
Dominik Solenicki is the co-founder and CEO of Sintratec, a Switzerland-based manufacturer of SLS 3D Printers. The company’s products are available in Europe (France), the USA and even in South Korea.
Even though they are not limited to the medical sector, readers of 3D Adept might remember applications such as the production of drugs carried out with Sintratec Kits.
At Formnext, the company unveiled a two-in-one system that might definitely change the way makers produce parts. Called Sintratec S2, Dominik Solenicki shared with 3D Adept the story behind the creation of this system.
What led to the manufacturing of Sintratec S2?
Speaking of their early beginnings, Dominik Solenicki explained that Sintratec started offering the market Sintratec Kits and S1. The company’s laser sintering technology enables the manufacturing of parts that are hard to design that require high accuracy on the one hand, on the other hand, comply with robustness and temperature standards.
However, a big challenge, users of the first systems faced, was the production of a final product. Sintratec wanted to best help them to achieve production of final products hence the S2, a system that can achieve “a perfect application development via its platform”.
“Sintratec S2”
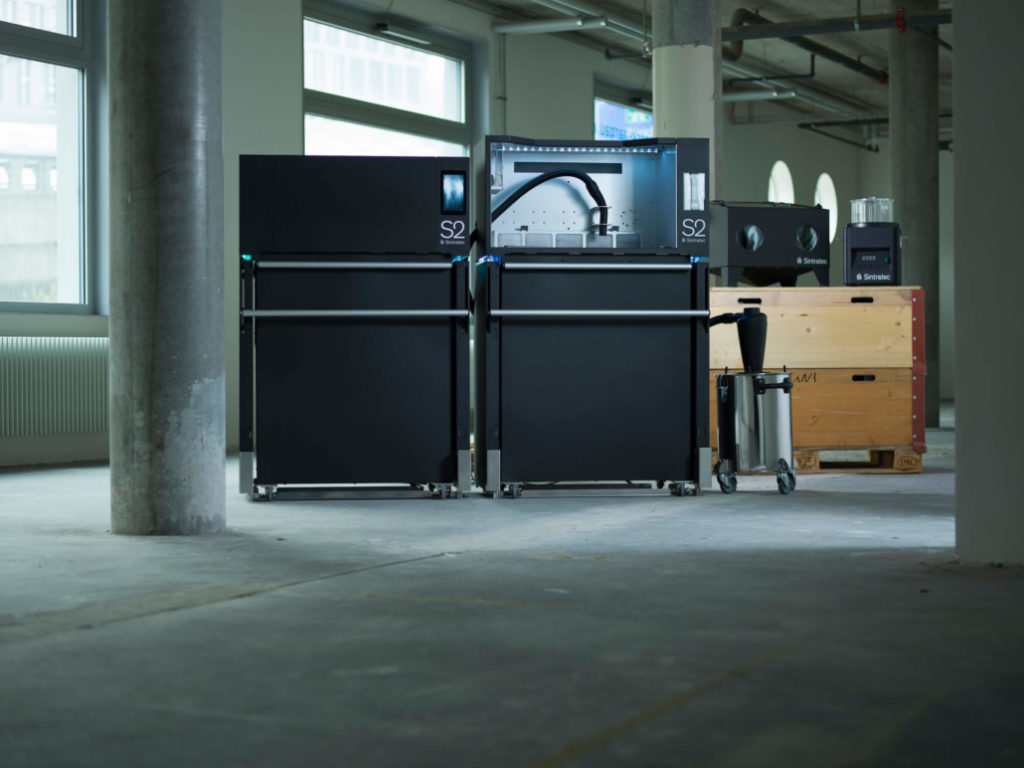
For Dominik, the “concept is built with scalability in mind”. The Sintratec Laser Sintering system integrates a cylindric printing area that comprises a new heating and ventilation concept. Through an integrated 4K camera, the user can control the print process and evaluate the surface of every print layer in real time.
Furthermore, the printer is equipped with a laser scanning system that facilitates repeatability and ensures a good printing speed.
Addressing the main challenges of SLS 3D printing
Even though SLS 3D printing is the favorite system of some users, there is almost no restrictions in this process. Furthermore, the technique still remains expensive for most users.
Sintratec aimed at addressing this first issue via the low-budget solution. Another problem faced by users is the difficulty to handle materials. Is there any feature that enables convenient powder handling? What’s the best way to proceed if the part should have a better surface quality?
As far as those questions are concerned, Dominik explained that the material handling station collects the used material and sieves it for its reuse. In addition, the blast cabinet enables to improve surface quality of parts so that they look more attractive.
Laslty, “the Sintratec Polishing Station, a magnetic tumbler, seals surface impurities and lends the printed components a smooth, stainless-steel like finish.”
For the CEO, the system enables any user to “execute his/her vision and can adjust to anyone’s demands”.
Top Objectives of 2019
As 2019 is around the corner, the CEO is also thinking about the vision of the company. All the team will dedicate time and energy to successfully bring the S2 solution to the world. Expanding their distribution network will therefore be a key goal to achieve.
In order to reduce waiting times for the Sintratec S2 system, the Swiss technology company recommends to place system reservations.
For further information about 3D Printing, follow us on our social networks and subscribe to our newsletter
Would you like to subscribe to 3D Adept Mag? Would you like to be featured in the next issue of our digital magazine? Send us an email at contact@3dadept.com
//pagead2.googlesyndication.com/pagead/js/adsbygoogle.js
(adsbygoogle = window.adsbygoogle || []).push({});