Hot isostatic pressing (HIP) is a process used to reduce porosity and increase density in powders, cast and sintered parts in a furnace at high pressure (100-200 MPa) and at temperatures from 900 to 1250°C (1652°F to 2282°F). To guarantee material properties in demanding environments, the process has been a key part of upstream production processes such as casting, MIM, and over recent years, Additive Manufacturing (AM). In AM especially, the process has proved its efficiency in removing defects and improving the mechanical properties of materials for critical 3D printed components. The dossier below aims to understand how and where exactly HIP can influence the AM process to make the most of it.
This dossier is part of our series of “post-processing” articles, which aim to demystify each post-processing task that can be used at the end of the additive production. Remember that post-processing is an umbrella term that covers a variety of stages that 3D-printed parts have to undergo before being used for their final purpose. Needless to say, the use of each post-processing task depends on several factors including the AM process and materials used as well as the ultimate goal to achieve for a given 3D printed part.
HIP is considered a type of heat treatment solution that can be applied to parts manufactured via both AM and traditional manufacturing processes. As a reminder, in a previous dossier, we discussed heat treatment for AM parts. In this feature, we will focus on helping AM users understand:
- The differences in the use of HIP for casting, MIM and AM
- How this process is being performed for 3D-printed parts especially
- The decisions that may lead to the use of HIP
The differences in the use of HIP for casting, MIM and AM
Although HIP is mostly associated with metallic parts, it should be noted that it can also be used to reduce porosity and increase density in ceramics, polymers, and composite materials. While metals and ceramics are the most-widely used materials with HIP, Greg Lane, Key Account Manager at Aalberts surface technologies, notes that Fe-, Ni-, and Ti-base (super-) alloys are some of the typical metals that can be treated via HIP, along with Aluminum ( AlSi10Mg and A357), Cu, SS , Tool Steels, Co alloys, MCrAlY. For this reason, in this article, most examples and insights will be given taking into account metal 3D printed parts.
Speaking of how porosity and defects occur, Greg Lane said: “Porosity is generated during solidification in investment castings and AM as well as during sintering. A remaining pore is always a weak spot and can serve as a possible crack initiation site, thus, limiting the lifetime of a part. Even a small network of pores within a part makes crack initiation and propagation very easy, especially when subjected to cyclic loading.”
If experts agree with the fact that the goal of HIP remains the same – enhance material properties and remove defects – regardless of the manufacturing process used, there are a few considerations that are specific to casting, Metal Injection Molding (MIM), or Additive Manufacturing (AM).
The HIP task in casting aims to mainly address porosity issues while with MIM, it helps to improve the density of the final product. As far as AM is concerned, HIP helps to meet issues related to defects and pores raised during the manufacturing process.
As you can see, HIP is not a “one-size-fits-all” solution. Understanding how it works is important to assess the specific considerations related to metal 3D printed parts.
How this process is being performed for 3D-printed parts especially

In general, the HIP process happens in a pressure vessel inside a hot furnace. Parts are placed inside the chamber, which is then heated up, filled with an inert gas like argon to make it pressurized, and kept at this temperature for a specific time. The heat and pressure are evenly applied to the part to remove any holes. Sometimes, rapid cooling with pressure is also used as a quick cooling bath. The whole process can take 8 to 12 hours or longer
HIP can be leveraged with parts produced via almost all metal AM processes. In his list of the most used processes, Lane counts Laser Beam Powder Bed Fusion (PBF-LB), Electron Beam Powder Bed Fusion (PBF-EB), Wire Arc Additive Manufacturing (WAAM), as well as Binder Jetting.
As far as HIP for 3D printed parts is concerned, Lane first recalls that most of the commercial HIP treatments applied to AM parts are the same as for cast parts, but are not optimized. “However, the nature of the AM process is quite different in comparison to the aforementioned manufacturing routes. The rapid solidification during the build job produces a very fine microstructure with unique properties. This structure can be up to two orders of magnitude finer in comparison to the investment cast counterparts, even for the same type of alloy. Because of this, a tailored HIP cycle can have a huge positive impact on the properties of an AM part and the AM production chain itself,” he adds.
“A typical HIP cycle starts with heating where pressure and temperature are increased. During the holding/soaking the combination of high temperature and pressure up to 200 MPa closes the pores and cracks in the material. The materials are virtually fused to a defect-free state. After a specific amount of time, the cycle is terminated via cooling. Modern HIP equipment can set desired heating and cooling rates as some processed materials require fast or fixed cooling rates,” he continues.
What we learned from Lane is that temperature, pressure and hold time are the three main parameters in an HIP cycle that determine densification. On another note, even though powder-based 3D printing materials are usually very dense, they can still lead to defects like pores and internal cracks. These defects including their size and occurrence depend on the type of powder and how it’s printed. They can therefore alter the mechanical properties of the material – especially fatigue behavior. HIP can help address these challenges and help deliver a relatively dense material.
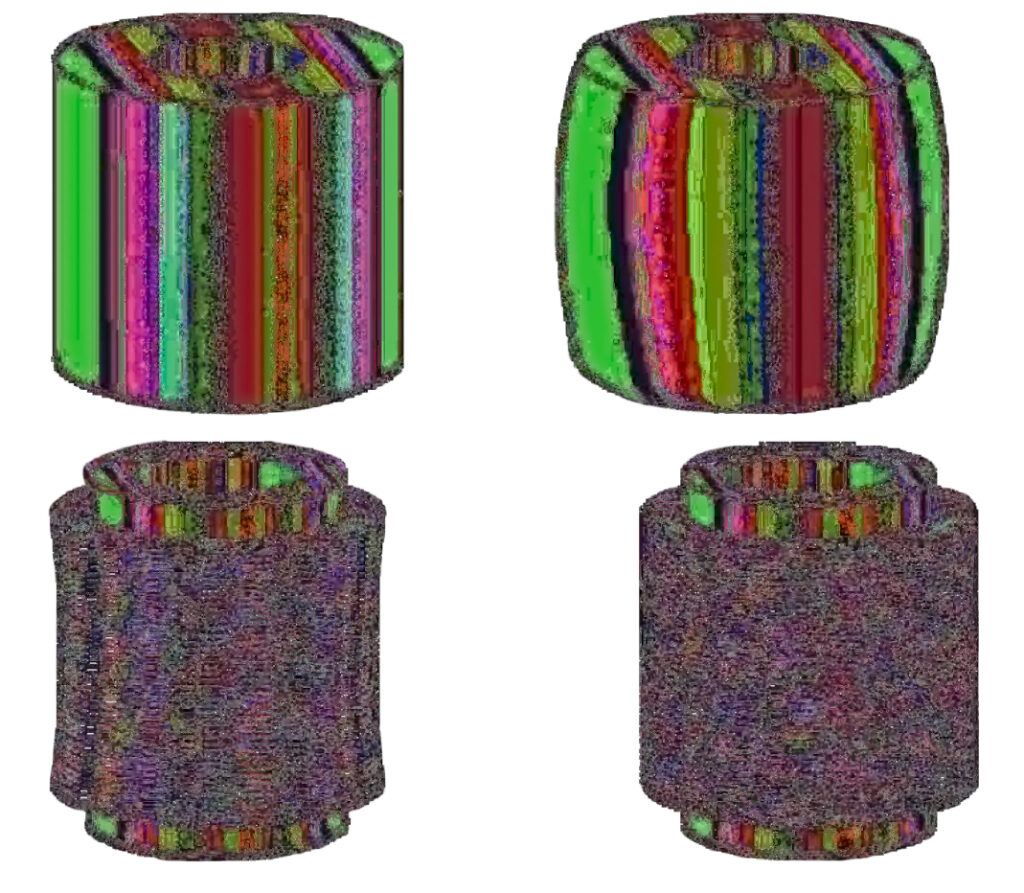
design (below). Without pressure applied (left) and with pressure applied
(right). Source: Heat treatment of PM parts by Hot Isostatic Pressing by Anders Eklund
The decisions that may lead to the use of HIP rather than another alternative post-processing process
Many are familiar with the use of HIP for the densification of castings for industries with very high demands on fatigue resistance, such as the aerospace industry and industrial gas turbine industry. Interestingly, AM yields an ever-increasing demand for HIP beyond these industries.
HIP has already led to the manufacture of different types of components such as the large and massive near net shape metal parts used in the oil & gas industry, weighing up to 30 tonnes, or net shape impellers up to one metre in diameter – all of which can be produced via AM processes. Other applications range from orthopedic implants to racing cars and rocket engines.
So, when and how does one know that HIP is the post-processing step one should use for a given application? For Lane, it all comes down to porosity:
“A well-controlled build job can minimize the tendency to introduce internal defects such as porosity in AM components to an acceptable level for some non-demanding applications. However, for use in critical applications in demanding industries such as energy, aerospace, defense and medical, where performance and safety are key, porosity must be eliminated. In the as-built condition because without HIP, the remaining porosity can lead to differences in mechanical strength (scatter of properties), either between parts from the same built plate, or in different cross sections of larger parts. A residual network of pores makes crack propagation very easy when subjected to cyclic loading in jet engines (blades) or within the human body (HIP-implants).”
To explain how HIP can generally improve productivity and product quality of critical 3D printed parts, he adds:
“The HIP process is often just one part out of the total processing route. A traditional route would include a pre-HIP stress relief treatment and post-HIP solution annealing and/or precipitation hardening carried out in a vacuum furnace. The state-of-the-art HIP equipment offers the possibility to incorporate stress relief and the solution annealing/hardening into the HIP cycle because defined heating rates with intermediate holding plateaus as well as fast cooling rates can be realized. This streamlines the AM post-process chain, increases productivity of the printers and, in the end, improve mechanical properties and the lifetime of AM components.”
The table below summarizes the benefits of HIP captured when applied to AM parts and the areas where operators should still pay attention:
Key benefits | Pay attention to: |
Removing printing defects regardless of their number
|
Residual stresses in the material introduced during the AM process may take place |
Enhancing fatigue properties
|
Due to their differences, the properties of printed metals may pose challenges during the HIP phase |
No distortion of the net shape AM parts is to be expected during HIP
|
|
A lean manufacturing route, leading to shorter production lead times | |
Reduced Environmental Impact (in the case of near-net-shape and net-shape parts)
|
Concluding thoughts
While HIPing processes are well-established and understood for processes like castings, a whole book still needs to be written to document the specifications of these processes for AM parts. While the article above provides a first introduction to HIP, it’s crucial to keep in mind that the diversity of material properties in metal 3D-printed parts continuously changes the way HIP can be applied.
Nevertheless, as per the words of Lane, HIP remains a post-processing step that significantly improves product performance while offering the potential for shorter overall printing times and reducing the final costs for AM companies.
Editor’s notes
To discuss this topic, we invited one company whose expertise in the field has been acknowledged across several industries adopting AM technologies and beyond:
Aalberts surface technologies, a global surface technology service provider. As a full-service provider of specialized heat-treating solutions, state-of-the-art HIP systems were added to the company’s existing thermal processing capabilities (vacuum heat treating) in its Nadcap facility in Greenville (S.C.) to meet the special needs of the aerospace and power generation industries. As a full-service provider under one roof, the cost avoidance benefits of logistics and material handling along with improved turn-around time over standard industry benchmarks places their customers at an advantage over their competitors. This advantage enables them to increase their cash flow through faster turn times and allows for getting products to market faster.