En général, beaucoup semblent être d’accord avec la flexibilité de conception et l’efficacité des matériaux que la FA procure, mais malgré ces avantages indéniables, une chose que les fabricants de technologies FA ont du mal à améliorer de manière significative dans leur processus est la vitesse. Nous nous sommes rendu compte qu’il existe une technique de fabrication qui est particulièrement reconnue pour sa capacité à répondre aux exigences de vitesse de production de certaines industries : Le dépôt de particules supersoniques (SPD = Supersonic Particle Deposition, également appelé pulvérisation à froid ou Cold Spray en anglais).
Cette rubrique exclusive a pour but de présenter les méthodes, les défis et les applications de ce procédé et les raisons pour lesquelles il est particulièrement bien placé pour répondre aux exigences de certaines industries. Pour discuter de ces sujets, nous avons invité deux entreprises qui ont fait de cette technique leur activité principale : Titomic et SPEE3D. Jeff Lang, fondateur de Titomic Limited, directeur exécutif et directeur technique, ainsi que les co-fondateurs de SPEE3D, Byron Kennedy et Steven Camilleri, sont les principaux contributeurs de cette exclusivité.
La fabrication à double vitesse
D’un point de vue économique, la vitesse idéale de fabrication nécessite un équilibre parfait entre les processus physiques de production, le système plus large qui permet à ces processus de fonctionner, et la coordination d’une chaîne d’approvisionnement dans la poursuite de la satisfaction des besoins des clients.
Cependant, dans le domaine de la fabrication – et en particulier dans les processus de fabrication additive – les choses sont légèrement différentes. La vitesse commence à poser des problèmes lorsque les fabricants doivent faire face à des délais courts et lorsque l’objectif est la production à grande échelle. Dans cette perspective de fabrication, les opérateurs qui travaillent sur les machines de FA métal auront tendance à rechercher un procédé qui ouvre plus de possibilités en termes de matériaux et qui supporterait des températures de fusion très élevées pour aller très vite.
Seul petit bémol, selon les mots de Jeff Lang, « le principal facteur que l’industrie de l’impression 3D métal a eu du mal à réaliser, est sa viabilité face à la vitesse de la fabrication traditionnelle de pièces métalliques à l’échelle industrielle, en particulier dans les industries aérospatiale et de la défense ».
En effet, « dans la FA traditionnelle, la poudre de métal est fondue par un laser – ce processus prend une poudre solide, la fait fondre en un liquide, puis la transforme en un solide. Ce processus prend du temps, basé sur la physique, et est facile à calculer. Afin d’accélérer ce processus pour plus d’efficacité, il fallait un procédé qui ne fasse pas fondre la poudre », expliquent Byron Kennedy et Steven Camilleri.
Ces défis conduisent donc à l’intérêt croissant pour la technologie de fabrication additive (FA) par dépôt de particules supersoniques (SPD) (également connue sous le nom de Cold-Spray).
Alors, qu’est-ce que le Cold Spray ?
Comme le note Jeff Lang de Titomic, le dépôt de particules supersoniques (Cold-Spray) est utilisé commercialement depuis plus de 30 ans, mais son application dans la fabrication additive est assez récente.
La pulvérisation à froid est définie comme un processus de consolidation des matériaux par lequel des particules de taille micronique d’un métal, d’une céramique et/ou d’un polymère sont accélérées par un pistolet de pulvérisation équipé d’une buse de fusée De Laval à l’aide d’un gaz chauffé à haute pression (hélium ou azote). Dans ce processus, les particules sortent à des vitesses supersoniques et se consolident en heurtant une surface appropriée pour former un revêtement ou une pièce en forme de filet à l’aide d’un impact balistique.
La principale innovation de ce procédé serait l’utilisation d’une « buse de Laval », une buse convergente-divergente qui permet à la poudre métallique d’atteindre des vitesses supersoniques. Selon les experts, le procédé a gagné en popularité dans la fabrication additive grâce à sa capacité à appliquer des revêtements à composants multiples.
En outre, contrairement aux autres technologies de dépôt de poudre, quatre avantages principaux caractérisent la SPD : pas de zone affectée thermiquement, pas d’oxydes d’interface, génération de contraintes de compression en surface ainsi qu’aucune limitation d’épaisseur.
Cela signifie que la liaison entre les matériaux et les particules ne nécessite généralement pas de source thermique. Il n’y a pas de cycle de fusion et de refroidissement car le processus est à l’état solide.
Considérations en termes de matériaux et de post-traitement
Comme il n’y a pas de chaleur, les opérateurs peuvent facilement explorer l’utilisation de matériaux réactifs tels que le titane, l’aluminium et le magnésium.
Selon les fondateurs de SPEE3D, « chaque poudre a ce qu’on appelle une vitesse de dépôt. En accélérant une puissance si sa vitesse est trop lente, la poudre rebondit, trop vite, et la poudre va éroder le substrat. Entre les deux, il y a ce que nous appelons la « fenêtre de dépôt rapide. Par exemple, le cuivre peut être déposé à 450 mètres par seconde, l’aluminium à 600 mètres par seconde, et l’acier inoxydable à 700 mètres par seconde. Ce sont les vitesses idéales. »
En ce qui concerne SPEE3D, les fondateurs expliquent qu’ils accélèrent « la puissance jusqu’à une valeur comprise entre Mach 1,5 et Mach 2 selon le matériau utilisé (la vitesse supersonique est supérieure à Mach 1 ou à 343 mètres par seconde) ».
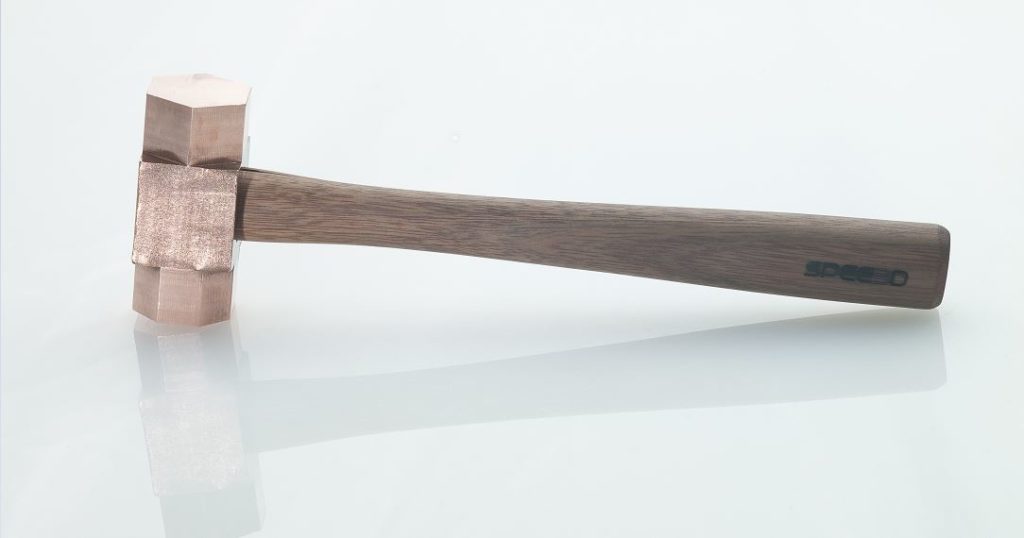
Cependant, il convient de prêter attention à la ductilité du matériau pulvérisé. En effet, les poudres moins ductiles sont moins sujettes à la déformation. Dans ce cas, la pièce imprimée en 3D révèle une fragilité qu’on ne voit pas dans les pièces traitées thermiquement. Il est intéressant de noter qu’un post-traitement thermique tel que le pressage isostatique à chaud (HIP) peut supprimer ces effets. En revanche, les matériaux plus ductiles (par exemple, l’aluminium, le cuivre) ne présentent pas cette caractéristique et nécessitent donc moins de post-traitement.
Des routes différentes mènent à la « vitesse ».
Au milieu de cet éventail de caractéristiques, la caractéristique la plus impressionnante de la pulvérisation à froid reste la vitesse. Il va sans dire que pour développer leur technologie, chaque fabricant a apporté quelque chose d’unique à son procédé.
Appelé Titomic Kinetic Fusion (TKFTM), le procédé breveté de Titomic permet la fabrication additive à l’échelle industrielle de pièces en titane.
Lang se rappelle qu’en 2008, il a été contacté par le CSIRO, l’organisation scientifique nationale australienne, pour étudier la création d’une chaîne de valeur holistique autour du titane, dont l’Australie possède les plus grandes réserves minérales au monde.
« Pour débloquer cette chaîne de valeur, il a fallu mener une enquête approfondie sur les technologies de production pour la fabrication du titane dans le but de trouver le processus le plus viable avec la proposition de valeur la plus unique. Après avoir étudié diverses technologies de fabrication de pièces en titane, il est apparu que la vitesse et la taille des pièces étaient limitées par les procédés de fabrication par fusion. Comme je cherchais à utiliser de grandes quantités de poudre de titane, il me fallait trouver une technologie de FA adaptée qui soit commercialement viable par rapport aux méthodes traditionnelles de fabrication du titane », explique Lang.
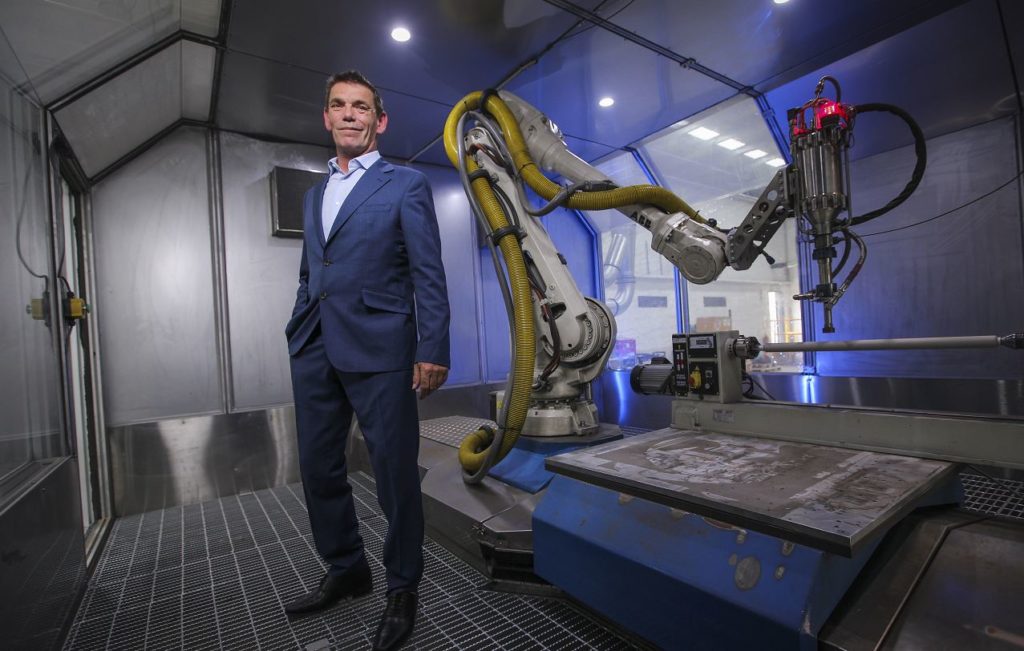
Lang a réalisé qu’en raison de ses taux de dépôt élevés, le procédé de revêtement métallique haute performance était un grand pari pour produire des pièces de FA plus rapidement et « sans les contraintes de taille des imprimantes 3D à base de fonte ».
Aujourd’hui, le fabricant d’imprimantes 3D métal commercialise le système TKF1000 qui permet des vitesses de fabrication de 6 à 10 kg par heure selon le type de matériau métallique utilisé et sa densité.
« Nos systèmes TKF personnalisés peuvent être configurés avec plusieurs têtes pour atteindre des vitesses de fabrication de 75 kg par heure. Comme pour tous les fournisseurs d’équipements de fabrication additive, certaines affirmations audacieuses concernant les vitesses de fabrication sont irréalistes, même si la machine peut être évaluée à ce maximum. Sur une seule tête du système TKF, nous pouvons fabriquer 30 à 45 kg par heure, mais il y aurait une porosité considérable à ces vitesses de fabrication, ce qui affecterait les propriétés mécaniques », ajoute l’expert.
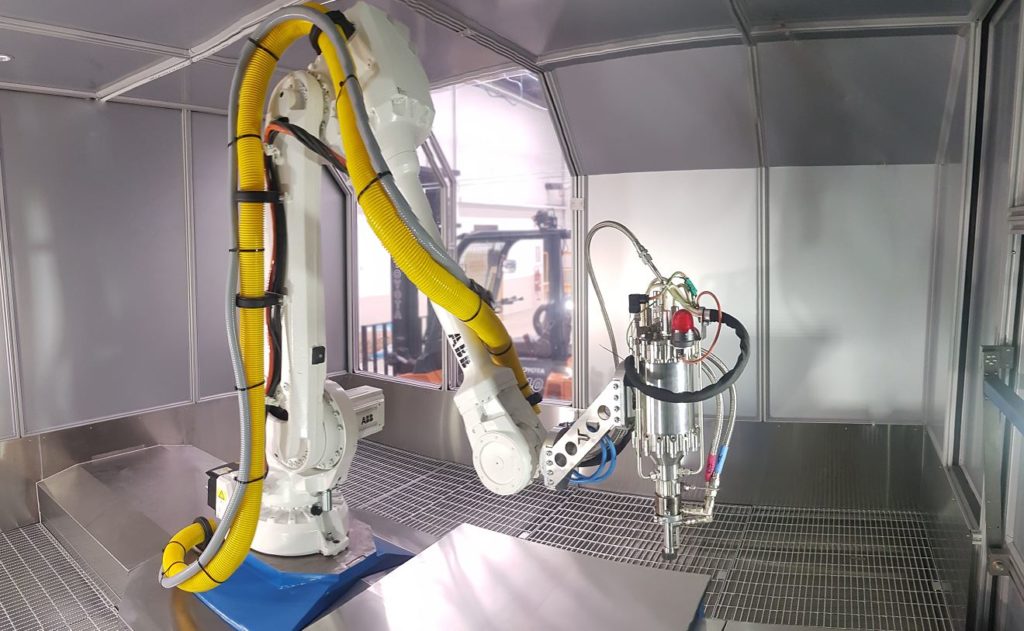
Dans le cas de SPEE3D, c’est une voie différente qui a conduit au développement de leur technologie de FA de pulvérisation à froid. Avec une décennie d’expérience dans le secteur manufacturier, SPEE3D n’est pas la première aventure entrepreneuriale de Kennedy et Camilleri. Dans la vie qu’ils menaient avant SPEE3D, ils ont réalisé le potentiel de l’impression 3D métal, mais ont également déploré ses limites.
« Le défi, cependant, était que la FA métal traditionnelle était trop chère et trop lente. Donc, en finissant avec l’entreprise de fabrication, nous avons décidé d’entrer dans l’espace de fabrication additive. Nous avons commencé à chercher une technologie de FA adaptée à la fabrication – une technologie rapide et peu coûteuse. C’est alors que nous avons découvert le Cold Spray, qui à l’époque était principalement utilisé dans des applications de réparation militaire, et de manière « manuelle ». Nous avons découvert que c’était quelque chose qui pouvait être amélioré. Donc, avec une formation en systèmes de contrôle et en robotique, nous avons pris un procédé manuel de projection à froid et l’avons transformé en une machine de projection métallique », soulignent les fondateurs.
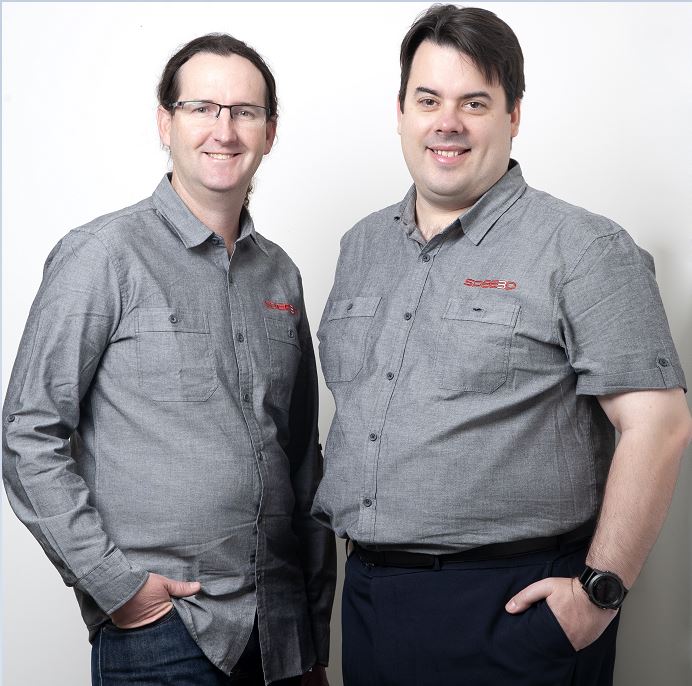
Les deux fondateurs travaillent sur leurs objectifs à long terme: « la limitation des imprimantes SPEE3D n’est pas la vitesse de dépôt, mais la robotique qui suit le Spray (projection à froid). Théoriquement, le processus pourrait être beaucoup plus rapide, ce qui rendrait le processus de FA encore plus facile, et c’est ce sur quoi SPEE3D travaille en permanence comme objectif à long terme ».
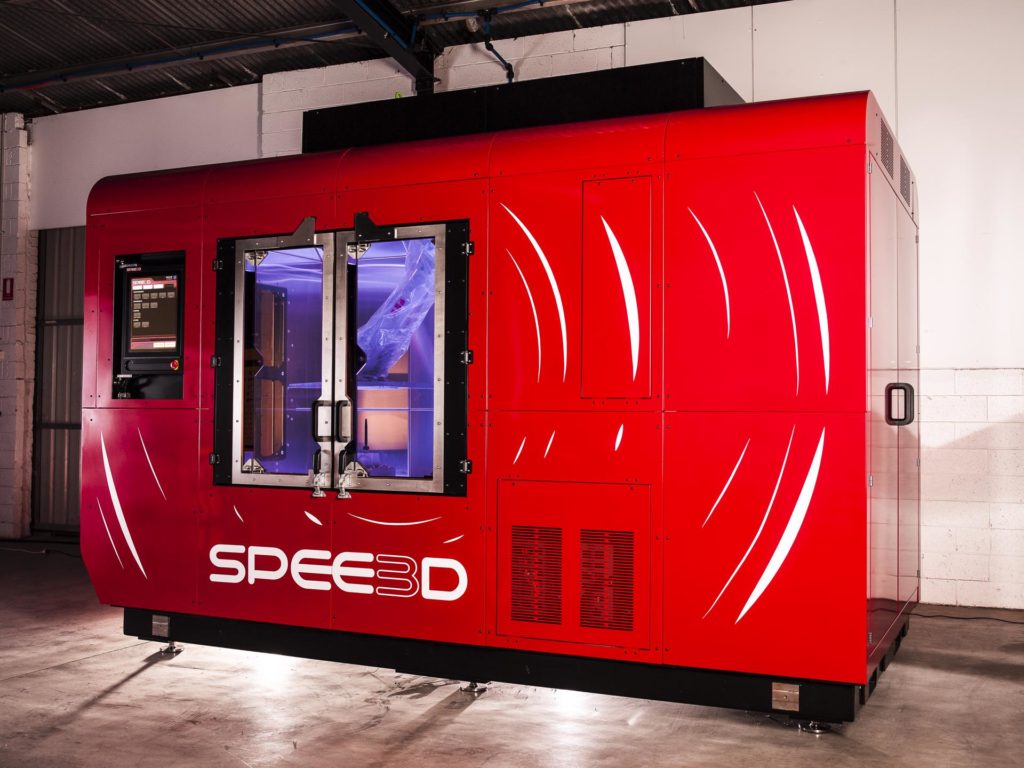
Un examen approfondi de ces deux procédés d’impression 3D métal montre que les deux technologies permettent d’optimiser facilement la vitesse de construction pour obtenir les géométries et les propriétés mécaniques souhaitées – sans compter que le post-traitement (traitement thermique et/ou post-usinage) dépend beaucoup du choix initial du matériau.
Applications et défis
Comme elle a été reconnue pour la première fois comme une technologie de réparation de pièces métalliques, les premières applications du SPD ont été vues dans la réparation des boîtes de vitesses d’hélicoptères en magnésium. Les fabricants soulignent les capacités technologiques de fabrication de pièces telles que les outils, les supports, les pompes, ainsi que de composants spécialisés. Selon les chercheurs, cet intérêt pour les applications militaires s’explique par la nécessité d’effectuer des réparations fréquentes sur le champ de bataille.
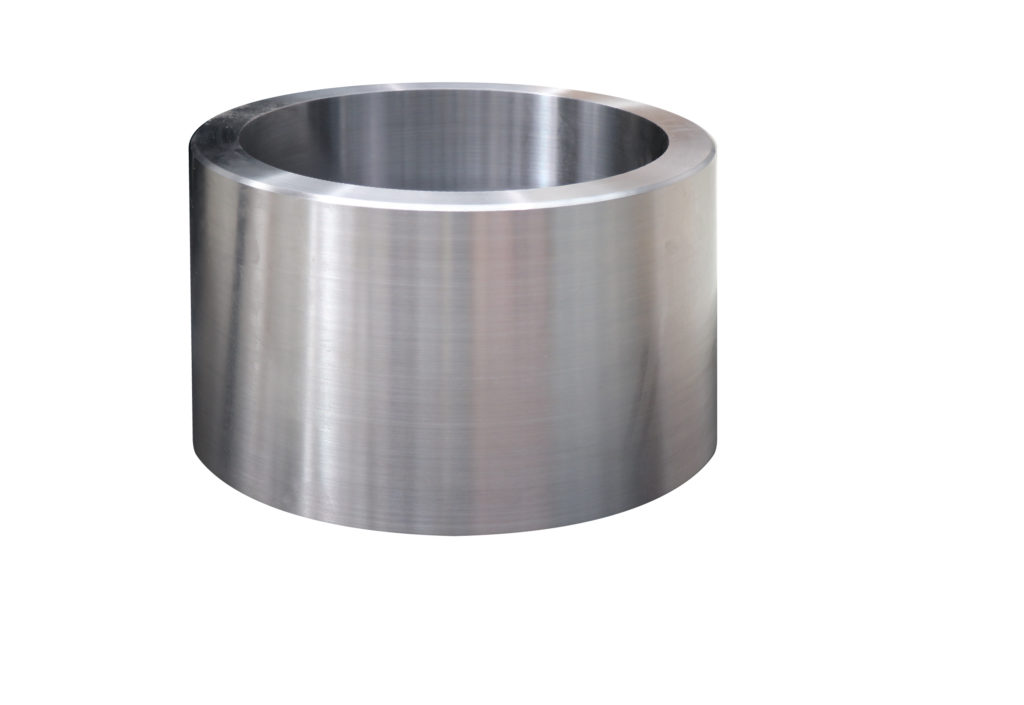
En parlant des boîtes de vitesses d’hélicoptères, Danielle Cote, professeur adjoint en science et ingénierie des matériaux et directrice du Centre de données sur le traitement des matériaux du WPI, note « Si vous devez remplacer une pièce de ce type, cela peut prendre des mois, voire des années, et le coût est important – en supposant que la pièce soit disponible ou même encore en cours de fabrication. Pour réparer une boîte de vitesses par projection à froid, il faut des alliages à haute résistance, ténacité et ductilité. Notre méthodologie nous permettra de mettre au point des poudres qui pourront être utilisées pour réparer efficacement, voire fabriquer des pièces de ce type et remettre rapidement les hélicoptères en vol. L’armée est particulièrement intéressée par les systèmes portables de projection à froid, mais la technologie peut également être utilisée à plus grande échelle – dans l’industrie, par exemple – et il sera passionnant de voir comment les robots peuvent contribuer à étendre l’utilisation de ce procédé et d’autres procédés de fabrication additive ».
Outre les applications militaires et de défense, nous avons également vu des applications de pulvérisation à froid de FA dans l’industrie spatiale et certains produits de consommation de luxe.
La FA Cold Spray semble cependant très prometteuse pour les entreprises de taille moyenne. Nous ne pouvons pas nier que la technologie est prête à répondre aux exigences de certaines industries, mais sa capacité à répondre aux besoins de production à grande échelle reste à démontrer.
En outre, les chercheurs encouragent vivement les fabricants à examiner de près la sélection des matériaux ainsi que la microstructure et les propriétés mécaniques des dépôts qui peuvent dépendre de différents paramètres de processus. Dans cet ordre d’idées, le contrôle géométrique peut souvent être une question assez dérangeante. « Le faible contrôle géométrique est attribué à une série de problèmes clés qui limitent l’application des technologies de fabrication additive, tels que la nécessité d’un post-usinage, la difficulté de fabriquer des formes complexes, les variations de propriétés induites par la géométrie et la qualité incohérente des pièces fabriquées. Par conséquent, relever le défi du contrôle géométrique est sans aucun doute d’une grande importance pour la FA Cold Spray ainsi que pour d’autres technologies de fabrication additive à grande vitesse », peut-on lire dans une étude.
Notes de conclusion
La pulvérisation à froid en FA a ouvert une nouvelle niche dans l’industrie de fabrication additive grâce à sa capacité à fabriquer des pièces de forme presque nette dans une variété de métaux. L’industrie militaire est l’un des principaux domaines qui voient un potentiel dans cette technologie. Néanmoins, l’adoption de la technologie pourrait être étendue à des secteurs d’activité qui cherchent à réduire considérablement le temps d’usinage et le gaspillage de matériaux et à produire des pièces dans des endroits éloignés.
Ce dossier a initialement été publié dans le numéro de Janvier/Février de 3D ADEPT Mag.