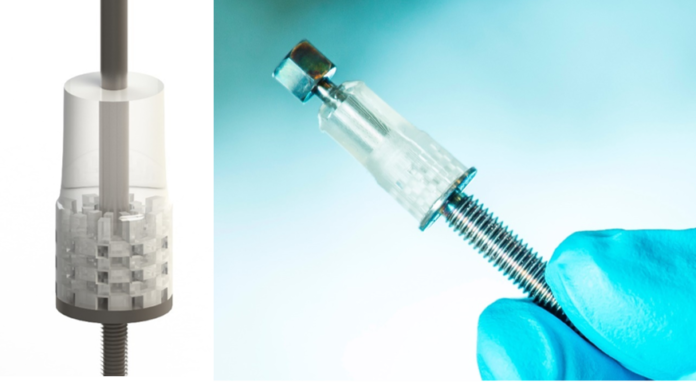
En ce qui concerne les applications, c’est généralement l’intérêt d’explorer un nouveau matériau qui n’est pas disponible en impression 3D qui motive le choix pour le FIM.
En sept ans d’activité, le déménagement d’AddiFab dans de nouveaux locaux plus spacieux a constitué une étape importante pour le fabricant danois d’imprimantes 3D à ce jour. En tant qu’entreprise, cette étape marque un pas en avant ; c’est le signe qu’elle se développe et va dans la bonne direction pour son objectif. D’autre part, pour l’industrie, l’important est de connaître la gamme d’applications que la technologie de l’entreprise permet et comment les implémenter.
Pour rappel, AddiFab développe à la fois « une technologie de fabrication additive et une technologie de moulage par injection » appelée Freeform Injection Molding (FIM). Ce procédé hybride vise à combler le fossé entre le prototypage et la production en offrant la liberté de la fabrication additive avec les volumes du moulage par injection au sein d’une même plateforme.
Avec sa récente levée de fonds, AddiFab a assuré que l’investissement aidera l’équipe à démontrer les capacités de sa technologie par des applications tangibles. Dans cette optique, la FIM semble être un candidat idéal pour diverses applications dont les dispositifs médicaux. Le CEO de la société, Lasse G. Staal, explique :
« Le moulage par injection de formes libres a déjà démontré son applicabilité dans des domaines aussi divers que le traitement anti-hypothermie, les vis osseuses implantables, l’équipement de protection COVID-19, le prélèvement de matières fécales et la distribution de gouttes ophtalmiques. La raison pour laquelle la FIM est en train de devenir un outil privilégié pour les développeurs de dispositifs médicaux est simple :
Les fabricants de dispositifs médicaux travaillent dans un domaine fortement réglementé et doivent démontrer que les matériaux qu’ils utilisent pour leurs dispositifs sont sûrs. Par conséquent, la plupart des fabricants de dispositifs s’en tiennent à un nombre limité de grades de polymères spécifiques, obtenus auprès de fournisseurs spécifiques ayant mis en place les systèmes d’assurance qualité nécessaires. Le plus souvent, ces qualités ne sont pas disponibles dans des versions pouvant être imprimées en 3D. Et même s’ils le sont, les matériaux imprimés en 3D ne présenteront pas les mêmes performances que les matériaux moulés par injection. Par conséquent, les fabricants de dispositifs médicaux qui souhaitent introduire sur le marché un dispositif comportant des composants moulés par injection devront invariablement commencer à mouler par injection avant de pouvoir vérifier et valider la sécurité et les performances de ce dispositif. Et le moulage par injection de formes libres est le moyen le plus rapide et le plus économique de mettre en place un outillage de moulage par injection, en particulier pour les matériaux difficiles à mouler et les géométries complexes. »
Cependant, l’expérience révèle que les fabricants de dispositifs médicaux partagent des défis similaires à ceux des autres industries manufacturières. C’est pourquoi, bien que le principal domaine d’intérêt en termes d’applications reste l’industrie médicale, il convient de noter qu’AddiFab propose la même offre à d’autres industries : « Un outillage de moulage par injection imprimé en 3D, compatible avec la quasi-totalité des matériaux thermoplastiques, et offrant une liberté de conception à la hauteur de l’impression 3D. »
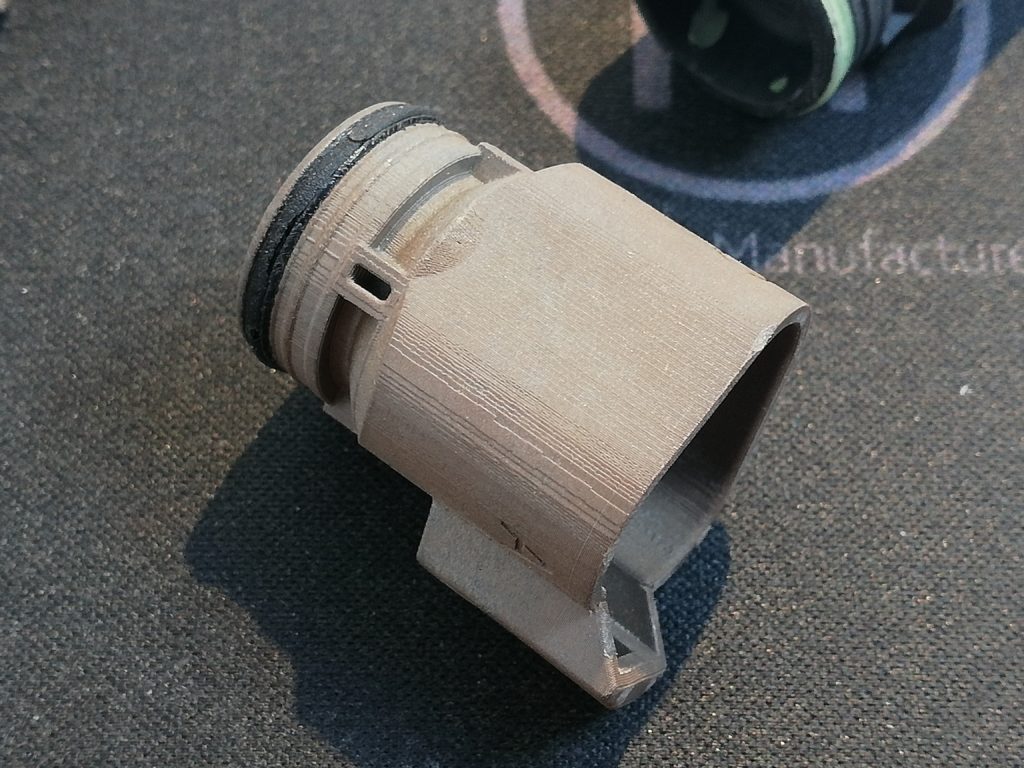
Alors, comment définir la FIM pour les applications de production ?
En matière de FA, il n’existe pas de directives standard permettant de déterminer si la technologie est ou non le processus idéal à exploiter pour la production. Dans un dossier récent, nous avons identifié trois cadres différents qui sont généralement explorés avant de s’engager dans la voie de la FA pour la production en série. Toutefois, dans le cas de la technologie FIM, que le client soit familier avec la FA ou le moulage par injection, la transition vers la FIM se fait assez facilement en raison de la capacité du FIM à intégrer les caractéristiques des deux processus.
En ce qui concerne les applications, c’est généralement l’intérêt d’explorer un nouveau matériau qui n’est pas disponible en impression 3D qui motive le choix du FIM.
« La plupart de nos clients sont des utilisateurs assez avertis de l’impression 3D conventionnelle, et ils nous contactent généralement lorsqu’ils veulent utiliser un matériau qui n’est pas disponible pour l’impression 3D. Mais nous voyons un nombre croissant de mouleurs par injection nous contacter parce qu’ils veulent accélérer la transition de l’impression 3D au moulage par injection », note Staal.
L’examen de la candidature du FIM pour une application suit donc un processus en trois étapes qui consiste à :
- Déterminer dans quelle mesure la FIM répondra à la demande d’un client
- Mettre en œuvre des analyses de flux de moule
- Identifier le meilleur modèle de mise en œuvre du moulage par injection de formes libres pour le projet spécifique du client.
Selon Lasse, pendant la phase d’essai – la première étape -, leur équipe évalue les principales caractéristiques du produit et les principaux matériaux de référence qui pourraient être utilisés pour une application donnée.
« Par exemple, la première chose que nous avons faite lorsque nous avons lancé les évaluations du FIM pour la fabrication de capsules à rabat, a été de faire un zoom sur la partie charnière elle-même. Nous avons enlevé les 90% du bouchon qui n’avaient rien à voir avec la fonction de charnière, et nous avons fait un certain nombre d’itérations avec des charnières moulées autonomes dans le matériau de référence du client jusqu’à ce que nous soyons satisfaits des performances de la charnière. Cette approche « zoom-in » est extrêmement rapide et rentable – et c’est l’une des premières choses qui différencient la FIM de l’outillage conventionnel de moulage par injection « tout est parfait du premier coup’’ », souligne l’expert.
Une fois qu’ils ont déterminé comment réaliser chaque nouvelle caractéristique d’une application donnée, le processus de fabrication des outils imprimés commence. À ce stade, les analyses de flux de moule permettent de s’assurer qu’ils ne gaspillent pas de plans sur des conceptions défectueuses. Elles permettent également de décider quelle est l’option idéale lorsqu’il s’agit de concevoir des outils fermés en une seule pièce ou des outils ouverts en plusieurs pièces.
Staal affirme que les outils fermés en une seule partie sont souvent les plus rentables et les plus faciles à concevoir, mais un composant peut présenter des caractéristiques (le plus souvent des surplombs) qui les obligent à diviser un outil en plusieurs composants.
« Nous sommes aussi fréquemment confrontés à des clients qui souhaitent obtenir le plus grand nombre de plans possible à partir d’un seul outil. Bien que la partie « Freeform » du moulage par injection exige que les outils soient dissous, les inserts que nous imprimons sont plutôt robustes. Et si nous devons prendre en charge des applications à plus grand volume, nous travaillons généralement avec le client pour développer des concepts d’outillage hybrides – où des inserts sacrificiels imprimés en 3D sont combinés avec des cavités d’outils métalliques conventionnels », ajoute-t-il.
Lorsqu’il ne fait aucun doute que la FIM peut effectivement être utilisée pour une application donnée, l’étape suivante consiste à mettre en œuvre le processus. À ce niveau, il convient de noter que le client ne dispose pas nécessairement toujours d’un système FIM en interne. En fonction des volumes qu’il doit produire, il peut soit travailler avec les partenaires d’AddiFab – Mitsubishi Chemical Advanced Materials – soit explorer différentes options d’acquisition avec l’équipe d’AddiFab.
Avec Mitsubishi Chemical Advanced Materials (MCAM) comme partenaire, AddiFab ne bénéficie pas seulement d’un éventail de matériaux compatibles avec sa solution FIM. Elle a également bénéficié d’un partenaire qui peut soutenir son offre de moulage par injection de formes libres en tant que service. Avec des systèmes AddiFab dans des installations aux États-Unis (Arizona), dans l’Union européenne (Belgique) et dans la région APAC (Japon), MCAM fournit depuis la mi-2020 des matériaux KyronMAX® de haute performance, remplaçant le métal, à ses clients dans des secteurs verticaux exigeants.
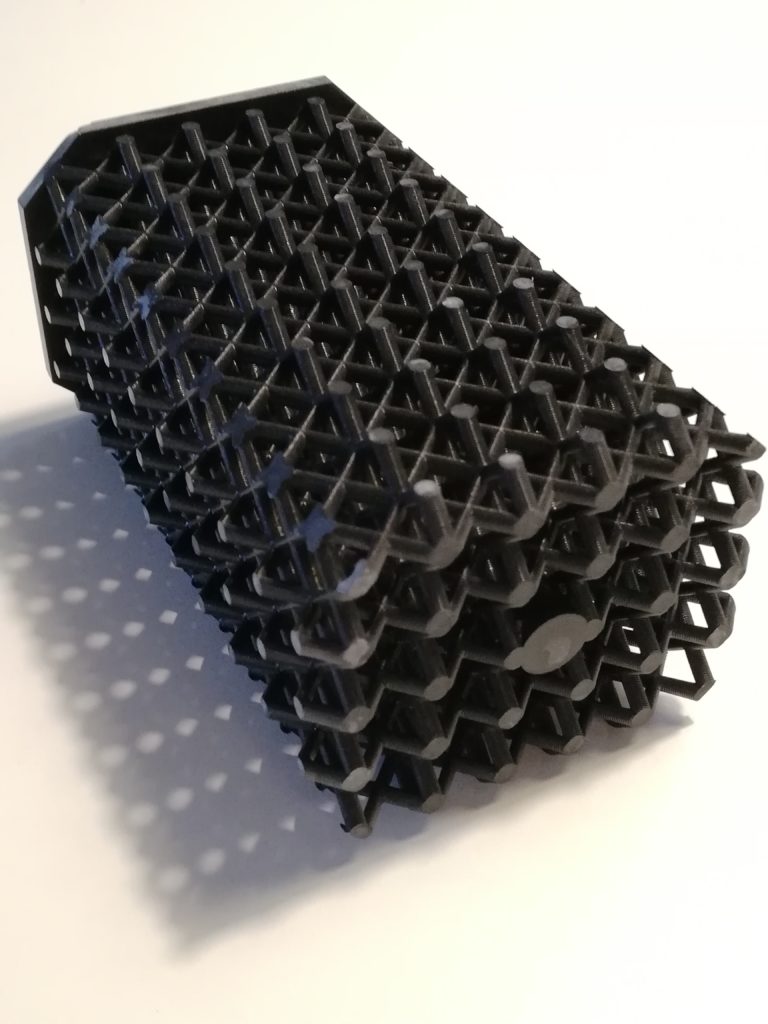
Selon l’entreprise, la combinaison d’inserts imprimés par FIM et d’éléments métalliques très résistants permet d’obtenir le meilleur de l’impression 3D et du moulage par injection.
À ce jour, une chose est sûre, ils « bénéficient de la possibilité d’agréger beaucoup de demandes sur très peu de variantes de résine ». Le moulage par injection de formes libres – comme d’autres technologies d’outillage imprimé – gagne en exploitant les vastes catalogues de matériaux hérités de l’industrie du moulage par injection, au lieu de devoir développer de nouveaux matériaux qui imitent les capacités de ceux déjà inventés ».
Aperçu du processus FIM : développements actuels et domaines à améliorer
L’année dernière, au plus fort de la pandémie de Covid-19, AddiFab a dévoilé un module permettant aux micro-injecteurs d’augmenter la résolution de leurs imprimantes de 50 µm à 10 µm. Ce développement est le résultat de l’expérience holistique de l’équipe avec son système Micro qui a d’abord été utilisé sur une unité autonome. Suite à plusieurs demandes de clients, ils ont exploré comment ils pouvaient améliorer la compatibilité du système Micro avec l’installation standard de 50 µm. Aujourd’hui, le module complémentaire interchangeable fonctionne avec une résine spécialisée qui peut être installée et utilisée sur une imprimante AddiFab existante.
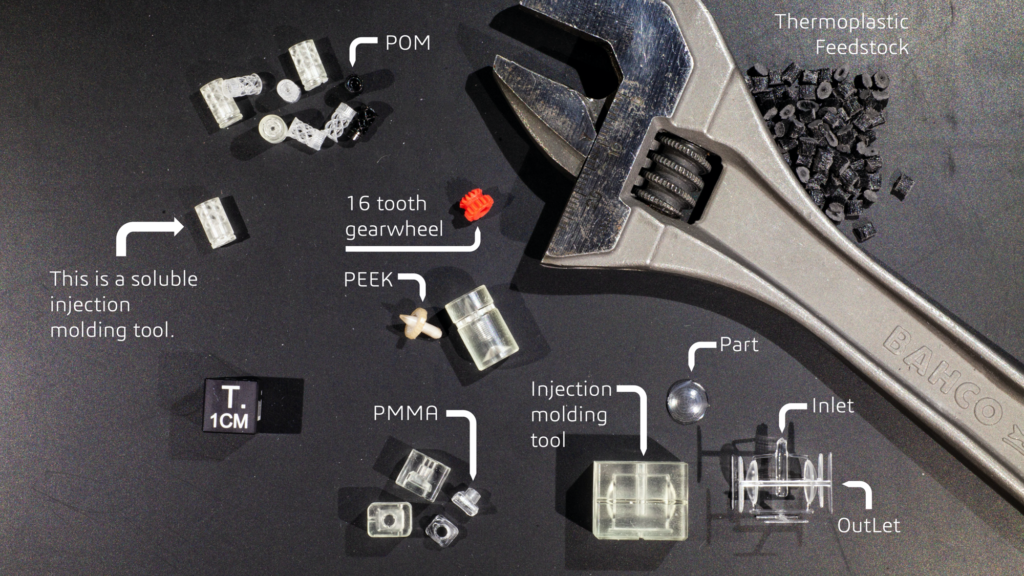
« L’AddLine Micro a été une véritable révélation pour nous. Lorsque nous avons décidé d’installer une imprimante pour effectuer un travail d’essai avec notre configuration 10 µm, nous pensions que l’imprimante serait remise en service à 50 µm dès que le travail serait terminé. Mais nous avons décidé de contacter de manière informelle quelques clients qui connaissaient déjà la FIM – et la réponse a été massive. Rétrospectivement, je pense que nous aurions dû nous rendre compte que le moulage par micro-injection est l’un des secteurs les moins bien desservis en matière de plateformes de prototypage. Par conséquent, nous avons déjà eu l’occasion de démontrer l’applicabilité de la Micro avec le moulage par injection de métal, le moulage par injection de silicone, les thermoplastiques haute performance, les guides de lumière et les impressions directes. Et nous voyons plusieurs de ces dialogues initiaux se transformer en demandes répétées presque dès que nous avons terminé les premières études. Je pense que le Micro set-up répond à un besoin non satisfait assez important sur le marché du micro-moulage », souligne Staal.
Qu’il s’agisse d’une seule configuration – le standard 50 µm – ou d’applications qui vont au-delà de la zone de frappe de leur premier système AddLine, l’équipe d’AddiFab reconnaît que ces demandes ont conduit au développement de meilleurs modules complémentaires pour leur technologie. Sans oublier que la demande de pièces plus grandes a conduit à des solutions hybrides qui combinent des inserts imprimés et des cavités métalliques.
Aujourd’hui, alors qu’ils écrivent le prochain chapitre de leur aventure dans leurs nouveaux locaux, ils souhaitent également améliorer l’expérience utilisateur et la facilité d’utilisation de leur plateforme.
« Réussir avec Freeform Injection Molding signifie combiner les compétences de l’impression 3D, de la conception d’outils et du moulage par injection, et nous élargissons avec diligence notre gamme d’outils matériels et logiciels pour faciliter la vie de nos clients », conclut Staal.
N’oubliez pas que vous pouvez poster gratuitement les offres d’emploi de l’industrie de la FA sur 3D ADEPT Media ou rechercher un emploi via notre tableau d’offres d’emploi. N’hésitez pas à nous suivre sur nos réseaux sociaux et à vous inscrire à notre newsletter hebdomadaire : Facebook, Twitter, LinkedIn & Instagram ! Si vous avez une innovation à partager pour le prochain numéro de notre magazine numérique ou si vous avez un article à faire connaître, n’hésitez pas à nous envoyer un email à contact@3dadept.com.