Au cours des sept dernières années, j’ai eu le plaisir de voir l’impression 3D de céramiques appliquée à des domaines de plus en plus variés : soins de santé et médecine, aérospatiale, énergie, architecture et même art. De tous ces domaines, je reste fascinée par les applications de cette technologie dans les domaines de la santé et de la médecine. Si vous vous intéressez de près ou de loin à l’impression 3D en céramique, vous savez probablement déjà que l’éventail des technologies d’impression 3D en céramique permettant de telles applications est très large. Mais pour être honnête avec vous, je dois probablement ma fascination pour ce secteur aux technologies de Lithoz – et je vais vous dire pourquoi.
Si vous êtes un lecteur régulier de 3D ADEPT Media, le nom de Lithoz vous dit probablement quelque chose. Avec plus d’une décennie d’activités dans le domaine de la FA, une acquisition et trois technologies propriétaires (LCM, LIS, LSD Print), le travail de Lithoz a été validé dans trois industries verticales principales : médicale, aérospatiale et spatiale, et semi-conducteurs. Dans tous ces domaines, l’entreprise a démontré que sa technologie LCM, leader sur le marché, est devenue un candidat prometteur pour la production dans les secteurs des soins de santé et de la médecine.
Si vous n’êtes pas encore familiarisé avec la technologie LCM (lithography-based ceramic manufacturing), sachez qu’il s’agit d’un processus au cours duquel des particules de céramique sont dispersées dans une résine photosensible. Cette dispersion est ensuite solidifiée par la lumière, couche par couche, pour former une pièce. La pièce subit ensuite un processus de frittage pour développer ses propriétés céramiques et peut être utilisée pour son usage final.
Au fil des ans, l’entreprise autrichienne a élargi le champ d’application de cette technologie avec la mise sur le marché de nouveaux matériaux, ouvrant ainsi la voie à de nouvelles applications en dentisterie. Dans ce qui est devenu notre traditionnel tête-à-tête, Daniel Bomze, directeur des solutions médicales, m’a expliqué ce qui se passe en coulisses depuis que l’entreprise a dévoilé son matériau à base de disilicate de lithium.
« Tout se résume en trois points principaux :
Tout d’abord, les applications d’impression 3D pour des restaurations dentaires hautement esthétiques avec notre matériau à base de disilicate de lithium gagnent du terrain dans le domaine dentaire. Nous continuons à recevoir un intérêt considérable pour ces applications dans le monde entier. Notre dernière participation au LMT Lab Day à Chicago témoigne de cet intérêt. Ce marché continuera à connaître une forte traction à l’avenir, car il met en évidence une nouvelle méthode de fabrication après des décennies dans ce domaine.
Nous avons également été impliqués dans plusieurs projets intéressants où nous avons pu repousser les limites de ce qui est possible avec notre impression 3D céramique multi-matériaux. »
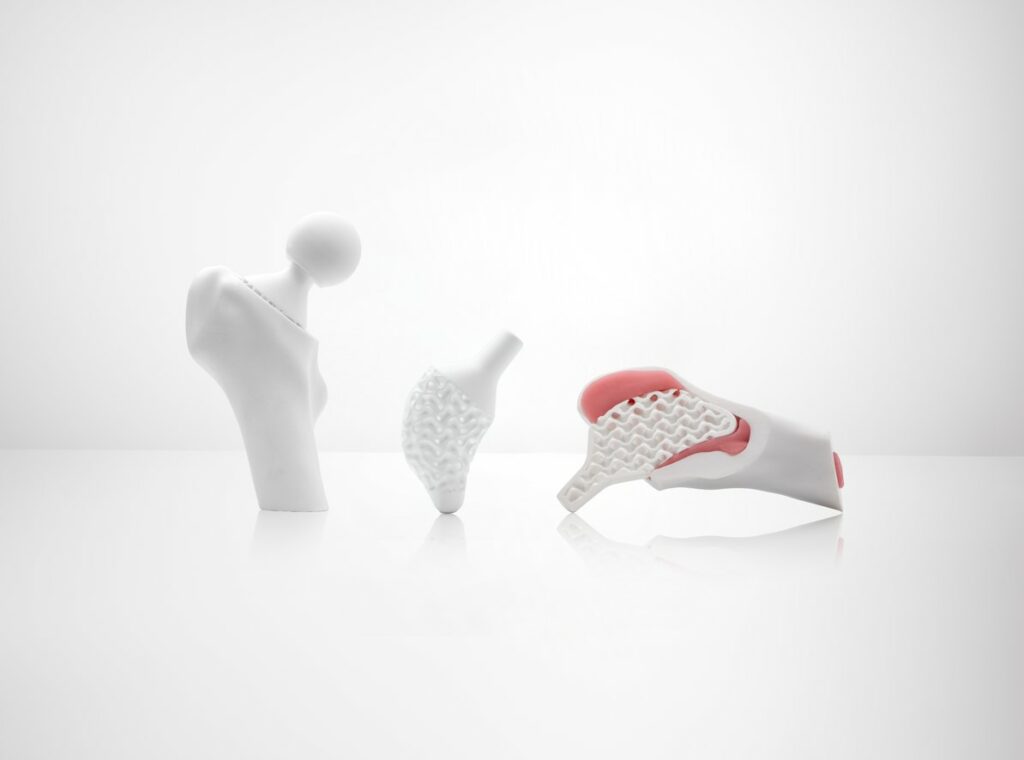
Pour rappel, Lithoz a lancé en 2023 l’imprimante 3D CeraFab Multi 2M30, une imprimante 3D capable de traiter des matériaux aux propriétés opposées comme la conductivité et l’isolation en une seule impression, créant ainsi la prochaine génération de pièces multifonctionnelles imprimées en 3D, ce qui était auparavant irréalisable avec un niveau de complexité.
« En ce qui concerne le domaine de la santé, nous nous sommes particulièrement concentrés sur les solutions de remplacement osseux multi-matériaux », explique Bomze. « Un exemple qui mérite d’être mentionné ici est l’augmentation mandibulaire après une atrophie osseuse qui, jusqu’à présent, a toujours consisté en un seul matériau. Normalement, vous avez un matériau de remplacement osseux et, par-dessus, vous avez toujours besoin d’une sorte de membrane pour empêcher la croissance prématurée des tissus mous. En effet, si un tissu mou comme la gencive pousse dans l’échafaudage, il n’y aura pas d’espace résiduel pour l’os lui-même. Cela est possible parce que l’os se développe beaucoup plus lentement que les tissus mous. C’est pourquoi, dans le cadre d’un projet de recherche, nous avons combiné un matériau à résorption rapide comparable, comme le phosphate tricalcique, avec un autre très bon matériau bioactif, l’hydroxyapatite, sur l’enveloppe extérieure, afin d’obtenir une membrane en céramique. Cette membrane céramique doit empêcher la croissance des tissus mous pendant la phase de cicatrisation. Nous sommes très satisfaits des résultats obtenus jusqu’à présent ; nous espérons partager bientôt plus de détails sur ce projet.
Le troisième sujet qui a fait l’objet de beaucoup d’attention ces derniers temps est celui des outils chirurgicaux, tels que les fraises et les rasoirs, ainsi que d’autres applications similaires. Nous avons découvert que nous avions touché le point sensible de l’industrie, car il est souvent difficile d’obtenir une qualité élevée dans la fabrication traditionnelle, et nous sommes très fiers de pouvoir atteindre une productivité élevée avec une grande liberté de conception grâce à l’impression 3D de céramique », ajoute-t-il.
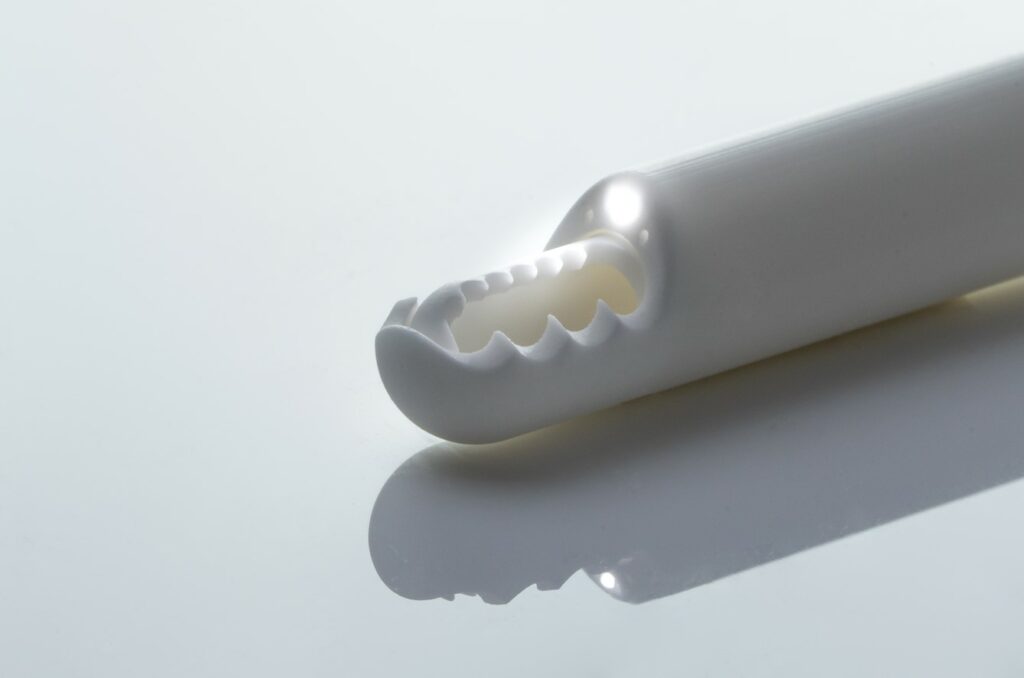
L’impression 3D en céramique et les applications dans le domaine de la santé : les outils chirurgicaux en point de mire
Au fil des ans, nous nous sommes rendu compte que les applications de l’impression 3D en céramique dans le secteur de la santé pouvaient être explorées sous quatre angles principaux : les applications dans les soins médicaux extracorporels, telles que les modèles médicaux et les aides à la rééducation, les dispositifs médicaux, les applications liées aux matériaux biologiquement actifs et biodégradables, telles que les échafaudages implantables à long terme pour l’ingénierie tissulaire ou les matériaux bioactifs pour la régénération et la réparation des tissus, ainsi que la bio-impression.
Il est intéressant de noter que la toute première série d’applications est actuellement utilisée dans des contextes cliniques à travers le monde et joue un rôle crucial dans la planification chirurgicale, l’amélioration de l’efficacité chirurgicale et l’augmentation des taux de guérison.
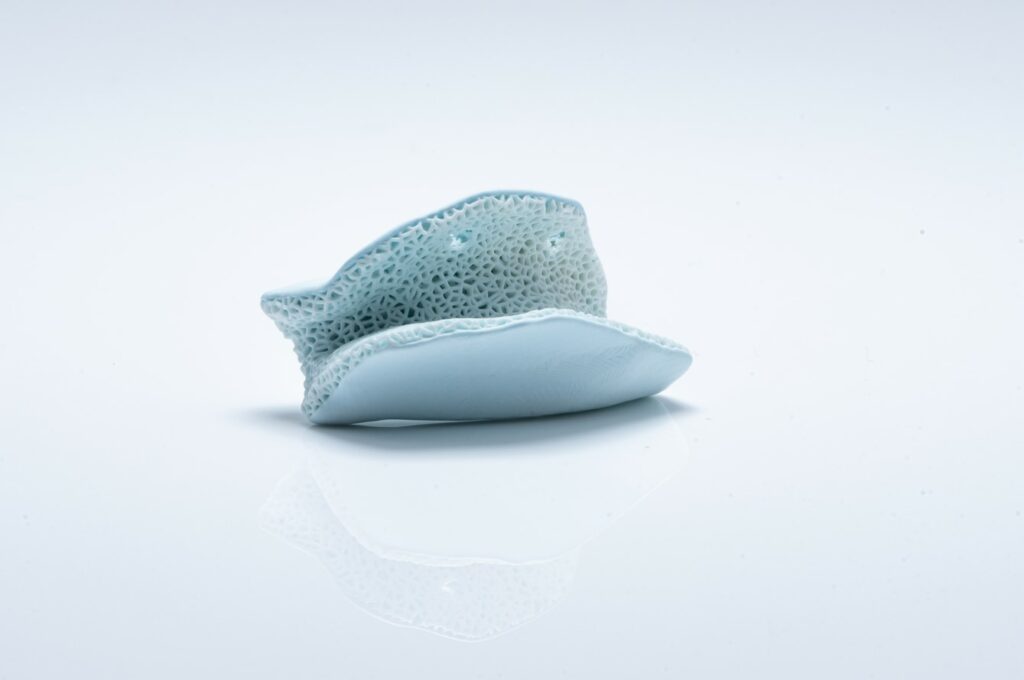
Ce que j’apprécie particulièrement dans l’approche de Lithoz, c’est que son équipe d’ingénieurs médicaux ne se contente pas de faire un effort supplémentaire pour améliorer le processus de fabrication, en tenant compte des limites des processus de fabrication conventionnels, mais qu’elle prend également en compte les limites existantes de sa technologie propriétaire. En fin de compte, ne dit-on pas : « Comparez-vous à ce que vous étiez hier » ?
Bomze souligne ici que « les outils chirurgicaux ont suscité un vif intérêt de la part des professionnels de la santé parce qu’il est désormais possible d’améliorer considérablement les propriétés mécaniques des céramiques haute performance imprimées en 3D. C’est quelque chose qu’il n’est pas facile d’obtenir par la fabrication conventionnelle, étant donné que les matériaux ne présentent pas toujours les propriétés souhaitées. »
Parlant de leur technologie LCM et de la façon dont ils ont été en mesure de pousser ses capacités, il ajoute : « Nous avons également pu élargir la fenêtre de traitement de certains de nos matériaux. Cela signifie qu’avec le même matériau, nous pouvons produire des pièces très délicates avec des caractéristiques minuscules ainsi que des pièces volumineuses qui sont vraiment robustes et destinées à des applications porteuses (une articulation artificielle de la hanche, par exemple). Il y a un an, nous aurions dit aux professionnels de la santé que cette « épaisseur de paroi » n’est pas possible à réaliser avec notre technologie LCM. Grâce aux progrès réalisés dans le domaine des matériaux, nous pouvons aujourd’hui mettre au point des articulations artificielles de la hanche sur mesure ou spécifiques au patient. »
Pour donner un exemple d’outil chirurgical pour lequel l’impression 3D céramique offre un meilleur moyen de fabrication par rapport à une approche de fabrication conventionnelle, le directeur médical de Lithoz m’a fait imaginer un scénario de la vie réelle.
« Imaginez un athlète qui s’est blessé au niveau du genou en faisant du jogging. Si le ménisque se déchire, il peut s’incruster avec le temps et cette incrustation peut éventuellement entraîner des douleurs et limiter la mobilité. Dans la mesure du possible, le chirurgien essaiera de le traiter de manière conventionnelle, mais à un moment donné, ce traitement conventionnel ne suffira pas. Le médecin devra procéder à une chirurgie mini-invasive en pratiquant de petites incisions dans plusieurs parties du genou et en insérant différents types d’outils afin de retirer le ménisque déchiré ou lésé. Les outils utilisés pour cette application spécifique sont connus sous le nom de rasoirs de genou.
Selon la manière dont le chirurgien utilise l’appareil, celui-ci va pénétrer dans le tissu ou retirer une quantité superficielle de tissu, tout le tissu retiré étant aspiré par le grand canal central. Cet outil spécifique comporte également plusieurs canaux de diamètres différents sur la face supérieure, qui servent à rincer le site de l’opération avec un liquide de rinçage, tandis que le canal central supérieur contient une fibre de verre (guide de lumière) pour éclairer la zone opératoire. Cela devrait permettre au chirurgien d’avoir une meilleure vue et un meilleur contrôle, et de n’enlever que ce qui est déchiré et non les tissus sains. La FA permettra de produire un outil aussi complexe tout en réduisant considérablement les étapes d’assemblage nécessaires ».
En termes simples, l’idée d’utiliser la FA au niveau de la fabrication est de réduire le nombre de débris pendant l’opération, ce qui permet d’éviter plus facilement les cicatrices accidentelles qui auraient pu se produire lors d’une opération traditionnelle. Sans oublier que la FA offre une durabilité maximale avec un effort de production minimal.
Une méthode de fabrication conventionnelle aurait nécessité l’utilisation du fraisage et de la pression isostatique à chaud (HIP) pour usiner le dispositif spécifique avant son utilisation finale.
La perspective de la fabrication
L’exemple de Bomze m’a amené à m’interroger sur les différentes exigences de fabrication dans un environnement médical. Dans ce secteur, il est facile de parler de l’importance d’une usine de FA dans un environnement industriel. Dans un environnement médical ou de soins de santé, j’étais curieuse de savoir à quoi cela ressemblait.
« Tout d’abord, les chirurgiens obtiennent leurs pièces imprimées en 3D auprès des fabricants d’appareils médicaux, qui restent les principales cibles de Lithoz dans ce secteur », précise Bomze. « Ceci étant dit, il existe une grande variété d’entreprises qui seraient en mesure de construire une usine de FA pour les dispositifs médicaux.
Les composants clés d’une usine de FA peuvent donc inclure une imprimante 3D standard et des matériaux de post-traitement thermique qui répondent aux exigences en termes de biocompatibilité. Il va sans dire qu’il est possible de faire évoluer cet équipement en fonction des besoins.
« Ce qu’il faut retenir, c’est que cette usine d’AM – si elle est composée du bon équipement – vous permettra d’atteindre la liberté de conception tout en économisant du temps et des coûts là où c’est nécessaire. Il ne s’agit pas seulement de l’imprimante 3D, mais aussi de normes de qualité de A à Z qui peuvent vous aider à obtenir des résultats prévisibles et reproductibles dans la production en série.
Ce que nous avons appris au cours des 13 dernières années, c’est qu’un résultat prévisible et reproductible est important pour la plupart de nos clients. C’est encore plus important dans la fabrication de dispositifs médicaux, car les fabricants de pièces doivent obtenir le même résultat à chaque fois. Dans cette optique, il est de notre devoir, en tant que fabricants d’usines de FA, d’offrir la possibilité d’une documentation automatisée du processus de production, ainsi que des conceptions intelligentes de nos appareils et logiciels afin d’éviter les erreurs humaines ».
Avec son éventail de technologies et l’un des plus grands portefeuilles de matériaux de l’industrie, Lithoz peut s’enorgueillir d’avoir développé un portefeuille technologique qui pourrait répondre aux exigences de production au-delà de l’industrie des soins de santé.
Même si les comparaisons de coûts et de performances entre une usine de FA de Lithoz et une autre usine (utilisant des processus de fabrication conventionnels ou d’autres technologies de FA) sont trop vastes et complexes pour être abordées dans cet article, je crois fermement que les applications discutées aujourd’hui et les partenariats que l’entreprise signe continuellement dans l’industrie des soins de santé témoignent du potentiel de ses solutions.
En fin de compte, qu’il s’agisse de restaurations dentaires, d’outils chirurgicaux ou d’implants, le parcours de Lithoz montre que des progrès sont réalisés dans la recherche et l’application de la technologie d’impression 3D de céramiques dans le secteur de la santé. Le fait d’avoir pu assister à son développement, étape par étape, me conforte dans l’idée que ses meilleurs jours sont encore à venir.
Ce contenu a été produit en collaboration avec Lithoz.
N’oubliez pas que vous pouvez poster gratuitement les offres d’emploi de l’industrie de la FA sur 3D ADEPT Media ou rechercher un emploi via notre tableau d’offres d’emploi. N’hésitez pas à nous suivre sur nos réseaux sociaux et à vous inscrire à notre newsletter hebdomadaire : Facebook, Twitter, LinkedIn & Instagram !