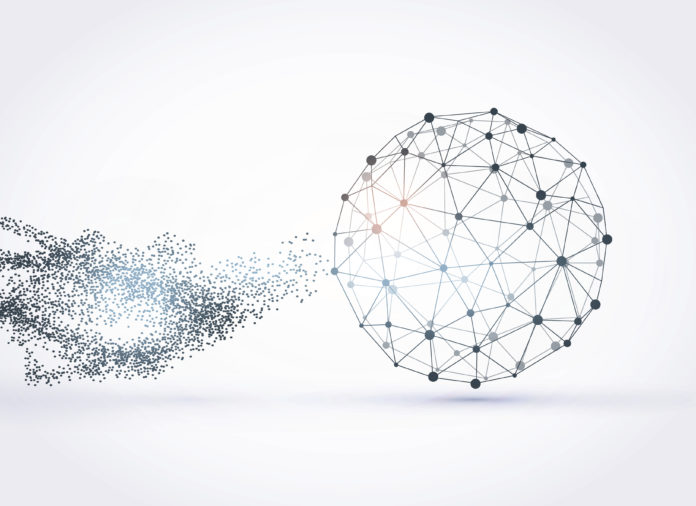
Au début de 2019, nous avons demandé aux experts du marché de la fabrication additive quelles étaient leurs prévisions pour l’année. La principale prévision pour les entreprises qui y ont répondu était de se concentrer sur l’éducation et sur les moyens de faire passer la fabrication additive à un mode de production viable.
Une autre tendance était de se concentrer sur le développement de nouveaux matériaux. Bien que nous avons remarqué des partenariats prometteurs entre les fournisseurs de matériaux et les fabricants d’imprimantes 3D, il faut noter qu’il existe toujours un déséquilibre entre l’offre et la demande sur le marché.
Néanmoins, l’année 2019 a été très excitante car elle a montré diverses stratégies de déploiement pour aider l’industrie à aller de l’avant. Les choses n’ont pas toujours été faciles, car parfois, le climat politique incertain dans certaines régions n’était pas propice aux affaires. Cependant, la plupart des entreprises ont montré des résultats optimistes par rapport à leurs objectifs tandis que d’autres ont décidé de prendre une direction différente afin d’être plus efficaces.
À la fin de l’année, nous avons contacté 21 entreprises pour savoir ce que 2019 signifiait exactement pour elles et, surtout, comment elles perçoivent le marché en 2020. Ces entreprises incluent des fabricants d’imprimantes 3D, des fournisseurs de matériaux, des sous-traitants, des bureaux de services d’impression 3D et des éditeurs de logiciels. Elles partagent leur vision ci-dessous.
Retour sur 2019 et perspectives pour 2020
Christophe Schramm, Directeur des nouvelles technologies pour l’unité business Solvay Specialty Polymers, fournisseur de matériaux.
« 2019 a été une année de déploiement de la stratégie de FA de Solvay, avec plusieurs partenariats avec des fabricants d’imprimantes, l’élargissement de notre portefeuille de produits et l’approfondissement de notre écosystème tout au long de la chaîne de valeur de FA. Cette stratégie s’aligne bien avec le passage de nombreuses industries utilisatrices finales du tapage médiatique à des projets réels. Nous nous attendons à ce que cette tendance se poursuive et s’accélère en 2020, avec d’autres nouvelles de Solvay, soutenant notre ambition de devenir le premier fournisseur de solutions de matériaux haute performance prêts pour la FA ».

Jon Donner CEO de Nanofabrica, spécialise en micro-impression 3D
« 2019 a été remplie de réalisations passionnantes à Nanofabrica. Nous avons envoyé des douzaines de pièces à des clients mondiaux, y compris des entreprises de Fortune 500. Les destinataires ont été très impressionnés par les résultats et par le niveau de précision que nous avons atteint. Plus tard dans l’année, nous avons finalisé notre machine industrielle qui offre un volume de construction impressionnant de 50x50x100mm, nous avons remporté un prix TCT pour celle-ci et nous avons signé nos premières ventes Bêta. En 2019, Gartner a publié ses prévisions pour les technologies émergentes et a déclaré que les technologies d’impression 3D à l’échelle nanométrique étaient en hausse. En 2019, nous avons pu en témoigner lors de différentes conférences et expositions à travers le monde. En 2020, nous constaterons par nous-mêmes le besoin réel de cette technologie. Le marché soumet sa demande, et nous sommes là pour y répondre ».

Phil Schultz, vice-président exécutif, Opérations, 3D Systems, fournisseur d’une gamme complète de produits et de services, notamment des imprimantes 3D, du matériel d’impression, des logiciels et des services de fabrication à la demande
« En 2019, 3D Systems a franchi plusieurs étapes clés, la plus importante étant que la production 3D n’est plus un but, mais une réalité. La dernière étude d’E&Y confirme que l’adoption de la fabrication additive s’accélère (passant de la phase de recherche et de prototypage à la production), alors que près de 75 % des entreprises ont recours à cette technologie. En tant qu’entreprise, nous continuons de placer le client au centre de tout ce que nous entreprenons.

D’ailleurs, nos clients ont joué un rôle clé dans la façon dont nous avons donné vie à la fabrication additive de production. Nous avons travaillé en étroite collaboration avec chacun d’eux, tout d’abord pour comprendre leur application, et ensuite pour déterminer où nous pourrions apporter de la valeur ajoutée à leur flux de travail. Dans de nombreux cas, les besoins de nos clients en matière de flux de production ont été le catalyseur de notre innovation, comme cela a été le cas avec le lancement de nos matériaux les plus récents. Au cours des 4 derniers mois, la majorité de nos 10 nouveaux matériaux ont été spécialement conçus pour des applications de production. D’ici fin 2019, les solutions de production de 3D Systems spécifiques aux applications produiront environ 200 millions de pièces de production d’utilisation finale – un record absolu dans l’industrie.
Tout comme l’intégration de notre technologie aux flux de travail de nos clients continuera de s’accélérer en 2020, nous verrons augmenter le nombre de fabricants capables d’imprimer en 3D des pièces d’utilisation finale en plastique et en métal pour des applications dans les secteurs de la santé, de l’aérospatiale, de l’automobile, de la dentisterie et des biens de consommation. L’impression 3D transformera la façon dont les entreprises créent des produits inédits et plus performants, en leur apportant des avantages qui leur permettront d’avoir une confortable longueur d’avance sur leurs concurrents. »
Stephan Kühr, CEO, 3YOURMIND, Editeur de logiciels destinés à la fabrication additive.
« En 2019, 3YOURMIND a obtenu son premier client axé principalement sur la fabrication additive en série : le groupe Erpro. Nous avons vu nos autres clients valider également de nombreuses pièces de FA de petites et grandes séries qui entreront en production en 2020.

Nous avons été heureux de pouvoir le faire grâce à notre logiciel d’identification de pièces, de commande et de gestion de production.
En élargissant nos fonctionnalités pour gérer ces nouveaux cas d’utilisation, nous nous rapprochons beaucoup de l’automatisation complète. Le travail que nous avons commencé avec umati en 2019 pour établir la connectivité des machines est également une étape importante vers cet objectif d’un flux de travail de FA entièrement numérique.
Nous savons que nos clients mettront beaucoup plus de pièces en production en 2020 et 2021 – nous allons donc nous concentrer encore plus sur la numérisation et le suivi des processus de production et de documentation dans l’Agile MES. Avec notre PLM Agile, nous aiderons nos clients à identifier beaucoup plus de cas d’utilisation positifs et à les stocker dans un inventaire numérique, afin qu’ils soient prêts à être commandés à la demande. »
Meddah Hadjar, CEO de SLM Solutions, fabricant d’imprimantes 3D métal
« SLM Solutions se penche sur 2019 et la décrit comme une année pendant laquelle les compteurs ont été remis à zéro. Nous avons annoncé que notre commande a augmenté de 21 % par rapport à l’année précédente et a doublé au quatrième trimestre.

La confiance que les clients et les partenaires accordent à nos produits et à notre entreprise est impressionnante. Cela se traduit non seulement par la croissance des commandes, mais aussi par de nombreux projets et partenariats réussis tout au long de l’année – que ce soit la lettre d’intention récemment annoncée d’étendre la coopération pour le développement de la prochaine génération de machines avec Divergent3D, l’annonce de Honeywell sur le développement de paramètres de 90 microns, la collaboration avec Bugatti pour la réalisation de composants fonctionnels ou l’utilisation de la technologie Selective Laser dans un projet de course de l’Institut danois de technologie et CeramicSpeed. SLM Solutions a présenté ces projets et bien d’autres projets passionnants lors du salon leader de la fabrication additive, Formnext, qui s’est avéré être un autre temps fort de l’année 2019. Le grand nombre de visiteurs professionnels a montré un grand intérêt pour la technologie SLM® Multi-laser, et la participation au salon a été couronnée par la signature de plusieurs contrats de vente et de partenariats.
En 2020, nous allons continuer à progresser sur le marché. Nous travaillerons avec nos clients pour augmenter l’adoption de la FA et SLM Solutions est bien positionnée pour être le leader dans la fusion laser sur lit de poudre. En tant que pionniers de la fusion par lit de poudre multi-laser, notre expertise en matière de machines productives et fiables continuera à fournir des solutions de production pour toute une série d’utilisateurs. En regardant vers l’avenir, nous travaillerons à faire avancer les technologies mises en avant sur notre stand pour les mettre à la disposition des clients en tant que solutions industrialisées qui donneront une perspective entièrement nouvelle au concept de productivité dans la fabrication additive métallique. SLM Solutions se dirige vers 2020 en se concentrant sur l’industrialisation de ses machines, la productivité et les paramètres des processus. »
Bruno Bourguet, Directeur Général, PostProcess Technologies International, spécialiste des solutions de post-traitement
Chez PostProcess, en 2019, nous avons vu les volumes de nos clients augmenter de manière significative, en particulier dans les entreprises qui comptent sur l’innovation rapide pour stimuler leur croissance, comme celles qui tirent parti de l’impression 3D pour le prototypage rapide. Nous avons également noté un intérêt accru de la part d’un plus grand nombre d’entreprises qui envisagent la fabrication additive pour la production de faibles volumes.

Avec ces tendances à l’augmentation des volumes, 2020 apportera un besoin accéléré de solutions évolutives pour l’étape de post-impression. L’approche traditionnelle consistant à compléter la post-impression par du travail manuel et des solutions mécaniques traditionnelles ne sera plus une option pratique pour les applications à l’échelle de la production qui cherchent à connecter le fil numérique de bout en bout. De plus, en 2019, le marché a continué à élargir son offre de matériaux et à permettre des géométries plus complexes. Cette évolution est également intéressante dans la mesure où PostProcess élargit son offre en 2020 pour améliorer ses solutions entièrement automatisées et pilotées par données afin d’aider les utilisateurs finaux à obtenir un débit accru et une meilleure cohérence de leurs pièces finales. »
Jack Cheng, DGM, Chef de ventes globales et du marketing chez Farsoon Technologies, Fabricant d’imprimantes 3D industrielles
« Avec notre engagement à offrir des systèmes de fabrication additive réellement ouverts et performants aux utilisateurs industriels de la FA, Farsoon a réalisé une croissance significative de ses ventes de machines en 2019.

Farsoon a pu étendre sa présence dans une variété d’industries dont les applications nécessitaient l’utilisation de la FA, notamment l’aérospatiale, l’automobile et les industries de prototypage. Grâce à une innovation technologique continue, Farsoon est en mesure de proposer au marché des systèmes différenciés, notamment le HT1001P, le FS421M, la Flight Technology et le dernier FS301M.
En 2020, Farsoon se concentrera sur l’innovation additive et l’industrialisation — en travaillant étroitement avec les clients industriels mondiaux pour partager et développer notre savoir-faire en matière de matériaux, de technologie additive et d’applications, avec pour objectif de transformer l’innovation de Farsoon en une véritable réalité de fabrication. »
Fernando Hernandez, Directeur Général EMEA at XYZprinting, fabricant d’imprimantes 3D
« 2019 a certainement été une année mémorable pour XYZprinting. C’est l’année où nous avons lancé notre gamme d’appareils industriels, consolidant l’offre dans des technologies telles que SLS, Binder JEtting et SLA/DLP. Mais nous ne nous sommes pas arrêtés là, nous avons également vu l’annonce de plusieurs nouvelles imprimantes industrielles qui sont parmi nos produits les plus innovants à ce jour, comme la PartPro120 xP qui offre des vitesses jusqu’à 75 fois supérieures aux imprimantes 3D conventionnelles sans sacrifier la qualité ou la résolution d’impression, grâce à la technologie Ultra-Fast Film de XYZprinting.

Avec presque toutes les solutions verticales et tous les services à offrir, nous avons continué à nous distinguer en tant que leader du marché de l’impression de bureau, de détail, d’éducation et d’articles de luxe, et en nous appuyant sur notre présence dans l’impression professionnelle également. Nous avons l’intention de continuer à nous distinguer dans les secteurs de l’automobile, de la médecine et de l’architecture.
A l’avenir, l’impression 3D sera favorisée par le volume et la qualité des nouveaux matériaux, ce à quoi XYZprinting contribuera en concluant ses propres partenariats avec des entreprises tierces très appréciées. Un autre thème clé que j’anticipe pour 2020 sera un changement de perception sur la façon dont l’impression 3D peut en fait compléter la fabrication traditionnelle au lieu d’être en concurrence avec elle. Enfin, en 2020, l’industrie de l’impression 3D tirera parti des derniers logiciels pour améliorer les chaînes d’approvisionnement et obtenir des résultats de qualité supérieure. Une chose est certaine, les prévisions pour 2020 sont brillantes ».
John Dulchinos, VP, Fabrication Digitale chez Jabil Additive, société de fabrication de services
« 2019 a été une année de croissance continue pour Jabil Additive, car l’organisation a profité de sa riche expérience en matière de science des matériaux pour accélérer le développement de matériaux sur mesure et faire progresser l’ensemble du marché de la fabrication additive.

Jabil prévoit de poursuivre sur sa lancée en 2020, en particulier la croissance des solutions intégrées comprenant des matériaux élaborés, des processus rigoureux et des machines d’impression 3D certifiées pour soutenir les applications des industries hautement réglementées, telles que l’aérospatiale, l’automobile, l’industrie et la santé, ainsi que celles nécessitant des géométries optimisées ou des nomenclatures consolidées (BOM).
Jabil prévoit également une augmentation des solutions de fabrication additive certifiées basées sur des systèmes de gestion de la qualité robustes qui accélèrent l’utilisation des réseaux de production distribués pour répondre aux exigences strictes de qualité et de performance des pièces. De plus, Jabil anticipe un afflux de nouveaux matériaux aux propriétés uniques pour permettre de nouvelles applications tout en réduisant les délais et les coûts de mise sur le marché de pièces de très haute qualité. A cette fin, Jabil continuera à évaluer, qualifier et valider un mélange diversifié de matériaux techniques pour une utilisation avec son réseau interconnecté de fabrication additive d’imprimantes 3D de classe mondiale et de processus de qualité pour fournir un chemin plus rapide du prototypage à la production à grande échelle de produits de rupture. »
Lukas Pawelczyk, Chef de ventes Freeformer, Arburg, fabricant de machines de moulage par injection et d’imprimantes 3D
« La fabrication additive va continuer à prendre de l’ampleur dans le domaine de la technologie médicale, comme le démontrent plusieurs clients renommés d’Arburg Plastic Freeforming (APF) en 2019. Ils utilisent désormais notre système ouvert pour traiter des matériaux originaux biocompatibles, résorbables, stérilisables et approuvés par la FDA. Je pense qu’en 2020, nous verrons des implants produits avec le Freeformer dans des environnements de salle blanche et utilisés dans le corps humain.
Pour nous, en tant que fabricant de machines, l’assurance qualité et la surveillance des processus sont également très importantes dans le processus de FA.

Grâce au système Freeformer et à notre vaste savoir-faire dans le domaine de la transformation des matières plastiques, nous sommes en mesure d’automatiser le processus de fabrication additive et d’enregistrer tous les paramètres de construction pertinents via des interfaces OPC/UA. Il est de plus en plus important de garantir des standards de qualité élevés lors de la fabrication de pièces fonctionnelles par fabrication additive et de documenter ce processus de manière fiable.
Notre objectif principal en 2020 ?
Penser additif ! En tant que constructeur de machines, nous devons développer avec nos clients les domaines d’application de la fabrication additive et exploiter les nouveaux degrés de liberté dans ce domaine. Nous nous concentrerons également sur des thèmes tels que la préservation des ressources et la durabilité, tant ici que dans le secteur du moulage par injection. »
Fedor Antonov, CEO chez Anisoprint, fabricant d’imprimantes 3D
« Pour Anisoprint, 2019 était l’année de la conquête de nouveaux territoires : [ notre technologie d’impression 3D que nous appelons] » anisoprinting » est maintenant distribuée dans plus de la moitié de l’Europe avec notre produit d’entrée de gamme – l’imprimante 3D de bureau à fibre continue Composer.

Nous nous tournons également vers l’avenir de la technologie : il y aura encore plus de possibilités de remplacer les métaux ou les composites non optimaux avec notre nouvelle ProM IS 500 – une imprimante 3D industrielle spécialement conçue pour l’impression de thermoplastiques à haute température avec renforcement par fibres continues.
En 2020, l’industrie de la FA continuera à rechercher de meilleurs matériaux, approches et applications pour rendre les inventions de fabrication additive compétitives par rapport aux technologies traditionnelles. Anisoprint, qui intègre une équipe de chercheurs et d’ingénieurs ayant une grande expérience des composites, contribuera également à ce niveau : nous continuerons à développer l’impression 3D à fibre continue qui tend à devenir populaire en raison de ses avantages. Certaines des plus grandes entreprises de la FA l’ont déjà compris, et nous attendons d’autres développements dans les années à venir. »
Keyvan Karimi, Fondateur & CEO, AMFG, fournisseur de logiciels d’automatisation des flux de travail pour la fabrication additive
« 2019 a été une année formidable pour AMFG, car nous avons constaté que de plus en plus de sociétés reconnaissent le rôle du logiciel MES dans l’établissement d’un flux de fabrication additive évolutif, automatisé et connecté. En 2019, nous avons considérablement augmenté notre base de clients dans des secteurs tels que l’automobile, les biens de consommation et les biens industriels, et nous avons ouvert un bureau en Allemagne dans le cadre de l’expansion de notre société.

Nous sommes donc extrêmement optimistes quant à la croissance de l’industrie en 2020. Cette année, nous prévoyons que le marché de la FA poursuivra son passage du prototypage rapide à la production en série, et que cette technologie permettra de nouvelles applications innovantes pour l’utilisation finale.
En outre, les logiciels MES joueront un rôle encore plus important en 2020, car de plus en plus d’entreprises investissent dans l’impression 3D et cherchent des moyens d’optimiser, d’automatiser et d’étendre leurs activités.
Cela signifie qu’AMFG continuera à développer des solutions visant à permettre aux sociétés de le faire. Cela inclut des initiatives telles que la connectivité des machines, sur laquelle nous avons commencé à nous pencher en annonçant notre partenariat avec EOS en novembre dernier. Nous allons également étendre les capacités de nos solutions de gestion et d’ordonnancement de la production et permettre une plus grande automatisation du processus de FA.
Grâce à ces initiatives, nous voulons faire de la production en série avec la FA une réalité. »
Filemon Schoffer, Co-fondateur et CCO de 3D Hubs, plateforme de fabrication en ligne
« Nous avons constaté un réel changement dans les commandes d’impression 3D en 2019. De plus en plus de petites et moyennes entreprises d’ingénierie profitent de la vitesse de prototypage et de la complexité géométrique que l’impression 3D peut offrir. Cela a eu un impact significatif sur le taux d’adoption de l’impression 3D dans le processus de développement de produits (par exemple, la vitesse et le nombre d’itérations), ainsi que dans les applications haut de gamme, où les avantages des pièces complexes imprimées en 3D l’emportent sur leur coût (par exemple, une performance inégalée en termes de rapport résistance/poids dans l’aérospatiale).

Grâce à l’accès à une capacité d’impression 3D à la demande pratiquement illimitée, ainsi qu’à un large éventail de technologies, ces entreprises relativement petites sont devenues compétitives à l’échelle mondiale en matière de développement de matériel. Nous prévoyons que le taux d’adoption de l’impression 3D continuera de s’accélérer au cours de l’année 2020, à mesure que de plus en plus d’entreprises saisiront son énorme potentiel.
Chez 3D Hubs, nous nous préparons à soutenir cette demande croissante d’impression 3D en ajoutant des délais de production toujours plus courts, plus d’options de matériaux et d’autres services de fabrication, notamment l’usinage CNC, le moulage par injection et la fabrication de tôles. Plus vite les ingénieurs peuvent recevoir leurs prototypes et leurs pièces finales, plus vite ils peuvent itérer et mettre leurs produits sur le marché. L’impression 3D continuera à jouer un rôle essentiel dans l’accélération de ce processus. »
Andreas Hartmann, Co-fondateur & CEO/CTO de Solukon, spécialiste en solutions de post-traitement de bout en bout pour la fabrication additive
« 2019 a été une année très réussie pour Solukon. Nous avons installé de nombreux systèmes et nous avons reçu un excellent retour d’informations de la part de nos clients. Par exemple, Materials Solutions, en tant qu’entreprise très avant-gardiste, a installé sa sixième grande unité de dépoudrage et nous sommes très fiers de fournir des entreprises aérospatiales de pointe aux États-Unis et en Europe.

Nous avons également pris des mesures importantes dans la croissance de notre entreprise et avons co-fondé AMP+ en tant que réseau spécialisé dans les solutions de poudrage. Et pour couronner le tout, Siemens et nous avons remporté, le prix de TCT dédié au post-traitement.
Nous sommes heureux que l’industrie de la FA reconnaisse de plus en plus la nécessité et la valeur de nos solutions de dépouillement hautement automatisées pour assurer une production sûre et efficace.
En 2019, l’industrie aérospatiale et énergétique a de nouveau poussé la FA vers l’avant avec un nouveau design léger et thermodynamique. Ici en particulier, nous avons pu marquer des points avec nos nouveaux algorithmes de dépoudrage pour les géométries complexes.
Nous voyons également un grand avenir pour les pièces de grande hauteur comme les moteurs de fusée et nous proposerons bientôt une solution pour le dépouillement de pièces de 1 mètre.
En raison des expériences positives de la coopération avec Siemens, nous nous associons à nouveau avec d’autres utilisateurs de la FA hautement spécialisés afin d’accroître notre expérience et de faire progresser nos technologies de manière conséquente ».
Guillaume Boisot, Head of Business Development, e-Xstream engineering, éditeur de logiciels
« En 2019, l’industrie de la fabrication additive est en pleine expansion et a atteint un niveau de maturité où la simulation joue un rôle central. L’industrie n’étudie plus seulement l’optimisation de la topologie et les géométries de fantaisie, mais se pose maintenant les bonnes questions : peut-on imprimer ? comment peut-on être léger et solide ? puis-je imprimer correctement du premier coup ? comment puis-je gérer toutes mes données relatives aux matériaux, aux constructions, à la microstructure de la poudre, …

Ce sont des questions typiques auxquelles nous avons répondu en 2019 et nous nous attendons à ce qu’elles augmentent en 2020. Nous prévoyons que notre écosystème de fabrication additive continuera à croître en 2020 : [nous travaillerons avec un plus grand nombre de fournisseurs de matériaux, d’OEMs, de bureaux d’impression et, bien sûr, d’utilisateurs finaux, et les accompagnerons dans l’industrialisation de la FA »
Gauthier Wahu, Directeur Général et Technique, CoreTechnologie France, éditeur de logiciels
« 2019 a marqué le lancement de notre logiciel 4D_Additive. Nos premiers clients, des industriels de l’automobile, de l’aéronautique et du médical sont conquis et les perspectives de commercialisation pour 2020 sont excellentes.

Notre atelier Texture est plébiscité par les équipes Design et Innovation pour son ergonomie et sa qualité d’impression.
En collaboration avec nos clients, nos développements 2020 vont se concentrer sur des innovations de productivité et de design.
Cette année, nos équipes vont renforcer la technologie de l’atelier Textures en intégrant la gestion de la couleur et prévoient l’ajout de la fonction « Batch Nesting » à 3D PartFinder. 4D_Additive sera aussi optimisé pour la technologie SLM.
Des couleurs imprimées et sublimées pour en mettre plein la vue
4D_Additive reportera les couleurs issues de la texture sur le modèle à imprimer pour un rendu plus cohérent et plus esthétique. Techniquement, le format de sortie .OBJ permettra de retranscrire à la fois les déformations et les couleurs. »
Tiago Brito e Faro, Chef du département d’ingénierie à Adira, fabricant de machines pour le secteur de la métallurgie
“La sortie de la grande imprimante métallique d’Adira est prévue pour la fin de l’année 2020. Tout en cherchant activement à accroître notre réseau de bêta-testeurs, nous consolidons également les relations de partenariat stratégique que nous avons déjà mises en place.
Au cours de l’année à venir, nous travaillerons sur quelques points qui nécessitent encore des ajustements, principalement en ce qui concerne l’utilisation de l’équipement. Ces ajustements permettront d’améliorer notre produit final UX et UI pour tous nos bêta testeurs / clients. »

Alessio Lorusso, Fondateur & CEO de Roboze, fabricant d’imprimantes 3D
« 2019 » signifiait pour Roboze contribuer à l’innovation continue sur le marché de la technologie d’impression 3D. Toutes les innovations que Roboze a présentées en 2019 répondent aux besoins de toutes ces réalités entrepreneuriales qui visent à augmenter leur productivité grâce aux super polymères à haute température et aux matériaux composites pour la production de pièces finies avec la plus grande précision.

Nous sommes en plein milieu d’une quatrième révolution industrielle, où la fabrication additive joue un rôle clé. L’industrie évolue rapidement, et Roboze analyse constamment les changements du marché mondial afin de répondre aux besoins réels des clients finaux. Un des principaux objectifs de Roboze sera de contribuer au développement de ces usines intelligentes capables de bénéficier des avantages technologiques résultant de l’intégration des machines, des processus de production et des produits finaux.
Nous sommes conscients que les fabricants vont de plus en plus utiliser l’impression 3D parallèlement à l’usinage CNC, un autre indicateur fort de l’importance de la fabrication additive dans les processus de production.
L’Europe, les États-Unis et l’Asie sont certainement les régions qui connaissent la plus forte croissance et où, aujourd’hui, la fabrication par adjuvants se développe au niveau mondial. C’est là que nous concentrons nos efforts pour augmenter la croissance des activités de Roboze, en particulier aux Etats-Unis. En 2020, notre objectif principal sera de faire des solutions d’impression 3D de Roboze un acteur clé dans le progrès de l’Industrie 4.0 en offrant des matériaux de haute performance adaptés aux applications de Remplacement de Métal et à la production de prototypes fonctionnels et de pièces de finition au niveau mondial. »
Joseph Crabtree, Fondateur & CEO, Additive Manufacturing Technologies (AMT), spécialiste en solutions de post-traitement de bout en bout pour la fabrication additive
« 2019 a été une année charnière pour Additive Manufacturing Technologies (AMT) Ltd.

Fondée en 2017, nous sommes maintenant entièrement commercialisés, et aujourd’hui il y a un nombre croissant d’OEMs dans le monde entier qui utilisent nos solutions de post-traitement AM sûres, durables et entièrement automatisées. Le post-traitement est l’un des principaux domaines d’intérêt des entreprises qui cherchent à intégrer la fabrication additive dans des cycles de production rapides et rentables, et la demande porte sur des solutions entièrement automatisées qui permettent de réduire considérablement le coût par pièce. Notre processus améliore les caractéristiques des matériaux ainsi que les surfaces entièrement lisses, et s’inscrit dans le cadre de notre volonté générale de mettre en place des systèmes de fabrication numérique entièrement connectés, personnalisés et de bout en bout. C’est le domaine dans lequel AMT opère afin d’apporter des solutions industrielles pratiques aux équipementiers qui utilisent la FA comme technologie de production, et nous continuerons à nous y intéresser en 2020. »
Kristof Sehmke, Responsible Communication, Materialise, Editeur de logiciels & Service d’impression 3D de bureau
« En 2019, Materialise a collaboré avec ses partenaires pour faire progresser la technologie de FA sur de nombreux fronts cruciaux : des machines plus rapides, de nouveaux matériaux et davantage d’options de finition.

Aujourd’hui, nous voyons toutes ces avancées s’unir pour créer un climat d’innovation passionnant qui suscitera des applications entièrement nouvelles qui étaient impensables ou inatteignables auparavant.
Alors que nous développons de nouveaux produits et technologies pour aider nos clients à créer des applications significatives, la durabilité doit devenir une priorité. Déjà, la FA fournit aux entreprises un instrument pour fabriquer de manière plus durable – tant sur le plan social qu’environnemental. Cependant, cela ne suffit pas. Collectivement, nous devons développer des initiatives pour réduire la consommation d’énergie, augmenter l’utilisation de poudre recyclée et créer des lieux de travail d’avenir. Ainsi, pour aller de l’avant, la question n’est pas : la FA est-elle une technologie de fabrication plus durable ? La question devient : que pouvons-nous faire pour rendre la FA plus durable ? »
Guillaume Feliksdal, Co-fondateur de FELIXprinters, Fabricant d’imprimantes 3D
« 2019 a été une année charnière pour FELIXprinters, qui s’est imposée comme un acteur clé dans le domaine de la fabrication additive industrielle, en offrant des plateformes de FA rentables mais très précises pour les applications de prototypage et de production. En 2019, nous avons ajouté à notre portefeuille deux machines à plus grande surface de construction, les Pro L et Pro XL, qui sont maintenant vendues dans divers secteurs de l’industrie où la demande est pour des solutions de FA faciles à utiliser, précises, répétables et sensibles au prix. La société a également la capacité de personnaliser les solutions en fonction des applications spécifiques des clients, ce qui est unique dans le secteur industriel à faible coût du marché de la FA.

En 2020, nous continuerons à positionner nos solutions de FA industrielle et nous ferons également la promotion de notre nouvelle machine FELIX BIO, qui fait des merveilles dans le domaine très dynamique de l’impression 3D et des applications biomédicales. »
Cet article a été premièrement publié dans le numéro de Janvier-Février de 3D ADEPT Mag.
Image de Une: ccam-va.com – N’oubliez pas que vous pouvez poster gratuitement les offres d’emploi de l’industrie de la FA sur 3D ADEPT Media ou rechercher un emploi via notre tableau d’offres d’emploi. N’hésitez pas à nous suivre sur nos réseaux sociaux et à vous inscrire à notre newsletter hebdomadaire : Facebook, Twitter, LinkedIn & Instagram ! Si vous avez une innovation à partager pour le prochain numéro de notre magazine numérique ou si vous avez un article à faire co