We just got back from Frankfurt, a European and German city best known for its production of high-quality sausages (frankfurters), but at this time of the year, for AM enthusiasts and specialists, the city becomes the global capital of industrial 3D printing. For many I talked to, it’s a bit like Christmas – the grey climate and the timing may have their part to play in this analogy, but I would rather say it’s a fAMily reunion.
(In case you are new to this industry, note that “fAMily” is a portmanteau coined by Mesago, the organizers of Formnext, that combines the words “family” and “Additive Manufacturing”.)
I don’t know about you, but from where I come, family reunions are sacred; so is the importance I attach to this fAMily reunion. And as in all families, one finds the elders whose wisdom and experience often pave the road toward success – for those who listen to them; there are always some uncles and aunts who will remain killjoys no matter how optimistic you are and there are babies and kids we rarely listen to, because they are just expected to follow the rules; yet the saying goes that out of the mouths of kids come words of truth and wisdom. So, yes, in all families we find these three groups of people and Formnext is surely no exception to that.
1- The killjoys
I usually never listen to killjoys – most of the time, they complain and they do nothing to address the situation they complain about. But the pandemic, and now the current political and economic situation countries have to handle make it impossible not to pay attention. These issues are actually the killjoys of this annual gathering as they continuously affect businesses.
For instance, this year, amid the 802 exhibitors present on the 51,148 square meters of booked exhibition space, there were no Russian companies. Well, you know why. We did see some Ukrainian companies though.
Also, it’s crazy how our brains are wired to scout for the bad stuff, focus on the threat or give weight to (and remember) negative experiences or interactions more than positive ones. As you know, I am not a psychologist, but I know these people refer to this as negativity bias. And that’s something that was present in some informal conversations I found myself plugged in:
- Curiosity was aroused at the sight of some companies’ large booths and onsite marketing actions, when we know that they recently laid off a great number of employees.
- Conversations were about mergers and acquisitions, inflation and geopolitics, and how they all affect businesses – and the ”glocal” AM world. (“Glocal” is a portmanteau I like to use to explain the fact that this industry is first and foremost global and local.)
So, what can AM really do about it? The short answer is that AM remains a technology of choice for decentralizing manufacturing processes and production, and a key enabler in making supply chains more resilient, facilitating resource and energy efficient production. How does this translate throughout the manufacturing value chain? That’s the one-million-dollar question, those who remember this event is about business, were trying to answer.
2- The elders
Aging is still considered as a sign of experience and wisdom and that’s something I am always eager to discover when I approach a company or an executive for the first time. Remember, a company might be new to the industry, but its founders’ experience or the company’s long-standing expertise in another industry may justify its presence on the AM market.
In this specific case, some of the elders that raised our interest at Formnext, highlighted some technology advances that we believe, represent a new direction or step forward compared to what was available last year. Anyway, this step forward or new direction was exactly what we were looking for, when we approached them.
New approaches in materials innovation
I was probably influenced by the September/October edition of 3D ADEPT Mag (distributed at Formnext and available here) that was dedicated to climate change actions within the AM industry, hence my keen interest in discovering more solutions and actions undertaken by material producers to drive sustainability.
A specific focus was placed on polymer material producers as the nature of their activity makes them an easy target to vanquish. Specialty chemicals company Evonik that has remained silent on this topic during the past years, had something interesting to say with the recent launch of a new grade of PA12 powders.
Speaking of this environmental issue, 3D printer manufacturer WASP showcased an example that is worth mentioning: recycled fishing net material that can now be used for 3D printing. To make it compatible with its 3D printers, the machine manufacturer improved the pneumatic adhesion systems to the printing surface and its systems for filtering printing fumes and anti-wrapping extruders to limit the shrinkage of these plastic materials.
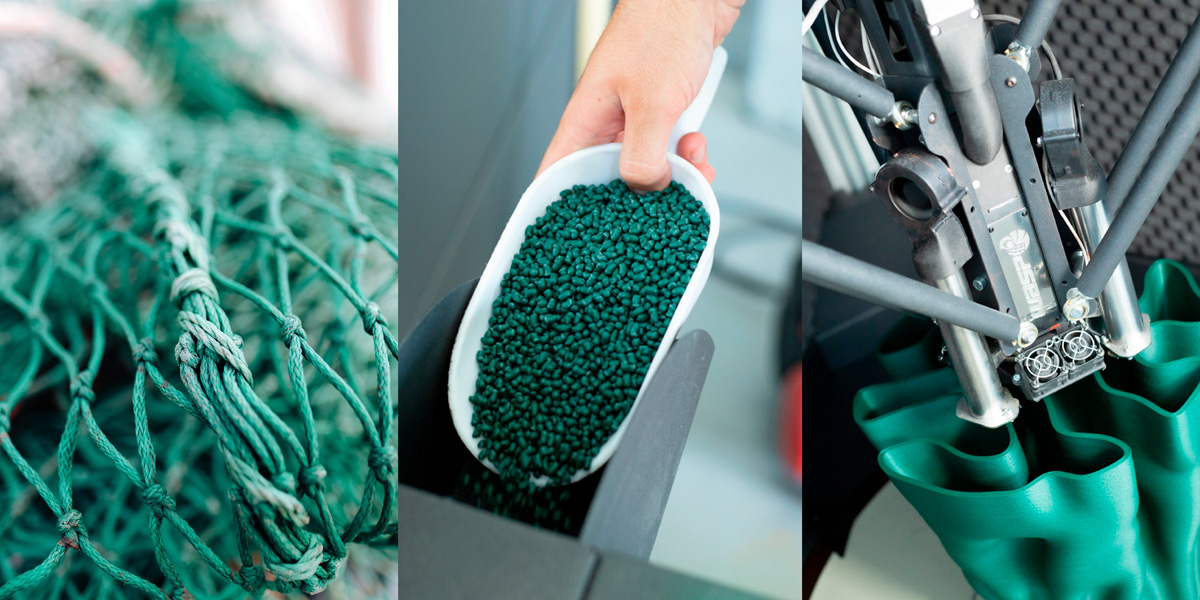
We also observed an increasing development of exotic materials that aim to meet the need of specific requests from manufacturers. ABS, PLA and high temperature materials like PEEK will always be the way to go for those who regularly use FFF 3D printing, but exotic 3D printing materials are here to push the boundaries of the technology – whether we talk about FFF or other AM technologies. It is now possible to envision more radiofrequency applications with FFF 3D printing thanks to Nanoe’s dielectric filaments for instance or impact protection applications such as padding, gloves, and helmets with new damping elastomers from Carbon.
On the metal AM side, I discovered that aluminum materials have a potential large enough to constitute the core business of certain AM companies. Due to their peculiar attributes, these materials were quite challenging to process at the very beginning when AM was still a nascent technology. Addressing this challenge required to develop high-performance aluminum alloys that could only be processed by AM.
Companies like VALIMET and Eckart AG bring tons of experience in the field and have decided to focus their business on aluminum materials for AM. If you have probably already heard about Eckart, VALIMET may be new music to your ears if you’re a regular reader of 3D ADEPT Media. The German owned, US-based manufacturer of spherical atomized metal powders focuses on aluminum and aluminum alloys. After atomization via inert gas for spherical morphology, its aluminum powders are sized to eliminate fines and enhance flowability. The particle size distributions (that range from -53 to +15µ) are tailored to maximize density, improve mechanical properties and optimize printing performance while meeting stringent OEM specifications.
Interestingly, at Formnext, ECKART made us realize that the fact that small powder particles are spherical in shape is not always the key item that enables aluminum alloys to stand out from the crowd.
Software solutions that talk to 3D printers but not only.
Manufacturing trends are often the very first items highlighted in our media coverage but this time, there was something about new software solutions that outpaced what we saw at the manufacturing level.
I like the fact that software companies start taking actions towards sustainability. Apart from the fact that the “DfAM” principle enables to design lightweight parts, it has always been difficult for software companies to truly justify their role in this journey.
A worth mentioning action is now seen with Siemens Digital Industries Software that introduces a “Product Carbon Footprint Calculator”- developed in collaboration with ClimateTech company sustamize GmbH. The new Teamcenter® Carbon Footprint Calculator software, part of the Teamcenter product cost management solution from the Siemens Xcelerator platform, enables organizations to measure, simulate, reduce and track their product carbon footprint early in the development phase. This will empower different departments to measure, optimize and manage carbon footprints at each level of the product value chain.
If AI has too often been mentioned, the people behind AI-powered software solutions are still struggling to demonstrate its true potential in the manufacturing value chain. One company that is building a path to follow here is UK-based Ai Build. Their focus on the show was maybe their software for robotic arms, but I can’t help but talk about their automated toolpath generation solution that enables to monitor, control, measure and optimize the entire AM value chain. Plus, the cloud-based platform has already repurposed over 10 tons of recycled materials to date, reducing greenhouse gas emissions by approximately 70%.
Moreover, unlike others who bring years of experience around the table, software company Cognitive Design Systems is not really what I will call an “elder” in this industry (the company was founded last year). It is rather a kid that may have the truth that engineers may need when it comes to the orientation of, nesting of, and support structure generation for parts. Its software solution relies on artificial intelligence (AI) to preform 3D modeling and numerical simulation to perform print preparation. Also, the fact that, the company no longer acts as the supplier of other software solutions, and solely focuses on their software services, may be the sign that something interesting is happening on their side.
Apart from AI, one notes that as the value of the digital thread is sung from all corners of the industry, the digital twin (DT) technology is gaining momentum. The technology has positioned itself as one of the advanced concepts that could help manufacturers earn credibility and viability in the new digital manufacturing realm.
Software company Flow Science told us how the concept when combined with computational fluid dynamics (CFD) solutions, help to understand or optimize different aspects of AM processes.
What’s even more interesting is the fact that for the first time, it is now possible to make the digital twin of a part usable in post-processing. Solukon, a company founded in 2013, whose founders bring over two decades of experience in this industry, is writing another page of their story with the SPR-Pathfinder® Software.
New manufacturing trends
Surprisingly, extrusion-based machines – with large-scale possibilities were quite predominant on the exhibition floor. American Thermwood showcased a couple of 3D printed parts produced with its LSAM technology but the company is no longer one of the only machine manufacturers present on the market of large 3D printed parts.
Legend: An Air Foil tool made from Sabic ULTEM (20% Carbon Fiber filled), 3D printed and trimmed on an LSAM 1020
Italian machine manufacturer Breton is coming into full force with GENESI, an industrial 3D printer with an enormous build volume of 2000 x 3200 x 8400 mm.
Large-scale AM possibilities come along the growing development of gantry systems and robot arm systems. BLOOM Robotics, a company that delivers serial additive robotics systems for mass customization is one of the companies I would like to keep in mind here. The company’s solutions are designed for AM, welding, milling and gluing with polymers. With AM, their unique selling proposition lies in their ability to eliminate the cost of creating various molds for every product through an automated process that enables mass-production. The company’s solutions are compatible with robotic systems from various different brands including STAÜBLI, KUKA, ABB, FANUC, Panasonic, and OTC to name a few. This means that, during the upcoming months or years, we will probably see a lot more of AM-dedicated developments from these robot makers.
On the metal AM side, we continue to observe the rise of Wire-Arc Additive Manufacturing (WAAM)/DED. Also, in this field, large-format, multi-laser metal AM is on fire. Until now, Nexa3D was one of the rare manufacturers to provide SLS systems with four lasers. As a matter of fact, that was one of their main selling points. Today, other manufacturers have pushed their technology so well that they can now market powder-bed fusion systems with four lasers. Farsoon is one of them.
Another manufacturing trend that represents a step forward in the use of AM technologies is the development of new ceramic 3D printing technologies that does not only open up a new range of applications in the industry but that also facilitate their integration into the traditional manufacturing value chain. One of these technologies is the Laser-Induced Slipcasting (LIS) technology developed by Lithoz. One thing we learned from the company is that dark ceramics are a key enabler in the range of new applications that the manufacturing process allows.
On another note, just when you think that there are not a lot to expect from FFF 3D printing anymore, a company comes to prove you wrong. A very intriguing manufacturing trend in this segment comes from a new entrant (that I will mention below in the group of “kids” of this industry): DUPLEX. The pink brand introduces MAP™ (multi-dimensional additive production) a technology that enables multi-directional printing. Not only does this speed up the fabrication process, but this two-directional process also reduces or eliminates the use of support materials, and makes it easy to print organic geometries. Amid the wide range of FDM 3D printer manufacturers that are present on the market, I think DUPLEX is the one that could make a big impact.
Lastly, on-site manufacturing or in-situ additive manufacturing remains a topic of interest for many professionals that are looking to manufacture locally or in remote areas. While the concept is easy to understand, we have to acknowledge the ingenuity for some companies to demonstrate it directly on the exhibition floor. With a 3D printer installed in a car, machine manufacturer XERION, a company known for the Fusion Factory, demonstrated in a practical way the ability to manufacture locally.
3- The kids
The kids of this “fAMily” reunion are actually new entrants to this market. They are not necessarily start-ups, sometimes, there are larger companies that decided to penetrate the market. I have to say that given the number of companies that filed for bankruptcy this year, I was pleasantly surprised to see a new range of companies try their luck on this market. Are considered kids here, companies that have less than three years on the AM market. In addition to DUPLEX mentioned above, the companies that I would like to follow moving forward include:
- Partbox, a 3D part streaming platform, ambitions to provide the fastest possible availability of parts through 3D printing on demand (in situ additive manufacturing). The company behind this platform is Schubert Additive Solutions GmbH, the AM division of large logistics company Schubert Group. There are a couple of things that I like about this concept: first you don’t need to have any 3D printing knowledge; the company works with a partner who already has an online shop with ready to print 3D models; the FDM 3D printers developed by Partbox are not to sell; the platform works under a leasing mode where the user buys a number of printing hours for a one-year period. At the end of the leasing period, it’s up to him to decide whether or not he should add more hours.
- KraussMaffei, a leading manufacturer of machines and systems for producing and processing plastics and rubber, is another OEM that debuted at Formnext with its powerPrint and precisionPrint machines. According to KraussMaffei’s Magdalena Schwangler, one of the project managers who worked on the launch of these machines, their development aimed to address their customers’ existing injection moulding challenges at the manufacturing level. 2023 will be dedicated to an intensive test phase with beta customers, after which the industrial 3D printers will be available on the market.
- Additive Assurance provides solutions for quality assurance of components made with additive manufacturing. The start-up decided to specialize in metal powder bed fusion techniques (SLM, DLMS, SLS etc.). It owns a patent pending in-situ analysis method that allows for the rapid detection of faults and variation in the AM process, enabling the user to take control of their AM builds.
- Additure, Grob and Jeol, three companies that you probably already discovered through our articles debuted at Formnext. They respectively provide metal 3D printing services for the former, and develop a liquid metal printing technology and an Electron Beam Powder Bed Fusion (PBF-EB) metal additive manufacturing machine (for the others).
- Moroever, another machine manufacturer is entering the market of affordable metal 3D printers. Headquartered in Slovenia, NPPower d.o.o introduces on the market the Malachite 3D printer, a metal AM machine based on LPBF – Laser Powder Bed Fusion. Available at a starting price of 75 000€ + VAT, the Malachite 3D printer would be suitable for all non-reactive metals, has a low inert gas consumption and integrates a unique 360° LED status bar that makes it easy to monitor the printing process from any place in the room. With a print volume (DxH) of Ø 125x 100 mm and a size of 715 x 705 x 1020 mm, the machine works with a laser power of 200 W and an operating voltage of 110 – 230V, 50Hz/60 Hz. It weighs 220 kg (485,017lbs) and enables a print layer thickness of 15-85 µm.
4- Applications that live up to AM’s promise?
To conclude…
With over 800 exhibitors, a wide range of sub-events, and a growing number of informal events and parties, summarizing Formnext often comes down to the holistic experience of each visitor. With a number of visitors totalling 29,581, the industry event’s number of visitors has grown by 65.6% compared to the 2021 edition that hosted 17 859 visitors and is gradually returning to the statistics of 2019.
“We are proud of the fact that Formnext has returned to its impressive pre-Covid level,” says Sascha F. Wenzler, Vice President Formnext at event organizer Mesago Messe Frankfurt GmbH. “We have once again demonstrated the importance of Formnext as the world’s premiere AM platform and the vital role of face-to-face interactions at Formnext for the further development of this highly innovative sector.”
While other announcements and insights will be covered individually and published on this online platform, it’s fair to say that the AM industry continues to grow, with more realistic expectations of where it wants to go.
Remember, you can post job opportunities in the AM Industry on 3D ADEPT Media or look for a job via our job board. Make sure to follow us on our social networks and subscribe to our weekly newsletter : Facebook, Twitter, LinkedIn & Instagram ! If you want to be featured in the next issue of our digital magazine or if you hear a story that needs to be heard, make sure you send it to contact@3dadept.com