A quick search on « bike » on our online media reveals that a lot is currently being done to produce bike using 3D printing and more sustainably. This time, things are different because the process sheds light on a single bike component, pedal, and the use of a unique manufacturing process: Cold Metal Fusion Additive Manufacturing technology.
This story is the result of the collaboration between AM technology developer Headmade Materials and Titanum GmbH, a start-up driven by its passion for cycling and with a knowhow of titanium. From first contact between both parties to the final design, it took about six months to achieve the project.
Today, the “MyTi clipless pedals” have become the first product of Titanum.
How did it start?
The whole story starts with Rico de Wert, cyclist fan and inventor of the MyTi clipless pedals. Last year, his clipless pedal design became a talking point after a mutual contact introduced Rico to Matthias Scharvogel, CEO of Element22*. When talks began about 3D printed pedal bodies and cleats, the enthusiastic response from Element22 brought the project on a different scale: “their case study found their proprietary and innovative additive manufacturing highly suitable for high volume series production of the MyTi pedal design”.
Titanum described the manufacturing process as inspired by aerospace because it required the use of Headmade’s Cold Metal Fusion process – the aforementioned proprietary process of Element22. The technology helps achieve fewer parts and failure points, which results in less weight yet increased strength. The sinter-based Additive Manufacturing process would be an ideal production candidate to achieve high volume production of 3D printed Titanium pedals.
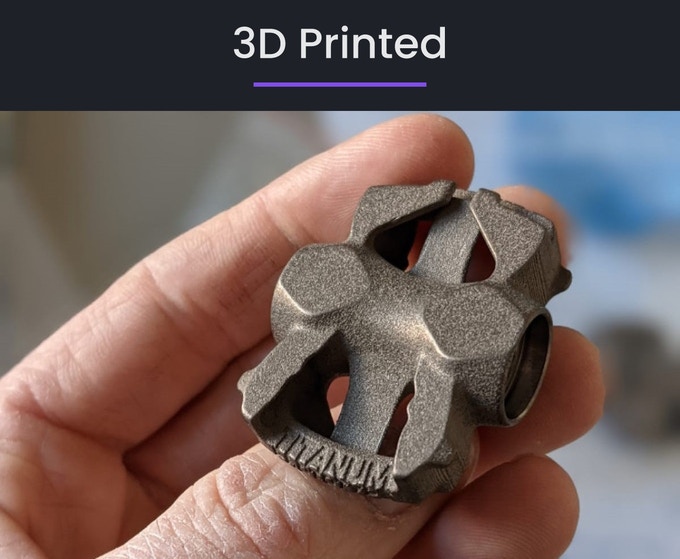
The milestone of a working clipless pedal was quickly attained. Test riders, who experienced Titanum MyTi pedals, felt that, with an increased connectedness and feeling more one with the bike, they form an optimal human foot-bike interface. Highlights of the MyTi pedals are:
- One-piece 3D Printed Titanium Pedal Bodies and Cleats with Blattfeder Technology
- About 100 grams a pair — The Lightest Dual-Sided Pedals on the Market
- 7.8 mm Stack Height (with 4-bolt cleat) — The Lowest for any Dual-Sided Pedal
- Intuitive and Safe Clip-in and Retention Mechanism — Releases Sideways Only
- Fully road and mountain bike compatible through 2, 3 and 4-Bolts Cleats
- ISO 4210-8:2014 certified by EFBE GmbH in Waltrop, Germany
- No rider weight limits
Titanum’s patent pending Blattfeder technology (German for leaf spring) further improves userfriendliness, durability and stability, and speeds up clip-in and release as well as manufacturing.
Titanum is launching a Kickstarter campaign with the goal of starting production and getting its innovative MyTi pedals on bikes of early adopters.
Remember, you can post job opportunities in the AM Industry on 3D ADEPT Media free of charge or look for a job via our job board. Make sure to follow us on our social networks and subscribe to our weekly newsletter : Facebook, Twitter, LinkedIn & Instagram ! If you want to be featured in the next issue of our digital magazine or if you hear a story that needs to be heard, make sure you send it to contact@3dadept.com