Two things trigger my interest in the development of the Lumia 3D printer: the product development time as well as the technology. This technological solution is the result of a collaboration between on-demand manufacturing platform Xometry and Axtra3D, a developer of advanced Additive Manufacturing solutions using Optoelectronics.
Together they have created a 3D printer based on a patented Hybrid PhotoSynthesis (HPS) technology, which could combine the benefits of SLA, DLP, and LCD. The stake is even higher when we know that, when it comes to resin 3D printing, operators are often hesitant between the advantages and disadvantages of SLA, DLP and LCD. According to Xometry, choosing between these three solutions requires compromises, either on print speed and resolution (DLP/LCD) or on surface quality and print area (SLA).
So, what makes Hybrid PhotoSynthesis (HPS) outstanding?
HPS enables a printing process with fine resolution and delivers high print speeds and excellent surface quality even with large print areas. The process combines two light sources in a custom assembly (DLP & Laser) in order to create a harmonized light engine that efficiently harnesses the power of the two sources.
“In our HPS technology, the Laser defines the resolution and as a result, HPS offers higher resolution and fine feature reproducibility than a standard DLP,” explains Gianni Zitelli, one of the founders of Axtra3D.
The new process therefore delivers the speed of DLP/LCD with the surface quality and scalability of SLA, along with ultra-fine resolution, continuous printing and isotropic part performance capabilities.
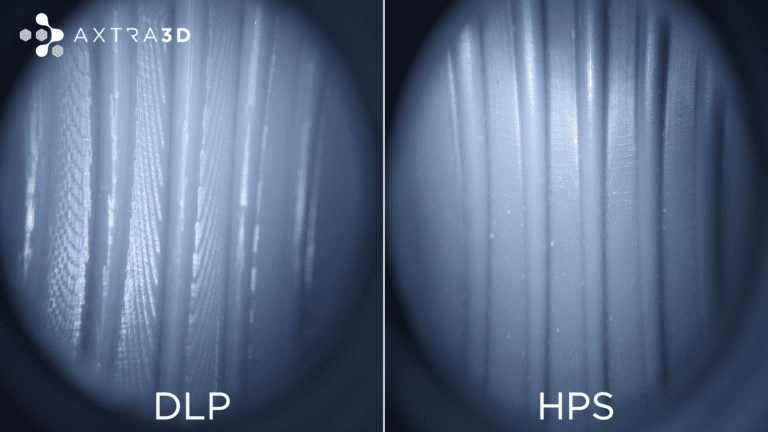
“Users often have high surface finish costs,” states Praveen Tummala, the other cofounder of the company, “but with the fine surface quality and resolution offered by HPS, they can save time and money as the 3D printed parts don’t require any post-print surface finishing”.
Where does Xometry come into play?
The story tells us that the project started at the beginning of 2021 with the objective of launching their 3D printer during the Formnext forum held in November of the same year. “We thought it would take us about 18 months to complete a project like this,” explains Tummala. “Thanks to the team and our partners in Europe, it only took us 9 months”.
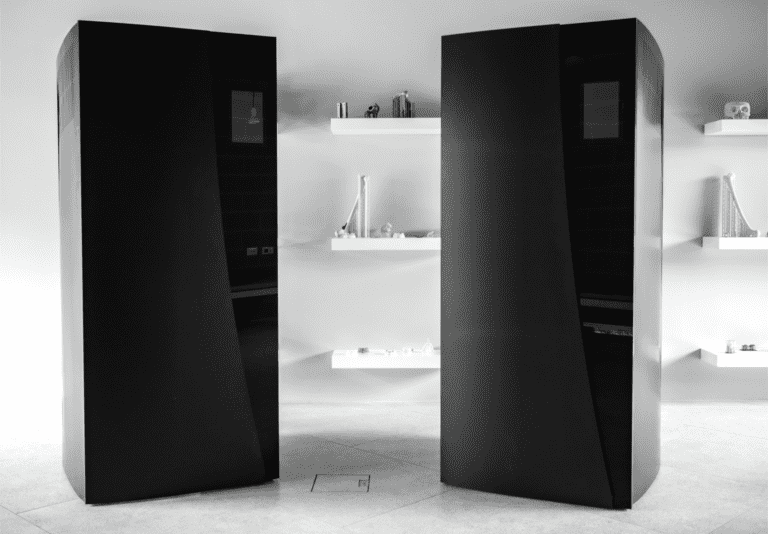
In August, the Italian team launched the first simulation of the complex optical system which was a resounding success. This breakthrough then accelerated the whole production process. “A lot of the credit goes to Xometry, as they were able to deliver about 2,000 parts in 6 weeks, an extremely demanding timeline,” states Zitelli. “We have access to CNC providers in Italy, but it wouldn’t have been a strategic move for our company. Working with Xometry gives us access to thousands of providers worldwide—this is the real value of our collaboration”.
In order to finish the project in time for the forum, Axtra3D called on Xometry to produce every single aluminium CNC machined part used to assemble the printer, from very small components for the light system to elements for the printer’s base. “We can’t imagine any other partner who could have been able to deliver the parts in time to allow us to launch the product and exhibit it at Formnext,” says Tummala. “
The Axtra3D team worked very closely with Liana Zedginidze of Xometry during the entire production process. “We are highly indebted to Liana for her support of our project. She was available for us round the clock and ensured that the ordered parts were produced and delivered on time,” said Zitelli.
The next step for both partners is now to produce 10 beta 3D printers by June 2022 in order to launch their product on the industrial market.
Remember, you can post job opportunities in the AM Industry on 3D ADEPT Media free of charge or look for a job via our job board. Make sure to follow us on our social networks and subscribe to our weekly newsletter : Facebook, Twitter, LinkedIn & Instagram ! If you want to be featured in the next issue of our digital magazine or if you hear a story that needs to be heard, make sure to send it to contact@3dadept.com