Climate change is a topic that is on everyone’s lips. Governmental authorities have sounded the alarm so loudly that both legal entities and individuals feel they have a mission: play their part in addressing climate change issues. Among the multiple fields this problem can be tackled on, there is manufacturing.
According to the Environmental Protection Agency, the American manufacturing industry accounts for almost a quarter (23%) of direct carbon emissions. The situation is just as dire for the European industry which emits an annual total of 880 million tonnes of carbon dioxide equivalents making it one of the largest emitters of greenhouse gases on the planet. Not to mention that, be it in Europe or in the US, manufacturing remains a field of activity that is deeply linked to other economic sectors such as power and transportation. Beyond these interconnected sectors, one should recognize that the more manufacturing grows, the more new technologies are being developed to help improve operations; new technologies that may be uniquely positioned to beat climate change. And, as you may already know, one of these technologies is Additive Manufacturing (AM).
Here is the thing, AM inevitably involves the contribution of different stakeholders for scaling manufacturing; stakeholders who include a wide range of software experts, material experts, 3D printer manufacturers, or post-processing** specialists, just to name a few. How can each of them address climate change issues? This is the million-dollar question we are going to discuss in this exclusive feature.
Climate change: the basics
To put this into context, climate change is about observed changes over the 20th century, in the average weather conditions of regions across the world. These changes include the rise in global average air and ocean temperature, increased global sea levels as well as long-term sustained widespread reduction of snow and ice cover. Furthermore, extra heat in the climate system is the cause of these changes, and this extra heat is due to the increase of greenhouse gases in the atmosphere (or greenhouse gas emissions), which are primarily the result of human activities.
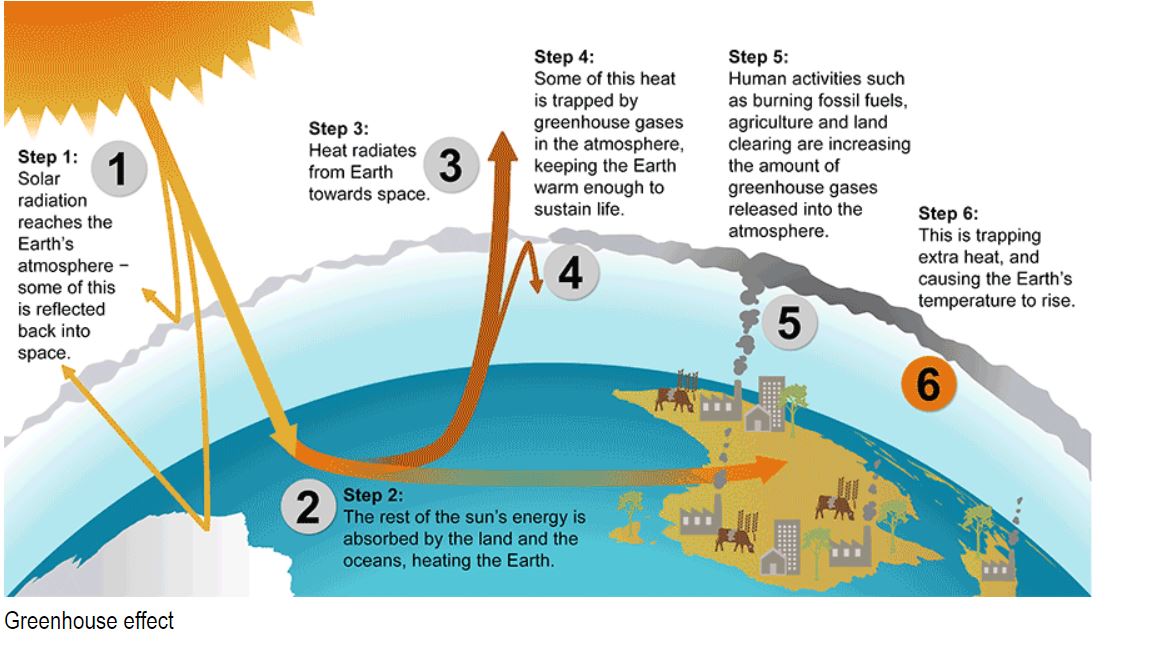
Those greenhouse gas emissions are measured in every product’s carbon footprint – hence the term carbon dioxide equivalents – at each stage of the lifecycle product. All of this becomes more complex for companies because, for each product – produced and consumed -, various factors should be taken into account to measure the total carbon footprint, factors that include the materials used in fabrication, the manufacturing processes or transportation.
These factors – which are the most widely mentioned ones when it comes to manufacturing – highlight the need for companies to implement a sustainability strategy to address them. That’s why climate change and sustainability issues are often addressed interchangeably within organizations.
According to Dr. Runze Huang, researcher in sustainability, CEO and Cofounder of ExLattice Inc, “climate change and/or other environmental impacts might be the most mentioned challenges to be addressed, and that could be possibly addressed now, regarding sustainability. Sustainability consists of economic, social, and environmental aspects, which is a much larger concept than climate change. Among those aspects in sustainability, economics is assumed to be addressed most of the time because it’s the traditional fundamental block to business/industry; social aspects are generally complicated, can be extremely difficult to address, and not easily tangible. So, this seems to leave environmental aspects including climate change to be the lower hanging “unaddressed challenge”, and often it leads to thinking that sustainability is being addressed when progress is made regarding climate change.
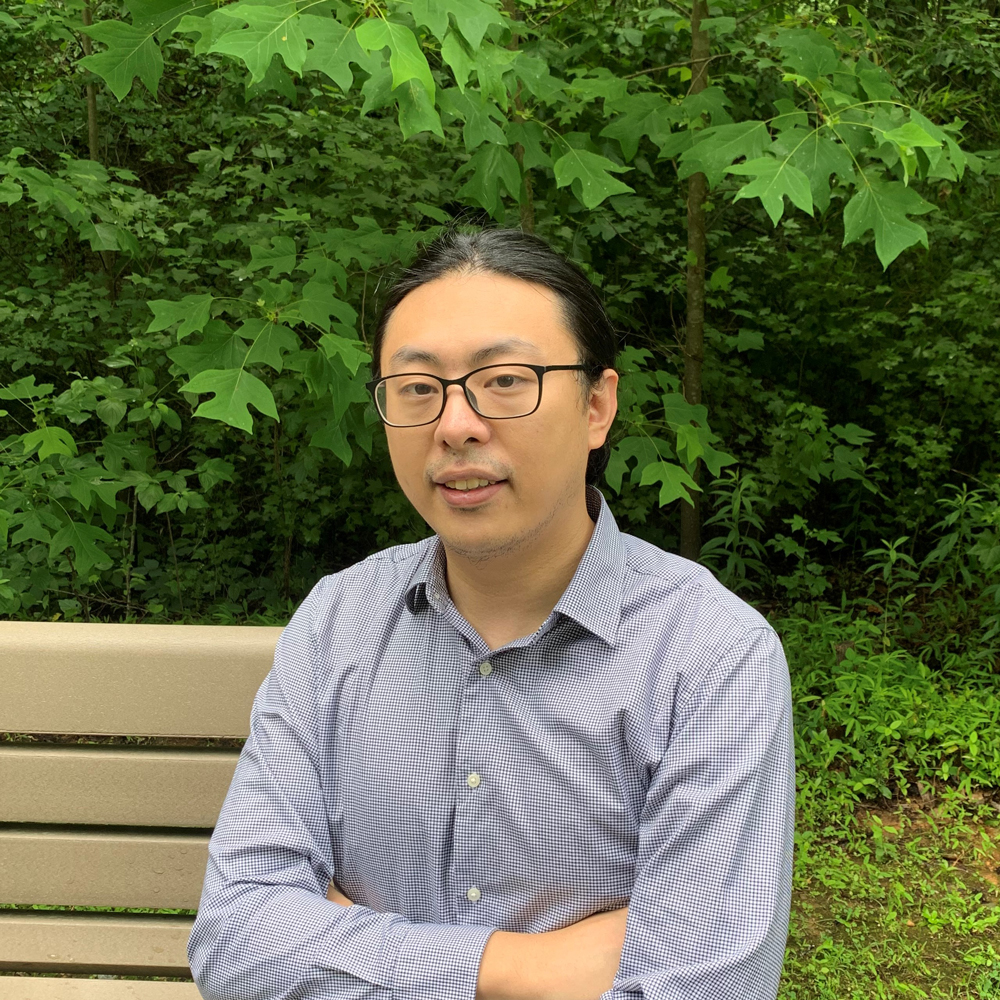
Secondly or more importantly, it is because addressing climate change and environmental impacts, in many cases, could also benefit the economic and social aspects from a larger perspective. Many measures taken to reduce emissions are related to improving efficiency, reducing waste, and leveraging new technologies, which brings long-term tangible economic gains and job growth at the same time to the factory/business and the whole society.”
On the other hand, although AM is said to beat climate change through its various stakeholders, the industry still lack a measurement model to confirm the validity of this statement. Researchers and sustainability experts like Dr. Huang said the most used tool/model for providing key data is life cycle assessments (LCA) or life cycle inventory analysis, a method that covers 5 major life cycle stages including material extraction, manufacturing, transportation, use, and end of life.
“A good LCA model generally contains parameterized sub-models for each life cycle stages to estimate energy use/GHG emissions from bottom-up with basic design/engineering data. And it also should include sub-models for various AM processes such as FDM or DMLS, and sub-models for traditional manufacturing processes like machining or injection molding for comparing purposes. The use phase sub-model should be customized for the specific application of the AM parts/products to be analyzed. Such model allows for estimation of the life cycle energy and emission net changes with changing inputs directly from AM users”, Huang notes.
How does this translate into each stakeholder influencing parts production via Additive Manufacturing?
The software perspective
The use of software in an additive manufacturing production requires various capabilities that can be categorized into five main types of software: Design (CAD), Simulation (CAE); Processing (CAM), Workflow (ERP/MES), and QA & Security. Depending on which software publisher an engineer relies on, it is possible to find a software that encompasses one or several of these capabilities.
Should every software company therefore apply the LCA model? The answer is much more complex than we think.
“We must be clear on the challenge we are up to: Not only do we need to reduce carbon emissions — this is where lightweighting could help — but we need to go to zero emissions, and likely less than zero, to stay below critical levels. Under our current engineering and manufacturing models, this change would take generations”, Lin Kayser, Founder and CEO of Hyperganic states from the outset.
According to Kayser, adopting a new engineering and manufacturing paradigm is an “absolute must” and while AM – as a manufacturing process – is a critical step under this paradigm, algorithmic design is another pivotal one.
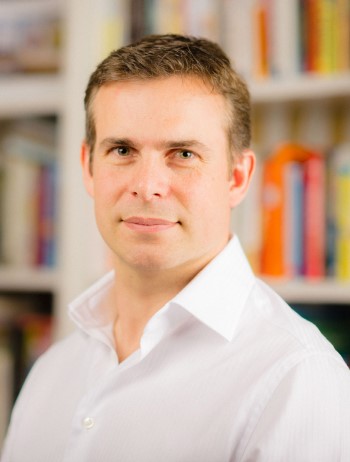
“We need to engineer objects through computer code, not through the current manual visual process – instead of an engineer drafting a blueprint in a CAD program, this new way of engineering uses algorithms to craft the most intricate and advanced objects in much shorter amounts of time. Coincidentally, this is exactly how Nature works. Nature builds things additively using blueprints or code contained in the DNA. Under our new paradigm, Nature shows us the way forward”, he adds.
Taking example on Hyperganic Core, a voxel-based geometry platform for AI-based and algorithmic design developed by his company, Kayser explains how interesting it becomes, to create objects by encoding the process one goes through when one designs something into a computer algorithm.
“Instead of creating one object, you create a process that designs objects of that category. Now, you can engineer complex objects in minutes instead of weeks and test out different input parameters quickly, which may result in radically different designs. If you think about it, almost all innovation that we witnessed in the last 40 years came from the Information Technology sector, and is driven by Moore’s Law. A software paradigm encourages re-use, standardized interfaces and accelerated information exchange. If someone builds a database, I can just use it, I do not need to learn how to build one. If someone builds a better one, I can probably just swap out that component, because it uses a standardized interface. This dramatically speeds up the development of complex software systems. In engineering, on the other hand, people are mostly busy designing the same thing all over again. Any improvement that you make to your objects rely on you, as an engineer, to learn some new tricks and apply new principles. There is little opportunity to share components and use what other people have done. The only way through is buying physical components, and that is a very limited way to re-use ideas”, he adds.
It’s quite paradoxical and interesting to see how Kayser’s explanation also illustrates two of the “three R’s rule” in sustainability (Reduce, Reuse and Recycle) – a rule that enables environmental protection and and the preservation of resources through a priority approach, the ultimate goal being to get the most practical benefits from products and to generate the minimum amount of waste. In this specific case, Kayser’s explanations highlight how an algorithmic design approach helps reduce time and re-use already built designs in the creation process.
While this is very interesting, we should recognize that it does not provide tangible data that proves its viability with regards to climate change. This makes us think that one way to measure the positive impact of this approach is through applications. How are applications made? And how do we measure improvements these new applications provide as compared to previous made using other manufacturing processes?
“Most people will think of having more lightweight components or functional integration. This is great, as it is important to save material and get away from “heavy metal” carbon-heavy processes. However, the real impact is going to come from radical innovation, enabled by AM. For example, 3D-printed copper spools for electric motors can have complex shapes that reduce eddy currents. This helps the motor get more efficient at high speeds. 3D-printed battery components can help us improve energy density and enable new types of energy storage in general. New types of AM-enabled rocket engines could enable single stage to orbit. These are just a few instances of how 3D printing can move entire industries towards more sustainable innovations” Hyperganic’s spokesperson said about the reduction of carbon footprint in vehicles.
The materials’ perspective and “the dirty little secret of additive manufacturing”.
Before we go further, please note that ‘carbon footprint’ and ‘energy’ will be used interchangeably as from now. We will take into account that sometimes, energy and carbon dioxide emissions are considered as separated items when it comes for instance to running the manufacturing tools on solar electricity and, other times, they are so intertwined that it is not just possible to consider them separately. A good example of the latter case, is the extraction of raw materials out of the earth and their processing into well-defined molecules.
That being said, it should be noted that the “inner energy” of materials used for fabricating products is an important – and often less-considered contributor to the total carbon footprint of those products. Furthermore, from a manufacturing standpoint, it’s a complex and difficult step to change the integrated energy of materials without changing the way they are produced and their final properties.
Imagine for a second that, this energy refers to everything that goes into the extraction, purification, production, and transportation of raw materials.
In this case, AM becomes a technology production of choice as it helps decrease the materials component of the carbon footprint through energy-efficient geometries that utilize much less material than traditional manufacturing processes.
6K Additive is drawing the industry’s attention here to the way materials – especially metals – are produced. According to Frank Roberts, Group President 6K Additive, “it’s at the material production stage that manufacturers can make a real change with regards to sustainability. In metal powder production, the industry is woefully behind on the environmental front. In fact, we refer to this as “the dirty little secret of additive manufacturing”. Specifically in metal powder production, the incumbent technologies use feedstock that needs to be created specifically for their process (such as wire) which consumes energy to manufacture and requires transport (often from overseas). Their process also creates waste during the manufacturing process that either is sold for scrap value or in the case of titanium will most likely be burned or end in a landfill. Using traditional methods for metal AM powder production, up to 70 percent of the material produced can be waste. A substantial volume of material is produced at unusable sizes and this waste material either goes back into the process – burdening the material with two or three times the energy cost – or is sent to landfill, this process is extremely wasteful.”
To avoid negatively counterbalancing the sustainability benefits reaped in later stages of additive manufacturing, 6K Additive has been developing a powder manufacturing process – named UniMelt®- that guarantees at 95%+ that most, if not all, of the material is usable powder and not waste from the process.
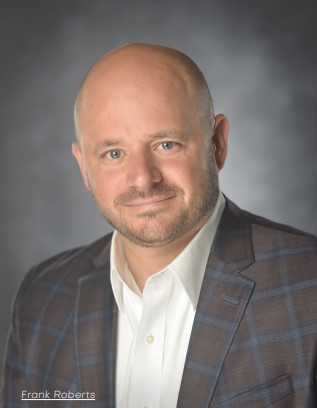
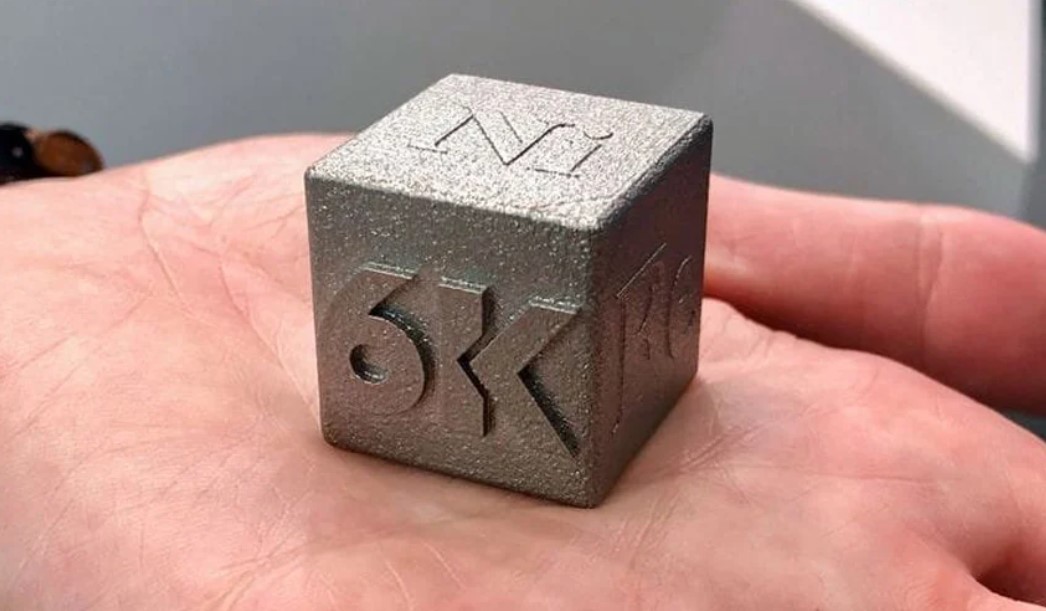
“Additionally, the UniMelt process can use feedstock material sourced from various input streams including machining scrap, used powder, AM supports and failed AM builds. All of these feedstock sources essentially count as near zero carbon footprint, as they are often considered scrap material. 6K Additive recycles and upcycles this “scrap” material into premium powder for AM”, the company’s expert points out.
“The UniMelt system is the world’s first and only industrial-grade microwave plasma production process that has a yield of near 100 percent, almost eradicating the production of unusable powder, and in addition uses scrap or used material as feedstock. This represents a true circular economy by recycling powders and materials from many different sources to be used in the UniMelt process – certified scrap materials from CNC manufacturing, used AM powders, failed models, even condensate materials from AM equipment. Using the UniMelt system to recycle these materials into premium metal AM powders, without losing any performance credentials in the process, merits a true sustainable alternative.
Additionally, the UniMelt process uses significantly less energy and gas to produce powder. Because the material is pre-sized prior to being put through the process, the UniMelt is only spheroidizing the material using far less gas than atomization. Additionally, because the material coming out of the process is the correct size, the post-processing time and energy after is also far less in the 6K Additive process. Below are four charts that illustrate these points. We currently have contracted with a 3rd party environmental agency to conduct a Life Cycle Assessment on the 6K Additive process against the incumbent technologies. This report is expected to be finalized in mid-Q4, 2021. Based on information we’ve received from industry experts and customers the below charts illustrate the energy comparison against other material manufacturing processes”, Frank Roberts told 3D ADEPT Media.

While waiting for this LCA report to be finalized, let’s note that the materials company is currently working with space company Relativity to produce quality certified powder from scrap material. The new material would later be used in the additive production of an end-use space part. Despite the confidentiality that surrounds this partnership, preventing 6K Additive to make any comment regarding this development, the company ensures that through other partnerships, with Form3D and Castheonfor instance, they sell powder derived from sustainable sources. Designed for production applications, these powder materials met or exceeded ASTM specifications.
As examples, here are the specifications for 6K Ni718 and Ni625 that are commercially available.
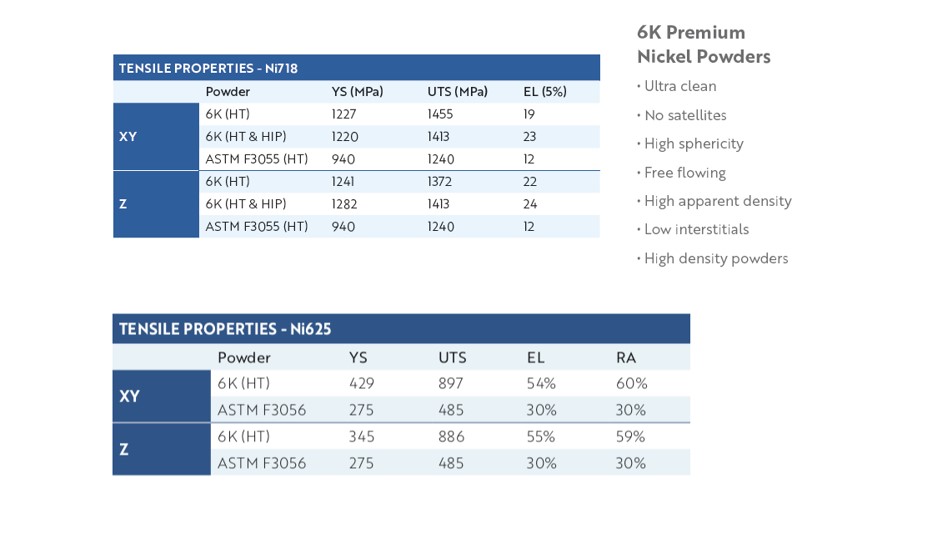
What about non-metals?
Bringing non-metals around this table is of paramount importance when we know that most AM users still leverage non-metal AM technologies. For those applications, AM can decrease the material’s embodied energy by displacing parts that would have traditionally been made with a high-embodied-energy material. In this case, AM users should keep in mind that every production part should not necessarily be fabricated with metal AM.
Sometimes, polymer or composite 3D printing can perfectly do the job, delivering even a lower embodied energy (and often lighter-weight) solution. From a materials producer standpoint, we’ve developed a keen interest in PolySpectra that ambitions to create high-performance AM materials and processes with overall carbon footprints that are a fraction of today’s state-of-the-art materials and processes.
The company has developed COR Alpha which stands for Cyclic Olefin Resin. The additive manufacturing polymer is described as unique because of its sheer ruggedness and integrates a set of qualities that are comparable to injection moulded plastics.
We mention the material today because the producer strongly believes that “in order to have a chance of making an impact [in climate change], you first need 3D-printed materials with the performance and durability to displace traditional manufacturing processes.”
To illustrate how COR Alpha does that, the company has shared the dramatic reduction in estimated carbon dioxide equivalents of printing with the COR Alpha material, compared to injection molding with three common engineering plastics.
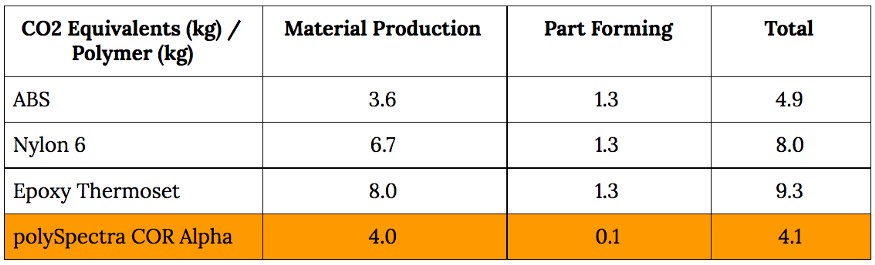
“With COR Alpha, we can 3D print parts with the strength, toughness, and working temperatures of today’s state-of-the-art polymers — with the bonus of a significantly reduced carbon footprint. If we’re successful at using polymers like COR Alpha to dramatically lower the energy required to manufacture durable goods, we’ll unlock a new paradigm of energy-efficient manufacturing by leveraging chemical bonds to displace the work currently performed by electrons. This could have a huge effect on the energy requirements and carbon footprint of manufacturing — and could be a climate change difference maker”, Raymond Weitekamp, Founder and CEO of PolySpectra declares.
The manufacturing perspective
Not only are there various types of 3D printing technologies, but most of them remain very energy hungry and are about comparable to machining at the production stage. This means that AM will not always win in the “process energy” category.
An example that might actually work in favour of AM is the energy usage of a typical benchtop-sized DLP printer. When compared to a traditional injection moulding tool, it turns out that the difference in the process energy is 100X, which means, as per Weitekamp’s words that, “DLP printing processes can use as little as 1% of the energy of an injection moulding tool.”
However, this is just one example that we have been able to identify. The market still presents a lack of resources regarding measurement methods of AM technologies’ environmental impact.
And…transportation?
Transportation after manufacturing does not only require to deal with transmission of the product to the end user. It has also required to take into account storage of these products and ultimately some loss if they are not purchased. Thanks to 3D printing production on-demand, decentralized production has become the way to go for manufacturers to reduce stocks and global footprints.
If you have been in this industry for a while, you know that the Covid-19 pandemic has expedited the implementation of distributed digital manufacturing across organizations, which means shorter lead times as well as lower transportation energy.
Even though the system has proven itself, we can’t help but question ourselves if it will not have an impact on companies producing traditional systems that are usually located on economies that need to base their production on the use of labour intensive.
To this, Dr. Runze Huang responds that “the impact would be noticeable in the short term. Decentralized production is a nice concept but does not bring large enough benefits for a major shift for most of the companies. It was applied more recently due to the impact of COVID-19 and its disruption of the existing supply chains. As that supply chain gets stable, the scale of the economy still works and dominates. And it depends on whether having a decentralized model can lead to a reduction in footprints from a life cycle perspective.” For the expert, “companies should focus more on the application than the supply chains. The potential benefits and impacts, both environmentally and economically, of the use phase are still greatly larger than the other life cycle stages combined in a lot of cases. The differences can be an order of magnitude. I think it applies to our AM industry, not just companies using distributed models. The best and fittest application wins.”
Concluding notes
As far as manufacturing is concerned, new business models based on AM, will potentially be complementary to the traditional models, and some cases, might even cannibalize the traditional ones. For these new model ones to work or even cannibalize the traditional ones effectively, they should necessarily involve infrastructures that go beyond the simple use of AM technologies, to encompass smart infrastructures related to Industry 4.0.
However, these smart infrastructures make it more complex to measure the environmental impact via the LCA model and might lead to the use of other individual analysis methods to prove the viability of a sustainability strategy. As a matter of fact, this feature highlights the importance of the LCA model, but also recommends at various levels to focus on applications to appreciate the environmental impact of AM on climate change.
One thing is certain, putting sustainability and climate change at the forefront of a business model that implies AM, requires to take into account all key stakeholders – at socio-economic and technological levels – that may have their part to play in this industry 4.0 transition.
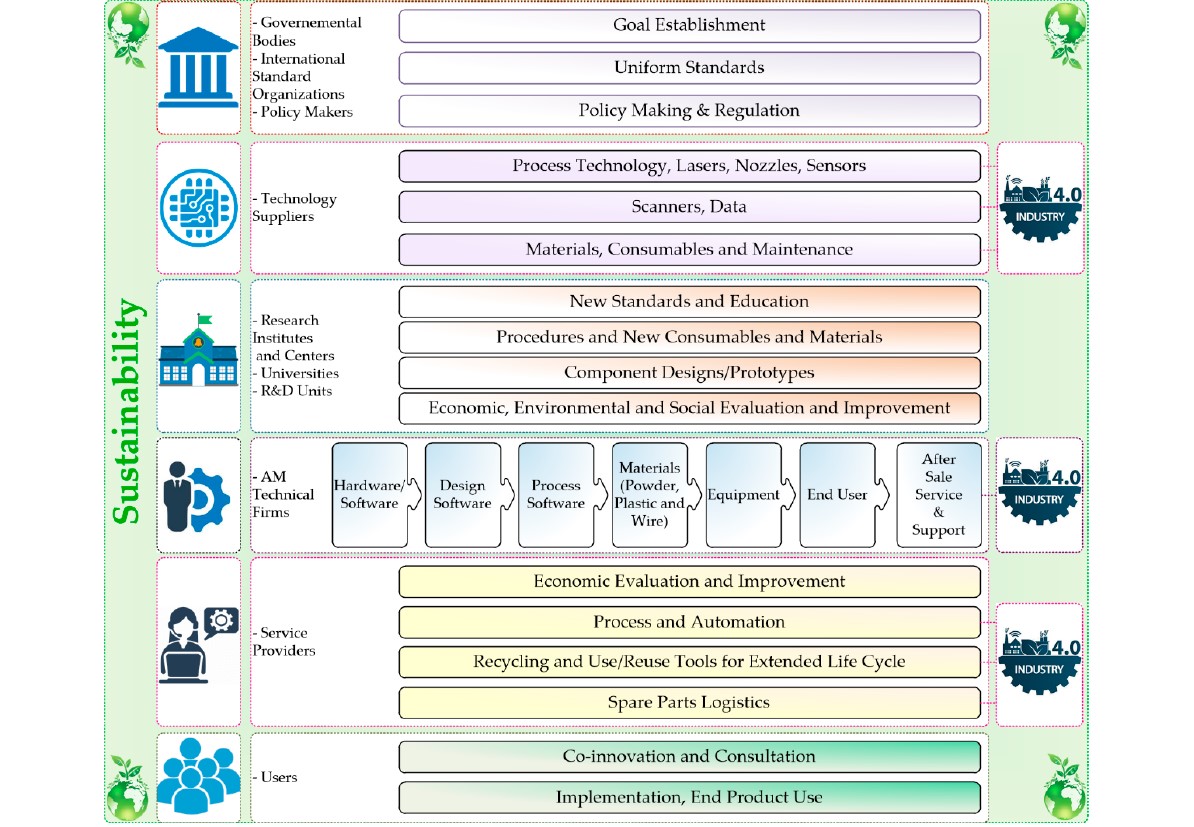
This exclusive feature has first been published in the 2021 September/October edition of 3D ADEPT Mag.
Remember, you can post job opportunities in the AM Industry on 3D ADEPT Media free of charge or look for a job via our job board. Make sure to follow us on our social networks and subscribe to our weekly newsletter : Facebook, Twitter, LinkedIn & Instagram ! If you want to be featured in the next issue of our digital magazine or if you hear a story that needs to be heard, make sure to send it to contact@3dadept.com