Exclusive feature sponsored by the Military Additive Manufacturing Summit.
Do you believe that necessity is the mother of invention? I do, and today, I think that this saying has never been truer than in the military sector. It takes a conversation with John Harrison, Director of Additive Manufacturing at Phillips to realize that the first additive manufacturing applications that have been commercialized in this industry, probably result from solutions deployed in the innovative secret garden of military experts.
While many technologies built for military purposes have found their way into industrial markets, let us not forget that transitioning technology from the defence sector to commercial markets and vice-versa often is challenging, and that’s certainly the reason why companies like Phillips Corporation exist.
I used to define the Phillips Corporation team as the “ideal mediators” between AM technologies’ manufacturers who are continuously trying to reach new industries and the Department of Defense that is continuously seeking to improve its use of AM technologies, but they are more than that. The company is acknowledged for its comprehensive range of manufacturing equipment and services it provides to various industries, equipment and services that encompass automation and robotics tools, preventative maintenance, training, as well as additive manufacturing to name a few of them – in a nutshell, solutions that can propel capabilities, profitability and productivity.
While it’s been six decades that federal government, private sector industry and education players have been relying on Phillips’ manufacturing solutions, it should be noted that the company has started its journey into AM about 16 years ago.
“One of our early applications was at Walter Reid hospital, where doctors were growing skull plates to be used on soldiers with head injuries. Phillips has grown our partnerships to ensure that we can fully support our customers’ needs. In powder bed fusion, we collaborate with EOS. Our Fused Filament partner is Markforged, in cold spray repair we partner with VRC Systems. Spee3D is a partner that has developed a great field-deployable unit. Haas and Sodick provide solutions for post-processing”, Harrison states from the outset.
Furthermore, for the AM industry, the company does not only provide third-party manufacturing equipment but also produces parts and develops an in-house hybrid machine that provides key benefits to the DoD.
“Why the focus on the DoD now?”
Several reasons might explain this increasing interest in AM solutions deployed by and for the DoD. One of them is the fact that the US Department of Defense (DoD) has released its first-ever comprehensive Additive Manufacturing (AM) Strategy in January 2021. This strategy demonstrates a common vision for the use of AM within the nation’s defense program. It also reveals some of the key cornerstones that will require specific attention from all stakeholders.
Those cornerstones include, among other things, improved development of qualification and certification guides, transparent exchange of ideas to foster innovation, new designs and the delivery of rapid capability; the development of a workforce of practitioners, designers, technicians, and acquisition, or even the establishment of guidance to their expeditionary and point of need sources.
Focus on the expeditionary manufacturing’s needs
This latest cornerstone on the guidance of expeditionary and point of need sources has become of paramount importance for the DoD. The truth is, the Army encounters ongoing readiness challenges due to part obsolescence and the inability to rapidly obtain service parts for ageing systems. Sometimes, fielded systems have a supply metrics average of 22 days (CONUS to OCONUS = Continental U.S. to Outside the continental U.S.), hence the interest in Additive Manufacturing that can enable the fabrication of parts directly from a digital file, on-demand, and at the point of need.
Harrison explains that the best example for such expeditionary manufacturing is the space industry, where engineers on earth have to quickly design models and send the digital files to their colleagues in “austere environments” so that they can print their missing parts. However, he also recalls Phillips’s first experience in such contexts:
“Our first experience was when a Marine Gunnery Sergeant cycled back from the Iraq war. His team was tasked with up-armouring Humvees in the field, and they didn’t have the right equipment to accomplish the mission. The Marines were familiar with Haas machines, so we adapted a Haas mill and lathe to fit inside a shipping container. This was later called the Shop Equipment, Machine Shop (SEMS). We entered into a CRADA with the Army to understand the expeditionary needs of the warfighter and worked with them to develop the prototype for the Metal Working Machine Shop Set (MWMSS). This unit improved on the Marine design and included shock mounting, a complete operators manual, and special height modifications. The MWMSS became a program of record, with Rock Island Arsenal receiving modified Haas machines from Phillips and incorporating them into the expeditionary unit. Phillips, in conjunction with Omax, developed a deployable waterjet unit that was used by Marines at Camp Leatherneck. Phillips also supported RFAST, a program that brought engineers and equipment into the Bagram Airbase to support rapid innovations to equipment on the battlefield. Most recently, Phillips has built a prototype that incorporates a wire fed direct energy deposition head onto a Haas mill. We feel that this will give the warfighter more capability to repair equipment in the field.”
Harrison’s example sheds light on the need for taking into account some consideration logistics such as materials, machines and personnel. Most importantly, it highlights how fast the whole process must be to respond to an urgent need, which becomes even more interesting when we know that certain AM technologies are ideal in research environments, therefore are not robust enough to meet the need for expeditionary use.
“While our work on the fielded equipment is important, the real innovation is done by the warfighter. Fielded American Soldiers, equipped with the best manufacturing resources, will tip the battlefield in our favour. They use their skills to find solutions on the fly. I have heard of examples of how the soldiers have made components to get equipment back in the fight, improved the design of the equipment to improve readiness, and even invent new solutions to protect the war fighter. Great minds within the DOD are imagining new possibilities with deployable manufacturing capabilities”, he continues.
Here is the thing, there is still a long road ahead as several questions still need to be addressed: what if expeditionary manufacturing was flexible enough to reduce the Iron Mountain by 20%? What about 50%? What if new expeditionary technology could create drones that could fly off the printer? What if additive technology could provide custom medical care for wounded soldiers?
At the research level, some of these questions are currently being explored. They include for instance the ability to print skin to heal wounds, or 3D printed soldier-enabled drones but one question remains unanswered: what’s happening on the ground?
What technologies are being deployed on the field? And most importantly, what does it imply?
The recent months saw the development of manufacturing in-situ solutions such as “portable 3D printing factory” or “mobile smart factory” concepts.
Although they are certainly very useful, Harrison outlines that “there are many parts that can be made in the field that do not require in-situ monitoring. As the technology becomes more accepted, flight and safety-critical parts will be made. These parts will need to be monitored and certified before use. Manufacturing as close to point of need is the future. I think there will be additive solutions at every layer of support, from CONUS(Continental U.S.) repair facilities to staging and intermediate bases OCONUS (Outside the continental U.S.), to forward operating bases, or “printing in the dirt.” What will vary is how far forward that additive technology can be deployed. Some technologies need better power, large volumes of assist gases, consistent environments, etc. Our partners have recognized this and have created machines designed for expeditionary: Markforged for instance created a field-deployable X7 that is being used by the Marines and tested by the Navy. Spee3D has conducted field trials with the Australian Army on the other hand.”
Technologies other than metal AM can be considered for military applications for sure. The thing is, the choice for another technology – polymer 3D printing for instance – refocuses the debate on part identification/selection. “There are hundreds of thousands of parts in the supply chain, quickly filtering them to determine what parts can be printed (according to the DOD’s needs) is important. We are very interested in deployable plastics that are durable”, our guest notes.
While Continuous carbon fibre and Kevlar reinforced materials from Markforged are worth mentioning as examples of technologies that can be used as metal replacement, the DoD should also confront with another reality: technologies are moving toward cloud-based software. Available power, utilities, equipment size, survivability, serviceability, training, and tooling are key items that need to be rethought so that soldiers can easily adapt to each situation. To comply with this need for flexibility, Philipps Corporation has developed the Phillips Hybrid machine with all these variables in mind.
A closer look at Phillips Hybrid Machine
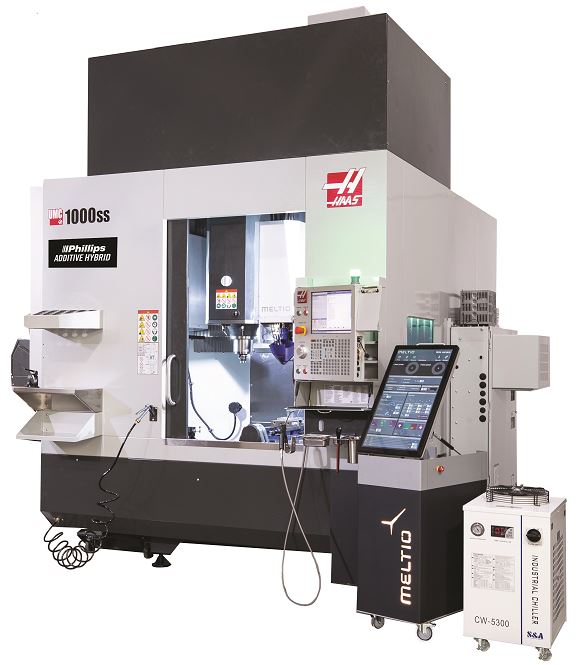
For a manufacturing process that is probably the best of both worlds (additive and subtractive), the team at Phillips has combined two technology solutions to develop the Phillips Additive HybridTM: a laser metal deposition technology and a Haas CNC mill.
Have a look at the March/April Issue of 3D ADEPT Mag that highlights an exclusive feature on Hybrid Manufacturing Processes.
For the team, the integration of a wire fed laser DED head on the Haas machine provides a perfect fit for repair and other manufacturing applications. Moreover, not only can the machine process different additive materials to the same part, achieving this way an accurate design, as well as ideal weight and strength, but it can also 3D print to near net shape. In addition, Harrison’ explanations also reveal that the machine enables the fabrication of high-density parts in a clean working environment with wire laser DED and is compatible with offline programming software such as Autodesk, GibbsCAM and Mastercam.
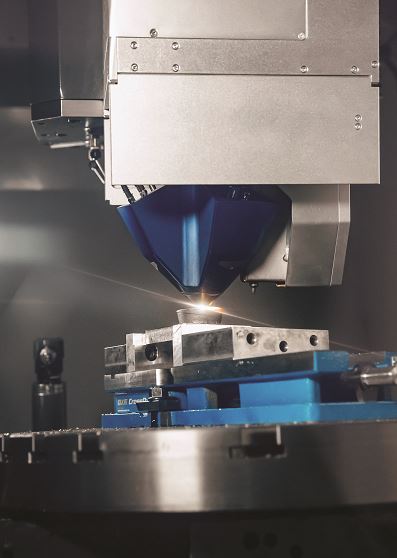
“We did a lot of homework. We like wire material for the process, as it is very clean and stable when the material is stored. The technology we selected does not need an inert environment and minimizes shielding gases. Response to the initial offering has been very good. We have shipped a large 5-axis model to a software company for development purposes. We also have earned a contract with the Navy for a shipboard prototype. The Army has also released a contract to us for developing a solution to retrofit the hybrid head on the MWMSS platform. In addition to DOD applications, interest in the commercial industry is strong. I think the reason is, we are combining the right additive technology with the most popular CNC mill in the U.S.”, the President of Federal Division points out.
What’s next then?
Expeditionary manufacturing is one of the key topics that raise the DoD’s interest right now. In the long-run, the ultimate goals are to modernize national defence systems by improving performance using AM-designed equipment; increase materiel readiness to rapidly prototype and produce direct parts, as well as enable warfighters to employ innovative solutions on the battlefield.
This conversation with John Harrison reveals some of the constraints the DoD might face. However, it also highlights existing solutions to enable expeditionary manufacturing. Harrison reminds that considering AM’s potential and capabilities does not aim to replace conventional manufacturing processes, but rather leveraging practical solutions where it is necessary, to act faster and more efficiently in the field. In this vein, we will keep the current work of SPEE3D with the Australian army on our radar as it may lead to technological solutions that can be commercialised in other markets.
One thing is certain, other solutions will be deployed, several applications will be achieved but the ‘defence secrecy’ will certainly make us wait for several years before we see them onto the commercial market. In the meantime, one of the options we have, to know everything that is happening inside by insiders, is to attend dedicated events like the Military Additive Manufacturing Summit.
Exlusive content created in partnership with the Defense Strategies Institute.
Remember, you can post job opportunities in the AM Industry on 3D ADEPT Media free of charge or look for a job via our job board. Make sure to follow us on our social networks and subscribe to our weekly newsletter : Facebook, Twitter, LinkedIn & Instagram ! If you want to be featured in the next issue of our digital magazine or if you hear a story that needs to be heard, make sure to send it to contact@3dadept.com