During the past 7+ years, I have had the pleasure to see ceramic 3D printing being applied in an increasingly diverse range of fields: healthcare & medical, aerospace, energy, architecture and even art. Of all these fields, I remain fascinated by the applications of this technology in the healthcare and medical fields. If you have a slight interest in ceramic 3D printing, you probably already know that the landscape of ceramic 3D printing technologies that can enable such applications is very broad. But to be honest with you, I probably owe my fascination to Lithoz’s technologies – and I will tell you why.
If you’re a regular reader of 3D ADEPT Media, the name Lithoz should probably already ring a bell to you. With more than a decade of activities in the AM field, an acquisition, and three proprietary technologies (LCM, LIS, LSD Print), Lithoz’s work has been validated across three main vertical industries: medical, aerospace & space, and semiconductor. Of all these fields, the company has demonstrated that its market-leading LCM technology has become a promising production candidate in the healthcare & medical industries.
If you’re not familiar yet with LCM which stands for lithography-based ceramic manufacturing, note that it is a process where ceramic particles are dispersed in a photosensitive resin. This dispersion is thereafter solidified by light layer-by-layer to form a part. Then the part undergoes a sintering process to develop its ceramic properties and can be used for its final purpose.
Over the years, the Austrian company has expanded the scope of this technology with the release of new materials, opening up new applications in dentistry. In what has become our traditional one-on-one, Daniel Bomze, Director of Medical Solutions, told me what has been happening behind the scenes ever since they unveiled their Lithium Disilicate material.
“It all comes down to three main points:
First of all, 3D printing applications for highly aesthetic dental restorations with our lithium disilicate material are gaining traction in the dental field. We continue to receive tremendous interest in these applications across the world. Our latest appearance at the LMT Lab Day in Chicago reflects that interest. This market will continue to see huge traction moving forward, as it highlights a new way of manufacturing after decades in the field.
We have also been involved in several interesting projects where we could push the boundaries of what’s possible with our multi-material ceramic 3D printing.”
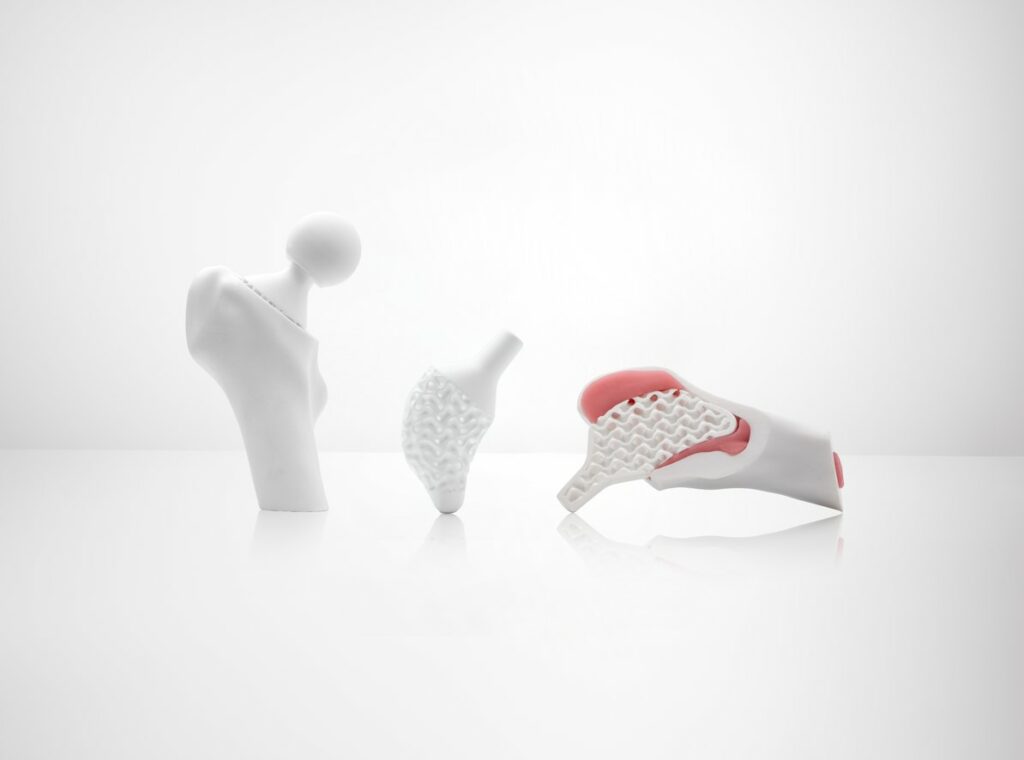
As a reminder, in 2020 Lithoz launched the CeraFab Multi 2M30 3D printer, a 3D printer that could process materials with opposing material properties like conductivity and insulation in one print run, creating the next generation of 3D printed multi-functional parts which was previously unachievable with a level of complexity.
“As far as the healthcare field is concerned, we focused especially on multi-material bone replacement solutions”, Bomze explains. “One example that is worth mentioning here is the mandibular augmentation after bone atrophy which so far has always consisted of one material. Normally, you have a bone replacement material and on top of it, you always need a kind of membrane to prevent premature ingrowth of soft tissues. Indeed, if a soft tissue like gingiva grows into the scaffold, there will be no residual space for the bone itself. This is possible because bone will just grow much slower than the soft tissue. That’s why as part of a research project, we combined a comparably fast resorbing material like tricalcium phosphate with another very good bioactive material of hydroxyapatite on the outside shell in order to obtain a ceramic membrane. This ceramic membrane then should prevent the ingrowth of the soft tissue during the healing phase. We are very happy with the results so far; we will hopefully share more details on this project soon.
And the third topic that has been receiving a lot of attention lately is surgical tools like burs and shavers as well as similar applications. We found that we actually hit the nerve of the industry here because it is often quite challenging to achieve high quality in traditional manufacturing and being able to achieve high productivity with a lot of design freedom with ceramic 3D printing is something we are very proud of,” he adds.
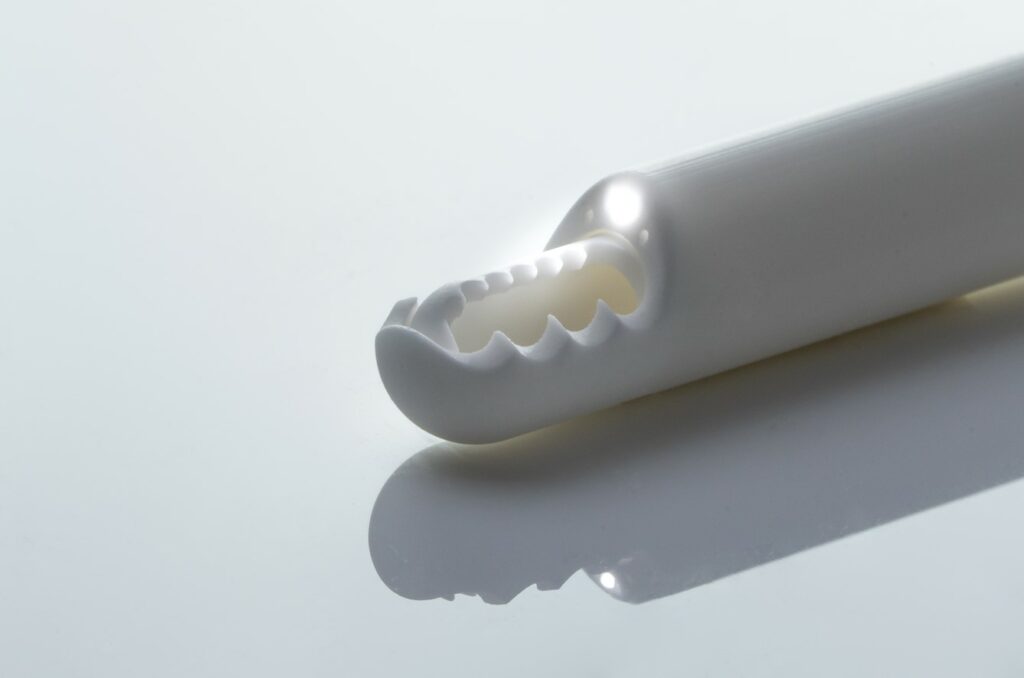
Ceramic 3D printing & healthcare applications: focus on surgical tools
Over the years, we came to realize that applications of ceramic 3D printing in the healthcare industry could be explored from four main angles: applications in extracorporeal assisted medical care, such as medical models and rehabilitation aids, medical devices, applications related to biologically active and biodegradable materials, such as long-term implantable tissue engineering scaffolds or bioactive materials for tissue regeneration and repair as well as bioprinting.
Interestingly, the very first set of applications is currently used in clinical settings across the world and plays a crucial role in surgical planning, improving surgical efficiency, and enhancing cure rates.
One thing I specifically like about Lithoz’s approach is that not only does their medical engineering team go the extra mile to improve the manufacturing process, taking into account the limitations of conventional manufacturing processes, they also take into account existing limitations of their proprietary technology. In the end, do we not say: “Compare yourself to who you were yesterday”?
Bomze outlines here that “surgical tools have gotten significant interest from medical professionals because one could now drastically improve the mechanical properties of 3D-printed high-performance ceramics. This is something that’s not easy to achieve in conventional manufacturing given the lack of desired properties often delivered by the materials.”
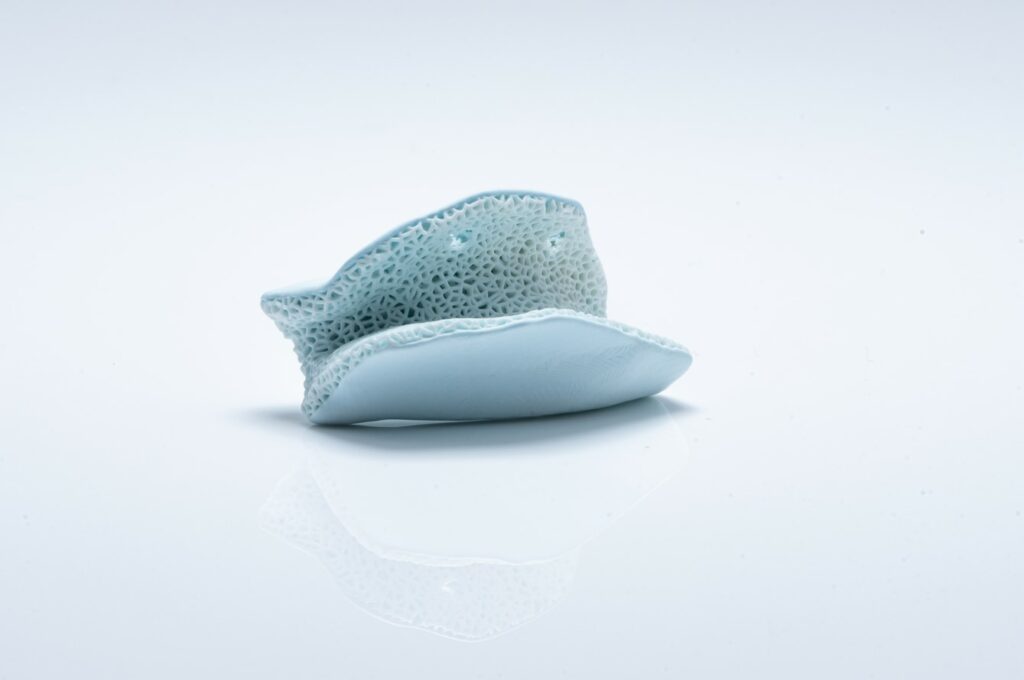
Speaking of their LCM technology and how they have been able to push its capabilities, he adds: “we could also broaden the processing window of some of our materials. This means that with the same material, we could produce very delicate parts with tiny features as well as bulky parts which are really sturdy and for load-bearing applications (an artificial hip joint for example). A year ago, we would have told medical professionals that this “wall thickness” is not possible to achieve with our LCM technology. With the advancement in material today, we can develop custom or patient-specific artificial hip joints.”
To give an example of a surgical tool where ceramic 3D printing offers a better way to manufacture compared to a conventional manufacturing approach, the Lithoz medical director made me envision a real-life scenario.
“Imagine an athlete who injured their soft tissue at the level of the knee while jogging. If the meniscus tears, it can get incarcerated over time and this incarceration can eventually lead to pain and limit mobility. As far as it’s possible, the surgeon will try to treat it conventionally but at some point, this conventional treatment will not be enough. The doctor will need to do a minimally invasive surgery where small incisions will be made in several parts of your knee and insert a different type of tools in order to remove those torn or injured meniscus. The tools used for this specific application are known as knee shavers.
Depending on the way the surgeon operates the device, it will go inside the tissue or remove a superficial amount of tissue, with all the tissue that has been removed being sucked away through the big central channel. There are also different channels on the upper side with different diameters in this specific tool, which used for rinsing the surgery site with a rinsing fluid while the central upper channel holds a glass fiber (light guide) to illuminate the surgery area. This should help the surgeon to have a better view and control, thus only removing what is torn and not healthy tissue. AM will help to produce such a complex tool while reducing the necessary assembly steps significantly.”
Simply put, the idea of using AM at the manufacturing level, is to have less debris during the surgery – making it easier to avoid any accidental scars that could have occurred in a traditional surgery. Not to mention that AM provides maximum durability with a minimal production effort.
A conventional manufacturing route would have required the use of milling and HIP (hot isostatic pressing) to mill the specific device before a final usage.
The manufacturing perspective
Bomze’ example made me question the different manufacturing requirements in a medical environment. As a trade press that covers the use of AM across various industries, it’s easy to talk about the importance of an AM factory in an industrial setting. In a medical/healthcare environment, I was curious to know what it looks like.
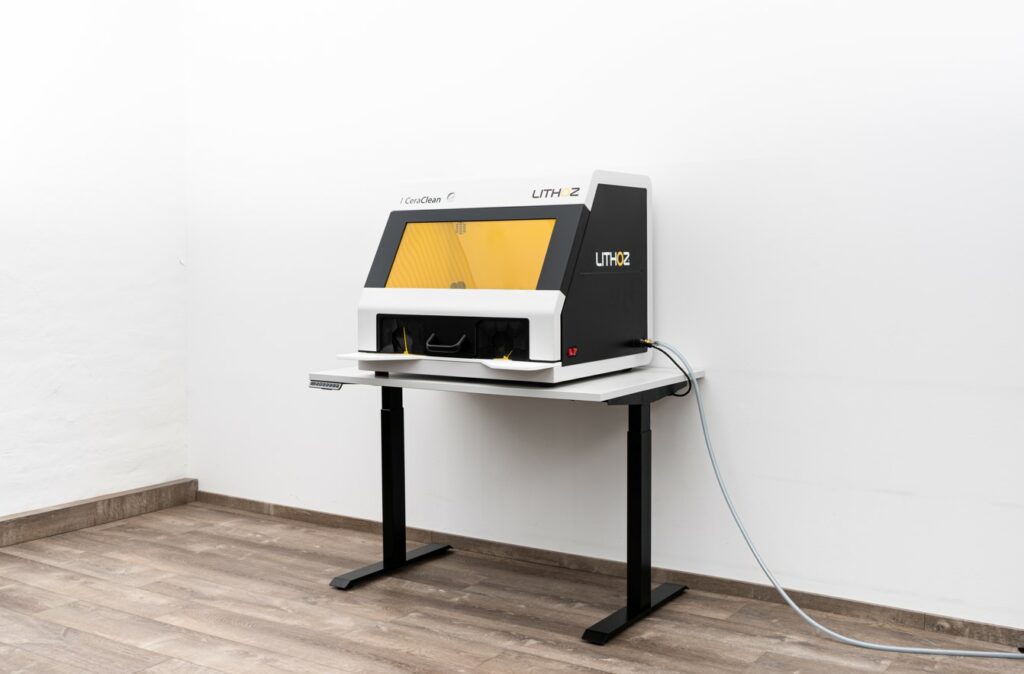
“First of all, surgeons get their 3D-printed parts from medical device manufacturers who remain Lithoz’s key targets in this industry”, Bomze clarifies. “That being said, there is a broad variety of companies that would be able to build up an AM factory for medical devices.
Key components of an AM factory may therefore include an industry-standard 3D printer and thermal post-processing materials that fulfill the requirements in terms of biocompatibility as a basis. Needless to say that it is possible to scale up this equipment depending on one’s needs.
“What’s important to keep in mind is that this AM factory – if made up of the right equipment – will allow you to achieve freedom of design while saving time and costs where necessary. It’s not only about the 3D printer but also about having quality standards from A to Z that could help you deliver predictable and repeatable results in serial production.
What we learned during the past 13 years is that a predictable and repeatable result is important for most of our customers. It is even more important in medical device manufacturing as part manufacturers must achieve the same result every single time. In this vein, it’s our duty as manufacturers of such AM factories to offer the possibility for automated documentation of the production process, and also smart designs of our devices and software to prevent human errors.”
With its array of technologies and one of the biggest material portfolios in the industry, Lithoz can pride itself on developing a technology portfolio that could meet production requirements beyond the healthcare industry.
While cost and performance comparison between a Lithoz’s AM factory and another factory (powered by conventional manufacturing processes or other AM technologies) are too broad and complex to be discussed in this article, I strongly believe the applications discussed today and the partnerships the company continuously signs in the healthcare industry testify to the potential of their solutions.
In the end, whether we talk about dental restorations, surgical tools or implants, Lithoz’s journey shows that advancements are being made in the research and application of ceramic 3D printing technology in healthcare. Being able to witness its development one step at a time makes me confident that its best days are yet to come.
This content has been produced in collaboration with Lithoz. It was first published in the March/April edition of 3D ADEPT Mag.
Remember, you can post job opportunities in the AM Industry on 3D ADEPT Media free of charge or look for a job via our job board. Make sure to follow us on our social networks and subscribe to our weekly newsletter : Facebook, Twitter, LinkedIn & Instagram! If you want to be featured in the next issue of our digital magazine or if you hear a story that needs to be heard, make sure to send it to contact@3dadept.com