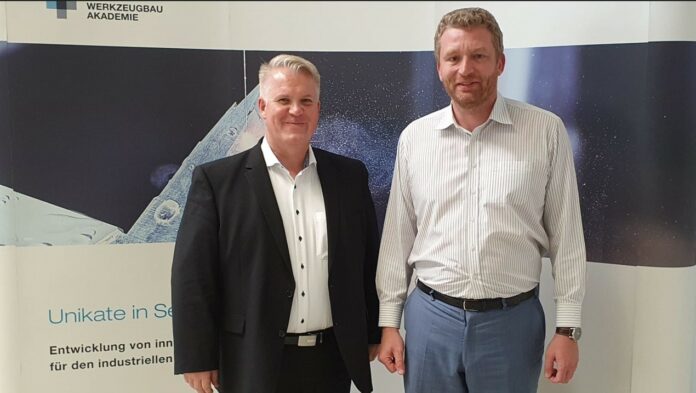
Germany-based WBA Aachener Werkzeugbau Akademie GmbH is a technical reference center that provides consulting, training, and research activities to the tooling industry. With the goal of enabling manufacturing in the tooling industry to take advantage of manufacturing processes that may improve their production, the organization has decided to partner with French metal AM company AddUp to strengthen its offering with a complete metal AM support for their project.
This means that, as from now on, any strategic and organizational assistance regarding toolmaking would take into account the capabilities of metal 3D printing and if required, might leverage the New Generation FormUp® 350 machine installed in the center.
The Laser-Powder Bed Fusion industrial 3D printer encompasses AddUp’s know-how in terms of productivity, part quality, and operator safety. It also comes with additional features that result from the manufacturer’s partnerships with other technology partners such as Interspectral; features like a 3D visualization software that makes it possible for end users to create multi-channel digital twins from design, simulation, monitoring, and post-build part analysis data collected during the AM process.
Together, the teams at AddUp and WBA will enable tool makers to study all aspects of their projects, from the design applied to the L-PBF, to the profitability analysis and the study of series production.
One of the most significant use cases for L-PBF technology in the tooling field is plastic injection molds. Traditionally, injection molding manufacturers must deal with certain constraints inherent to the manufacture of their molds. The mold’s performance is directly related to its ability to cool the injected parts. The L-PBF technology is adapted to create complex cooling channels, positioned as close as possible to the mold walls. Finally, by adapting the shape of the channels to cool the surface of the part more homogeneously, manufacturers can see improved quality and experience higher productivity with a reduction of cooling and cycle times, a press release reads.
Remember, you can post job opportunities in the AM Industry on 3D ADEPT Media free of charge or look for a job via our job board. Make sure to follow us on our social networks and subscribe to our weekly newsletter : Facebook, Twitter, LinkedIn & Instagram ! If you want to be featured in the next issue of our digital magazine or if you hear a story that needs to be heard, make sure you send it to contact@3dadept.com