The launch of Desktop Health, a healthcare business within Desktop Metal, first saw the development of material solutions that could be leveraged with EnvisionTec’s photopolymer 3D printers. The machine manufacturer has just expanded this dental technology portfolio to include a technology solution it has a deep expertise in: metal binder jetting.
To do so, it has updated its famous Shop SystemTM so that it can meets the requirements of dental labs.
At the heart of these upgrades, one notes that the Shop System removes labour costs associated with machine programming required for CNC milling, typically a common manufacturing process for producing metal dental components.
Desktop Metal reminds that this machine can print up to 32 partials in less than four hours, as compared to the nearest competitive system which supports up to 10 partials in 9 ½ hours. In addition, metal parts on the Shop System print fully supported in the powder bed and feature hand-removable sintering setters, drastically reducing labour time and costs associated with post-processing parts printed on laser-based 3D printing systems.
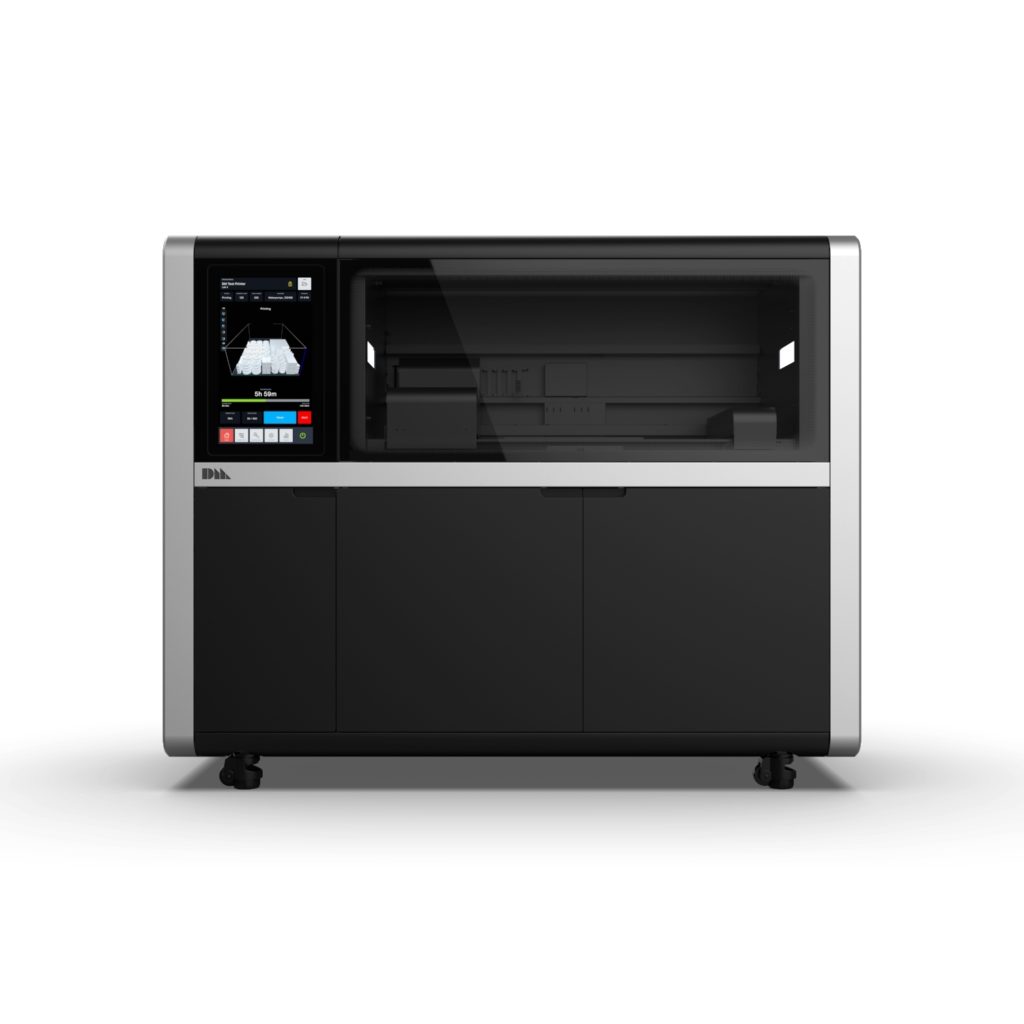
Furthermore, according to the manufacturer, by reducing post-processing and providing high throughput printing, the Shop System can drive down part costs for custom dental applications, such as partials, to as low as one-third the cost that can be achieved for comparable part quantities produced using laser-based 3D printing systems.
“We are excited to introduce the Shop System and chrome cobalt for binder jetting to the dental community, expanding our suite of best-in-class 3D printing solutions from photopolymers to metals,” said Michael Jafar, President and CEO of Desktop Health. “We are uniquely positioned by offering dental labs not only a leading photopolymer platform, but also a turnkey solution to produce metal appliances and surgical guides with superior surface finish in higher production volumes compared to laser-based 3D printing systems.”
Other key benefits of the Shop System include a user-friendly software interface, variable build sizes up to 16L and a high-speed, single pass print carriage as well as a print quality which is enabled by the 5x nozzle redundancy on the printhead.
Remember, you can post job opportunities in the AM Industry on 3D ADEPT Media free of charge or look for a job via our job board. Make sure to follow us on our social networks and subscribe to our weekly newsletter : Facebook, Twitter, LinkedIn & Instagram ! If you want to be featured in the next issue of our digital magazine or if you hear a story that needs to be heard, make sure you send it to contact@3dadept.com