Chaque année, ARIS (abréviation d’ « Akademische Raumfahrt Initiative Schweiz ») lance des projets aérospatiaux innovants pour les étudiants des universités suisses.
En novembre 2020, l’organisation a fabriqué la première fusée supersonique de Suisse dans le cadre du projet EULER. Le fabricant d’imprimantes 3D SLS Sintratec, sponsor du projet, a soutenu l’équipe avec la production de certains composants imprimés en 3D. Aujourd’hui, le fabricant de machines a partagé une expérience similaire qu’il a vécue dans le cadre du projet étudiant PICCARD.
Nommé en l’honneur du physicien Auguste Piccard, le projet 2021 a pour ambition de construire la première fusée à propergol hybride d’ARIS en moins d’un an, et de remporter un concours international de fusée. Des tests de simulation révèlent que la fusée hybride atteint une altitude de plus de 6 kilomètres et établit un nouveau record mondial.
L’un des éléments clés qui ont conduit à ce résultat est l’utilisation de diverses technologies lors du processus de fabrication, notamment l’impression 3D.
Samuel Rütsche, un ingénieur structurel qui a travaillé sur le projet, a mis au point un nouveau mécanisme d’accouplement, qui est nécessaire pour combiner les différents segments de la fusée. Une fois la fusée mise en place et son réservoir rempli, la buse de remplissage est rétractée juste avant le lancement. « Comme nous ne voulions pas qu’il y ait de trou sur le côté de la fusée, j’ai développé une trappe qui se ferme automatiquement lorsque la buse de remplissage est retirée« , explique Rütsche. Cette trappe est l’un des éléments que les étudiants ont réalisés à l’aide des technologies d’impression 3D.
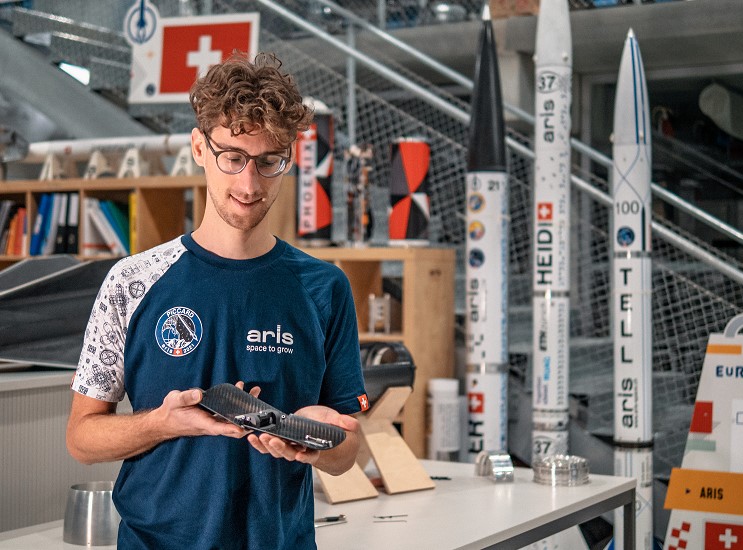
Pour développer et tester rapidement leurs conceptions, l’équipe PICCARD s’est appuyée sur des prototypes FDM. Pour les pièces structurelles plus exigeantes, comme la charnière de la trappe, le frittage laser sélectif (SLS) s’est avéré la meilleure solution. « La SLS peut être très bien utilisé dans l’aérospatiale, car il permet de fabriquer des composants très légers et d’intégrer plusieurs fonctions dans une seule pièce« , souligne Samuel. Sintratec a ensuite produit et parrainé les pièces en nylon PA12 requises. Selon Samuel, « les propriétés du matériau des pièces de Sintratec sont (presque) isotropes et ont une meilleure résistance à la température que nos imprimantes FDM » – un avantage clé lorsqu’il s’agit des conditions extrêmes dans lesquelles ces pièces doivent fonctionner.
Une fois les pièces combinées à la trappe, le mécanisme a fonctionné comme prévu et a permis un carénage en douceur de la fusée lors du décollage. « Cela a permis à notre fusée de ne pas fondre au soleil et a donc contribué à la réussite de notre lancement en octobre« , résume Samuel.
N’oubliez pas que vous pouvez poster gratuitement les offres d’emploi de l’industrie de la FA sur 3D ADEPT Media ou rechercher un emploi via notre tableau d’offres d’emploi. N’hésitez pas à nous suivre sur nos réseaux sociaux et à vous inscrire à notre newsletter hebdomadaire : Facebook, Twitter, LinkedIn & Instagram !