Une fois par an, nous nous asseyons pour évaluer certaines des informations clés que nous avons recueillies lors de nos conversations avec des équipementiers utilisant la technologie de FA et avec des utilisateurs (potentiels) de cette technologie lors des salons professionnels que nous avons visités. Cela nous permet de déterminer les problèmes ou les solutions qui sont communs aux différents secteurs. L’année dernière, nous avons appris que la nécessité de qualifier et de certifier les pièces imprimées en 3D reste un obstacle à une utilisation plus étendue de la FA sur toutes les plates-formes. À vrai dire, la conversation sur la « qualification » et la « certification » n’est pas nouvelle chez 3D Adept Media, mais comme cette technologie entre dans une phase de maturation, il est nécessaire de documenter et de caractériser les efforts de qualification, (pour tenter) de fournir un cadre qui pourrait vraiment aider les industries.
Dans cette optique, ce dossier a pour ambition d’aider les industriels à comprendre/évaluer :
- Les approches de la qualification des pièces
- Les outils qui peuvent être utilisés dans la qualification des pièces
- S’il est possible d’exposer des considérations spécifiques pour la qualification dans des industries telles que la défense, l’automobile et l’aérospatiale.
Nous comprenons qu’il est difficile de parler de qualification sans mentionner la certification. Toutefois, dans cet article, nous nous concentrons sur la qualification des pièces imprimées en 3D.
Si je devais choisir une façon de vous expliquer ce qu’est la qualification des pièces, je reprendrais les mots de John Barnes : la qualification est atteinte lorsqu’ « un composant répond à l’intention de la conception ». Pour garantir l’intégrité d’une application, le processus de qualification implique un ensemble d’exigences liées aux pièces elles-mêmes, aux machines, aux matériaux, aux processus et au personnel. Comme l’explique Chuck Nostedt, ingénieur qualité de Jabil pour la fabrication additive, le défi consiste à comprendre une multitude d’exigences du client ou de l’utilisateur final et la manière dont elles sont liées à la combinaison matériau-machine.
Si des lignes directrices sont déjà en place pour les pièces fabriquées à l’aide de procédés conventionnels, il convient de noter que les organismes de réglementation et de normalisation, tels que SAE et ASTM, travaillent régulièrement sur les spécifications des matériaux et des procédés qui pourraient contribuer à la qualification et à la certification des pièces fabriquées par FA. Il n’est pas surprenant que ce manque de clarté sur ce qui constitue la qualification avec la FA soit à l’origine des difficultés rencontrées tout au long de la chaîne de valeur de la fabrication.
I – Approches à la qualification des pièces imprimées 3D
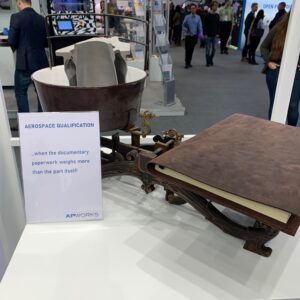
Je voudrais attirer votre attention sur un point : la qualification est un défi auquel sont confrontés aussi bien les utilisateurs expérimentés que les débutants dans l’industrie de la FA. Les premiers ont juste eu la chance de commettre les erreurs que les seconds voudraient éviter. Cela dit, la qualification peut se faire de plusieurs manières.
Pour Nostedt, l’approche de la qualification des pièces peut suivre quatre étapes : la sélection des matériaux/équipements, la qualification des équipements, la validation des processus et la production des pièces.
Cela signifie que l’équipe de FA doit être en mesure de « choisir une combinaison optimale matériau/plateforme d’impression 3D en fonction des exigences du client » (sélection du matériau/équipement) et de « s’assurer que toutes les imprimantes 3D et l’équipement connexe comprennent un équipement de test qui fonctionne comme prévu avant de passer à l’étape suivante de la validation du processus » (qualification de l’équipement).
La validation du processus vise à « confirmer que les pièces peuvent être produites avec les niveaux de répétabilité souhaités et de manière fiable pour répondre à toutes les exigences (mécaniques, visuelles et dimensionnelles). Cela comprend toutes les étapes des processus d’impression 3D et des processus post-impression 3D (par exemple, l’enlèvement de la poudre, le nettoyage, l’enlèvement du support, le traitement thermique, la finition de la surface, l’usinage des pièces à la dimension voulue, l’emballage, etc :
– Pour que la validation des procédés puisse commencer, l’utilisateur doit comprendre quels sont les paramètres critiques de chaque procédé, ce qu’on appelle parfois la caractérisation du procédé. Les plans d’expériences (DOE) peuvent être utilisés pour déterminer les paramètres critiques du procédé. Il peut également s’agir d’études sur le recyclage des poudres afin de déterminer la fréquence à laquelle la poudre peut être recyclée ainsi que la quantité de matière vierge pouvant être mélangée à la matière récupérée.
– La validation du processus proprement dit utilise les paramètres critiques du processus établis lors de la caractérisation du processus pour prouver que les pièces peuvent être fabriquées de manière répétée et fiable à l’aide de ces paramètres.
– Pour prouver que les pièces répondent à toutes les exigences, il faut procéder à des essais, qui peuvent comprendre des tests mécaniques, visuels et dimensionnels. L’utilisateur doit savoir si l’essai est destructif et nécessite le sacrifice d’une pièce ou si un coupon d’essai peut être utilisé à la place de la pièce. La complexité et le volume des pièces déterminent la stratégie d’essai. Par exemple, les méthodes de contrôle dimensionnel, qui dépendent de la pièce, détermineront si la pièce peut être mesurée à la main à l’aide d’un pied à coulisse, d’une jauge de type « go/no go », d’une machine à mesurer tridimensionnelle (MMT) ou d’un tomodensitomètre (CT), etc.
– La dernière étape – la production de pièces – intervient une fois la validation du processus achevée. Selon les termes de Nostedt, elle permet de « s’assurer que le produit peut être fabriqué en continu et qu’il répond toujours à toutes les exigences ». Cela peut inclure, sans s’y limiter, la surveillance des paramètres du processus (puissance du laser, capteurs de température, capteurs d’oxygène, etc.) et les essais du produit (mécaniques, visuels et dimensionnels). Les essais de produits en cours de production sont généralement effectués en fonction de l’importance des exigences de qualité établies par le client ».
Cette approche comprend des étapes (et probablement des sous-étapes) que beaucoup utilisent ou utiliseraient, mais probablement pas dans le même ordre.
En outre, il ne faut pas oublier que la FA est un processus holistique par nature. C’est pourquoi il convient de se poser d’abord quelques questions dont les réponses peuvent aider à définir le cadre qui répond le mieux aux besoins de chacun.
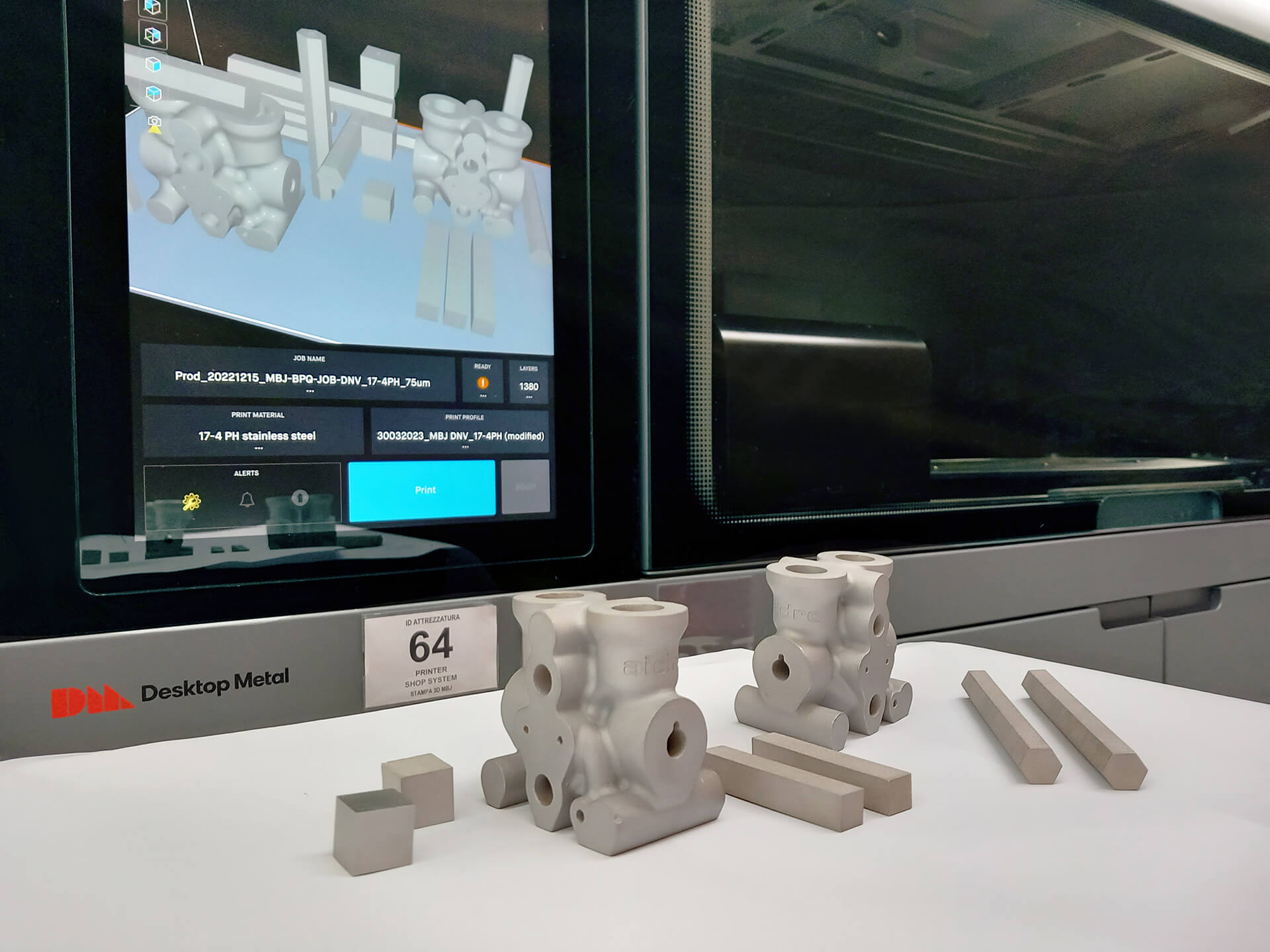
Pour le président de The Barnes Global Advisors, ces questions sont les suivantes : « S’agit-il d’une nouvelle pièce ou d’un concept de système ? ou S’agit-il d’une pièce existante et d’un système existant ? Pour Barnes, le cadre idéal de qualification devrait être commun à toutes les pièces techniques et englober la certification et la qualification. Rappelez-vous, je vous ai dit au début qu’il était difficile de parler de qualification sans mentionner la certification.
Ainsi, lorsqu’il s’agit d’une pièce existante sur un ancien système, « c’est une bénédiction et une malédiction », sourit Barnes. « La bonne nouvelle, c’est qu’il y a des exigences. La mauvaise nouvelle, c’est qu’elles ont été satisfaites par un processus de fabrication différent. » Dans cette optique, Barnes propose un processus de qualification des pièces en trois étapes :
- La première étape consiste à définir vos exigences et l’environnement dans lequel vous travaillez.
- Idéalement, le rêve de chacun est de se trouver au « stade du nouveau concept », où on envisage la FA de manière plus holistique, de sorte qu’il ne s’agisse pas seulement d’une pièce et d’un système. Il ne s’agit pas seulement d’une pièce ou d’un système, mais de la manière d’améliorer le système dans son ensemble. De cette manière, les exigences sont un peu moins connues, mais vous passez par les processus habituels définis comme des exigences.
- La deuxième étape consiste à disposer d’un processus de fabrication reproductible et fiable
- Prenant des exemples de leur fonctionnement, Barnes explique qu’à ce niveau, elles indiquent exactement comment fabriquer la pièce. L’idée est de pouvoir utiliser les spécifications des normes existantes et de démontrer qu’on peut atteindre les performances de la pièce.
- La troisième étape consiste à prouver que vous l’avez fait. « C’est la partie validation», commente Barnes. C’est exactement là qu’intervient la certification.
Votre objectif, quelle que soit l’approche que vous utilisez, doit rester le même : atténuer ou prévenir les risques et garantir les mêmes niveaux de fidélité que ceux observés dans les processus de fabrication conventionnels tels que le moulage, le forgeage et l’usinage.
II – Les outils pouvant être utilisés pour la qualification des pièces
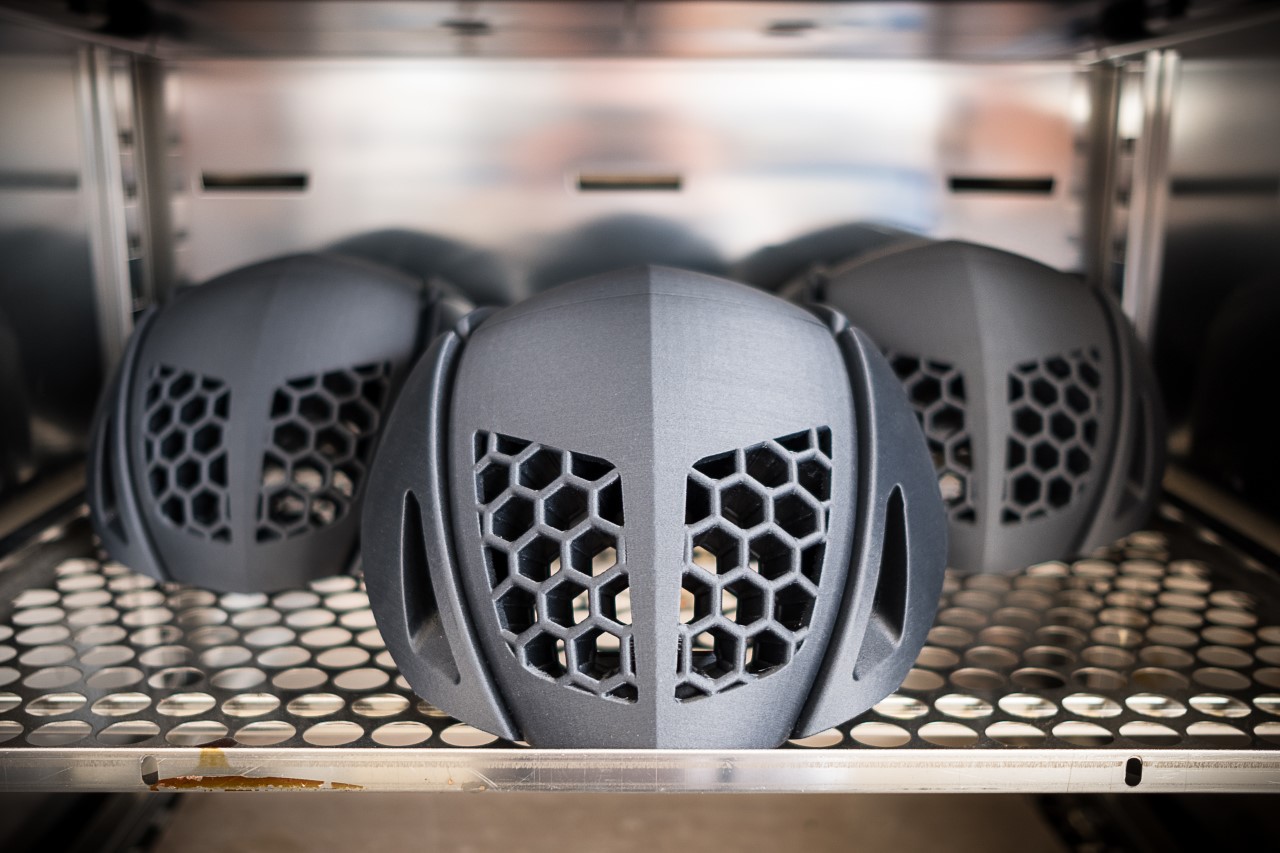
Il existe une liste non exhaustive d’outils ou de dispositifs qui peuvent être utilisés pour qualifier les pièces. Certains d’entre eux sont souvent utilisés de manière interchangeable pour l’étape de certification. L’ingénieur qualité de Jabil explique que les essais mécaniques et l’inspection dimensionnelle/visuelle font souvent partie de la qualification des pièces.
« Les essais mécaniques comprennent, sans s’y limiter, la traction, la compression, la flexion, la rupture, la rugosité de surface, la densité de la pièce, la composition chimique, le duromètre, la résistivité, l’inflammabilité, l’impact, le cisaillement, etc. En outre, les inspections visuelles/dimensionnelles recherchent généralement des fissures/défauts visibles, tandis que les inspections dimensionnelles sont facilitées par l’utilisation d’outils de mesure manuels, notamment des pieds à coulisse, des jauges de hauteur, des jauges d’épingle, etc. Les contrôles dimensionnels peuvent également être améliorés par l’utilisation d’équipements semi-automatiques, tels que les MMT ou les tomodensitomètres », souligne Nostedt.
Le scanner, par exemple, est l’un des outils utilisés par Conflux Technology pour qualifier ses échangeurs de chaleur imprimés en 3D. Il permet de détecter les fissures dans les pièces et de vérifier la porosité pour valider la densité des pièces. Il permet également aux utilisateurs de vérifier que leur équipement fonctionne correctement et que leurs processus sont sains et reproductibles, de sorte que les mêmes propriétés métallurgiques et mécaniques puissent être obtenues à tout moment sur les pièces imprimées en 3D.
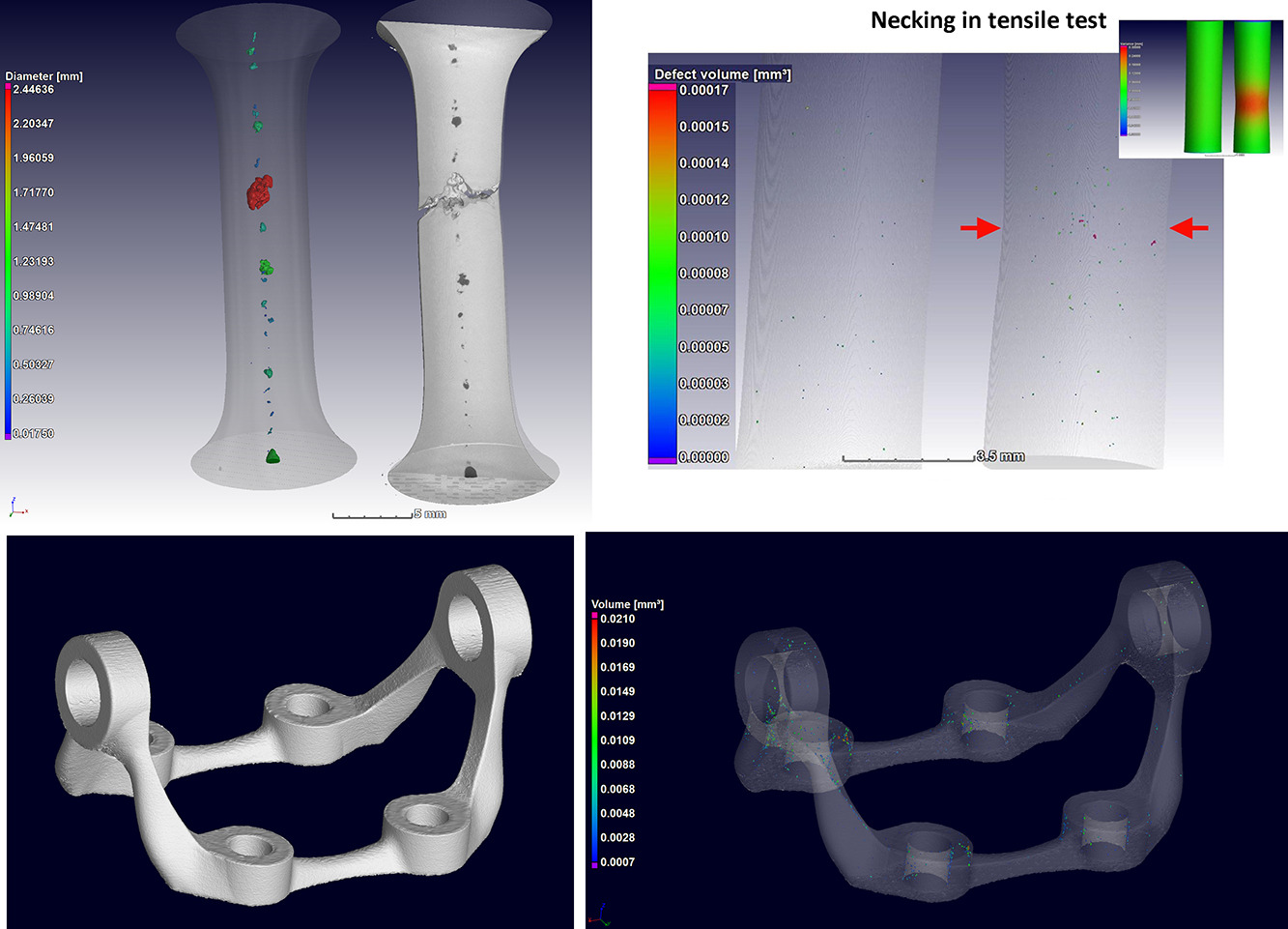
Pour Nostedt, il est important de garder à l’esprit que les outils nécessaires pour qualifier les pièces peuvent varier en fonction de la technologie, d’autant plus que certaines technologies nécessitent plus de processus de test que d’autres. En outre, la précision de la mesure du dispositif doit être déterminée en fonction de la plage de spécification de la pièce. La validation de la méthode d’essai (par exemple, Gage R&R) est recommandée pour démontrer que le dispositif est capable et cohérent, conformément aux exigences de l’application.
Quelle que soit la diversité de votre gamme d’outils, Barnes recommande aux fabricants de pièces d’être prudents et d’éviter le piège des « processus fixes » :
Certaines personnes essaient souvent de commencer par des « processus fixes ». Cela signifie qu’ils essaient de verrouiller tous les paramètres qu’ils pensent pouvoir contrôler, ce qui risque d’exclure toute amélioration future, explique-t-il.
Il donne l’exemple d’une pièce qu’ils ont qualifiée pour Airbus. « Cette pièce était fabriquée sur un système à deux lasers et, parce que ce processus fixe a été écrit à partir d’un système à deux lasers, la pièce aurait dû être requalifiée pour utiliser un système à quatre lasers, par exemple. Il peut s’agir de la même taille, du même fabricant, de la même marque, mais cela ne laisse pas de place aux améliorations. Le responsable de la conception doit donc être très clair sur les exigences et l’équipe de fabrication ne doit pas essayer de « surcontraindre » la pièce », souligne Barnes.
En fin de compte, « ce que vous recherchez, c’est un processus reproductible pour fabriquer la pièce », ajoute t-il. « La FA est une série de processus. Tout ce que vous pouvez faire, que ce soit au niveau de la conception ou de l’inspection, vous donne une orientation à partir de laquelle vous pouvez travailler. Si nous prenons le cas d’un système existant, la question que vous vous posez est la suivante : « Comment puis-je démontrer que je vais obtenir des performances identiques ou supérieures à celles du processus de fabrication précédent et que les performances de la première pièce seront les mêmes que celles que j’obtiendrai pour des milliers de pièces par la suite ? »
III – Quelles sont les considérations à prendre en compte dans des secteurs tels que l’armée, l’automobile et l’aérospatiale ?
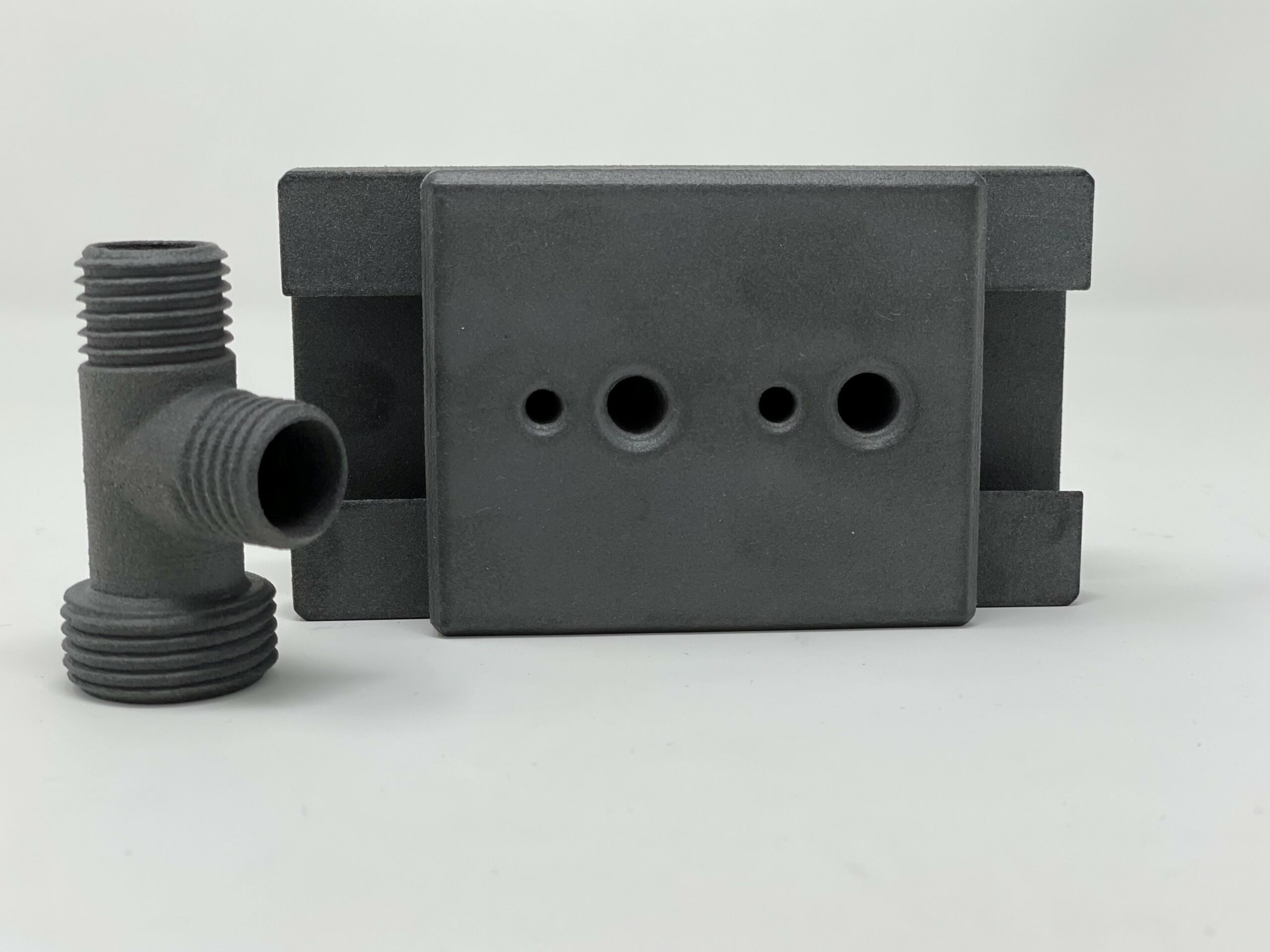
Des pièces différentes peuvent nécessiter des ensembles de paramètres différents. C’est un fait. Souvenez-vous de notre conversation avec Melissa Orme, vice-présidente de la division FA de Boeing, qui exhortait les équipementiers à prendre sérieusement en compte la question de l’application par rapport à l’organisme de réglementation et à faire leurs devoirs.
Comme l’explique Nostedt, « les exigences de validation d’une pièce conçue pour être utilisée dans une industrie réglementée sont généralement plus strictes. L’autorité chargée de la conception doit comprendre comment la pièce sera utilisée, ainsi que l’impact global d’une application critique en cas de défaillance de la pièce. En règle générale, les exigences sont plus nombreuses pour une pièce dont le risque de défaillance est plus élevé.
Les exigences peuvent également aller au-delà de la pièce elle-même et s’étendre à la documentation, comme les qualifications de l’équipement et les dossiers de formation qui ne nécessitent généralement pas de documentation pour un produit de consommation. Il est toutefois dans l’intérêt du fabricant de pièces de s’assurer que des étapes telles que la qualification de l’équipement sont franchies d’un point de vue commercial afin de garantir la production de pièces de la plus haute qualité tout en maintenant les coûts à un niveau minimum. »
Il n’est pas encore possible de discuter des spécifications de la qualification des pièces pour chaque industrie hautement réglementée. Toutefois, pour favoriser le débat et, sur le long terme, l’établissement de cadres de qualification, les équipementiers des industries verticales devraient faire preuve de transparence quant aux défis auxquels ils sont confrontés dans leur secteur respectif.
Les pièces produites pour l’automobile et l’aérospatiale, par exemple, ne sont pas soumises au même environnement et l’industrie définit la quantité d’essais nécessaires pour un événement de qualification.
« Le processus de qualification ne change pas, mais le niveau de données requis pour répondre aux exigences d’une industrie donnée peut changer. Pour tester une pièce d’engin spatial, par exemple, on examinera des environnements à très basse température et à faible teneur en oxygène. Pour une pièce automobile, nous n’avons pas besoin de tels tests », explique Barnes.
Dans le même ordre d’idées, comme l’a expliqué Barnes, les pièces imprimées en 3D fabriquées dans cette industrie doivent résister à un environnement très austère. Les pièces traditionnelles achetées et utilisées dans les applications navales, par exemple, doivent subir des tests destructifs pour s’assurer que leurs performances répondent à ces exigences d’environnement austère. Le problème de la FA est que, malgré son potentiel, il n’existe pas encore de mécanisme standard pour évaluer si les pièces imprimées en 3D sont plus ou moins conformes aux spécifications militaires établies.
Pour Barnes, il existe de nombreuses pièces qui sont nécessaires mais dont la défaillance n’entraînerait pas la perte du système. Aujourd’hui, de nombreuses organisations militaires font face à des challenges avec des pièces traditionnellement fabriquées par moulage. La FA soulève un certain nombre de questions, la première étant la capacité à répondre aux exigences de conception. Cela dit, au-delà de ces contraintes de fabrication, la principale préoccupation du secteur militaire à l’heure actuelle reste la possibilité de fabriquer à temps.
Conclusion
La qualification (et la certification) resteront toujours un sujet d’actualité dans l’industrie dont les cadres seront continuellement mis à jour car les propriétés de la pièce imprimée en 3D sont déterminées à la fois par le matériau, le traitement et la géométrie du composant. Pour reprendre les termes de Nostedt, étant donné que différents secteurs ajoutent continuellement des documents d’orientation sur la classification des pièces pour aider les utilisateurs de la FA à qualifier les pièces, il est conseillé de se tenir au courant des processus d’essai des pièces.
Notes de l’éditeur
En tant qu’ingénieur qualité Jabil pour la FA, Nostedt supervise le processus visant à garantir la qualité des polymères et des métaux utilisés dans les assemblages imprimés en 3D pour les secteurs de l’aérospatiale, de la médecine et des biens de consommation. En outre, il prend en charge les qualifications ISO, crée/met à jour les PFMEA et les plans de contrôle, et dirige l’analyse des données pour l’amélioration continue des processus. En tant que membre de l’ASTM International, il a contribué à plus de 90 documents ou révisions de documents relatifs aux orientations, spécifications et normes de l’organisation concernant la FA, y compris la documentation conjointe ISO/ASTM.
L’expérience notable de Barnes avant de fonder TBGA en 2017 est son expérience en tant que cadre supérieur chez Skunk Works de Lockheed Martin où il a aidé à apporter des pièces métalliques imprimées en 3D à un certain nombre d’avions militaires expérimentaux et où il a dirigé plusieurs autres programmes visant à favoriser l’adoption des technologies de FA. Aujourd’hui, avec une équipe d’ADDvisors®, l’objectif de TBGA est de qualifier la FA et de la mettre en service dans un grand nombre d’industries.
Ce dossier a été initialement publié dans le numéro de Juillet/Août de 3D ADEPT Mag.