Before entering a new year, at 3D ADEPT Media, we have made it a tradition to sit down and discuss highlights, milestones, or solutions that have somehow marked our industry throughout the year. Reasons that may explain the choice of one highlight differ from one person to another. For some reason, the picks below underscore the ingenuity and resilience driving this ever-evolving field.
1.    Fifty shades of large format Additive Manufacturing
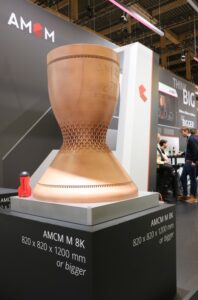
It’s an interesting time for OEMs manufacturing large-format 3D printers. The demand for such 3D printers increases over time and this leads to the development of new solutions across other stages of the manufacturing chain. Take the example of depowdering for instance, the development of the depowdering system SFM-AT1000-S from Solukon is the result of an inquiry from machine manufacturer AMCM GmbH. Now that AMCM can tune 3D printers with building envelopes of 820 x 820 x 1200 mm or even larger, I guess Solukon’s newly launched SFM-AT1500-S would be a great fit for such metal 3D printers.”
That being said, LFAM is truly a trend regardless of the type of AM process whether we talked about composites 3D printing, LPBF, WAAM, polymer 3D printing, or even VAT photopolymerization. This year the common thread within most of the 3D printer launches is the ability to manufacture bigger parts in one single print.
2.    Customization continues to be the manufacturers’ priority
We have highlighted and seen some very cool applications this year. No matter how beautiful they may be, I am sometimes questioning their raison d’être. As money is currently the nerve of war, is customization enough to make AM profitable? Customization can even be part of the agenda, but is it necessarily linked to series manufacturing? So far and from our observation, we cannot always have both. However, those who have been making a profit with AM have been delivering series manufacturing services.
3.    Semiconductors and defense are leading the way
Semiconductors and defense are the two vertical industries where a growing use of AM technologies has been observed. These are the vertical industries one should watch next year.
Today’s challenges in semiconductor production include global production capacity, long lead times and supply demand – all of which can be addressed by AM. If VAT photopolymerization and LPBF processes are the AM technologies that have been put forward the most this year for these applications, other technologies can also be ideal production candidates.
Compared to last year, this year’s coverage analysis saw a rising interest of defense organizations in AM. As announced in the first part of this review, we are not done yet. Whether it is in Europe or in the USA, defense organizations will continue to invest in AM…The number of events that shed light on the use of AM in this vertical is a testament to that. Despite the sensitive nature of the coverage of AM in this vertical, it would be interesting to see what AM can do better in this vertical industry.
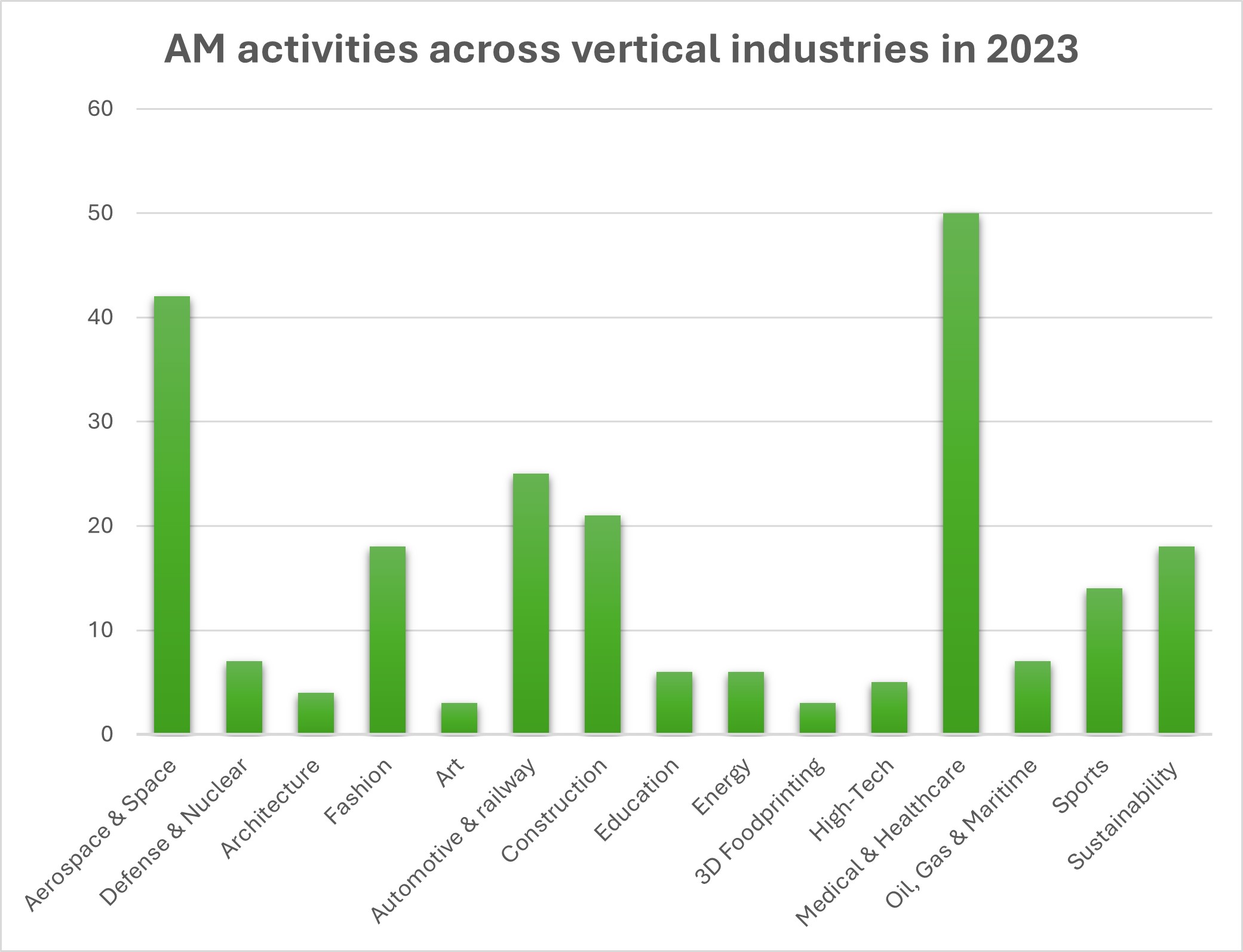
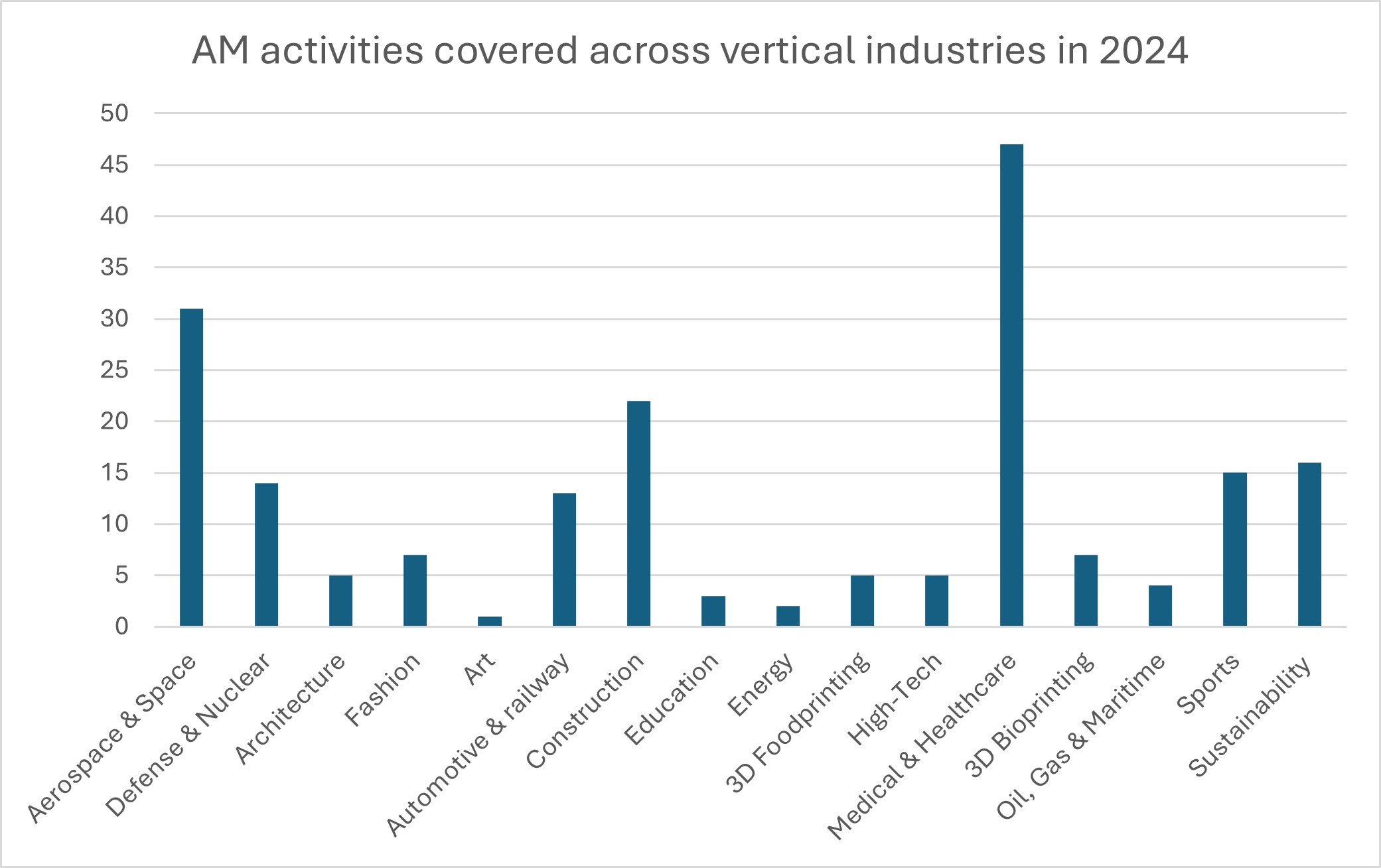
4.    Material extrusion, the segment where we saw the most 3D printer launches
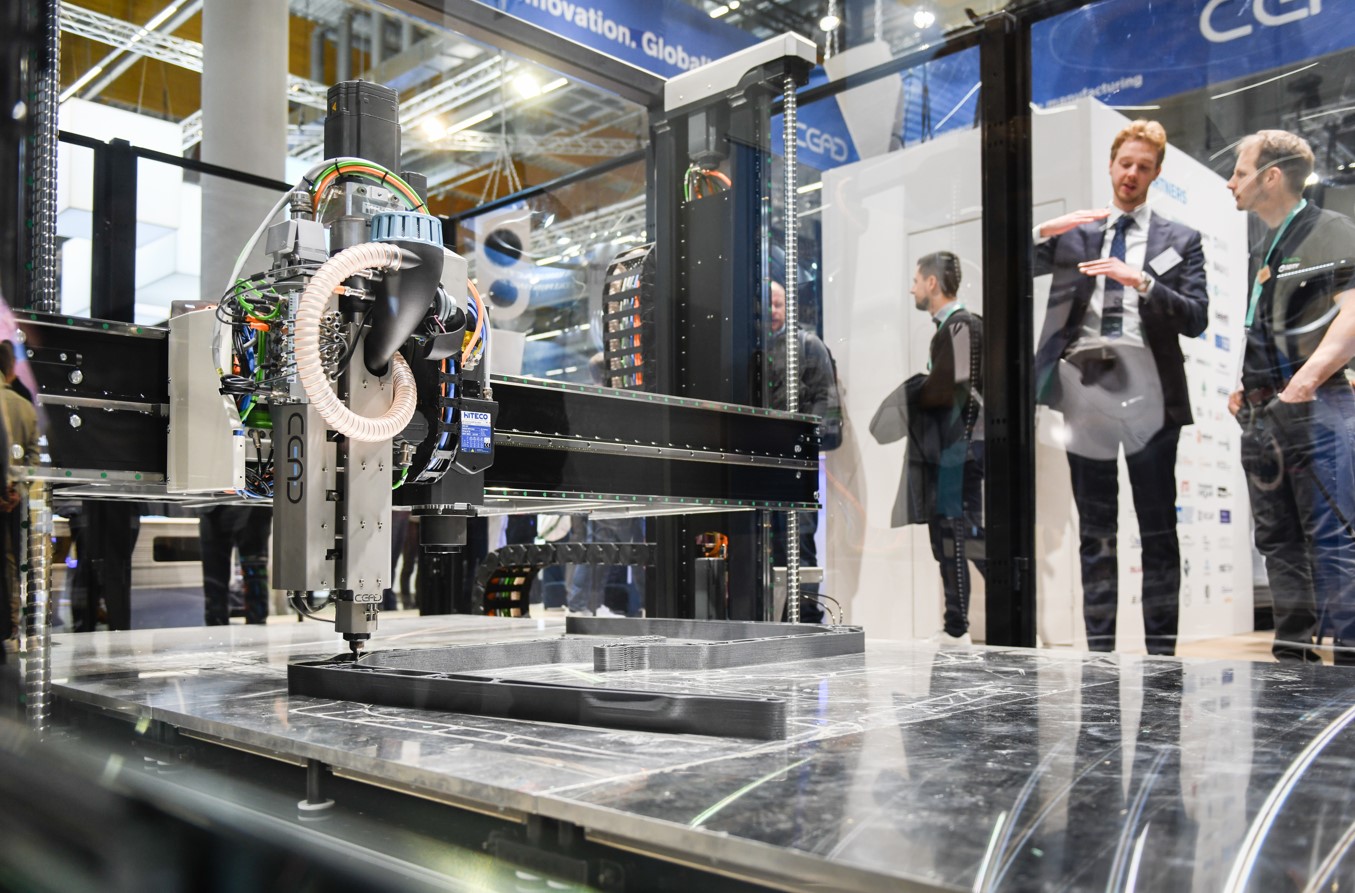
The majority of 3D printer launches covered this year fall into the category of material extrusion, closely followed by powder bed fusion and VAT photopolymerization.
Although most of these launches fall into allegedly known categories of AM processes, each 3D printer features a terminology specific to its manufacturer. This emphasizes the need for a common language framework that can allow users and technology providers to work together more effectively.
That being said, we can’t ignore OEMs who stood out from the crowd with the launch of intriguing AM processes. Among them, there is Rosotics and its Halo “supercreator” – a large-format metal 3D printer described as being at the intersection of materials science and AI; Fugo Precision 3D and its centrifugal 3D printing solution as well as ADDiTEC and its hybrid machine which combines both Liquid Metal Jetting and laser-based Directed Energy Deposition with CNC machining.
5.    The rise of the entry-level 3D printer
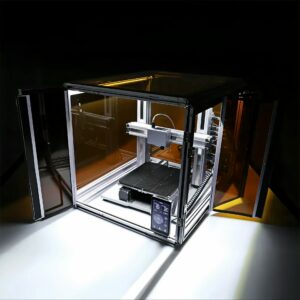
OEMs fabricating desktop and entry-level 3D printers claim their ability to meet the demand for industrialization and to be honest after this latest Formnext, I am sure they can live up to that promise – at least part of that promise.
According to the latest report from CONTEXT, the low-end ENTRY-LEVEL category (<$2,500) excelled with shipments up 34% sequentially, 65% YoY and 41% on a TTM basis. Creality continued to crush the competition with shipments up 64% YoY (and 45% for the full half year) accounting for 47% of all printers shipped in the price class during the quarter. Their growth rate was only bettered by Bambu Lab which again registered triple-digit YoY shipment growth (up 336%) giving them 26% of the global share. A total of 94% of shipments in this sub-$2,500 category were from the top 4 vendors – Creality, Bambu Lab, Anycubic and Elegoo.
6.    The AM software landscape continues to be fragmented
The more we advance, the more the software landscape becomes fragmented. It’s probably the segment of the manufacturing value chain that reveals the most the need for a common language framework and a platform where one can access everything.
It’s a landscape that is increasingly shaped by a growing number of AI-powered solutions. Although I recognize the potential of AI-powered solutions, I can’t help but remind product designers to remain cautious. Indeed, the more boundaries are pushed for AI-powered technologies, the more product designers should pay attention and do their best not to leave apart their creative brainstorming skills.
Furthermore, if software solutions to enhance production come in many shapes and colors, the common thread of this year’s coverage remains their ability to optimize manufacturing while delivering fewer failed builds.
7.    Process monitoring: Defect identification tools
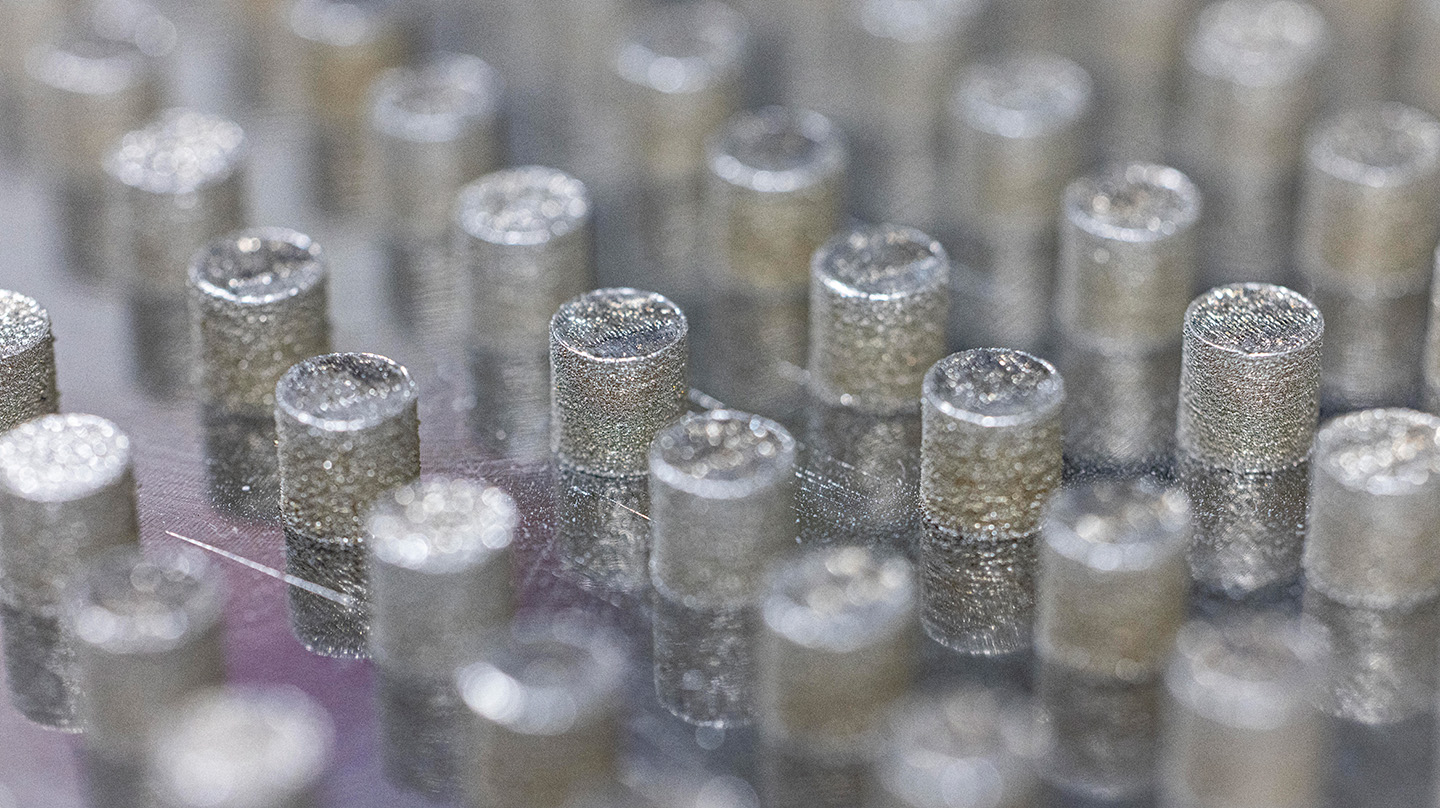
To me, progress in defect identification is one of the best things that could happen to this industry. Its importance is simply underrated yet beyond the ability to improve surface quality and mechanical properties of 3D printed parts, its benefits may lead to material savings, enhanced machine capability, better testing time, and avoiding failure, crashes, and unnecessary testing.
In the list of solutions highlighted this year, whether it is at the research level or in the area of solutions already commercialized, I am hoping to see more cases of defects one can identify “by listening” as they occur in a metal 3D printer and cases related to Phase3D’s software solution.
8.    The combination of several manufacturing processes

Describing this point as a highlight is probably hyperbolizing since we usually note a combination of AM technologies and conventional manufacturing processes in applications that involve series manufacturing. However, it’s quite unusual to see a combination of two AM processes within the same part – as discovered at the recent Formnext show.
One key advantage of such techniques remains the possibility to deliver locally optimized material properties that can fulfill specific functions and that’s something that could be beneficial for a lot of applications if well pursued.
9.    Tungsten 3D printed parts
There is something fascinating about tungsten and the way manufacturers and researchers are trying to “crack the code” of its manufacturing. As a reminder, tungsten’s hardness and extremely high melting point have always made it difficult to process via AM technologies. While LPBF is often mentioned as one of the AM processes that could process it, I want to shed light on part manufacturers who were willing to explore other techniques this year among which Electron-beam additive manufacturing as well as laser powder-blown directed-energy deposition.
10.    SpaceX Raptor 3 gives faith in AM
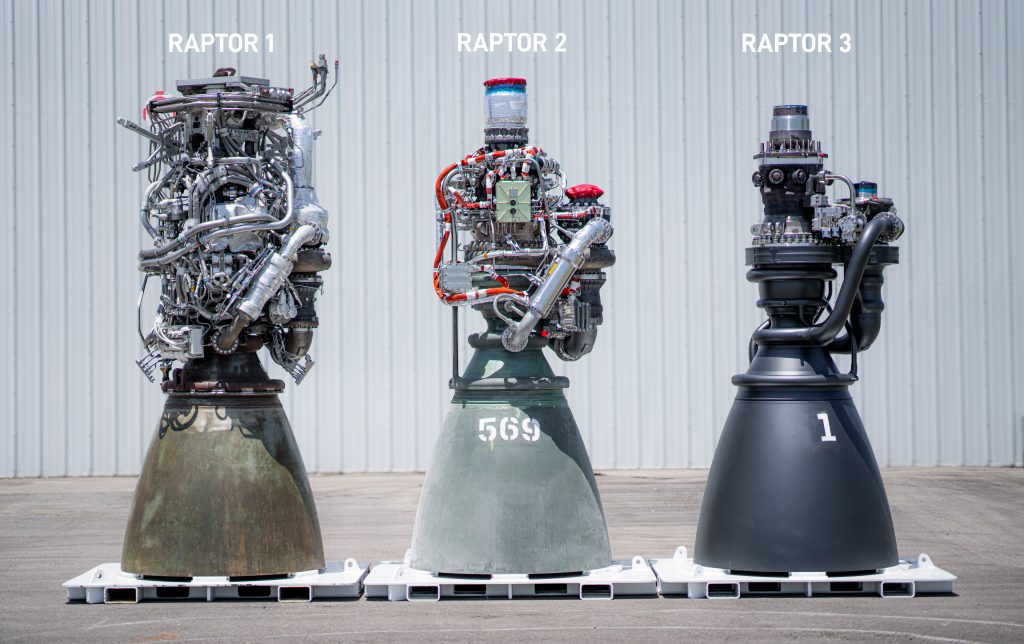
If at any point you thought you’d lost faith in Additive Manufacturing, SpaceX’s Raptor 3 engine should be enough to change your mind. This is certainly the application that grabbed the most attention this year and for good reason: Metal Additive Manufacturing played a pivotal role in transforming space exploration, enabling the transition from state-led programs to private enterprises by reducing cost barriers and shortening the development timeline for space technology.
With this innovation, the team at SpaceX shared a zest of their recipe: less labor and inspection steps, less workforce, enhanced safety and a drastically optimized design.
What more can we ask?
This dossier has first been published in the 2024 November/December edition of 3D ADEPT Mag. Featured image: Copyright: Mesago / Mathias Kutt