Bien que les utilisateurs finaux de l’industrie des biens de consommation ne se demandent pas toujours quelle technologie a été utilisée pour la fabrication de leurs produits, les applications de la fabrication additive dans ce domaine d’activité sont celles qui favoriseront encore la croissance de cette technologie. Le dernier exemple que nous avons vu dans cette industrie est celui des lunettes de ski qui ont été partagées par OECHSLER.
Connue pour la fabrication de pièces automobiles et médicales, l’entreprise fournit des pièces imprimées en 3D depuis 2017. Elle s’appuie sur les technologies de FA de HP et Rösler au niveau de la production, et elle est également connue pour son partenariat avec AREVO.
OECHSLER estime que la multiplicité des pièces entraîne un potentiel de défaillance plus élevé pendant la production, un risque accru de défaillance du produit et, au final, des coûts plus élevés. C’est pourquoi, au début de la saison hivernale, ils ont décidé d’explorer une technique qui apporterait plus de confort et de fonctionnalité à l’un des produits sportifs les plus utilisés de cette saison : les lunettes de ski.
L’entreprise souhaitait simplifier le processus de fabrication des lunettes de ski, ce qui était facilement réalisable dans le cadre d’une production à faible volume. Grâce à la technologie de FA lattice, le processus de développement de ce produit a nécessité un délai d’environ quatre semaines du début à la fin du produit.
Le processus de fabrication
Normalement, 13 pièces sont utilisées pour fabriquer une seule paire de lunettes de ski. C’est plutôt élevé pour un article de sport aussi standard, non ?
L’utilisation de la FA pourrait permettre de réduire ce nombre de pièces mais nécessiterait également de repenser le processus de fabrication. Selon l’équipe d’OECHSLER, « la mousse PU utilisée doit être remplacée par une structure en treillis fabriquée de manière additive, le nombre de pièces doit être réduit au strict minimum et le confort de port augmenté. »
Pour atteindre cet objectif, l’entreprise a dû adopter une approche de rétro-ingénierie. Dans cette optique, l’équipe a d’abord démonté l’échangeur de lentilles, y compris l’élément rotatif pour le retrait de la lentille. Cet élément rotatif est crucial car il facilite le changement des lentilles dans certaines conditions météorologiques ou lorsqu’elles ne sont plus fonctionnelles. La partie suivante qui a été démontée est le cadre extérieur, qui est maintenu par des clips, et pour finir, les godets qui maintiennent l’élastique.
Au cours du processus de reconception, l’équipe de conception du fabricant allemand avait deux possibilités : soit créer un produit tout-en-un et éliminer toutes les étapes de montage, soit réduire les éléments de sorte que les mousses soient remplacées par un treillis imprimé en 3D.
L’équipe a opté pour la première solution et a décidé de scanner toutes les pièces par tomodensitométrie afin de mieux connaître les dimensions des composants. Ensuite, elle a reconstruit chacune de ces pièces dans un programme vectoriel afin de générer un fichier d’impression approprié pour les pièces solides et en treillis.
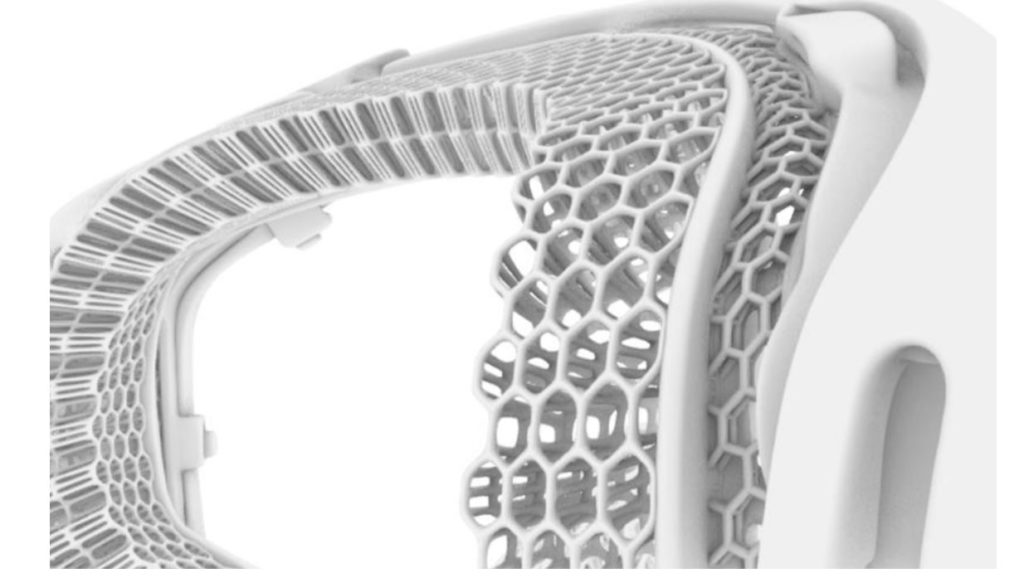
Malgré leur expérience, comme beaucoup d’entreprises, l’équipe a également été confrontée à un échec lors de la première tentative de création des fichiers d’impression. Ils expliquent que les premières impressions étaient trop rigides, par conséquent, les poignées n’étaient pas assez flexibles. « Contrairement à ce que l’on pensait au départ, ce problème n’était pas dû au fichier d’impression mais aux étapes de post-traitement de la production. Il a fallu procéder à un nettoyage différent et plus intense des structures en treillis pour éliminer une plus grande partie des résidus d’impression. Même si l’optimisation du fichier d’impression a été assez rapide, l’ajustement du post-traitement pour augmenter la flexibilité de la structure en treillis a été un défi. »
Au final, les résultats démontrent les avantages suivants de l’application de la fabrication additive à la fabrication de ces lunettes de ski :
- Confort de port accru et fonction d’amortissement intégrée en cas d’accident.
- Combinaison d’éléments rigides et souples en un seul composant.
- Joints mobiles au lieu de pièces supplémentaires comme des clips
- Réduction de la variété des matériaux, ce qui facilite le recyclage à la fin du cycle de vie du produit.
- Réduction des coûts de production grâce à l’élimination des étapes de montage.
- Remplacement de la mousse par une structure en treillis imprimée en 3D : dureté réglable – les mousses multicouches existantes peuvent être remplacées.
N’oubliez pas que vous pouvez poster gratuitement les offres d’emploi de l’industrie de la FA sur 3D ADEPT Media ou rechercher un emploi via notre tableau d’offres d’emploi. N’hésitez pas à nous suivre sur nos réseaux sociaux et à vous inscrire à notre newsletter hebdomadaire : Facebook, Twitter, LinkedIn & Instagram !