How many times have you seen the word “lightweighting” used next to “additive manufacturing”? When one looks beyond the buzz that this combination of words might create, we’ll come to realize that this manufacturing concept involves value equations for specific types of parts, which can lead to improvements on existing products, new business models and new markets.
“Doing more, with less” has always been (and somehow still is) the primary purpose of lightweighting – a manufacturing concept that requires to leverage a wide range of methods to make industrial parts and products weigh less while retaining or improving their technical and mechanical characteristics.
Interest in this manufacturing concept started with aerospace companies that were looking to decrease part size, part count and part weight. At the time, the idea was pretty simple: every gram removed from the weight of an aircraft equates to a reduction in fuel. In another area, they saw that reducing part size for satellites could provide more space to add battery power, thus augmenting the amount of time the satellite could remain in space. Over time, R&D teams have explored the advantage of this concept in AM for other applications and industries, and found out that the benefits in terms of materials, performance, costs, and manufacturing lead time can also be of paramount importance.
The article below aims to understand the basics surrounding “lightweighting of parts using AM”. With a key focus on the software standpoint, the article will discuss the decisive factors that lead to lightweighting of parts, as well as the software strategies that could be explored in this process.
The decisive factors that may lead to lightweighting of parts
Let’s note that lightweighting is primarily often understood as the removal of material from an assembly or part to reduce its weight. In theory, that’s exactly what happens. That’s also the reason why, an emphasis is usually laid on “material reduction” and/or the replacement of some materials by other materials which are lightweight or which can deliver incremental gains.
“It is possible to reduce the overall weight of a part by selecting materials with a higher specific strength. For example, if we compare a stainless steel, an aluminum alloy and a titanium alloy, the higher specific strength of the titanium alloy will enable the use of less material to achieve the same performance level”, Rhushik MATROJA, CEO & Co-Founder of software company Cognitive Design Systems notes.
This focus on “materials” therefore impacts the design of the part that should reflect how the fundamental design changes operated help to minimize material consumption, and eventually build time.
This need for reducing weight using the right material is often addressed alongside another pressing issue: waste. While it increasingly raises questions on how sustainable the production process is, it also raises a number of challenges that are worth considering at the design level. That’s in any case, what Rhushik MATROJA explains:
“Since lightweighting of any structure will impact directly on the mechanical performance of the part, it should be done keeping in mind the mechanical performance of the material.
Manufacturability is one of the most influencing factors for lightweighting. One can have the most lightweight and performant theoretical design, but this design becomes useless, if it is not manufacturable.
Another important factor is the cost of the part. If the lightweighted part using topology optimization is not well designed, then there will be additional costs for the removal of excessive support structures and for the added surface treatment. On the other hand, printing lattice and TPMS structures could increase printing time which leads to increased price of the part”.
Software strategies at the heart of lightweighting
It’s been two decades that manufacturers have been leveraging Additive Manufacturing but advancements in lightweighting of parts have only been seen recently with the utilization of new software strategies designed to address this challenge.
One of the first software strategies often explored at this level is topology optimization. The capability to optimize part topology towards stiffness or strength targets based on Finite Element Methods (FEM) enables purposeful lightweight design of parts. This design strategy optimizes material layout within a given design space, for a given set of loads, boundary conditions and constraints.
The use of lattice or TPMS infill structures is another interesting method to explore. These are hybrids of solid material and empty space that are created in such a way that they dictate the mechanical properties. Using intelligent lattice structures can help explore interesting thermo-mechanical properties. “Knowledge about the performance of those kind of structures is highly critical. Design and simulation processes are required to obtain insights on the performance. Cognitive Design Systems has created a large database of such meta materials with their mechanical properties. Our tool ”Infill Optimizer”, which is part of our additive software ”Cognitive Additive”, intelligently places such structures based on the stress path to reduce the overall weight without decreasing mechanical performance”, Matroja explains.
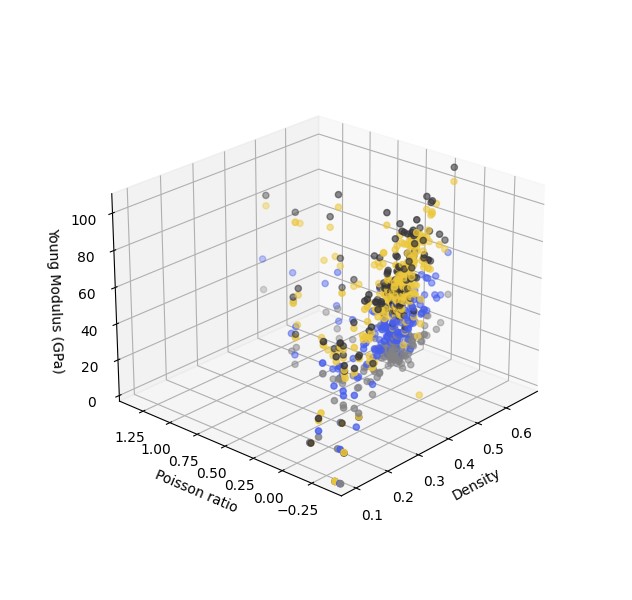
According to Matroja, usually, topology optimization is best suited for powder/resin-based technologies, while the infill strategy works best for FFF or DED processes.
Part consolidation is a strategy that requires solid expertise and ability in bringing several parts into one. If well designed, the part can deliver an improved functionality. A few years ago for instance, Airbus Defence and Space and 3D Systems, developed the first air-worthy metal printed Radio Frequency (RF) filter, tested and validated for use in commercial telecommunication satellites. RF filters are traditionally designed using standard elements such as rectangular cavities and waveguide cross-sections with perpendicular bends, with shapes and connections dictated by standard processes such as milling and spark eroding. Typically, cavities for RF filters are produced by machining two halves that are bolted together, increasing weight, adding assembly steps and extra quality checks. Using CST MWS software, a 3D electromagnetic simulation tool, the 3D Systems team developed a depressed super-ellipsoidal cavity to channel RF currents and reject out-of-band signals. The design was driven by pure functionality, and not dictated by manufacturability and resulted in a single-build part that was faster to produce, reduced production costs and reduced weight by 50%.
Conformal ribbing comes next. The technique is very prevalent in aerospace. According to software company nTopology, whether built from polymers, metals or composites, conformal ribbing aims to enable thinner walls while improving buckling resistance.
New software solutions based on artificial intelligence enable design engineers to “program” algorithms so that they take into account the various constraints of what can (and can’t) be made with a specific type of manufacturing process. This way, their designs evolve and develop into something that can easily be fabricated by AM.
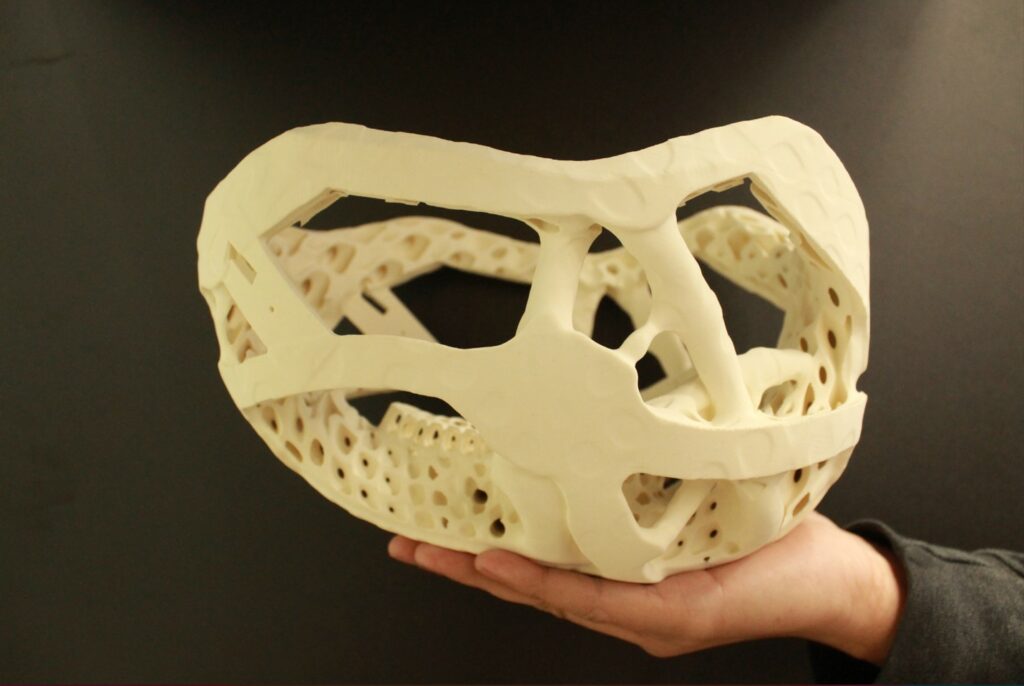
Concluding thoughts
The desire to leverage the full capabilities of AM to reduce time to market or save costs, inspire engineers to develop alternative part geometries resulting in innovative technical solutions portrayed in final applications.
The truth is, what was once considered to be “light” is now obsolete. And this trend will continue, arguably indefinitely, as software solutions continue to evolve.
This exclusive feature has first been published in the July/August edition of 3D ADEPT Mag.
Remember, you can post job opportunities in the AM Industry on 3D ADEPT Media or look for a job via our job board. Make sure to follow us on our social networks and subscribe to our weekly newsletter : Facebook, Twitter, LinkedIn & Instagram ! If you want to be featured in the next issue of our digital magazine or if you hear a story that needs to be heard, make sure you send it to contact@3dadept.com