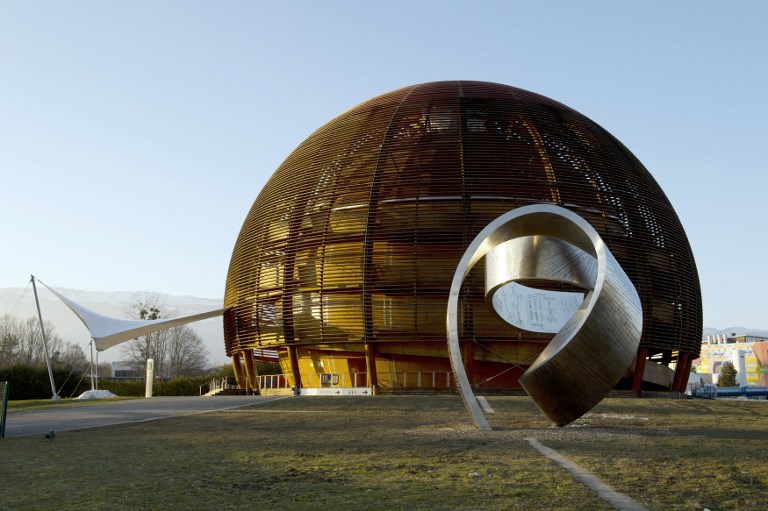
Following the recently launched depowdering system for Metal AM, Solukon is already undertaking a new adventure and this time, the company brings its expertise in CERN’s engineering department additive manufacturing workshop (The Mechanical and Materials group ).
CERN is the European Organization for Nuclear Research which integrates the Mechanical and Materials group. The latter will be using Solukon’s automated depowdering units to clean laser melted metal parts made from reactive Titanium-alloys.
According to Romain Gérard, AM engineer at The Mechanical and Materials group, powder removal remains a big issue in an additive manufacturing process, especially when it comes to Ultra-High-Vacuum. “We observed that powder residues, that are subsequently sintered during heat treatment, act like sponges by trapping gases and releasing them at a very low rate. The SFM-AT300 automated depowdering unit from Solukon ensures a high depowdering quality with a safe environment for titanium and niobium powder” explains Romain Gérard.
“The high requirements for safety and cleaning results make CERN an exemplary customer for Solukon. The combination of the reactivity of the used titanium powder and the complex internal structures of the parts make it perfectly suitable for our systems” said Andreas Hartmann, CEO and technical director at Solukon. “Through programmable rotation of the part and the build plate around one or two axes, non-fused build material is removed from complex voids and support structures”, added Dominik Schmid CEO.
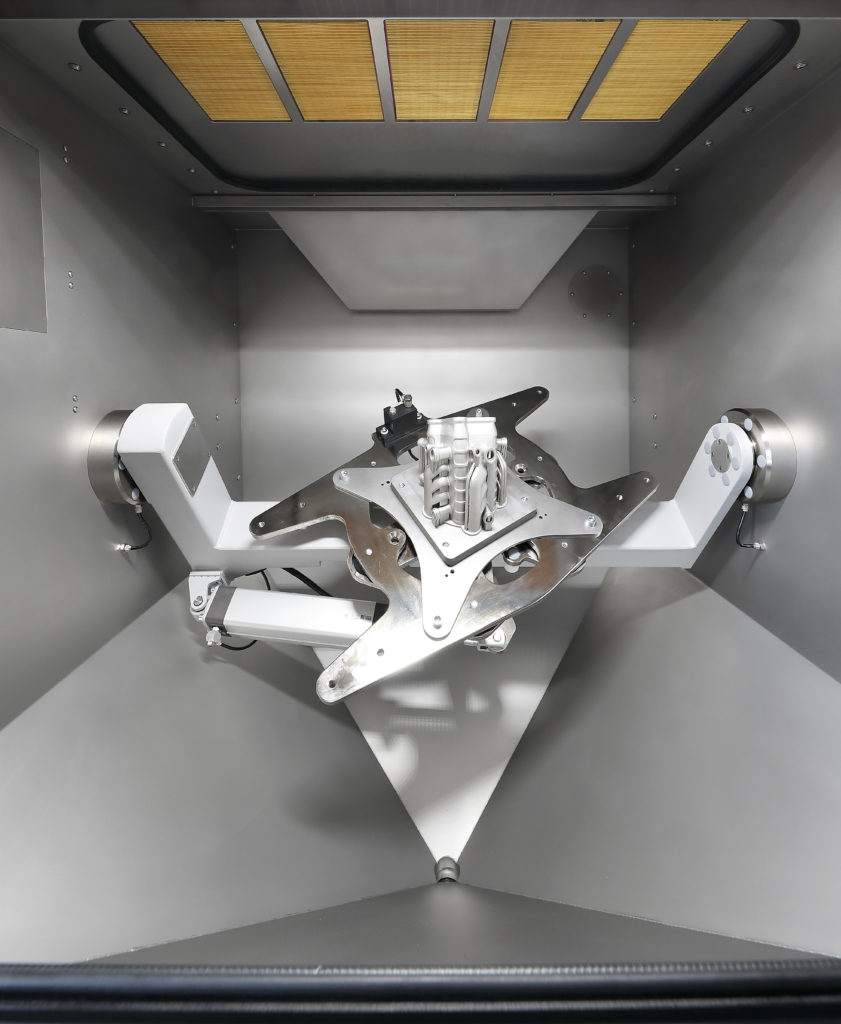
As far as Solukon automated depowdering units are concerned, some advantages include a high degree of protection from hazardous dust build-up, a fast and economical powder removal with time saving up to 90%, an inert gas infusion to prevent explosive atmosphere as well as a sustained inert material handling to avoid contamination with oxygen.
For further information about 3D Printing, follow us on our social networks and subscribe to our newsletter! Featured image via Inquirer.net
Would you like to be featured in the next issue of our digital magazine? Send us an email at contact@3dadept.com
//pagead2.googlesyndication.com/pagead/js/adsbygoogle.js
(adsbygoogle = window.adsbygoogle || []).push({});