L’investissement croissant des entreprises dans la recherche est de plus en plus focalisé sur le développement des polymères. Et pourtant lorsqu’il s’agit de besoins industriels, le marché présente une forte utilisation de la fabrication additive métallique. Cet article propose un regard sur les raisons qui expliquent le choix des professionnels pour les matériaux métalliques plutôt que les polymères, les opportunités qu’ils présentent dans la fabrication et les technologies qui leur sont adaptées.
Pour Jérémie Soulestin, chercheur à IMT Lille Douai, les professionnels utilisent souvent les polymères pour fabriquer des prototypes. En effet, ils ne sont pas souvent très enclins à combiner impression 3D et matière plastique pour servir les besoins industriels. Pour ce qui est des technologies, il faut dire que des procédés tels que la stéréolithographie (SLA) sont compatibles avec des résines thermodurcissables, qui polymérisent au cours de la fabrication. Celles-ci sont en réalité utilisées en très faible quantité par l’industrie plastique.
Par ailleurs, une raison qui explique la préférence du métal par rapport au plastique est la recherche constante de la réduction du poids. Pour les secteurs exigeants tels que l’aéronautique ou l’aérospatiale, les industriels ont tendance à préférer la FA métallique aux polymères pour alléger les pièces, et pourtant les avancées technologies présentent des possibilités intéressantes pour l’impression 3D des thermoplastiques haute performance comme le carbone.
De même les matériaux ULTEM et PEEK de plus en plus proposés par les fabricants peuvent être utilisés à la place des métaux. Techniquement parlant, remplacer des supports d’avion en aluminium par des alternatives en PEEK pourrait entraîner une réduction de 5 à 9 % du poids, autrement dit, un gain au niveau de la consommation de carburant d’un avion.
Quelles sont les opportunités que présentent les polymères pour l’industrie ?
L’impression 3D industrielle présente un large éventail de possibilités de fabrication avec les matériaux polymères.
L’industrie automobile
Le prototypage évoqué ci-dessus est l’utilisation la plus courante. L’industrie automobile présente d’ailleurs un certain nombre d’applications avec ces matériaux. Selon des analyses récentes, l’industrie automobile aurai acheté le plus grand nombre d’imprimantes en 2017 pour des besoins de prototypage. Les diverses technologies sont notamment utilisées pour la forme, l’ajustement, les tests ou encore la validation.
Dans le secteur des sports automobiles par exemple, la fabrication additive est souvent utilisée avec des matériaux polymères afin de produire des pièces fonctionnelles pour les essais de voitures de course.
Le CRP Group, fabricant italien de motos de course, a l’habitude de combiner les techniques de fabrication additive et les techniques soustractives pour la fabrication de ces motos. La fabrication additive s’effectue en général avec le matériau polymère de la société, Windform®. Ce matériau contribue notamment à la fabrication de pièces fonctionnelles utilisés dans les tests effectués par la société. Il est flexible, élastique et résistant aux vibrations, aux déformations, aux hautes et basses températures et aux liquides. L’Ego Corsa et le Bolid-E sont quelques exemples de motos qui ont été fabriqués en utilisant ce matériau.
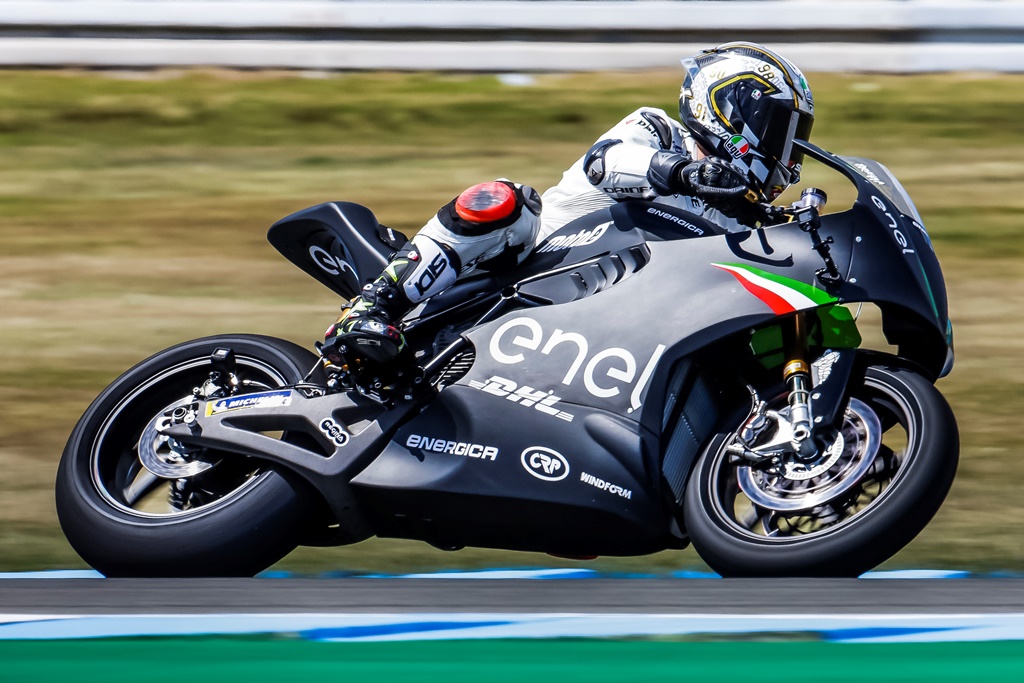
CRP Group fabrique des pièces aérodynamiques par impression 3D avec des matériaux Windform®. Sa filiale, CRP Meccanica (partenaire stratégique des équipes de F1 dans la production de composants mécaniques de haute technologie) travaille sur le développement du système de freinage et de suspension. Les deux entreprises travaillent sur le développement d’une nouvelle batterie. Tous ces éléments ont amélioré la performance générale de la moto en la rapprochant des cibles prédéfinies.
Pour Randy de Puniet, ancien pilote MotoGP et vainqueur de la course 250cc qui a pris part aux premiers tests avec l’Ego Corsa : « La connexion avec la manette des gaz et la puissance délivrée sont très fluides. La moto atteint une vitesse élevée en très peu de temps, et c’est une bonne chose. Un autre bon point de la moto est que l’arrière est très stable lors de l’ouverture de la manette des gaz. Il est très facile à maîtriser, il serait donc amusant de courir l’Energica Ego Corsa contre une vingtaine de pilotes ou plus sur des machines identiques. Je suis vraiment heureux de cette expérience et reconnaissant pour l’opportunité ; J’espère que mes commentaires aideront Energica à continuer dans la bonne direction. »
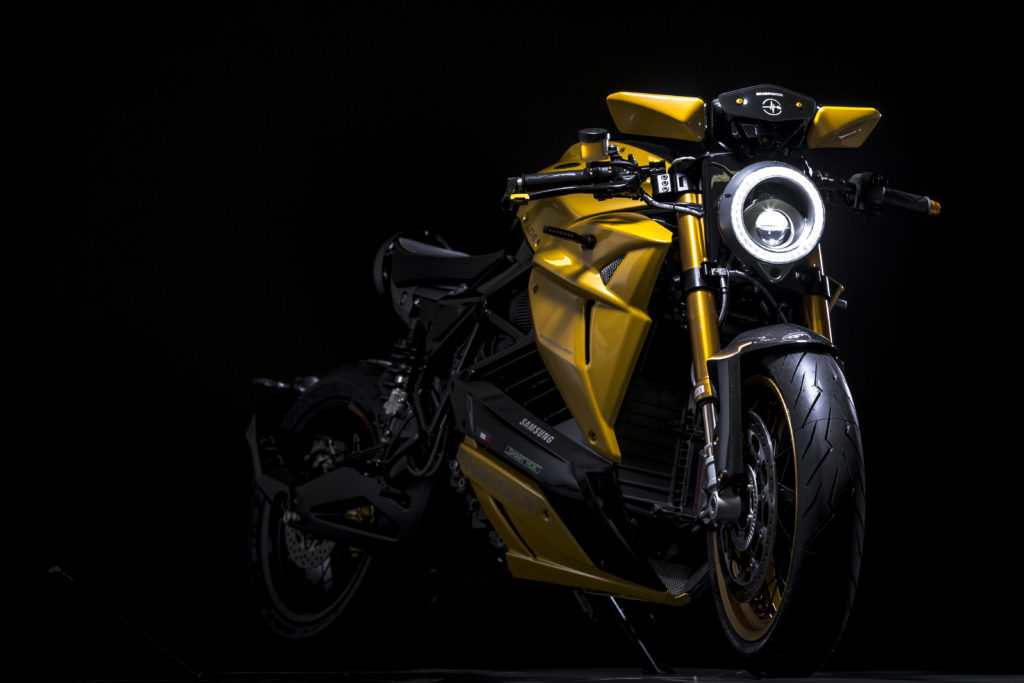
Pour la construction du Bolid-E, Les phares avant et arrière/supports de feux arrière ont été fabriqués à l’aide de la technologie SLS tandis que le support structurel du siège a été fabriqué par usinage CNC de haute précision.
Un outillage plus efficace
L’impression 3D de polymères pour l’outillage permet d’obtenir des outils plus rapides, moins chers et personnalisés.
Dus à leur facilité d’utilisation et à leur prix abordable, les technologies FDM et SLA sont souvent plébiscitées pour ces applications. Pour citer un exemple de l’industrie automobile, Ford a fait le choix des imprimantes Ultimaker pour son outillage.
L’industrie médicale
L’impression 3D de polymères est exploitée dans bon nombre d’applications médicales : les guides, outils chirurgicaux imprimés en 3D, la fabrication d’organes humains, la planification pré-chirurgicale et même la fabrication des prothèses.
Toutefois, les applications qui tendent à sortir du lot sont les prothèses et les aides auditives qui requièrent l’utilisation du procédé SLA.
ACS Custom, fabricant de protections auditives personnalisées, de moniteurs intra-auriculaires et d’autres dispositifs de communication a quadruplé la production de protections auditives en utilisant des imprimantes 3D Figure 4 ™ Standalone. La plateforme de 3D Sytsems intègre le moulage numérique haute vitesse, un procédé qui accélère et simplifie la production de pièces plastiques.
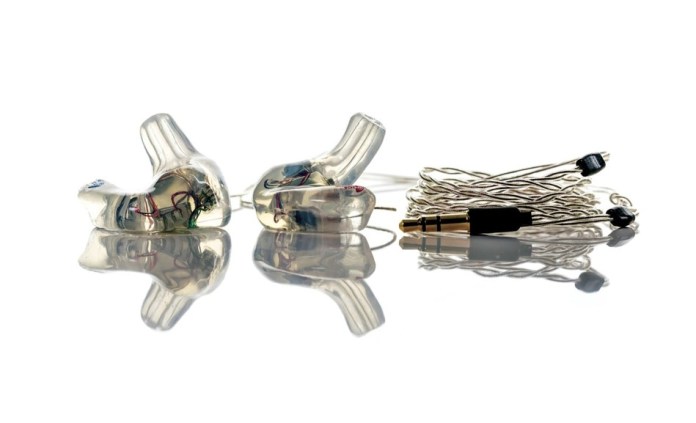
Les produits personnalisés de consommation de masse
L’utilisation de l’impression 3D pour la production de masse reste raisonnable (financièrement parlant) et de qualité lorsqu’on utilise l’impression 3D de polymères.
En s’associant à Formlabs pour créer des manches de rasoir personnalisés, Gilette présente un bel exemple de l’impression 3D de polymères.

Une fois qu’ils auront choisi parmi une gamme de 48 modèles complexes, les consommateurs choisiront le manche idéal et le personnaliseront de nouveau en choisissant parmi sept couleurs (noir, blanc, rouge, bleu, vert, gris et chrome) et en ajoutant du texte au modèle. Les manches peuvent recevoir les cartouches de rasoir MACH3 ou Fusion5 ProGlide de Gillette.
Les procédés de la fabrication additive de polymères
Vous l’aurez compris, il existe de nombreuses technologies qui peuvent traiter les polymères. Les procédés d’impression 3D qui permettent l’utilisation de ces matériaux sont classés comme suit :
Material Extrusion | Vat Polymerisation | Powder Bed Fusion | Material Jetting | |
FFF | SLA | SLS & Multi Jet Fusion | Material Jetting | |
Disclaimer : cet article a été initialement présenté dans le numéro de février 2019 de 3D ADEPT Mag.