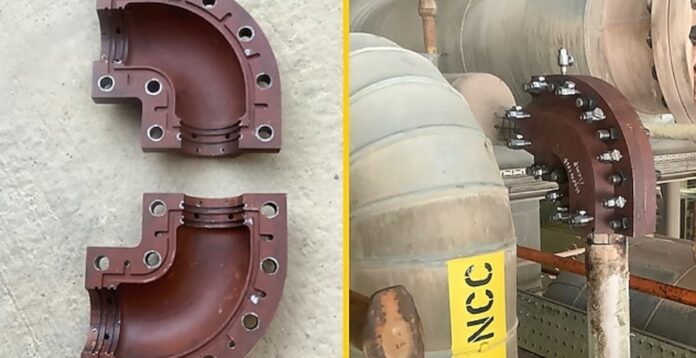
On the heels of a joint design and engineering project conducted in collaboration with GE Additive and the decision to join a consortium of companies to advance the use of 3D Printing as a repair method of underwater assets, energy company Shell achieves another milestone in its additive manufacturing journey.
The company’s AM division 3D printed and installed a leak repair clamp on its site. Also known as mechanical leak repair enclosures, clamps are used to encapsulate and restore integrity of operating pipelines against defects or wall thinning arising through erosion and corrosion mechanisms.
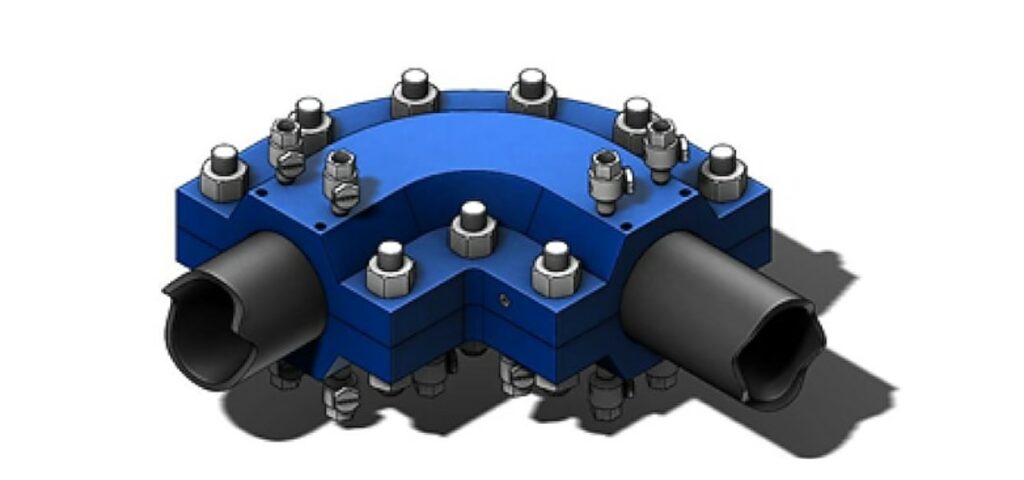
According to Shell, a simple clamp can be manufactured within 3-5 days while complex ones may take 4 weeks or more. The ability to apply such temporary repairs is critical to enable facilities to remain on-stream. The availability of essential equipment can be maximised, thereby reducing production loss and environmental emissions. Defects can occur in diverse locations given the complexity of piping systems, often triggering the need for dedicated, customised solutions. The speed of response to restore the mechanical integrity and continuous safe operation of the asset is critical, the company explains.
In this specific case, the manufacturing process required a proof of concept that was executed by Shell, TEAM, Inc. and Vallourec. Team, Inc. is an industrial services company offering an array of specialized services related to the construction, maintenance, and monitoring of pressurized piping and associated systems. Vallourec is a multinational manufacturing company that has built up extensive expertise in the production and delivery of critical parts using the WAAM technology.
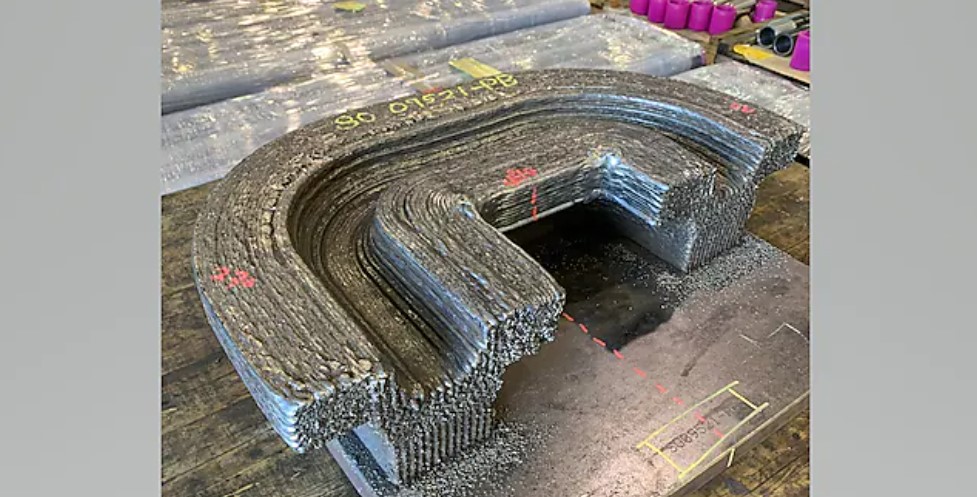
Together, the team established a technical specification and inspection test plan for the first clamp with an industrial application to be produced completely with the Wire Arc Additive Manufactured (WAAM) technique. The goal was to verify the feasibility of using a WAAM technique to produce clamps for leak repair which will meet the required quality assurance for medium-pressure steam systems. The proof of concept helped gather insights into the steps needed to improve the quality and productivity for future applications, a press communication states.
The results of the burst test at 142.4 bar (over 5 times that of the intended design pressure) met the qualification requirements of Shell for a given application.
Interestingly, in this case, due to the highest criticality category under the DNV B203 standard for Additive manufacturing of metallic parts, the overall delivery lead time of this fabrication process was longer than the one usually obtained via conventional manufacturing process. Furthermore, three sets of clamps were produced for extensive testing even though only one set was eventually installed. As it was a first of its kind demonstration project, the team focussed more on designing the clamp for a 100% success rate in inspection rather than on design optimisation. This increased lead time and costs was a design choice for the POC.
Not to mention that the project involved shipment of the parts for printing and testing at different locations and countries, which contributed to the increased lead time and costs. However, this timing and costs would be reduced if Shell installs AM equipment on sites that require such production.
Lastly, the different steps involved in procurement process as well as quality assurance and quality control account for more than 50% of the time required for the POC.
This will constitute one of the areas of focus of the AM division, moving forward. Moreover, to ensure the product quality and consistency, as well as reduce the lead time and costs for the additive manufacturing of selected clamps, Shell ambitions to streamline the qualification process and reduce the need for duplicable parts.
To do so, key areas of focus will require to create a database with all inspection and qualification test results reflecting the quality variance in WAAM parts. Accurate analysis of these data will help reduce the criticality classification of the 3D printed spare parts or the among of non-destructive testing required prior to using the parts in production.
The development of application specific qualification requirements, will allow more complex parts to be qualified based on case history and successful in-service use cases of simpler parts; and the creation a library of qualified configurations to reduce qualification efforts of same or similar products in future.
Needless to say that these are objectives that could be achieved through collaboration with interested end users who have similar needs.
Remember, you can post job opportunities in the AM Industry on 3D ADEPT Media free of charge or look for a job via our job board. Make sure to follow us on our social networks and subscribe to our weekly newsletter : Facebook, Twitter, LinkedIn & Instagram ! If you want to be featured in the next issue of our digital magazine or if you hear a story that needs to be heard, make sure you send it to contact@3dadept.com