The growing investment of companies in research and development aims to foster the development of polymers. Yet, when it comes to industrial needs, the market presents an increasing adoption of metal additive manufacturing. This article features the opportunities of polymers for the additive manufacturing industry.
According to Jérémie Soulestin, researcher at IMT Lille Douai, professionals often use polymers to produce prototypes. They are often not willing to combine 3D printing and plastic to meet industrial needs. As far as technologies are concerned, processes such as stereolithography rely on thermosetting resins which polymerize during the process. In fact, thermosetting resins are even used in extremely low quantities by the plastics industry.
One reason that explains the choice for metallic materials over plastic is the constant search for weight reduction. Industrials in demanding sectors such as aerospace tend to exploit metal additive manufacturing due to its ability to lighten parts, yet, technological developments show interesting opportunities for 3D printing of high-performance thermoplastics such as carbon.
The market therefore reveals an increasing development of ULTEM and PEEK materials to replace metals. For instance, replacing aluminium aircraft supports with PEEK alternatives could result in a 5 -9% reduction in weight, impacting therefore fuel consumption of an aircraft.
What are the opportunities of 3D printing with polymers?
Polymers enables a wide range of applications in industrial 3D printing.
The automotive industry
As mentioned earlier, prototyping is one of the most common applications that require the use of polymers. The automotive industry would have purchased the larger number of 3D printers in 2017 in order to meet prototyping purposes. Those technologies are usually leveraged for shape, fit, testing and validation of parts.
In the motor sports sector for example, additive manufacturing is often used with polymer materials to produce functional parts for racing car tests.
CRP Group, an Italian manufacturer of racing motorcycles used to combine additive and subtractive manufacturing techniques for the fabrication of racing motorcycles. The additive manufacturing process is done with the proprietary polymeric material of the company, Windform®. This material contributes to the manufacturing of functional parts that enable to perform various tests of the motorcycle carried out by the company. It is flexible, elastic and resistant to damages from vibration, deformation, high and low temperatures, and liquids. The Ego Corsa and the Bolid-E are a few examples of motorcycles that have been manufactured using this material.

CRP Group manufactures aerodynamic parts in 3D printing with Windform® materials. CRP Meccanica (partner of F1 teams for the production of hi-tech mechanical components) is working on the development of the braking and suspension system. The two companies are working on the development of the new battery.
Randy de Puniet, former MotoGP rider and 250cc race winner shares his feelings about the demo lap: “The connection with the throttle and the power delivery are very smooth”, he said. “The bike reaches high speed in a very short amount of time, and that’s a good thing. Another good point of the bike is that the rear is very stable when opening the throttle. It’s a very easy bike to get to grips with, so it would be fun to be racing the Energica Ego Corsa against twenty or more riders on identical machinery. I am really pleased with this experience and grateful for the opportunity; I hope my feedback will help Energica continue in the right direction.”
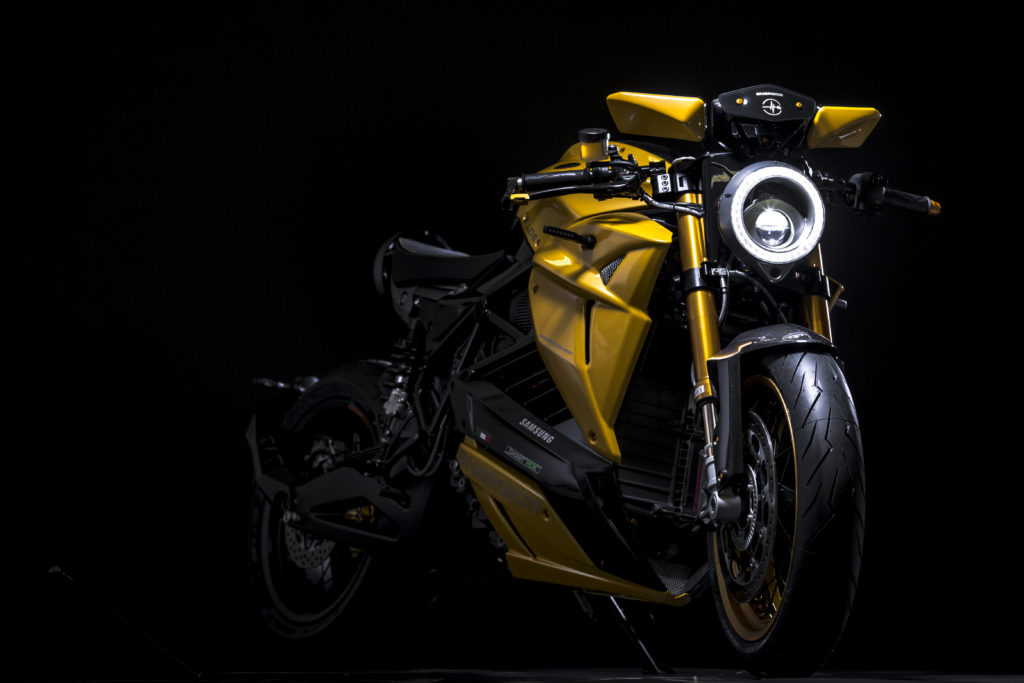
In the construction of the motorbike Bolid-E, front and back headlights/Tail light support have been manufactured using SLS whereas the structural support of the seat has been manufactured using high precision CNC machining.
Effective tooling
3D printing with polymers enables a more efficient tooling. Polymers enable to produce faster, cheaper and more customized tools.
Due to their ease of use and affordable price, FDM and SLA technologies are often preferred for these applications. In the automotive industry, Ford chose for instance Ultimaker printers for its tools.
The medical industry
3D printing with polymers is exploited in a variety of applications: guides, 3D printed surgical tools, production of models, pre-surgical planning and even manufacturing of prostheses.
However, prostheses and hearing aids are part of the applications that stand out from the crowd. They require the use of the SLA process.
ACS Custom is a manufacturer of custom hearing protection, in-ear monitors and other communication devices. The company has quadrupled the production of custom hearing protection with Figure 4™ Standalone 3D Printers. The platform of 3D Systems integrates high speed digital molding, a process that speeds and simplifies the production of plastic parts.
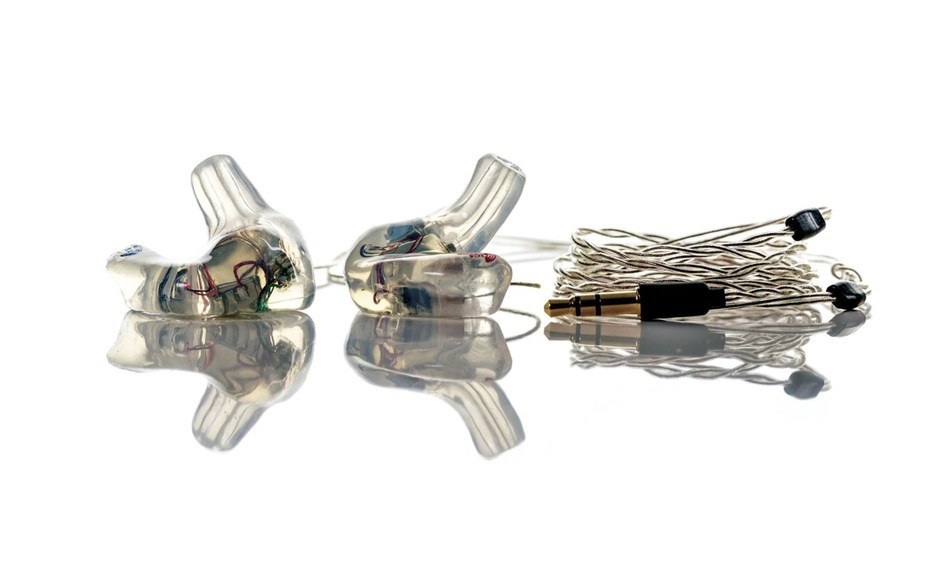
Customization of mass consumption products
The use of polymers in additive manufacturing enables to produce affordable and quality products for mass consumption.
A good example of such type of application is the partnership of Formlabs and Gilette. Gilette has launched Razor Maker™: powered by Gillette®, a platform that takes advantage of Formlabs’ SLA printing technology to offer a series of customizable 3D-printed handles.
Once they have chosen from a range of 48 complex designs, consumers will select the handle and personalize again by choosing from seven color options (black, white, red, blue, green, grey and chrome) and by adding text to the design. Handles can accommodate either Gillette’s MACH3 or Fusion5 ProGlide razor cartridges.
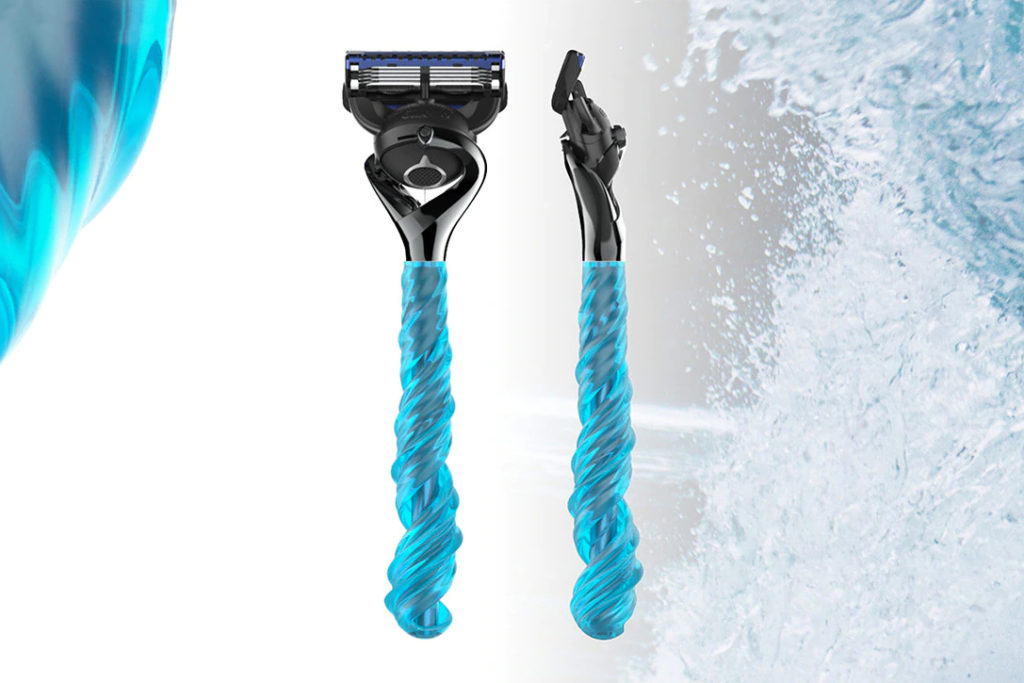
3D printing processes that require the use of polymers
As you may have noticed, several 3D printing technologies can process polymers. They can be ranged as follows:
Material Extrusion | Vat Polymerisation | Powder Bed Fusion | Material Jetting | |
FFF | SLA | SLS & Multi Jet Fusion | Material Jetting |
Disclaimer: this article has originally been featured in the 2019 February issue of 3D ADEPT Mag.