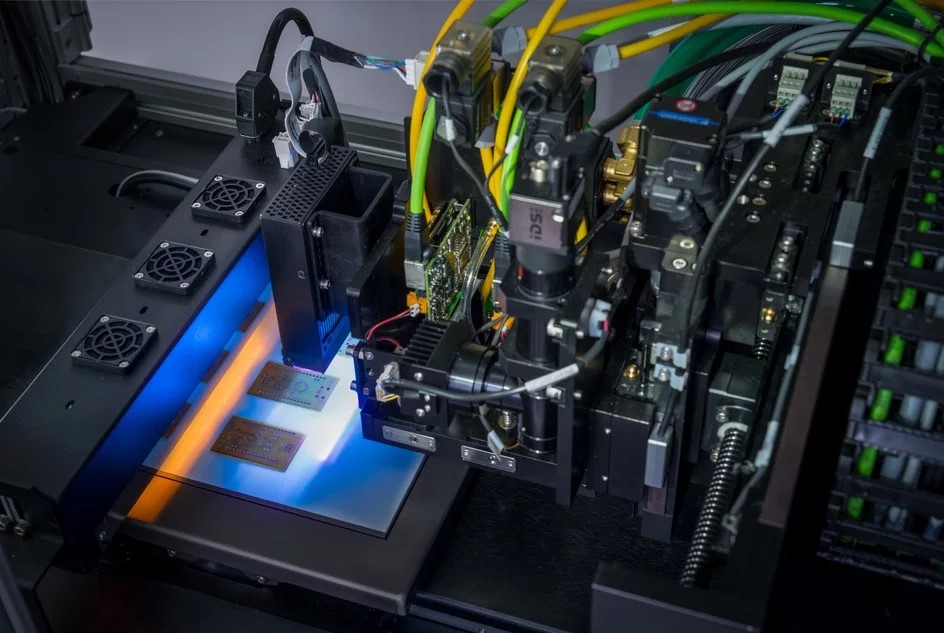
Additive electronics provider Nano Dimension has recently demonstrated the capabilities of its Dragon Fly Pro in shortening and simplifying end-to-end process for mounting BGAs and surface mounted electrical components into printed circuit boards (PCBs).
The viability of 3D printed electronics compared to other manufacturing processes has already been proven effective in some areas. Remember how Harris produced functional circuits in a single print.
Electronic devices with BGA and other SMT components are both small and big devices (phones, watches, large vehicles and airplanes). BGAs are used for integrated circuits and can provide more interconnection pins than can be put on a dual in-line or flat package. This is due to the fact that the entire bottom surface of the device can be used rather than just the perimeter.
Using the DragonFly Pro, the engineers have been able to remove all the stages of ordering and delivering assembled PCBs from external suppliers. Such process simplification leads to more tests and feasibility studies that would not be considered without an electronic 3D printer.
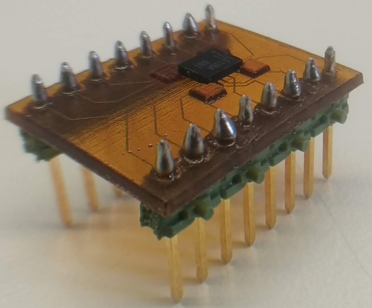
New design changes are not that easy to implement in this area. Indeed, they require a lot of communication between different suppliers which leads to delays in product development cycles, therefore creating a certain number of risks for errors.
According to Nano Dimension, the DragonFly Pro 3D-printed socket structure even improves mounting accuracy of the BGA component since there is less risk that the mounting position will shift.
“With the DragonFly Pro, companies can easily assemble BGA components within one hour,” said Amit Dror, CEO of Nano Dimension. “This means companies can do everything in-house, with no need for outside contractors, less risk of errors and they can complete complex PCB prototypes without high volume manufacturing processes. Greater flexibility enables teams to innovate more freely, resolve problems quickly, and makes it much easier to control product quality.”
For further information about 3D Printing, follow us on our social networks and subscribe to our newsletter!
Would you like to be featured in the next issue of our digital magazine? Send us an email at contact@3dadept.com
//pagead2.googlesyndication.com/pagead/js/adsbygoogle.js (adsbygoogle = window.adsbygoogle || []).push({});