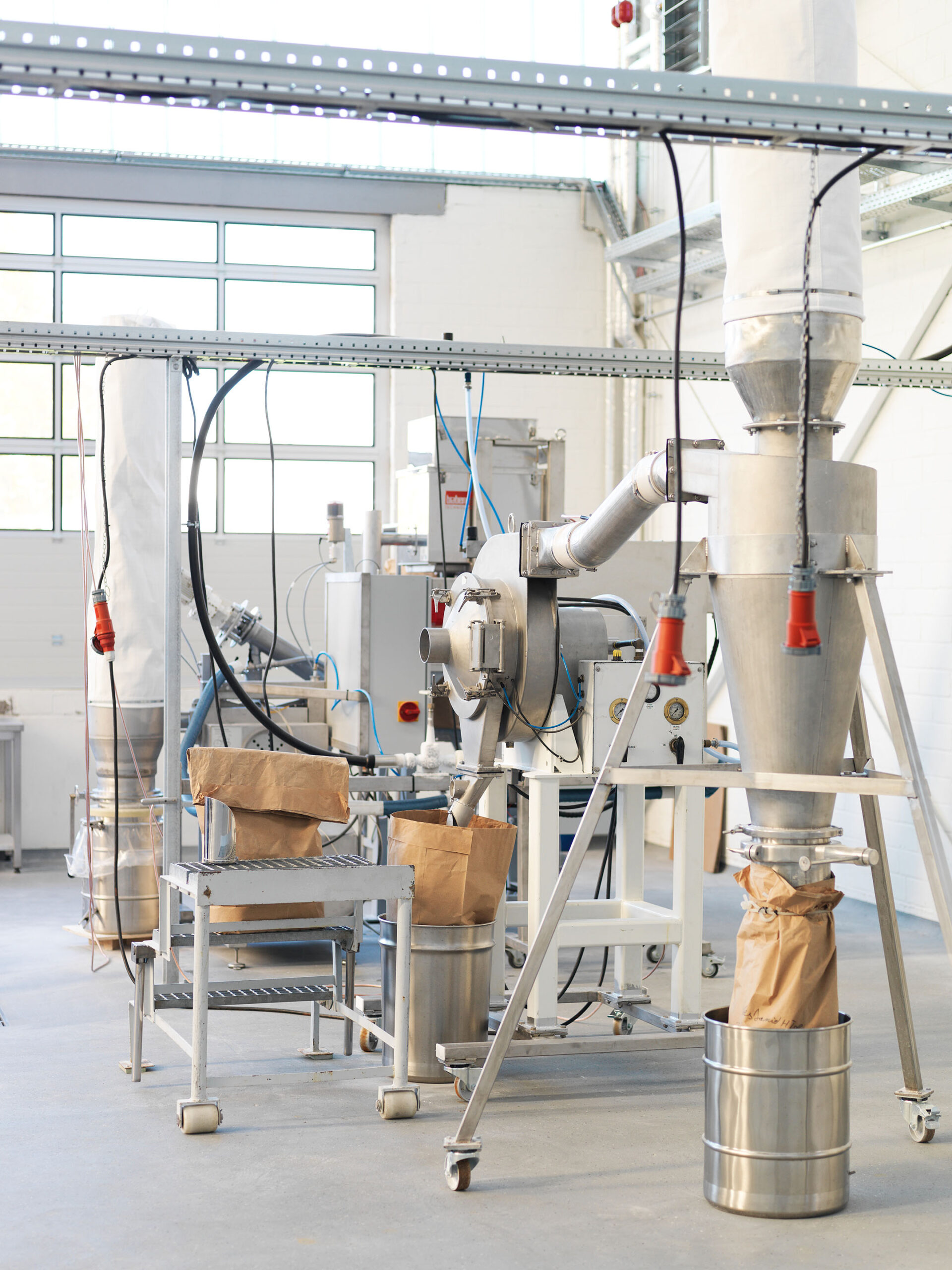
“When manufacturing on an industrial scale, high batch-to-batch consistency is essential. We set high standards in this regard, not least of all for ourselves. Over the years we have documented our methods and processes so they can be replicated at any time. Moreover, our grinding techniques are energy-efficient and also take into account factors like generating as little dust as possible, ensuring very little post-processing is needed, etc.
In order to avoid rejects in production, materials that are tough to process are just as important to us as a powder manufacturer as they are for the end user. A major challenge in the future will be resource conservation through reducing energy usage, avoiding waste, as well as the remanufacturing and more intensive use of materials and auxiliary materials”, Dressler lays emphasis on.
The powder designer and long-term systems partner may be acknowledged as "The Grinding Authority"; nevertheless, moving forward, the company ambitions to earn the same reputation for megatrends like optimising the circular economy for example.
“To our mind, environmental sustainability also has huge economic potential for powder and processing quality through developing new materials and construction processes, for example. Our powders should not only offer real added value to our customers, but also to their customers”, the CEO concludes.
Remember, you can post job opportunities in the AM Industry on 3D ADEPT Media free of charge or look for a job via our job board. Make sure to follow us on our social networks and subscribe to our weekly newsletter : Facebook, Twitter, LinkedIn & Instagram ! If you want to be featured in the next issue of our digital magazine or if you hear a story that needs to be heard, make sure to send it to contact@3dadept.com