The rise of ‘Metal Injection Moulding-like’ Additive Manufacturing processes seems to be linking to previous technologies that were leveraged way before the fast adoption of metal AM technologies. In the following dossier, Ralf Carlström of Digital Metal, Larry Lyons of Desktop Metal and John Hartner of ExOne review how one technology has led to the success of the other. They also compare the potential and limitations of binder jetting and MIM in manufacturing and explain why metal binder jetting is taking off as a new manufacturing technology.
MIM has come a long way since the early days, and its operators have proven that this technology is capable of reliable high-volume production and strong material properties. On the other hand, with the growing adoption of AM technologies that rely on a sintering process as a final production stage, a key focus is often made on “MIM-like” AM processes.
Several questions led to this investigation: why do we associate MIM to binder jetting? What are the real advantages of MIM? Will binder jetting replace MIM over time? Are applications the same for each technology? Several references have been consulted to confirm the validity of our assertions and the expertise of participating companies has been a key strength to remove uncertainties.
All participating companies specialise in metal additive manufacturing. Some of them shared their experience in both MIM & Metal AM.
Whilst this dossier will give a more detailed overview of these technologies, the article aims at guiding prospective users to identify the technology that best meets their needs.
The evolution of Metal Injection Moulding (MIM)
Thirty years ago, MIM first came onto the manufacturing scene. The technology is seen as a combination of plastic injection moulding and traditional powder metallurgy. Experts of the field even consider the manufacturing technique as a branch of both technologies.
Indeed, one similarity between MIM and plastic injection moulding is observed when the material is fed into a heated barrel, mixed and pushed into a mould cavity where it cools and then hardens to the mould die cavity shape.
As far as traditional powder metallurgy is concerned, the similarity occurs in the way the procedure is implemented. This technique can compact a lubricated powder mix in a rigid die by uniaxial pressure, eject the compact from the die and sinter it.
Furthermore, MIM is also seen as a branch of a broader area, powder injection moulding (PIM); that involves the use of both metallic and non-metallic powders in the fabrication of small-to-medium-complex-shaped parts in large numbers.
Description of the process
Several developments of the MIM process have been observed during the past 30 years. They include MIM with space holders and forming processes to name a few of them.
However, we will keep in mind this explanation of the technology principles from Ralf Carlström, General Manager of Digital Metal:
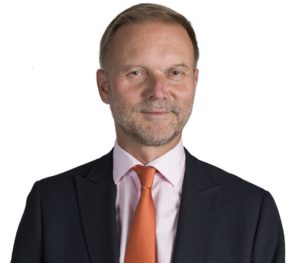
“The process steps involve combining metal powders with polymers such as wax and polypropylene binders to produce the “feedstock” mix that is injected as a liquid into a mould using plastic injection moulding machines. The moulded or “green part” is cooled and ejected from the mould. Next, a portion of the binder material is removed using solvent, thermal furnaces, catalytic process, or a combination of methods. The resulting, fragile and porous (40 volume per cent “air”) part, is in a condition called the “brown” stage. To improve handling often the debinding and sintering are combined into a single process. Sintering heats the powder to temperatures near the melting point in a protective atmosphere furnace to densify the particles using capillary forces in a process called sintering. MIM parts are often sintered at temperatures nearly high enough to induce partial melting in a process termed liquid phase sintering. For example, a stainless steel might be heated to 1350 to 1400 degrees Celsius). Diffusion rates are high leading to high shrinkage and densification. If performed in a vacuum, it is common to reach 96–99% solid density. The end-product metal has comparable mechanical and physical properties with annealed parts made using classic metalworking methods. Post sintering heat treatments for MIM are the same as with other fabrication routes, and with high density, the MIM component is compatible with the metal conditioning treatments such as plating, passivating, annealing, carburizing, nitriding, and precipitation hardening.”
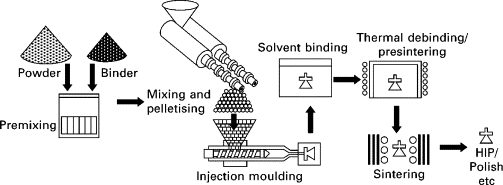
In addition to explaining the process, the description announces a few similarities with binder jetting technology, but that’s something we will discuss in the lines below. First, let’s see how and why this technology increasingly leads engineers to consider metal 3D printing as a much valuable tool in their toolkit.
From what setbacks did MIM suffer?
First of all, components from a wide range of sectors can be created using MIM. A few examples include parts in the medical field, the manufacturing industry, firearms and much more.
However, the truth is, for many years, at the manufacturing level, part repeatability, voids, fatigue issues and part performance have given operators so many headaches that they have started considering the technology as a production method of last resort, or considering its use when cutting costs was prioritized over part performance.
Reality shows that the technology has known its array of improvements but has not fundamentally changed its principles hence the increasing interest in another manufacturing technology that can bring “diversity” in the production facility. This technology is metal additive manufacturing.
Metal 3D Printing adds another option to the engineer’s toolkit
There are at least a dozen metal AM technologies on the market today. Each of these technologies presents its advantages and limitations when it comes to mechanical properties and costs, which does not simplify the decision-making process.
The two well-known types of metal AM technologies are melting processes and sintering processes. However, our focus today will be on sinter-based AM processes, especially binder jetting.
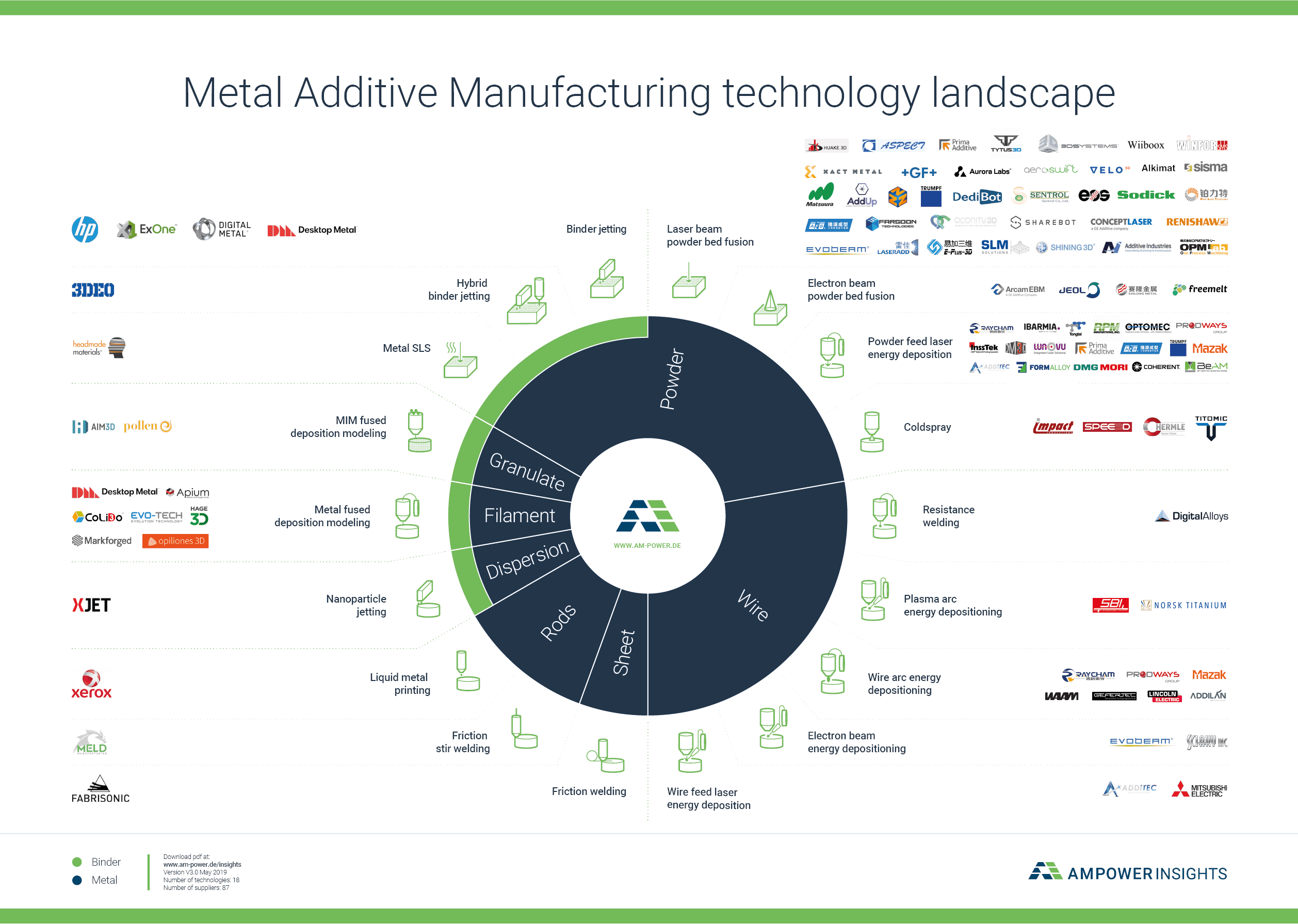
From MIM to binder jetting
Following Ralf Carlström’s explanations on MIM, we realized that MIM & binder jetting share some characteristics in their development.
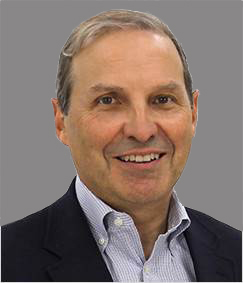
First, “binder jetting is a metal AM technology that leverages decades of powder metallurgy experience. Thin layers of powder are dispensed, selectively bound, cured, and then sintered to high density. By using the same powders and furnaces as MIM, binder jetting produces parts that meet MPIF Standard 35 for MIM”, said ExOne CEO John Hartner.
“The 3D Printed part is built up from many thin cross-sections of the 3D model. An inkjet print head moves across a bed of powder, selectively depositing a liquid binding material. A thin layer of powder is spread across the completed section and the process is repeated with each layer adhering to the last. When the model is complete, the unbound powder is automatically and/or manually removed in a process called “de-powdering” and maybe reused to some extent. The de-powdered part requires sintering to develop final properties”, adds Digital Metal’s Managing Director.
In other terms, in a binder jetting process, metal powder is moistened for a specific purpose by a liquid binding agent, binding it together. The binder is applied to the powder, before the addition of the next layer. Furthermore, the process requires the use of various types of metal powder to be processed, which typically would need to be processed by Metal Injection Moulding (MIM). In a nutshell, the technique involves one layer of powder and binder and is repeated until the part is entirely produced.
Desktop Metal on its side explains how they leveraged the potential of MIM to develop their binder jetting technology, and it all starts with the expertise of their founding members in these technologies.
Indeed, one of the co-founders of Desktop Metal, Professor Ely Sachs invented binder jet printing in the late 1980s when he was at Massachusetts Institute of Technology (MIT). Sachs’ technology allows engineers to create functional parts and end-use products rather than prototypes.
The VP of products also mentioned the expertise of Dr Animesh Bose, who has been involved in the area of powder metallurgy and particulate materials (PM) for more than thirty years. As per Larry Lyons’ words, Dr Bose’s “experience of working with similar materials in the context of the MIM process, to what we’re working with today has been crucial to developing new capabilities of 3D Printers specifications.”
ExOne, which was part of Extrude Hone Corporation, became a stand-alone company in 2005 and remained the only company to offer metal binder jetting services and systems until the early 2010s. At that time, the first MIT patents for the technology began to expire, allowing new companies into the market.
From Desktop Metal’s Larry Lyons statement, MIM has somehow inspired the development of the company’s metal additive manufacturing systems:
“Desktop Metal aims to deliver affordable 3D metal printing, in the same way, low cost plastic 3D Printers are accessible on the market today. So, when the company was founded, a wide range of researches on different technologies was carried out to figure out the best way to do this.
The initial technology that was leveraged during these researches for our systems – the Studio System especially– was primarily based on Metal Injection Moulding chemistry where we would take “MIM-like” materials and process them on a 3D printer.
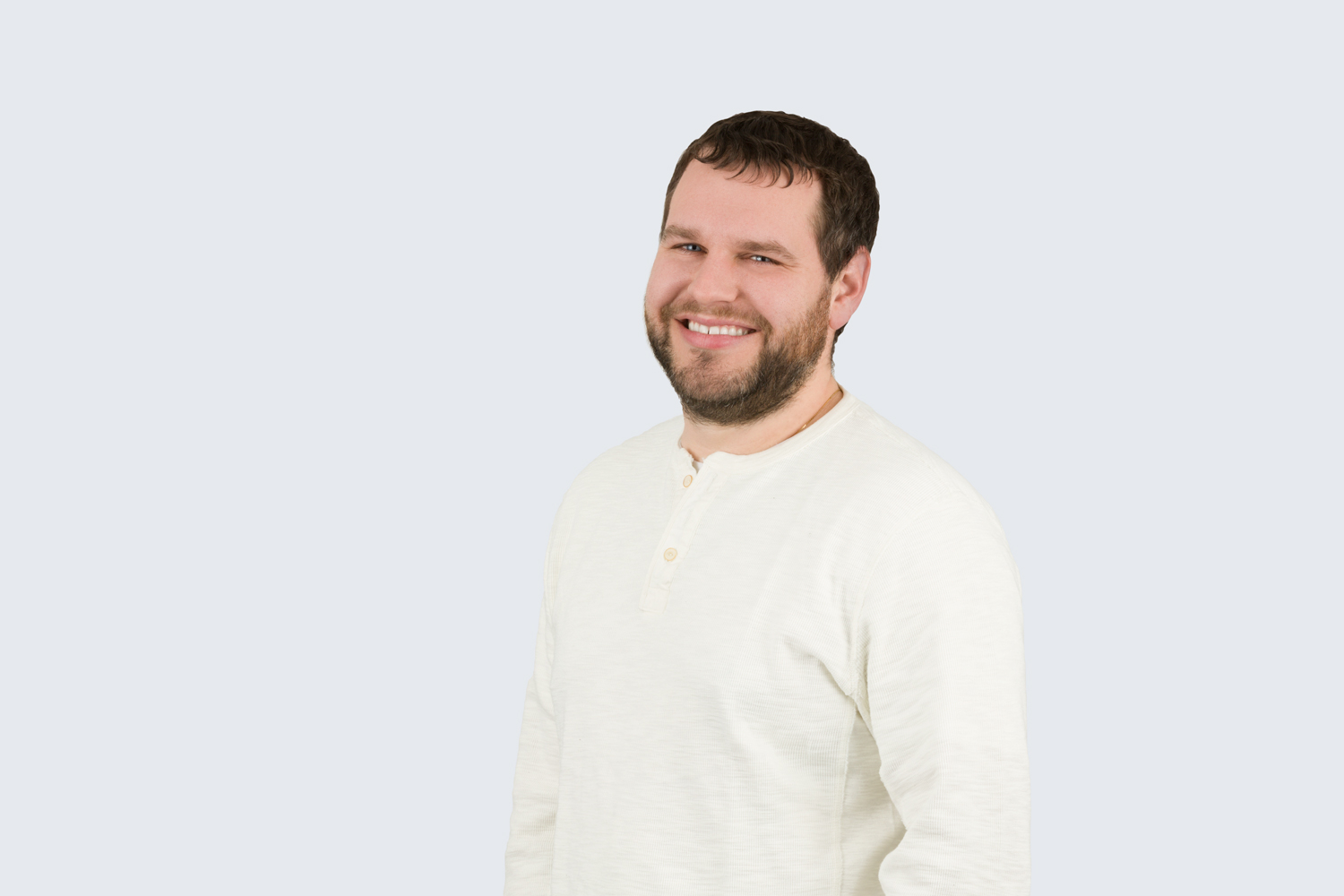
We then created our own user-friendly system to obtain a process that would produce solid metal parts. However, over time, a key focus was made on another range of the spectrum: large industrial systems such as our “Production System”, that are much faster at making parts.
Working on this system, we realized that we couldn’t make a 3D printer based on the science of MIM. Indeed, if the knowledge of materials resulting from the MIM process is useful, the MIM technique remains utterly different from binder jetting. Only the experience in the field of materials has been useful to leverage AM capabilities.”
Applications & Engineering: MIM vs Binder Jetting Technology
Applications
Let’s explore the applications that both technologies enable. We have mentioned above that MIM enables the production of firearms, parts in the medical field and the manufacturing industry.
The three experts agree with the fact that these applications are almost the same when using binder jetting:
“Applications for MIM and binder jetting are very similar. Since binder jetting uses the same powders as MIM and the same furnaces, binder jetting produces similar quality parts. Automotive and firearms are the biggest applications for metal binder jet parts currently”, said ExOne’s CEO.
“MIM components are used where there is a need for small intricate parts like in medical & dental, Industrial, automotive, aerospace and luxury applications. This is also relevant for metal binder jetting as mechanical properties are in general similar as for MIM”, completes Digital Metal’s Managing Director.
Apart from the manufacturing processes that involve a few differences, at first glance, two key factors that will be taken into account in the decision-making process are the design of the part and the quantity to produce.
Indeed, from an economic perspective – the holy grail in a manufacturing process -, if manufacturers do not intend to change the design of a given part for the next 5 to 10 years, and if they plan a production of thousands to millions of this part, then, an investment in MIM tooling makes sense.
However, from the end-user perspective, the Binder Jetting technique currently offers an even wider choice: the one to explore several forms of the same product within a limited period of time, the one to mass produce or to produce small volumes of a given part – even if this part is a prototype that is meant to be built with MIM.
With that being said, it is also interesting to mention that the AM supply chain is currently experiencing some change with the increasing adoption of binder jetting. Indeed, metal powder suppliers now supply mass markets such as automotive that increasingly leverage binder jetting technology.
Engineering
As far as engineering is concerned, key factors that have been compared include design & size of the manufactured part, surface quality, post-processing & cost.
Speaking of design, it is no secret that additive manufacturing technologies enable to obtain superior design possibilities compared to conventional manufacturing techniques. However, experts also say that residual stresses and the need for support structures sometimes add restrictions to this freedom of design.
“Binder jet parts range in size from smaller than a golf ball to larger than a basketball. Similar to MIM, small parts work very well with the binder jet process because shrinkage is minimized. The relatively low binder content in binder jet parts enables binder jetting to produce larger parts than [the ones that] can be made with MIM”, explained ExOne’s John Hartner.
Ralf Carlström, on the other hand, compares MIM & binder jetting in general: “binder jetting facilitates the forming stage for making large parts compared to MIM, but challenges during the sintering operation are similar for both processes for making large parts. [As far as surface finish is concerned, MIM brings a significant advantage due to the interaction with the mould during the forming step.]”
Larry Lyons lays emphasis on the technical aspect when giving his point of view on the points mentioned above:
“Binder jetting can do any parts made by MIM. MIM does tend to produce small parts whereas binder jetting provides a wider range of geometries and can produce parts of different sizes, both small and large.
As far as surface quality is concerned, you should know that injection moulding consists of a high-pressure injection of the raw material into a mould. Such high-pressure creates a smooth and repeatable surface that comes out of the mould. In binder jetting, there is no mould to provide that very smooth exterior surface so, we tend to have a rougher surface on binder jetting because you are at the mercy of the powder particles.
However, the postprocessing between the two manufacturing techniques is slightly different.
One of the final steps in a MIM process is debinding, which consists in removing a major portion of proprietary binder. Depending on the binder, some debinding processes can also be done in a furnace. After this step, the “brown” part is created.
In the binder jetting technology, instead of going into a sort of debinding in the next step out of the printer, you go into basically just depowering before going straight to the furnace. Thereafter comes the postprocessing step that depends on the part geometry and what the operator tries to achieve.”
In other terms, following the part infiltration, at the end of the binder jetting process, a finishing step such as polishing can be applied in order to obtain aesthetically pleasing surface finishes.
To sum up
This dossier aimed at comparing the potential & limitations of MIM & Binder jetting. The development of materials in the MIM process has somehow facilitated the use of these materials in a binder jetting process. In a nutshell, our findings can be summarized in the table below:
|
|
|
|
|
|
|
|
|
|
Today, the success of metal binder jetting lies in its compatibility with relatively MIM powders. Desktop Metal, Digital Metal and ExOne are not the only players in the metal binder jetting arena. Several companies are aware of the breakthrough potential of this technology and are now doing their best to seize the opportunities it presents.
Moving forward, these companies might evolve the technology even further. No matter what happens healthy competition can only help both technologies to carve out a valuable share in the manufacturing sector.