Carbon® & Specialized® partner to produce a digitally printed bike saddle. Named the “S-Works”, the bike saddle leveraged Mirror technology and is designed to improve rider comport and performance.
This partnership between Carbon® & Specialized® is not that surprising given Carbon’s involvement in projects related to sport. Riddell’s helmets, adidas’ shoes are a few examples. The truth about cycling is that the whole experience relies on the saddle. If this specific part of the bike is not comfortable, it will compromise the whole experience. According to enthusiasts, the comfort on the bike saddle will tell you whether you are having a bad ride or a great ride.
What’s then the challenge at the production level?
The challenge is to maximize comfort and stability. For manufacturers, this means leverage appropriate materials and complex lattice geometries during the production. Carbon therefore produced a saddle that absorbs impact while reducing the chance of injury for the rider.
Indeed, bike saddle might easily lead to injuries and health issues, such as neuralgia (nerve pain), numbness, and urinary problems. At the design level, engineers faced hurdles to mitigate the pressure and discomfort cyclists experienced while riding. Carbon Digital Light Synthesis™ (DLS™) technology addressed this issue by developing a lattice design that enables the saddle to rebound quickly, giving riders the experience of having a ‘suspension’ for their sit bones. The saddle not only disperses pressure, but also significantly improves breathability. As a result, the rider definitely feels less pain and faces fewer injuries, leading to better health and performance.
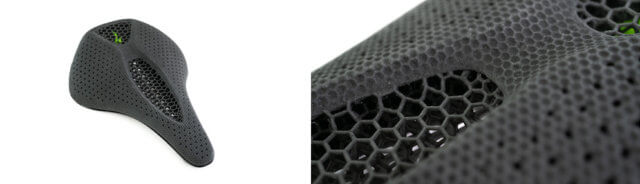
“Carbon and Specialized share a mission to challenge the acceptable, create the extraordinary, and ultimately make products that enable people to push the limits of what’s possible,” said Dr. Joseph DeSimone, CEO and Co-Founder of Carbon. “Our partnership with Specialized represents not only a breakthrough in bike saddle technology, but also our companies’ shared commitment to drive meaningful change by making products that improve human health and well-being.”
“Specialized has a long history of improving the rider experience. We created our first Body Geometry saddle over 20 years ago to address serious issues impacting cyclists. Together with Carbon, we are challenging the norms of the cycling world, from design to production time, to create technology that will allow riders to improve performance, increase comfort, and reduce the chance of injury,” said Garrett Getter, Specialized Product Manager of Saddles. “With Mirror technology, we’ve only scratched the surface of what’s possible.”
The overall development process takes 10 months instead of the usual 18-24 months. Over 70 designs have been created during this timeframe and it only requires 2 months to achieve the overall design process. The new S-Works Power Saddle with Mirror technology will be available in 2020. Riders, stay tuned and let us know your feedback!
https://pagead2.googlesyndication.com/pagead/js/adsbygoogle.js
(adsbygoogle = window.adsbygoogle || []).push({});
You can now post free of charge job opportunities in the AM Industry on 3D ADEPT Media.For further information about 3D Printing, follow us on our social networks and subscribe to our newsletter : Facebook, Twitter, LinkedIn & Instagram !Would you like to be featured in the next issue of our digital magazine? Send us an email at contact@3dadept.com