Si vous êtes allé chez le dentiste au début des années 2000, il y a de fortes chances que vous ayez reçu une couronne en métal ou en or pour votre dent qui avait besoin d’être restaurée. Personnellement, voir mon dentiste utiliser un matériau en or ou en métal pour une couronne ou une obturation ne fait pas partie de mes meilleurs souvenirs. Une couronne en métal dans la bouche me donnait l’impression d’être l’un de ces rappeurs que l’on voyait dans les vidéos musicales américaines à la mode à l’époque. Heureusement, aujourd’hui, il est possible d’avoir une couronne ou un plombage qui s’harmonise parfaitement avec la couleur de nos dents et il a fallu une conversation avec Daniel Bomze pour que je comprenne que le secret d’une telle solution réside dans l’utilisation d’un matériau vitrocéramique appelé disilicate de lithium.
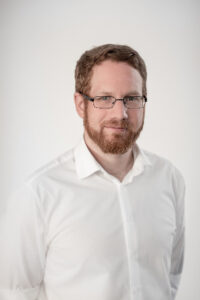
Si vous êtes un lecteur régulier de 3D ADEPT Media et que vous vous intéressez de près aux applications d’impression 3D dans le domaine de la santé, le nom de Daniel Bomze vous est peut-être familier. Le directeur des solutions médicales de la société d’impression 3D de céramiques Lithoz a discuté avec 3D ADEPT Media l’année dernière des facteurs à prendre en compte lors de l’exploration des céramiques techniques dans la fabrication additive médicale et des raisons pour lesquelles elles conviennent bien aux applications dentaires. L’un des points forts de notre conversation était que la zircone, l’ATZ et le ZTA – qui font tous partie du portefeuille de matériaux de Lithoz – pouvaient être traités avec la technologie de fabrication de céramique basée sur la lithographie (LCM) de l’entreprise pour réaliser la production de masse de certaines applications dentaires.
Depuis notre conversation, Lithoz a approfondi sa collaboration avec Metoxit, une entreprise suisse de céramique de haute technologie qui développe des céramiques d’oxyde. Ensemble, ils explorent les applications dentaires imprimées 3D en céramique. « Avec Metoxit, nous étudions actuellement l’utilisation de l’ATZ (zircone durcie à l’alumine) pour développer des implants dentaires. Nous étudions également la possibilité de produire une large gamme de dispositifs tels que des fraises ou des outils de fraisage. D’autre part, nous travaillons également avec une université sur des applications relatives à ce sujet qui, nous l’espérons, seront bientôt publiées. La vérité, c’est que beaucoup de gens optent aujourd’hui pour des solutions sans métal lorsqu’il s’agit d’implantologie dentaire. Ils paient cher pour avoir des solutions avec d’autres matériaux tels que la zircone et l’ATZ, mais leur utilisation est souvent combinée à des processus standard. Lorsque nous avons réalisé que certains fabricants proposaient également des fraises en céramique, nous avons décidé d’explorer davantage l’utilisation de ces matériaux pour les applications dentaires réalisées par fabrication additive céramique – sachant que les avantages de la technologie (liberté de conception et capacité à réaliser différentes géométries) joueraient en notre faveur pour obtenir des applications avec de meilleurs résultats. »
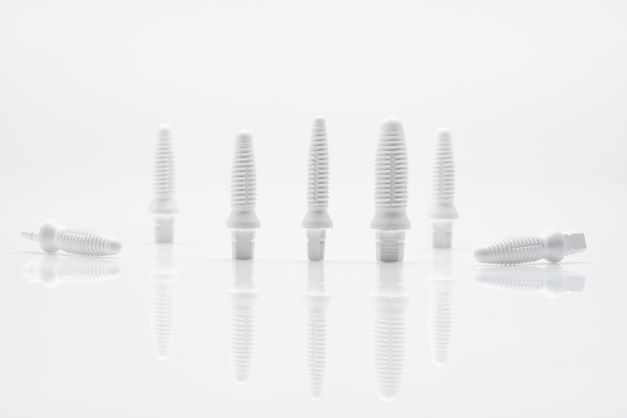
Dans le même ordre d’idées, le disilicate de lithium, matériau vitrocéramique reconnu pour sa translucidité (ce qui signifie qu’il peut s’harmoniser avec la couleur des dents naturelles), est largement utilisé pour les restaurations dentaires telles que les couronnes et les facettes.
L’anion silicate (une structure tétraédrique de 4 atomes d’oxygène autour d’un atome de silicium) est le matériau de base de la plupart, sinon de tous les matériaux en verre. Le lithium est ajouté sous forme d’ions pour obtenir les propriétés souhaitées de la vitrocéramique dentaire par rapport au verre à vitre standard, par exemple. Le développeur de la technologie de fabrication de céramique par lithographie (LCM) s’est associé à Ivoclar, un fabricant de solutions intégrées pour des applications dentaires esthétiques et de haute qualité, pour mettre au point ce nouveau matériau à base de disilicate de lithium. Basé sur la poudre de disilicate de lithium IPS e.max (IPS e.max signifie qu’il appartient à une famille de matériaux de restauration dentaire utilisés par des méthodes de façonnage traditionnelles et utilisés en raison de leur esthétique et de leur aspect similaire à la dent naturelle), le matériau permet de fabriquer des facettes d’une épaisseur de 0,3 mm et des couronnes avec un niveau de détail élevé, en particulier au niveau des surfaces occlusales.
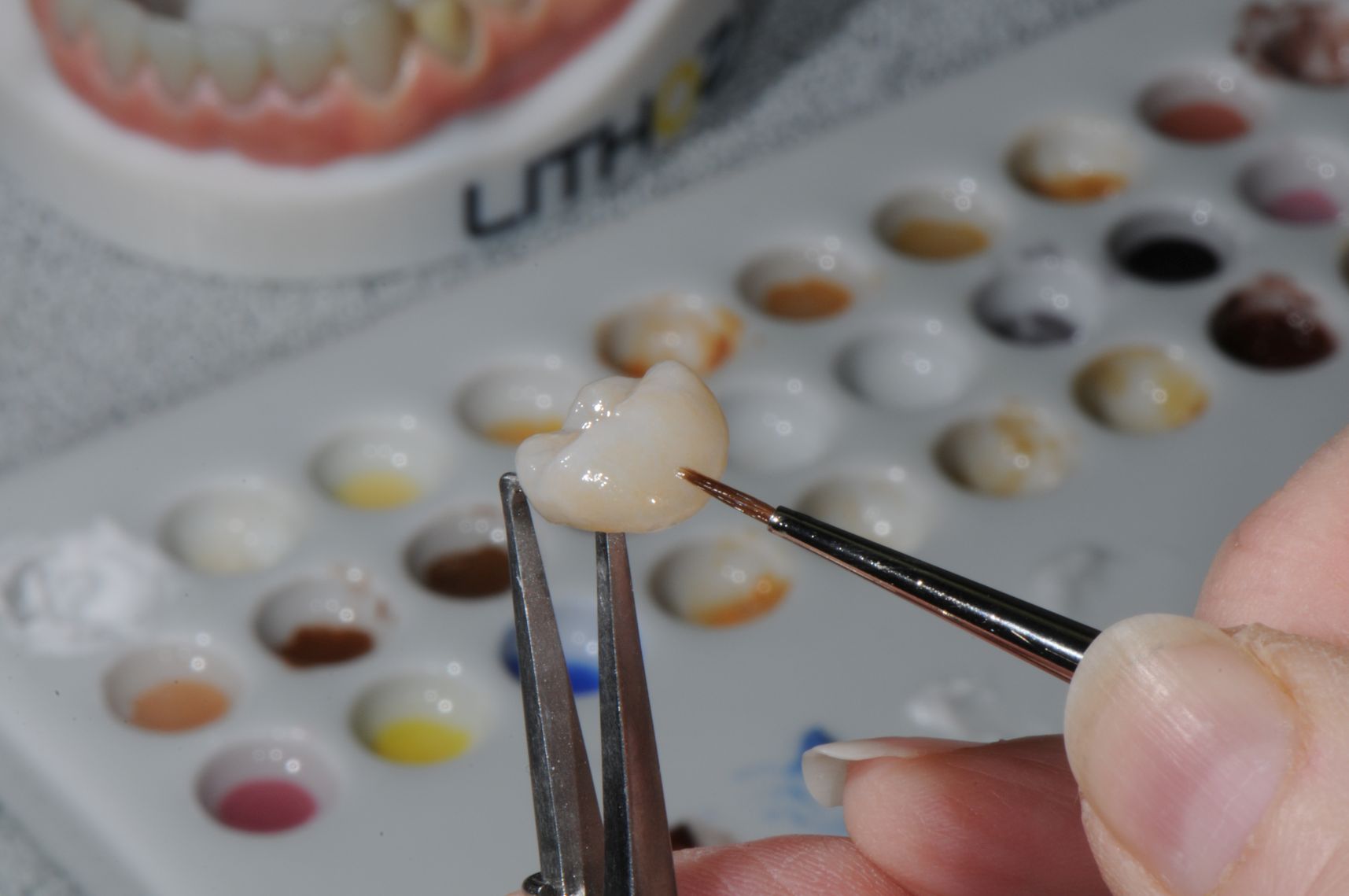
Les différents procédés de fabrication du disilicate de lithium
Selon Bomze, il existe actuellement trois façons de créer des applications de dentisterie restauratrice avec ce matériau : le procédé le plus traditionnel est le pressage à chaud/pressage thermique. Ici, le processus de fabrication commence par le modèle de la couronne ou de la facette et repose sur l’utilisation d’une technique de cire perdue, un processus couramment utilisé pour couler les alliages dentaires.
Le fraisage est un autre procédé conventionnel qui peut être utilisé pour traiter ce matériau. Il utilise des fraises diamantées à grande vitesse pour obtenir la forme finale de la restauration. Les restaurations en disilicate de lithium sont fraisées par usinage dur avant leur cristallisation complète. Un traitement thermique est ensuite effectué pour obtenir les caractéristiques mécaniques et optiques finales.
Et puis vient l’impression 3D. Dans ce cas précis, le processus de fabrication de céramiques par lithographie de Lithoz permet de fabriquer les applications susmentionnées à l’aide du matériau de disilicate de lithium récemment mis au point. Pour ceux qui ne sont pas familiers avec ce procédé, il convient de noter qu’au cours de ce processus de fabrication, les particules de céramique sont dispersées dans une résine photosensible et cette dispersion est ensuite solidifiée par la lumière, couche par couche, pour former une pièce. La pièce est ensuite soumise à un processus de déliantage et de frittage afin de lui conférer ses propriétés céramiques et de pouvoir l’utiliser pour son usage final.
Notre conversation avec Bomze nous a permis de comprendre les différents avantages et inconvénients de chaque processus de fabrication :
Avantages- | Inconvénients | |
Pressage thermique | Il existe un effet caméléon qui permet d’avoir de meilleures propriétés optimales que la zircone.
Procédé qui repose sur l’utilisation d’une technique de cire perdue. Faibles coûts d’investissement pour l’équipement. Connu de la plupart des prothésistes dentaires. Faible coût des matériaux car les lingots sont comparativement peu coûteux et plusieurs restaurations peuvent être réalisées à partir d’un seul lingot. |
Limité en termes de précision et de finition. |
Fraisage | L’effet caméléon permet d’obtenir des propriétés optimales supérieures à celles de la zircone.
Le procédé offre une meilleure qualité de surface à la pièce. Une résistance finale à la flexion d’environ 500 MPa. Peut convenir pour les restaurations MOD indirectes de classe II dans divers modèles de préparation de cavité. |
Selon une étude, la résistance caractéristique des échantillons de disilicate de lithium est réduite d’environ 33 % après le fraisage.
Des fissures ou des défauts potentiels peuvent apparaître en raison de l’accumulation de contraintes ou du changement de diamètre des bavures. Le processus de fabrication nécessite beaucoup de matériau (80 % du matériau pourrait être gaspillé). Production d’une seule facette à la fois. Coût élevé des matériaux pour une seule restauration. L’obtention de la restauration finale peut prendre jusqu’à cinq jours. |
Processus de fabrication de céramiques par lithographie | Il y a un effet caméléon qui permet d’avoir de meilleures propriétés optimales que la zircone. La finition avec l’impression 3D sera identique aux dents du patient.
Beaucoup d’économies de matériaux. Si le processus de fraisage gaspille jusqu’à 80 % d’une quantité « x » de matériau pour une application donnée, la fabrication additive (FA) céramique ne perd que moins de 10 % de matériau pour la même application. Stabilité de l’opération. Meilleure évolutivité et personnalisation de masse : on peut produire jusqu’à 100 facettes sur mesure en même temps en utilisant ce matériau et une imprimante 3D médicale CeraFab System S65. Possibilité de réaliser un traitement peu invasif dans certaines applications. La FA permet de réaliser un large éventail d’applications. |
La restauration finale peut prendre jusqu’à deux ou trois jours.
|
Il est bien connu que la nature des matériaux céramiques souffre de quelques problèmes, tels que la fragilité, la faible résistance à la traction, à la flexion et aux chocs, qui limitent leurs applications dans les restaurations dentaires. Toutefois, il faut reconnaître que les facettes imprimées en 3D peuvent présenter les mêmes propriétés mécaniques que le disilicate de lithium pressé et fraisé (avec une résistance de l’ordre de 470-530 MPa).

Par ailleurs, alors que la plupart des patients aspirent à ce que leur restauration dentaire soit réalisée lors du même rendez-vous à la clinique de leur dentiste, ce délai est difficile à respecter, quel que soit le processus de fabrication utilisé. À l’heure actuelle, la FA garantit les meilleures performances en termes de délais pour les facettes et les obturations et, surtout, « aucun entretien n’est nécessaire. Une fois la restauration imprimée en 3D, le succès du traitement dépend de l’expertise du dentiste », souligne Bomze.
Outre les avantages techniques qui peuvent résulter de l’utilisation de la fabrication additive céramique avec le disilicate de lithium, j’ai été impressionnée par les différents cas ou scénarios dans lesquels cette technologie peut apporter une valeur ajoutée :
« Pour les personnes qui ont un diastème par exemple [un espace entre les dents], un traitement peu invasif peut être réalisé pour résoudre le problème. Dans ce cas, les facettes sans préparation sont un excellent candidat pour la FA céramique », explique Bomze. De plus, en fonction des besoins spécifiques du patient, les facettes imprimées en 3D peuvent être réalisées in situ, après fixation par adhésif, ou sur la base d’un scan intraoral, après individualisation sur le modèle produit par fabrication additive.
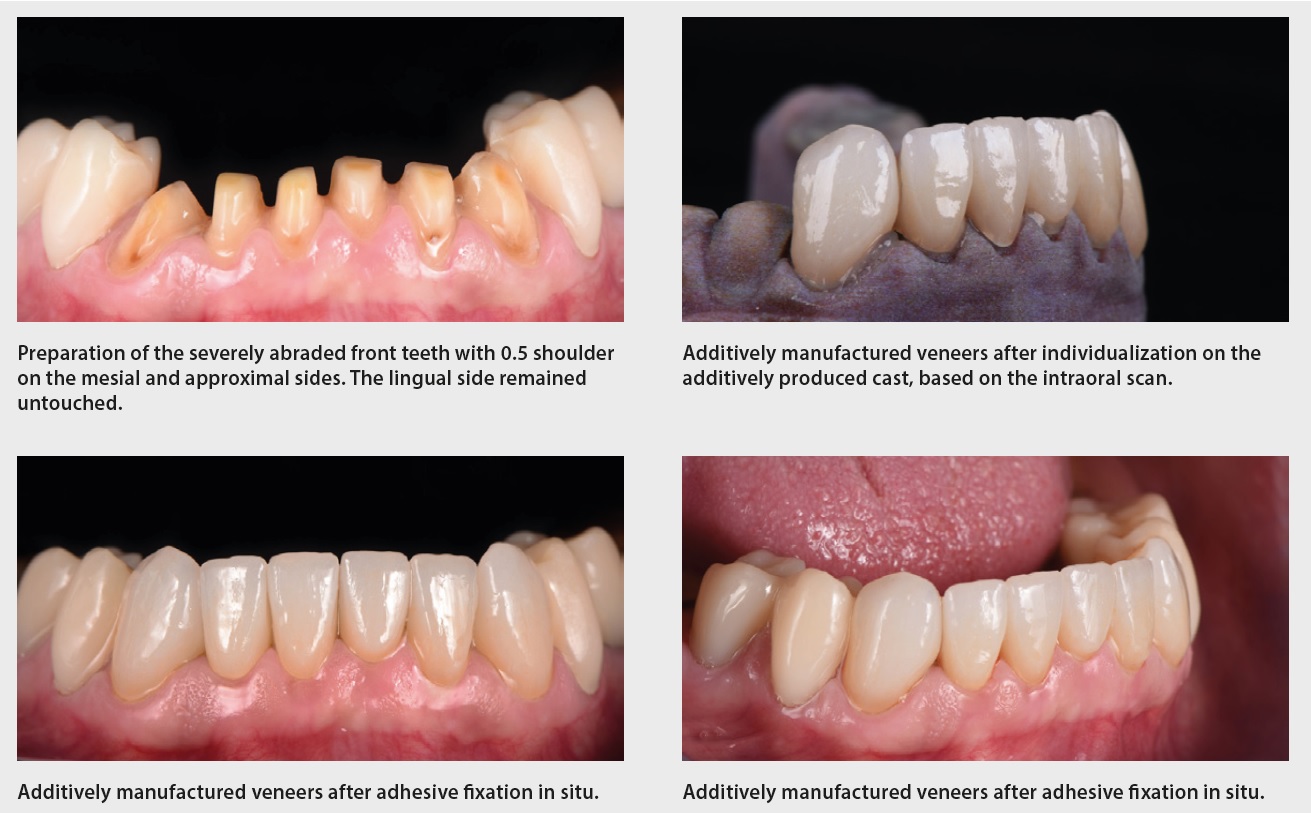
Pour aller de l’avant…
Alors que les États-Unis seront le premier marché où les produits à base de disilicate de lithium seront mis à la disposition des clients, les activités de recherche se poursuivent chez Lithoz pour faire progresser l’utilisation de ce matériau et ses applications dans le domaine de l’impression 3D de céramiques. L’entreprise étudie actuellement la possibilité de combiner deux formes de disilicate de lithium pour obtenir une pièce multi-matériaux imprimée en 3D. « Si les résultats de ce projet sont concluants, cette application changera la donne dans le domaine de la dentisterie numérique », conclut Bomze. Et compte tenu de la base installée et de la part de marché importante de Lithoz, je ne doute pas que l’entreprise soit prête à capitaliser sur cette opportunité de marché relativement sous-développée.
Ce contenu a été rédigé en collaboration avec Lithoz.
Quelques mots sur Lithoz et Daniel Bomze
Lithoz est le leader mondial et technologique des matériaux céramiques de haute performance et des imprimantes 3D. Fondée en 2011, Lithoz s’engage à repousser les limites de la production de céramique et à aider ses clients à élargir les possibilités de fabrication de l’industrie céramique. En tant que spécialiste innovant de l’impression 3D céramique de haute précision pour des applications dentaires et médicales biorésorbables complexes, Lithoz a également été le premier fournisseur de systèmes au monde à développer avec succès des céramiques dentaires haut de gamme pour l’impression 3D. L’entreprise a une part d’exportation de près de 100%, 150 employés et 4 sites différents dans le monde. Depuis 2016, Lithoz est également certifiée ISO 9001-2015.
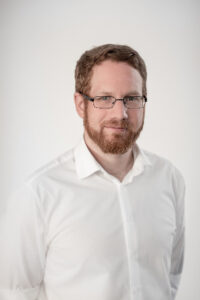
Daniel Bomze est chimiste polymériste de formation et a obtenu son doctorat à l’Université technique de Vienne. Dans sa thèse de doctorat, réalisée à l’Institut de chimie synthétique appliquée, Bomze a mis au point des méthodes alternatives de durcissement par irradiation pour les résines époxy. Il a commencé sa carrière professionnelle en tant qu’ingénieur indépendant spécialisé dans les applications web et en tant qu’assistant de projet à l’université technique de Vienne. Bomze a acquis une vaste expérience dans la recherche sur les matériaux dans différents domaines et est l’auteur de nombreuses publications et brevets. Depuis novembre 2016, il est employé en tant que développeur des affaires médicales chez Lithoz. En 2019, il est devenu responsable de l’unité commerciale médicale, qui comprend également des applications dentaires. À partir de 2022, le Dr. Bomze est directeur de la division des solutions médicales chez Lithoz.