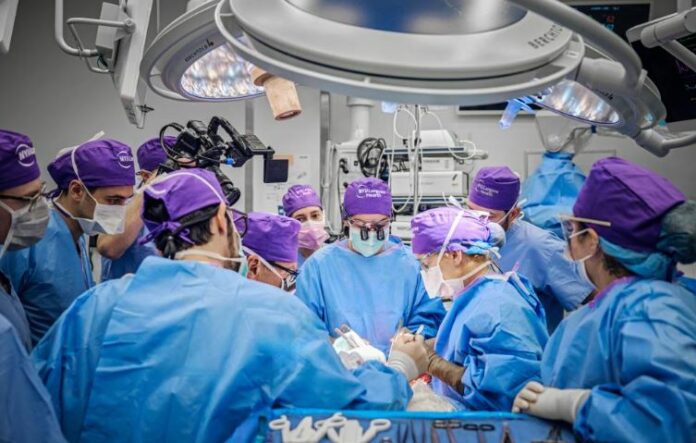
The surgeons at the NYU Langone Health Hospital in New York successfully transplanted a whole eye using 3D printed cutting instruments made by Belgian 3D printing company Materialise, months after the company opened a new medical 3D printing facility in the US.
Materialise virtual pre-operative 3D plan of surgery was used to 3D print various medical devices for the world’s first whole eye transplant which also involved a partial face transplant. The Belgian company’s 3D printing services helped to align medical devices according to the donor and the patient’s needs, resulting in faster and accurate surgery.
The same instruments are used in routine surgical procedures and hence can be used by surgeons to improve patient outcomes in other surgeries.
Enhancing bone fragments positioning
In an operation lasting 21 hours, over 140 surgeons, medical staff and clinical engineers from Materialise treated Aaron James from Kansas whose face was deformed after accidentally receiving a 7200 volt electric shock in June 2021. This is the first time a whole eye transplant is done with a partial face transplant.
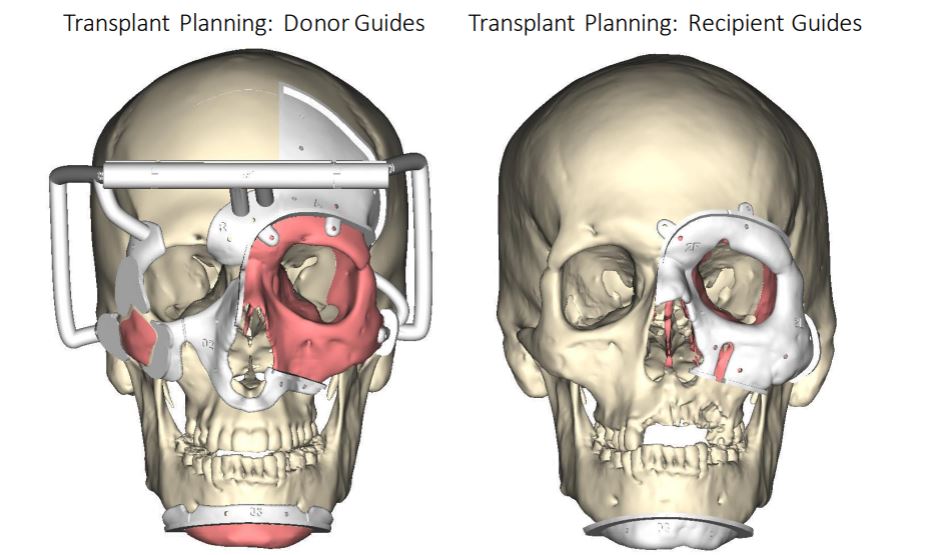
To make this complicated surgery possible, clinical engineers from Materialise worked with the NYU Langone Health Hospital surgical team for several months to develop a virtual plan based on CT scans. Through the preoperative 3D plan surgeons could visualise different scenarios that need to be tackled during surgery and prepare accordingly.
The company also helped the surgeons with cutting guides and bone models to support the seven cadaver labs leading up to the surgery.
Materialise 3D printed personalized bone models and cutting instruments as per the specifications of the donor and the patient which ensures faster bone fragments positioning with enhanced precision.
The company took 24 hours to preplan, design and 3D print the cutting instruments and bone models once they were informed about the donor and supplied the necessary CT scans.
Remember, you can post job opportunities in the AM Industry on 3D ADEPT Media free of charge or look for a job via our job board. Make sure to follow us on our social networks and subscribe to our weekly newsletter : Facebook, Twitter, LinkedIn & Instagram ! If you want to be featured in the next issue of our digital magazine or if you hear a story that needs to be heard, make sure to send it to contact@3dadept.com